Volkswagen公司基于模塊化柴油機標準部件(MDB)開發的新型2.0 L TDI發動機,搭載在Multivan車型和Transporter車系上,并首次投放市場。采用滿足商用車特殊要求的統一基礎動力,逐步替換原4缸機型,使功率范圍更大、燃油耗更低。該高功率版動力總成采用新開發的可調兩級渦輪增壓系統。
1 更高的要求
未來,對于輕型商用車動力裝置的要求將會越來越嚴苛。為獲得更好的經濟性和效率,商用車發動機必須降低燃油耗,同時提高功率和扭矩。為此,數十年來輕型商用車都以整體能力優于其他動力的現代柴油機為主要動力源。
Volkswagen公司的商用車發動機如今已是該領域的最佳動力系統。為進一步提高在商用車領域的競爭力,Volkswagen公司主要針對以下重點進一步開發:(1)通過模塊化柴油機標準部件降低復雜性;(2)堅持降低CO2排放;(3)提高升功率和扭矩;(4)優化響應特性和扭矩曲線;(5)滿足歐6排放法規要求;(6)良好的可靠性和耐久性。
自2012年以來,Volkswagen公司已非常成功地將新模塊化柴油機標準部件和共軌技術引入乘用車領域。在此基礎上,商用車特定版MDB將首次應用于Volkswagen的新Transporter T6車型。并且在要求歐6排放法規的市場上,將完全取代目前使用的發動機。
在概念階段,新發動機設計時就考慮到了商用車特有的嚴苛工況,以及有別于乘用車的特定安裝環境。同時,考慮到Transporter車系中乘用車車型(Multivan)占了很大比例,所以在行駛性能、聲學和振動特性方面均必須滿足乘用車要求,因此,在整個轉速范圍內具有適當的功率、豐滿的扭矩曲線和優良的起動性能至關重要。但是,輕型商用車較高的行駛阻力進一步加劇目標沖突。為此,輸出功率高達110 kW的發動機采用可變幾何截面渦輪增壓器(VTG)(圖1),而功率為150 kW的高功率版動力總成(圖2)則對原機型的兩級增壓進行全面改進,并同樣在高壓級增加可變幾何截面渦輪。從而進一步顯著提高工作范圍的適應性和扭矩特性。
圖1 單渦輪增壓發動機
圖2 雙渦輪增壓發動機
2 新型商用車發動機的主要部件
為使商用車在預定的外部尺寸下的可用空間盡可能大,其發動機安裝長度應小于相對的乘用車發動機(Volkswagen標準為既定的橫置發動機模塊化平臺MQB)。由于發動機傾斜度偏離MQB(由向后傾斜12°變為向前傾斜8°),因此幾個模塊必須專門用于可用空間比MQB更大的車輛(圖3)。
圖3 新型4缸商用車發動機模塊化結構
所有功率等級都采用相同的2.0 L基本發動機。通過調整渦輪增壓和噴油系統的部件來實現特定功率。表1為Transporter車系新型商用車發動機的主要技術參數。
表1 Transporter車系新型4缸商用車發動機的主要技術參數
3 氣缸體曲軸箱、平衡軸模塊、雙聯泵
氣缸體曲軸箱由灰鑄鐵GJL250制成并采用成熟的長裙設計。曲軸箱和平衡軸模塊均采用Volkswagen模塊化柴油機標準部件。除了采用帶平衡軸的曲軸箱,扭矩減小的較低功率等級發動機還可以采用可降低質量和成本的無平衡軸方案。
機油泵和真空泵組成的雙聯泵放置于同1個壓鑄鋁殼體內,壓鑄鋁殼體位于油底殼的氣缸體曲軸箱法蘭之下。通過調整吸入管,使其適用于更深更大的商用車油底殼,這樣就可采用模塊化柴油機標準部件下的乘用車發動機雙聯泵。
4 氣缸蓋、整體式氣門機構模塊
以176 kW雙渦輪增壓乘用車發動機為基礎,改進商用車發動機的氣缸蓋。Volkswagen公司的柴油機首次采用氣門桿直徑為5 mm的氣門。通過減輕氣門質量,可顯著減小氣門彈簧力,從而明顯降低摩擦。
與原機型相同,氣門組呈直線對稱排列,所有進氣門和排氣門分別位于一條線上。這種布置方式使冷卻通道幾何結構更簡單并提高芯子的穩定性。平行布置的氣門和優化了壓力損失的通道使氣缸充氣效率更高。通過氣門座渦流斜角和與之相配的氣道幾何形狀,確保了良好燃燒所需的渦流水平。
由于采用鉆孔和螺栓相互連接,所以可以利用模塊化柴油機標準部件的生產線節約制造氣缸蓋的成本。
新型商用車柴油機和4缸TDI模塊化柴油機標準部件發動機的氣門機構模塊具有相同的基本結構,但氣門正時是專為商用車設計的,從而能獲得非常豐滿的扭矩曲線。
5 增壓空氣冷卻器和進氣歧管
