一、機械加工工藝規程設計的內容及步驟
(1)分析零件圖和產品裝配圖設計工藝規程時,首先應分析零件圖和該零件所在部件或總成的裝配圖,了解該零件在部件或總成中的位置和功用以及部件或總成對該零件提出的技術要求,分析其主要技術關鍵和應相應采取的工藝措施。
(2)對零件圖和裝配圖進行工藝審查審查圖紙上的視圖、尺寸公差和技術要求是否正確、統一、完整,對零件設計的結構工藝性進行評價(評價方法及要領參見本章第六節),如發現有不合理之處應及時提出,并同有關設計人員商討圖紙修改方案,報主管領導審批。
(3)由產品的年生產綱領和產品自身特性研究確定零件生產類型(參見第一章第三節)。
(4)確定毛坯提高毛坯制造質量,可以減少機械加工勞動量,降低機械加工成本,但同時可能會增加毛坯的制造成本,須根據零件生產類型和毛坯制造的生產條件確定毛坯制造方法。應當指出,我國機械制造工廠的材料利用率較低,只要有可能,應提倡采用精密鑄造、精密鍛造、冷軋、冷擠壓、粉末冶金等先進的毛坯制造方法。材料利用系數是衡量工藝規程設計是否合理的一個重要參數。
(5)擬訂工藝路線其主要內容包括:選擇定位基準,確定各加工表面的加工方法,劃分加工階段,確定工序集中和分散程度,確定工序順序等。在擬定工藝路線時,須同時提出幾種可能的加工方案,然后通過技術和經濟的對比分析,最后確定一種最為合理的工藝方案。
(6)確定各工序所用機床設備和工藝裝備(含刀具、夾具、量具、輔具等),對需要改裝或重新設計的專用工藝裝備要提出設計任務書。
(7)確定各工序的加工余量,計算工序尺寸及公差。
(8)確定各工序的技術要求及檢驗方法。
(9)確定各工序的切削用量和工時定額。
(10)編制工藝文件。
二、工藝路線的擬訂
擬訂工藝路線是設計工藝規程最為關鍵的一步,需順序完成以下幾個方面的工作。
(一)選擇定位基準
在工藝規程設計中,正確選擇定位基準,對保證零件技術要求、確定加工先后順序有著至關重要的影響。定位基準有精基準與粗基準之分。用毛坯上未經加工的表面作定位基準,這種定位基準稱為粗基準;用加工過的表面作定位基準,這種定位基準稱為精基準。在選擇定位基準時一般都是先根據零件的加工要求選擇精基準,然后再考慮用那一組表面作粗基準才能把精基準加工出來。
1.精基準的選擇原則
選擇精基準一般應遵循以下幾項原則:
(1)基準重合原則
(2)統一基準原則
(3)互為基準原則
(4)自為基準原則
2.粗基準的選擇原則
工件加工的第一道工序所用基準都是粗基準,粗基準選擇得正確與否,不但與第一道工序的加工有關,而且還將對該工件加工的全過程產生重大影響。選擇粗基準,一般應遵循以下幾項原則:
(1)保證零件加工表面相對于不加工表面具有一定位置精度的原則
(2)合理分配加工余量的原則
(3)便于裝夾的原則
(4)在同一尺寸方向上粗基準一般不得重復使用的原則
(二)零件表面加工方法的選擇
(三)加工階段的劃分
當零件的加工質量要求較高時,一般都要經過粗加工、半精加工和精加工等三個階段;如果零件的加工精度要求特別高、表面粗糙度要求特別小時,還要經過光整加工階段。各個加工階段的主要任務是:
(1)粗加工階段
(2)半精加工階段
(3)精加工階段
(4)光整加工階段
將零件的加工過程劃分為幾個加工階段的主要目的是:
(1)保證零件加工質量
(2)有利于及早發現毛坯缺陷并得到及時處理
(3)有利于合理利用機床設備
