雖然芯片制造商正在推進技術的發展,但是在前道工序(front-end-of-line :FEOL)中微縮晶體管,以及在中間工序(Middle-of-line:MOL)和后道工序(back-end-of-line:BEOL)中改進觸點和連線則變得越來越困難。
在本文中,imec的 CMOS器件技術總監Naoto Horiuchi和納米互連項目總監Zsolt Tokei匯集了他們的專業知識,提出了一份技術路線圖。沿著微縮路線,他們在FEOL中引入了新的器件結構,在MOL和BEOL中引入了新的材料和集成方案。他們討論了各種方案背后的現狀、挑戰和原理——這些方案為芯片行業提供了一條通往1nm技術代際的可能之路。
FEOL、BEOL和MOL——邏輯芯片的關鍵部分
前沿邏輯芯片的制造可以細分為三個獨立的部分:前道工序(FEOL)、中間工序(MOL)和后道工序(BEOL)。
FEOL涵蓋了芯片有源部分的加工,即位于芯片底部的晶體管。晶體管作為電氣開關,使用三個電極進行操作:柵極、源極和漏極。源極和漏極之間的導電通道中的電流可以被“開”和“關”,這一操作由柵極電壓控制。
BEOL是加工的最后階段,指的是位于芯片頂部的互連。互連是復雜的布線方案,它分配時鐘和其他信號,提供電源和地,并將電信號從一個晶體管傳輸到另一個晶體管。BEOL由不同的金屬層、局部(Mx)、中間線、半全局線和全局線組成。總層數可以多達15層,而Mx層的典型數量在3~6層之間。這些層中的每層都包含(單向)金屬線(組織在規則的軌道中)和介電材料。它們通過填充有金屬的通孔結構垂直互連。
FEOL和BEOL由MOL聯系在一起。MOL通常由微小的金屬結構組成,作為晶體管的源極、漏極和柵極的觸點。這些結構連接到BEOL的局部互連層。雖然單元尺寸在微縮,但要連接到的引腳數量大致不變,意味著接觸它們的難度更大。
隨著器件規模不斷縮小到3nm及以下,這些模塊的加工都伴隨著許多挑戰,這迫使芯片制造商在FEOL中采用新的器件架構,以及在BEOL和MOL中采用新的材料和集成方案。
在本文中,我們介紹了imec對擴展路線圖的看法,并深入探討了各種方案。從最先進的主流FEOL、BEOL和MOL技術開始,我們逐步引入新的FEOL器件架構(例如,環繞閘極(GAA) nanosheet、 forksheet,以及互補場效應晶體管 (CFET) 器件)。這些架構將立即影響局部互連層,要求采用新型BEOL材料(如釕(Ru)、鉬(Mo)和金屬合金)和新的集成方案(即混合金屬化(hybrid metallization)、半鑲嵌(semi-damascene)和具有零通孔結構的混合高度)。
在這一激動人心的旅程中,我們還引入了有助于提高MOL連通性的結構微縮助推器(如自對準柵極觸點(SAGC)和埋入式電源線(BPR))。這些助推器還將有助于減少標準單元級的面積,允許減少局部互連級的金屬track數量,這稱為軌道高度微縮。
imec對CMOS技術微縮路線圖的觀點
最先進的主流技術及其微縮瓶頸
(1)FEOL中的FinFET
根據摩爾定律,晶體管尺寸每兩年縮小0.7倍。為了保持這種微縮路徑,業界在幾年前就從 “老式”的平面MOSFET轉向了FinFET晶體管架構。在FinFET中,源極和漏極之間的溝道呈鰭片狀,柵極環繞這個3D通道,從溝道的3個側面提供控制。這種多柵極結構可以消除短溝道效應,短溝道效應在柵極長度減小時開始降低晶體管的性能。