新型商用車柴油機與模塊化柴油機系列的其他發動機一樣,也采用水空增壓空氣冷卻器。不同于乘用車4缸機,Transporter車系的發動機艙空間較小,因而要求將增壓空氣冷卻器布置在氣缸蓋的上方。
冷卻芯由22個成對焊接的冷卻板組成,空氣按逆流原理流經冷卻芯。這樣既確保鋁板至冷卻液的傳熱良好,也保證壓力損失較低。湍流板改善了增壓空氣至冷卻液的傳熱。塑料空氣箱確保冷卻板內的氣流流動均勻。塑料空氣箱與冷卻器部件用卷邊固定在一起。為減少振動負荷,借助彈性緊固機構使增壓空氣冷卻器與發動機激振解耦。
由于商用車的用戶任務剖面比乘用車更寬廣,因而要求所設計的燃燒過程非常穩定。尤其在低速運行情況下,要求根據特定工況點設置進入燃燒室的氣流渦流,以減少顆粒物排放。由聚酰胺6.6制成的進氣歧管配有氣動操作的渦流瓣閥,能有效控制渦流。
6 廢氣再循環(EGR)系統
由于歐6廢氣排放標準提高了對發動機廢氣排放性能的要求,尤其是必須降低新歐洲行駛循環(NEDC)冷起動后的廢氣排放,因而需大幅改善高壓EGR系統的效率。
根據前幾代EGR模塊的經驗,T6開發在全工況下均有較高穩定性的全新氣門和冷卻器。開發重點為穩定轉換冷卻器旁通功能,避免燃燒殘留物冷凝。同時通過氣門桿的無側力運行,降低了氣門導管區域的磨損。
通過唯一的執行器無級控制冷卻器路徑和旁通,這種驅動可以最大程度地利用發動機側面及變速器上方的現有空間,無需采用真空控制旁通閥。EGR閥有2個浮子置于氣門桿上的氣門頂,鉻鎳鐵合金制成的壓縮彈簧將氣門頂壓入各自的氣門座內。
考慮到模塊在發動機熱端至冷端的氣路中的位置,不能采用傳統的U型流動冷卻器。而I型流動冷卻器在相同空間內效率太低,因此采用新的S型氣流管(圖4)。
圖4 高壓EGR模塊
EGR閥有3種不同的開關工作狀態:(1)在中間位置時,冷卻路徑和旁通路徑均關閉;(2)在旁通位置時,執行器向下推動處于中心位置的氣門桿,從而打開上方的氣門頂,使冷卻器旁通管的氣路通暢;(3)在冷卻位置時,執行器向上拉動氣門桿,從而打開下方的氣門頂,使S型冷卻管路通暢。
7 噴油系統
新型商用車柴油機采用Delphi公司系統壓力為200 MPa的噴油系統。雖然對商用車發動機的功率要求高于乘用車發動機,但屬于模塊化柴油機標準部件的DFS 1.20噴油系統的所有零部件幾乎都可用于功率高達110 kW的單渦輪增壓發動機。8孔噴嘴的霧化狀態與使壓縮比降低到15.5的新活塞凹腔形狀相匹配。
為確保雙渦輪增壓頂級動力在低轉速、大扭矩工況時所需的噴油量,新機型采用供油量顯著提高的雙柱塞DFP 7.20高壓泵。
8 單渦輪增壓系統
功率分別為62 kW、75 kW和110 kW的發動機采用在2.0 L TDI發動機VTG渦輪增壓器基礎上進一步升級的增壓系統。由于必須符合歐6排放法規,要求燃油耗和CO2排放較低,并具備使牽引力優化的扭矩特性,因而該渦輪增壓系統適用于此車系。
為了實現特定功率優化,分別針對功率高達75 kW和110 kW的發動機開發新型渦輪增壓器。此外,為了提高整個工作范圍的效率,重新設計了原機型的壓氣機葉輪和渦輪葉輪。
9 針對150 kW機型的雙渦輪增壓系統
隨著首次成功將兩級渦輪增壓用于Transporter車系,Volkswagen公司自2009年起成為優化牽引力的商用車發動機開發的引領者。為確保和擴大競爭優勢,新2.0 L雙渦輪增壓發動機與原機型相比大幅提高了功率和扭矩。
這種高功率版動力總成與功率較小的機型一樣,配裝于商用車時也需考慮到即使在最大載重5.5 t的情況下,也要有較高的載荷譜和起動性能。
基于原機型的成功經驗,再次采用可調兩級渦輪增壓系統,包括旁通在內的葉輪和壓氣機側為串聯模式。為進一步提高起動性能,高壓級采用VTG。低壓渦輪仍繼續由放氣閥控制。除了壓氣機被動旁通,還采用渦輪主動旁通閥及常見的放氣閥作為執行器。后2種閥門均配有真空調節的執行器(圖5),VTG也由真空調節。
圖5 增壓裝置零部件名稱
10 功率與扭矩
與原機型相比,新Transporter車系的2.0 L 4缸共軌發動機將功率范圍向上擴展為62~150 kW,原機型為62~132 kW。功率最大的單渦輪增壓發動機功率可達110 kW,原機型為103 kW。盡管功率提高,但僅在轉速1 500 r/min時就可獲得額定扭矩,而原機型轉速則需達到1 750 r/min時才能獲得額定扭矩。此外,在轉速3 000 r/min時可獲得最大扭矩340 N·m。在3 200~3 800 r/min的寬廣轉速范圍內,均可達到擴展的最大功率110 kW(圖6)。