在選擇加工方法時,一般總是首先根據零件主要表面的技術要求和工廠具體條件,先選定該表面終加工工序加工方法,然后再逐一選定該表面各有關前導工序的加工方法。例如,加工一個精度等級為1T6、表面粗糙度為0.2的鋼件外圓表面,其終加工工序選用精磨,則其前導工序可分別選為粗車、半精車和粗磨(參見圖5-5)。主要表面的加工方案和加工方法選定之后,再選定次要表面的加工方案和加工方法。
(三)加工階段的劃分
當零件的加工質量要求較高時,一般都要經過粗加工、半精加工和精加工等三個階段;如果零件的加工精度要求特別高、表面粗糙度要求特別小時,還要經過光整加工階段。各個加工階段的主要任務是:
(1)粗加工階段高效地切除加工表面上的大部分余量,使毛坯在形狀和尺寸上接近成品零件。
(2)半精加工階段去除粗加工后留下的誤差和缺陷,使被加工工件達到一定精度,為精加工作準備,并完成一些次要表面的加工,例如鉆孔、攻絲、銑鍵槽等。
(3)精加工階段保證各主要表面達到零件圖規定的加工質量要求。
(4)光整加工階段對于精度要求很高(IT5以上)、表面粗糙度值要求很小(0.2μm)的表面,尚需設置光整加工階段,其主要任務是降低表面粗糙度和進一步提高尺寸精度和形狀精度,但一般沒有提高表面間位置精度的作用。
將零件的加工過程劃分為幾個加工階段的主要目的是:
(1)保證零件加工質量粗加工階段要切除加工表面上的大部分余量,切削力和切削熱都比較大,裝夾工件所需夾緊力亦較大,被加工工件會產生較大的受力變形和受熱變形;此外,粗加工階段從工件上切除大部分余量后,殘存在工件中的內應力要重新分布,也會使工件產生變形。如果加工過程不劃分階段,把各個表面的粗、精加工工序混在一起交錯進行,那么安排在工藝過程前期通過精加工工序獲得的加工精度勢必會被后續的粗加工工序所破壞,這是不合理的。加工過程劃分為幾個階段以后,粗加工階段產生的誤差和缺陷,可以通過半精加工和精加工階段逐步予以修正,零件的加工質量可以得到保證。
(2)有利于及早發現毛坯缺陷并得到及時處理粗加工各表面后,由于切除了各加工表面的大部分加工余量,可及早發現毛坯的缺陷(氣孔、砂眼、裂紋和加工余量不夠),以便及時報廢或修補,不會浪費后續精加工工序的制造費用。
(3)有利于合理利用機床設備粗加工工序需選用功率大、精度不高的機床加工,精加工工序則應選用高精度機床加工。在高精度機床上安排做粗加工工作,機床精度會迅速下降,將某一表面的粗、精加工工作安排在同一機床上加工是不合理的。
應當指出,將工藝過程劃分成幾個不同的加工階段進行是對零件整個加工過程而言的,不能拘泥于某一表面的加工,例如,工件的定位基面,在半精加工階段(有時甚至在粗加工階段)中就需要加工得很精確;而在精加工階段中安排某些鉆、攻螺紋孔之類的粗加工工序也是常見的。
當然,劃分加工階段并不是絕對的。在高剛度、高精度機床設備上加工剛性好、加工精度要求不特別高或加工余量不太大的工件就可以不必劃分加工階段;有些精度要求不太高的重型零件,由于運送工件和裝夾工件費時費工,一般也不劃分加工階段,而是在一個工序中完成全部粗加工和精加工工作;在這類加工中,為減少夾緊變形對工件加工精度的影響,一般都在粗加工后松開夾緊裝置,然后用較小的夾緊力重新夾緊工件,繼續進行精加工,這對提高工件加工精度有利。
(四)工序的集中與分散