2012年,第一款商用22nm FinFET問世。從那時起,為了提高性能和減小面積,人們對架構進行了改進。例如,鰭片高度增加,以在相同的面積上獲得更高的器件驅動電流。如今,工業界已經有7nm芯片投入生產,其“內部”有FinFET。在最先進節點的單元層面,track高度為6T的標準單元每個器件具有2個鰭片,接觸間距小至57nm。6T的意思是在單元高度范圍內可以容納6條金屬線。
具有2個鰭片的6T標準單元設計(CPP=觸點多晶硅間距;FP=鰭片間距;黑色=金屬-2布線track;紅色=柵極;藍色=柵極觸點;綠色=有源部件(即鰭片);紫色=有源觸點)。
(2)BEOL中的銅基和鈷基雙鑲嵌(dual-damascene)
為了跟上前道工序的面積微縮,BEOL尺寸以更快的速度減小,導致金屬間距越來越小,導線的橫截面積也越來越小。如今,大多數關鍵的本地互連(如M1和M2)的金屬間距都只有40nm。銅基雙鑲嵌(dual damascene)是制造互連的主要工藝流程。
雙鑲嵌始于在結構上沉積低k介電材料。這些低k薄膜旨在降低芯片的電容和延遲。在接下來的步驟中,會形成孔隙和溝槽。最近,所有領先的邏輯制造商都宣布在他們的技術中使用EUV光刻技術,以便在狹窄的間距下保持成本效益。
在圖案化后,人們添加金屬阻擋層,以防止銅原子遷移到低k材料中。通過內襯和銅種子對阻擋層進行涂層后,對結構進行銅電鍍,然后采用化學機械拋光(CMP)步驟來完成雙鑲嵌模塊。
布線擁塞和顯著的RC延遲(由于增加的電阻電容(RC)產品)已成為進一步擴大互連規模的重要瓶頸,推動了在BEOL中引入新材料和集成方案的需求。最近,業界已將Co用作局部的替代金屬,并且一些公司在中間層使用氣隙作為替代的低k介電材料。
(3)減小接觸電阻,提高MOL的連接性
FEOL和BEOL之間的連接由MOL提供。在很長一段時間內,MOL被組織成單層接觸,但現在它擴展到幾個層,包括例如Mint和Vint層。這些層將電信號從晶體管的源極、漏極和柵極傳送到本地互連,反之亦然。
在晶體管方面,源極/漏極接觸電阻已成為芯片行業的重要問題。隨著晶體管尺寸的縮小,可用于制造觸點的面積相應地減小了。由于源極/漏極接觸電阻與接觸面積成正比,這就導致了源極/漏極接觸電阻的急劇增加。多年來,imec開發了改進的源/漏接觸方案,以減小寄生電阻,這主要是通過提高半導體側的摻雜水平,以及優化金屬(通常是過渡金屬硅化物)和半導體之間的界面質量來實現。
為了進一步提高MOL的連通性,我們引入了結構微縮助推器(structural scaling boosters)。其中一個例子是自對準柵極觸點(self-aligned gate contact),它允許將柵極觸點直接放置在有源器件的頂部。這使得柵極接入更加靈活,并減少了整體接觸面積。業界在當今的芯片設計中采用了這種技術,以進一步提高布線能力。
(左)MOL堆棧;(右)自對準柵極觸點。
FEOL、BEOL和MOL的下一個創新選擇
(1)FEOL:垂直堆疊的nanosheet器件,以及后續的forksheet
隨著微縮到5 nm以下,預計FinFET將走到盡頭。在減小柵極長度的情況下,該器件不能提供足夠的溝道靜電控制。除此之外,向更低(5T)track高度標準單元的演進需要向單鰭片器件過渡,即使鰭片高度進一步增加,單鰭片器件也不能提供足夠的驅動電流。
