鏜孔加工困難的原因有很多,為了便于正確分析問題,避免采用錯誤的處理方式,下面整理了鏜孔加工要點、及典型鏜孔加工質量問題分析等資料供大家參考。
▲大型工件手動定位
鏜孔加工各步驟要點
1.鏜刀安裝
安裝鏜刀工作部是非常重要的,特別是針對采用偏心原理的工作調整,安裝鏜孔刀后一定要注意觀察鏜刀的主刀刃上平面,是否與鏜刀頭的進給方向在同一水平面上?安裝在同一水平面上才能保證幾個切屑刃是在正常的加工切削角度。
2.鏜刀試鏜孔
鏜刀按工藝制造要求調整預留0.3~0.5mm余量,擴鏜、配鏜孔按初孔余量調整粗鏜余量≤0.5mm,必須保證滿足后續精鏜加工余量。
鏜刀安裝借出后,需進行試鏜驗證鏜刀調試是否滿足粗鏜要求。
3.鏜孔要求
鏜削加工前仔細檢查工裝、工件的定位基準、各定位元件是否穩定可靠。
用卡尺檢測待加工初孔的直徑是多少?測算現在還有多少預留加工余量?
鏜孔加工前檢查設備(主軸)重復定位精度、動態平衡精度是否滿足工藝加工制造要求。
臥加鏜孔試鏜過程中須檢查鏜桿重力懸伸動態跳動值,合理修正切削參數減少加工離心剪切振動影響。
按粗鏜、半精鏜、精鏜步驟合理分配層鏜削余量,粗鏜余量約0.5mm為宜;半精鏜、精鏜余量約0.15mm,避免半精鏜因余量過大產生讓刀現象影響精鏜余量調整精度。
對于難加工材料、高精度鏜孔(容差≤0.02mm)可增加精細鏜加工步驟,鏜削余量不小于0.05mm避免加工面彈性讓刀。
鏜刀對刀過程中,須注意避免鏜刀工作部(刀片和刀座)與對刀塊發生沖擊,損壞刀片及刀座導向槽使鏜刀調整值發生變化影響孔徑加工精度。
鏜削加工過程中注意保持冷卻充分,增加加工部位的潤滑效果以減少切削力。
各加工步驟中嚴格排屑,防止切屑參與二次切削影響孔徑加工精度與表面質量。
鏜削加工過程中隨時檢查刀具(刀片)磨損程度,及時更換以保證孔徑加工質量;精鏜步驟嚴禁更換刀片防止誤差
每步驟加工后須嚴格執行過程質量控制要求,仔細檢測實際加工孔徑并做好記錄,便于分析、調整完善鏜孔加工。
鏜削加工面臨的主要問題
1.刀具磨損
在鏜削加工中,刀具連續切削,易出現磨損和破損現象,降低孔加工的尺寸精度,使表面粗糙度值增大;同時,微調進給單元標定出現異常,導致調整誤差使加工孔徑出現偏差甚至引發產品質量故障。