確定加工方法之后,就要按零件加工的生產類型和工廠(車間)生產條件確定工藝過程的工序數。確定零件加工過程工序數有兩種迥然不同的原則,一種是工序集中原則,另一種是工序分散原則。按工序集中原則組織工藝過程,就是使每個工序所包括的加工內容盡量多些,組成一個集中工序;最大限度的工序集中,就是在一個工序內完成工件所有表面的加工。按工序分散原則組織工藝過程,就是使每個工序所包括的加工內容盡量少些;最大限度的工序分散就是使每個工序只包括一個簡單工步。
按工序集中原則組織工藝過程的特點是:
1)有利于采用自動化程度較高的高效率機床和工藝裝備進行加工,生產效率高;
2)工序數少,設備數少,可相應減少操作工人數和生產面積;
3)工件的裝夾次數少,不但可縮短輔助時間,而且由于在一次裝夾中加工了許多表面,有利于保證各加工表面之間的相互位置精度要求。
按工序分散原則組織工藝過程的特點是:
1)所用機床和工藝裝備簡單,易于調整;
2)對操作工人的技術水平要求不高;
3)工序數多,設備數多,操作工人多,占用生產面積大。
按工序集中原則和工序分散原則組織工藝過程各有特點,生產上都有應用。傳統的以專用機床、組合機床為主體組建的流水生產線、自動生產線基本是按工序分散原則組織工藝過程的,可以實現高效生產,但對產品改型的適應性較差,轉產比較困難。采用數控機床和加工中心加工零件都按工序集中原則組織工藝過程,雖然設備的一次性投資較高,但由于可重組生產的能力較強,生產適應性好,轉產相對容易,仍然受到愈來愈多的重視。
(五)工序先后順序的安排
1.機械加工工序的安排
機械加工工序先后順序的安排,一般應遵循以下幾個原則:
1)先加工定位基面,再加工其它表面;
2)先加工主要表面,后加工次要表面;
3)先安排粗加工工序,后安排精加工工序;
4)先加工平面,后加工孔。
安排數控加工順序,尚須考慮以下情況:(1)在換刀時間大于工作臺轉位時間的情況下,為減少換刀次數和換刀時間,在不影響加工精度的條件下,宜將所有能用同一把刀具加工的表面都集中在一起依次完成;(2)為減少工作臺轉位誤差和由于工作臺轉位帶來的時間損失,在換刀時間小于工作臺轉位時間的情況下,采用工位集中加工原則安排加工順序,即將所有能在一個工位加工的表面通過不斷更換刀具的辦法都集中在同一工位加工;(3)對于位置精度要求很高的孔系,宜在同一工位中安排該孔系各相關表面的加工工作,以消除工作臺轉位重復定位誤差對孔系位置精度要求的影響。
2.熱處理工序及表面處理工序的安排
為改善工件材料切削性能安排的熱處理工序,例如退火、正火、調質等,應在切削加工之前進行。
所謂人工時效,就是將毛坯件以50~100℃/h的速度加熱到500~550℃,保溫3~5h,然后以20~50℃/h的速度隨爐冷卻。所謂自然時效就是將毛坯件在露天放置幾個月到幾年時間,讓毛坯件在自然界經受日曬雨淋的“錘煉”,使材料組織內部應力松弛并逐漸趨于穩定。
3.其它工序的安排
為保證零件制造質量,防止產生廢品,需在下列場合安排檢驗工序:1)粗加工全部結束之后;2)送往外車間加工的前后;3)工時較長工序和重要工序的前后;4)最終加工之后,除了安排幾何尺寸檢驗工序之外,有的零件還要安排探傷、密封、稱重、平衡等檢驗工序。
零件表層或內腔的毛刺對機器裝配質量影響甚大,切削加工之后,應安排去毛刺工序。
零件在進入裝配之前,一般都應安排清洗工序。工件內孔、箱體內腔易存留切屑,研磨、珩磨等光整加工工序之后,微小磨粒易附著在工件表面上,要注意清洗。
在用磁力夾緊的工序之后,要安排去磁工序,不讓帶有剩磁的工件進入裝配線。