在這里,垂直堆疊的環繞閘極(GAA) nanosheet 晶體管進入了人們的視野。它們可以被認為是FinFET器件的自然演變。想象一下,將一個FinFET側放,并將其分成獨立的水平sheet,這些sheet構成了溝道。由于現在柵極完全包裹在溝道周圍和溝道之間,因此與FinFET相比,可以獲得更優的通道控制。同時,溝道截面在3D體積中的更優化分布,優化了單位面積的有效驅動力。
Imec自2015年以來一直致力于這種架構的研究,從而優化了最關鍵的工藝步驟。制造垂直堆疊的GAA nanosheet晶體管的工藝流程首先是外延沉積多個Si/SiGe層,并形成和填充淺溝隔離(STI)模塊。在后面的步驟中,SiGe層被選擇性地去除,釋放出Si nanosheet 結構。在這些Si nanosheet 層的周圍和中間,以雙重功能置換金屬柵極(RMG)流形成柵極疊層。
除了實現優化的工藝步驟,imec團隊還開發了將垂直nanosheet間距降至10nm以下的工藝。這樣一來,寄生電容就可以大幅降低。如今,一些芯片制造商正準備向這些器件發展,以生產其下一代芯片。
垂直堆疊的GAA nanosheet晶體管的優化:(左)nanosheet形狀控制;(右)nanosheet垂直空間還原分離。
為了將nanosheet器件的可微縮性延伸到2nm節點及以下,imec最近提出了一種替代架構,稱為forksheet器件。在這種架構中,sheet由叉形柵極結構控制,在柵極圖案化之前,通過在pMOS和nMOS器件之間引入介電層來實現。這個介電層從物理上隔離了p柵溝槽和n柵溝槽,使得n-to-p間距比FinFET或nanosheet器件更緊密。根據仿真結果,imec預計這種forksheet具有卓越的面積和性能微縮性(允許trace高度從5T縮減到4.3T),以及更低的寄生電容。在SRAM設計中實現時,有望減少單元面積。
從FinFET到nanosheet,再到forksheet。
(2)BEOL:混合金屬化(hybrid metallization)和半鑲嵌(semi-damascene)
為了與FEOL中實現的面積減小保持同步,最關鍵的局部互連層(M1和M2)的金屬間距最終將變得緊湊至21nm。現在,這些層之間的通孔的臨界尺寸小至12~14nm。在傳統的銅雙鑲嵌集成方案中,在實際的銅金屬化之前,在溝槽和通孔結構內沉積了阻擋層和襯墊層。但在這些狹小的尺寸下,襯墊/阻擋層占據了太多的空間,留給銅填充的空間很小。這會對通孔電阻和可變性產生負面影響,現在通孔電阻和可變性已經成為一種限制因素。此外,由于高電流密度的要求,電遷移可靠性受到挑戰。
克服這一挑戰的一種選擇是混合金屬化,其中替代的通孔金屬(如釕、鎢或鉬)以無障礙的方式連接到銅線的底部。這種結構允許更薄(2納米)的銅線阻擋層,同時保持電遷移可靠性,同時降低通孔的電阻。雖然從電阻的角度來看,這樣的方案很有吸引力,但關鍵是它也是可靠的,這是人們為尋求解決方案而積極研究的領域。
混合金屬化結構的示意圖
對于低于21nm的金屬間距,imec提出半鑲嵌作為一個有趣的選擇。半鑲嵌的關鍵是它允許互連高度增加,同時保持電容的可控性,因此總體上有望獲得RC效益。
半鑲嵌模塊:示意圖和SEM圖片
從工藝技術的角度來看,它使用可圖案化的替代金屬,最終形成氣隙。雙鑲嵌和半鑲嵌的本質區別是省略了金屬的化學機械拋光(CMP)步驟,這是雙鑲嵌工藝流程的最后一步。在半鑲嵌工藝中,通孔以單鑲嵌方式形成圖案,然后用金屬填充和過填充,這意味著金屬沉積繼續進行,直到在電介質上形成一層金屬(即,無勢壘金屬,如釕或鉬)。然后對金屬進行掩蔽和蝕刻,以形成金屬線。通過這種方式,與雙鑲嵌工藝相反,可以形成具有較高縱橫比的線路——因此,電阻較小。在金屬圖案化之后,線條之間的空隙可以由電介質填充,也可以用來在局部層形成部分氣隙。