圖6 新機型與原機型的功率和扭矩曲線比較(110 kW單渦輪增壓發動機與103 kW發動機對比)
Volkswagen公司的新型商用車高功率版動力總成采用額定功率為150 kW(轉速4 000 r/min)的2.0 L 4缸雙渦輪增壓發動機(圖7)。它以大于76 kW/L的升功率成為商用車領域的引領者。最大扭矩450 N·m遵循傳動系的機械傳動極限,在轉速1 400 r/min時就可達到最大扭矩。這與原先的高功率版動力總成相比,整個轉速范圍內的可用扭矩提高12%以上。
圖7 新機型與原機型的功率和扭矩曲線比較(150 kW雙渦輪增壓發動機與132 kW發動機對比)
11 行駛動力性、廢氣排放及燃油耗
新Transporter車系的發動機設計重點是大幅降低各功率等級的發動機的燃油耗和CO2排放,同時改善行駛動力性能。各功率等級的發動機均符合法規要求,滿足歐6排放標準。
深入的細節工作及專為商用車設計的渦輪增壓系統,使所有發動機的扭矩曲線更豐滿,因此,無論是0~100 km/h的標準加速度,還是行駛運行中較重要的機動性,都優于原來的車型。與原機型相比,頂級動力的功率大幅提高,因而需重新設計傳動比,使行駛動力性明顯改善(表2)。
同時,廢氣排放限值降低,要求優化進氣、充氣運動和噴油系統,顯著減少發動機原始排放,同時,將選擇性催化還原(SCR)系統用于排氣后處理系統。
整個排氣后處理系統由改進的氧化催化器和顆粒捕集器組成,顆粒捕集器帶有減少氮氧化物(NOx)的特殊涂層。在顆粒捕集器上游添加AdBlue尿素水溶液。集成在顆粒捕集器殼體內的阻擋催化轉化器防止NH3泄漏。結合機內措施,有助于顯著減少整個發動機工作范圍內的排放,尤其是NOx排放。
盡管已大幅降低有害物質排放并改善行駛動力性能,仍可顯著減少所有發動機的CO2排放。進一步優化的手動變速器和雙離合變速器(DSG)也對CO2減排做出重大貢獻。采用DSG的汽車,因其采用帶離心擺重的雙質量飛輪,因而換擋速度明顯減小,從而降低燃油耗,并提升駕駛舒適性。結合車輛措施,能比原機型減少CO2排放30 g/km(圖8)。
表2 新Transporter T6汽車(陰影部分)與原車型的行駛動力性比較(手動版,前驅)
圖8 新Transporter T6汽車與原車型的CO2排放比較(初值,僅針對前驅車型)
12 結語
Volkswagen公司采用4氣門技術的新型2.0 L 4缸TDI發動機為其輕型商用車的廣泛應用和未來發展打下了基礎。模塊化柴油機標準部件是設計商用車專用發動機的起點,采用模塊化柴油機標準部件可使發動機降低成本成為現實,通過現有的模塊化柴油機標準部件生產系統節約發動機生產成本。
目前,Transporter車系新型發動機的功率范圍為62~150 kW,扭矩范圍為220~450 N·m。它以高于76 kW和225 N·m的升功率和升扭矩,成為其細分市場的引領者,新發動機的升功率和升扭矩比原機型提高約13%。起動扭矩超比例提升,雙渦輪增壓系統的VTG高壓級完全發揮出優勢。
降低燃油耗和CO2排放是研發重點之一。通過優化燃燒過程、降低摩擦功和減小換氣損失,新車系的燃油耗比原車系平均降低約14%。Transporter車系的原機型滿足歐5排放法規要求,而所有新機型均滿足歐6排放法規要求。
在相關的所有特性上,如行駛動力性、燃油耗及排放等,量產的所有發動機均優于原機型。由于功率和扭矩得以提升,發動機結構非常緊湊,以及采用乘用車發動機現有的模塊化柴油機標準部件,所以才能在短期內根據需要,設計并實現新型發動機在商用車領域的深入應用。
-
發動機
+關注
關注
33文章
2443瀏覽量
69177 -
功率
+關注
關注
13文章
2057瀏覽量
69788 -
冷卻器
+關注
關注
0文章
85瀏覽量
11911
發布評論請先 登錄
相關推薦
[原創]2011中東商用車展/迪拜商用車展/商用車零配件展/商用車
[原創]2011中東商用車展/迪拜商用車展/商用車零配件展/商用車
2019第六屆上海國際商用車、專用車及零部件展覽會
2019第六屆上海國際商用車、專用車及零部件展覽會
CAN總線在商用車上數據采集實現
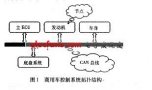
評論