(六)機床設備與工藝裝備的選擇
(七)實例
三、加工余量
(一)概述
用去除材料方法制造機器零件時,一般都要從毛坯上切除一層層材料之后最后才能制得符合圖紙規定要求的零件。毛坯上留作加工用的材料層,稱為加工余量。加工余量有總余量和工序余量之分。某一表面毛坯尺寸與零件設計尺寸的差值就是總余量值,以Z0表示。上工序與本工序基本尺寸的差值為本工序的工序余量Zi。
工序余量有單邊余量和雙邊余量之分。
由于工序尺寸有偏差,各工序實際切除的余量值是變化的,工序余量有公稱余量(簡稱余量)、最大余量和最小余量之分。
工序尺寸偏差一般按“入體原則”標注,對被包容尺寸(例如軸徑),上偏差為0,其最大尺寸就是基本尺寸;對包容尺寸(例如孔徑、槽寬),下偏差為0,其最小尺寸就是基本尺寸;孔距類工序尺寸偏差按“對稱偏差”配置。
(二)影響加工余量的因素
為了合理確定加工余量,必須深入了解影響加工余量的各項因素。影響加工余量的因素有以下四個方面:
(1)上工序留下的表面粗糙度值Rz(表面輪廓的最大高度)和表面缺陷層深度Ha
(2)上工序的尺寸公差Ta
(3)Ta值沒有包括的上工序留下的空間位置誤差ea
(4)本工序的裝夾誤差εb
(三)加工余量的確定
確定加工余量有計算法、查表法和經驗估計法等三種方法:計算法;經驗估計法;查表法。
四、工序尺寸及其公差的確定
零件圖上所標注的尺寸公差是零件加工最終所要求達到的尺寸要求,工藝過程中許多中間工序的尺寸公差,必須在設計工藝規程中予以確定。工序尺寸及其公差一般都是通過解算工藝尺寸鏈確定的。為掌握工藝尺寸鏈計算規律,這里先介紹尺寸鏈的概念及尺寸鏈計算方法,然后再就工序尺寸及其公差的確定方法進行論述。
(一)尺寸鏈及尺寸鏈計算公式
1.尺寸鏈的定義
在工件加工和機器裝配過程中,由相互連接的尺寸形成的封閉尺寸組,稱為尺寸鏈。組成尺寸鏈的每一個尺寸,稱為尺寸鏈的環。尺寸鏈中凡屬間接得到的尺寸稱為封閉環,尺寸鏈中凡屬通過加工直接得到的尺寸稱為組成環;組成環按其對封閉環的影響又可分為增環和減環。當其它組成環的大小不變,若封閉環隨著某組成環的增大而增大,則此組成環就稱為增環;若封閉環隨著某組成環的增大而減小,則此組成環就稱為減環。
2.尺寸鏈的分類
按尺寸鏈在空間分布的位置關系,可分為直線尺寸鏈、平面尺寸鏈和空間尺寸鏈。
3.尺寸鏈計算
尺寸鏈計算有正計算、反計算和中間計算等三種類型。已知組成環尺寸、公差求封閉環尺寸、公差的計算方式稱作正計算;已知封閉環尺寸、公差反求各組成環尺寸、公差稱作反計算;已知封閉環及部分組成環的尺寸、公差,求其余的一個或幾個組成環尺寸、公差,稱作中間計算。
尺寸鏈計算有極值法與統計法兩種。用極值法解尺寸鏈是按尺寸鏈各環均處于極值條件來分析計算封閉環尺寸與組成環尺寸之間關系的。用統計法解尺寸鏈則是運用概率論理論來分析計算封閉環尺寸與組成環尺寸之間關系的。
4.用極值法解算直線尺寸鏈基本計算公式
5.用統計法解算直線尺寸鏈基本計算公式
(二)工藝尺寸及其公差的計算實例
1.定位基準與設計基準不重合時工序尺寸公差的計算
2.一次加工滿足多個設計尺寸要求時工序尺寸及其公差的計算
3.用綜合圖表跟蹤法計算工序尺寸及其公差
五、工藝過程的生產率