對于第二代產品,可以預見到完全的氣隙,在更晚的階段,可采用有序金屬合金作為導體。這種順序導致一代接一代的逐步改善。氣隙的使用限制了電容的增加,而電容的增加是由實現更高縱橫比的線引起的。這種針對最關鍵的金屬層M1和M2所設想的半鑲嵌集成方案,可以與上述較不關鍵的互連層的傳統雙鑲嵌或混合金屬化方案相結合。
半鑲嵌的技術選擇
(3)MOL:連接性革命,有微縮助推器的支持
在MOL中,我們已經看到了結構微縮助推器的引入,以提高可布線性。這種連通性的發展將繼續下去,允許MOL層的其他實現,這取決于器件和互連之間的連接需求。例如,forksheet器件架構允許更靈活的柵極連接和柵極切割,從而提高布線靈活性。
另一個新興的助推器是埋入式電源線(buried power rail:BPR)。電源線是供電網絡的一部分,傳統上在芯片的BEOL層(即Mint層和M1層)實現。相反,BPR被埋在芯片的FEOL中,以幫助釋放互連的布線資源。這一具有挑戰性的構造直接影響了FEOL和BEOL的制造。
在VLSI 2020上,imec在FinFET CMOS測試工具中提出了鎢(W)埋地電源線(BPR)集成方案,該方案對CMOS特性沒有產生不利影響。補充評估研究也顯示了在邏輯和SRAM設計中實現BPR作為微縮助推器在系統級的優勢。
這種集成方案可以擴展到所謂的VBPR,在VBPR中,到BPR的通孔現在與MOL層(M0A線)相連。在VLSI 2020上,imec團隊展示了一種鎢基BPR,該BPR與Ru過孔(VBPR)相連,以與Ru M0A線接觸。這種結構獲得了優異的電阻和電遷移效果。
透射電子顯微鏡(TEM)顯示了集成有Si FinFET的W-BPR線。
此外,我們還需要創新來進一步降低源極/漏極的接觸電阻。Imec已經提出了改進的接觸方案,包括環繞接觸(通過金屬的原子層沉積實現)作為金剛石外延接觸的替代物。這再次擴大了接觸面積,因此降低了接觸電阻。
進一步的選擇:繼續向1nm節點邁進
(1)FEOL中的CFET:走向3T邏輯標準單元之路
超過5T后,單元高度的進一步降低現在主要受到可布線性問題的限制,這應該在邏輯塊層面進行評估。優化可布線性將我們帶到了CFET,它將摩爾定律的視界推得更遠。CFET的概念在于將nFET“折疊”在pFET之上(fin-on-fin或sheet-on-sheet),從而充分利用了器件3D微縮的可能性。這種架構最強的優勢是面積擴展,最終可以實現3T邏輯標準單元和SRAM單元,而布局面積卻大大縮小。
CFET架構
在VLSI 2020上,imec展示了CFET器件的第一個實驗概念證明,它是在單片工藝流程中制造的。該團隊設法克服了這一復雜工藝方案的關鍵工藝挑戰,即從大塊襯底開始,從下到上地加工CFET。如今,人們正在探索采用順序CFET作為一種替代的、不太復雜的集成流程。在順序式CFET中,對底層器件(如pFET)進行加工后,再進行晶圓鍵合,形成頂層器件(如nFET)溝道,然后對頂層器件進行進一步加工。順序CFET為頂層器件中使用的溝道材料提供了更靈活的選擇。
(2)BEOL:“零通孔的混合高度”,以及尋找替代導體
金屬線和通孔的電阻和電容仍然是BEOL最關鍵的參數。解決這個問題的一種方法是另一種金屬化結構,稱為“零通孔混合高度”。這種方案可以根據金屬線的應用需求,靈活地將電阻換成電容。