▲刀片刃口磨損變化
2.加工誤差
鏜孔加工的加工誤差反映在孔加工后的尺寸、形位及表面質量變化上,主要影響因素有:
刀桿長徑比過大或懸伸過長;
刀片材質與工件材質不匹配;
鏜削用量不合理;
余量調整分配不合理;
初孔孔位偏移導致余量周期性變化;
工件材料高剛性或低塑性,刀具或材料呈讓刀趨勢;
3.表面質量
鏜削已加工表面的魚鱗狀或螺紋狀切紋,是比較常見的表面質量現象:
▲主要因刀具的進給和轉速不匹配造成
▲主要因鏜削加工的剛性振動及刀具磨損造成
4.調整失誤
鏜削加工中由于需要操作人員調整分配層吃刀量,在調整分配進刀余量過程中因操作不當易引發加工尺寸精度偏差。
5.測量誤差
鏜削加工中、加工后測量過程的量具使用不當、測量方式錯誤,是鏜削加工中常見的質量隱患(如測量工具失誤、測量方法不正確等)。
拓展:典型鏜孔加工質量問題分析
責任編輯:wv
-
加工
+關注
關注
0文章
86瀏覽量
16369
發布評論請先 登錄
相關推薦
SMT貼片加工虛焊現象:原因分析與解決步驟全解析
PCBA加工打樣要經過哪些流程?每一步驟都很關鍵
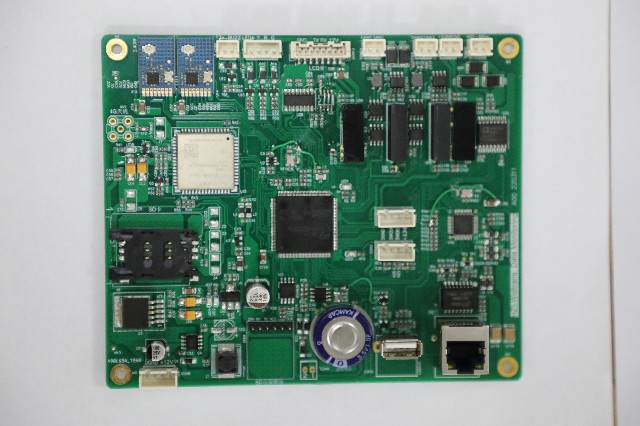
PCBA加工預加熱的目的
MT6825磁編碼IC在自動鏜孔機的應用
數控銑削加工在加工前數控程序需要編程嗎
數控加工工藝分析的一般步驟與方法
數控加工工藝處理的原則和步驟是什么
數控車床t指令對刀步驟
SMT加工廠的貼片加工工藝及可靠性分析
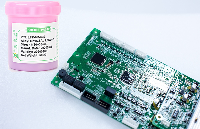
SMT來料加工模式加工流程
機械加工行業MES系統實施步驟
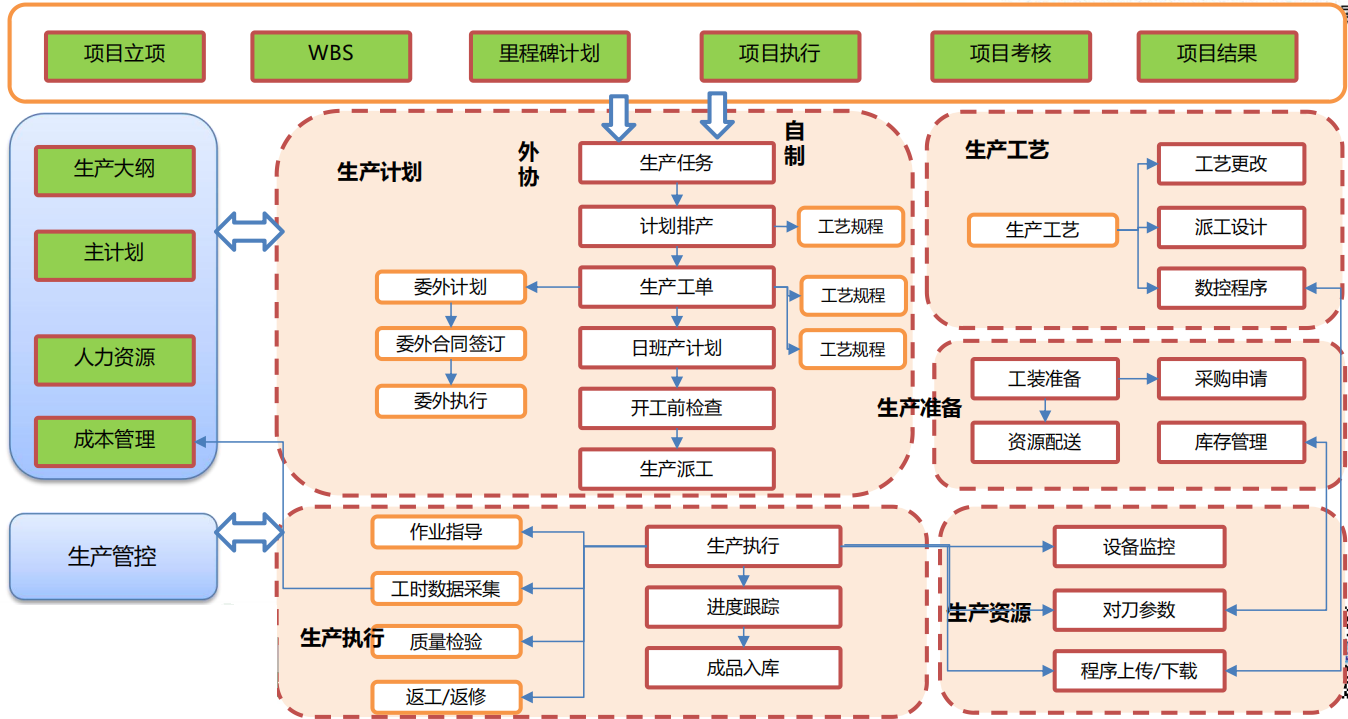
線纜的加工與測試步驟
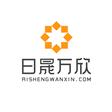
線束加工的基礎步驟講解
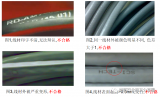
線纜加工的幾個步驟呢?
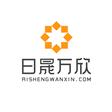
評論