(一)時間定額所謂時間定額是指在一定生產條件下規定生產一件產品或完成一道工序所需消耗的時間。時間定額是安排作業計劃、進行成本核算的重要依據,也是設計或擴建工廠(或車間)時計算設備和工人數量的依據。時間定額規定得過緊會影響生產工人的勞動積極性和創造性,并容易誘發忽視產品質量的傾向;時間定額規定得過松就起不到指導生產和促進生產發展的積極作用。合理制訂時間定額對保證產品加工質量、提高勞動生產率、降低生產成本具有重要意義。時間定額由以下幾個部分組成:
(1)基本時間
(2)輔助時間
(3)布置工作地時間
(4)休息和生理需要時間
(5)準備與終結時間
(二)提高生產率的工藝途徑
勞動生產率是以工人在單位時間內所生產的合格產品的數量來評定的。不斷提高勞動生產率是降低成本、增加積累和擴大社會再生產的根本途徑。提高勞動生產率是一個與產品設計、制造工藝、組織管理等都有關的綜合性任務,此處僅就提高生產率的工藝途徑作一簡要說明。
1.縮減基本時間的工藝途徑
(1)提高切削用量
(2)縮減工作行程長度
(3)多件加工
2.縮減輔助時間的工藝途徑
(1)直接縮減輔助時間
(2)將輔助時間與基本時間重合
3.縮減布置工作地時間
4.縮減準備終結時間
1)運用成組工藝原理
2)采用可換刀架或刀夾
3)采用刀具微調和快調機構
4)采用數控加工過程擬實技術
六、工藝方案的經濟分析
所謂經濟分析就是通過比較各種不同工藝方案的生產成本,選出其中最為經濟的加工
方案。生產成本包括兩部分費用,一部分費用與工藝過程直接有關,另一部分費用與工藝
過程不直接有關(例如行政人員工資、廠房折舊費、照明費、采暖費等)。與工藝過程直接
有關的費用稱為工藝成本,工藝成本約占零件生產成本的70%~75%。
(一)工藝成本的組成及計算
工藝成本由可變費用與不變費用兩部分組成。
(二)工藝方案的經濟評比
對幾種不同工藝方案進行經濟評比時,有以下兩種不同情況:
1.當需評比的工藝方案均采用現有設備或其基本投資相近時,可用工藝成本評比其優劣。
(1)兩加工方案中少數工序不同,多數工序相同時,可通過計算少數不同工序的單件成本St1與St2進行評比。
(2)兩加工方案中,多數工序不同,少數工序相同時,則以該零件加工全年工藝成本S1與S2進行比較。
2.兩種工藝方案的基本投資差額較大時,則在考慮工藝成本的同時,還要考慮基本投資差額的回收期限。
投資回收期必須滿足以下要求:
1)回收期限應小于專用設備或工藝裝備的使用年限;
2)回收期限應小于該產品的市場壽命(年);
3)回收期限應小于國家所規定的標準回收期,采用專用工藝裝備的標準回收期為2-3年,采用專用機床的標準回收期為4-6年。
七、編制工藝規程文件
工藝規程設計出來以后,須以圖表、卡片和文字材料的形式固定下來,以便貫徹執行,這些圖表、卡片和文字材料統稱為工藝文件。在生產中使用的工藝文件種類很多,這里只介紹兩種最常用的工藝文件。
(1)機械加工工藝過程卡片
(2)機械加工工序卡片
-
零件圖
+關注
關注
0文章
6瀏覽量
7712 -
機械加工
+關注
關注
1文章
70瀏覽量
14064
發布評論請先 登錄
相關推薦
基于綠色機械加工技術的應用與研究
機械加工廠制造工藝過程中熱處理工序位置
機械制造工藝及專用夾具設計指導
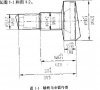
輸出軸零件的機械加工工藝及規程
微機械加工工藝的三維仿真模型及算法
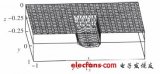
評論