這個想法是將每個金屬層分成三個獨立的子層:一條中心線,以及可能在其上方或下方的延伸。對于每個金屬層,我們現在得出四種可能的情況(僅中心線;中心線+向下延伸;中心線+向上延伸;中心線+向上和向下延伸)。這允許我們在相同的覆蓋區內調整金屬線的高度和縱橫比。
例如,如果該線需要用作對電阻非常敏感的電源線,則可以形成具有高縱橫比(因此電阻小)的線。如果線路需要傳送信號,則僅使用中心線來保持較小的電容。這種結構不僅可以靈活地將電阻換成電容,而且有望提高整體能量和速度。
從制程角度看,不同的高度是通過金屬凹槽刻蝕步驟來實現的。通過一直凹到末端,該線可以用作垂直通孔連接,從而省略了對經典通孔結構的需要。Imec正在解決處理這種“零通孔混合高度”結構帶來的各種挑戰。
概念圖:零通孔混合高度,應用于金屬2層
此外,將標準單元面積減小至3至4 track將要求導體具有極小的電阻。Imec探索了多種新型導體材料,這些材料有望獲得比釕和鉬更好的品質因數。該品質因數定義為體積電阻率乘以金屬中載流子的平均自由程的乘積。令人感興趣的是非常小的尺寸下具有低電阻率的有序二元金屬間化合物。
例如Ru和Al基化合物,例如AlNi或RuV 3,雖然這不是唯一的候選物。自始至終的計算已經顯示出各種金屬在未來互連應用中的良好特性。尋找下一種新的導體并不容易,但令人鼓舞的是,世界各地的一些研發小組已經接受了這一想法,并正在尋找候選物。
從長遠來看,石墨烯/金屬混合導體也是一個有趣的選擇。眾所周知,石墨烯非常薄,具有很高的導電性和導熱性。然而,這種材料沒有足夠的電荷載流子來用作局部互連。但是,有辦法調節電導率。一種方法是使用混合金屬/石墨烯方案,其中金屬(例如,銅、釕、鉬等。)被石墨烯包裹。Imec早些時候展示了這種混合金屬/石墨烯方案的低電阻率和高熱穩定性。
(3)MOL
為了進一步緩解布線擁擠并滿足新提出的晶體管結構的要求,MOL層需要進一步創新。例如,在CFET中,需要為接觸柵極提供新的解決方案,現在,這對于nFET和pFET器件來說是通用的。此外,高縱橫比的通孔將把各種構件互連起來,這些構件現在已經擴展到三維。但是,這些深通孔的主要寄生電阻需要降低。這可以通過引入先進的MOL觸點來實現,例如使用釕。
總結
隨著微縮到5nm以下,芯片制造商可能會逐漸遠離主流技術,例如FinFET(在FEOL中),Cu雙金屬鑲嵌(在BEOL中)和傳統的觸點方案(在MOL中)。我們介紹了FEOL、BEOL和MOL的下一步創新方案,提供了通往1nm技術節點的可能途徑。
責任編輯:YYX
-
芯片
+關注
關注
454文章
50430瀏覽量
421872 -
時鐘
+關注
關注
10文章
1720瀏覽量
131366 -
1nm
+關注
關注
0文章
15瀏覽量
3910
原文標題:關注 | 1nm將如何實現?
文章出處:【微信號:wc_ysj,微信公眾號:旺材芯片】歡迎添加關注!文章轉載請注明出處。
發布評論請先 登錄
相關推薦
臺積電1nm進展曝光!預計投資超萬億新臺幣,真有必要嗎?
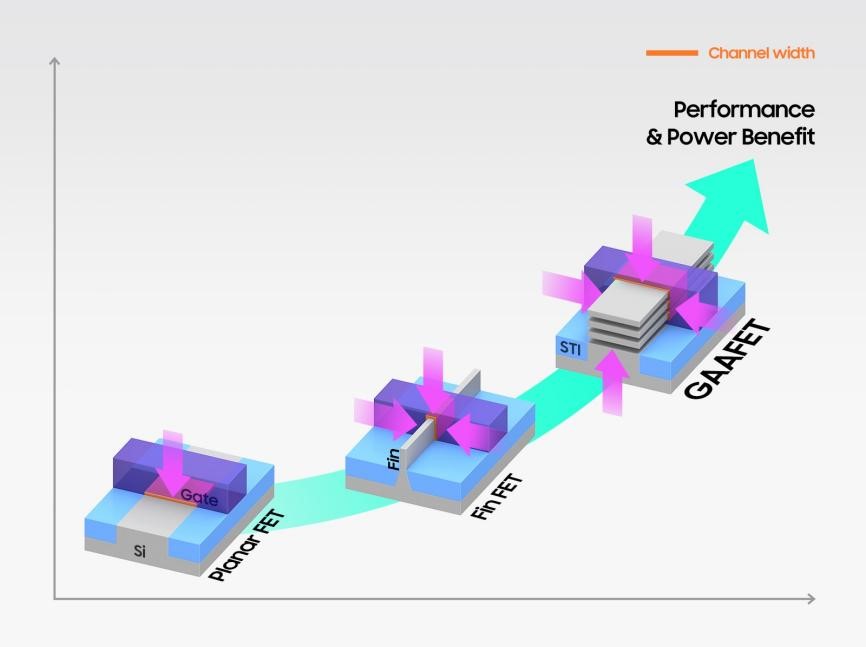
2024 Arm Tech Symposia圓滿落幕,思爾芯創新方案備受矚目
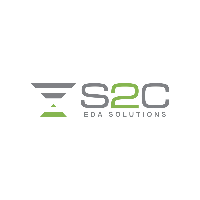
面向未來的智能視覺參考設計與汽車架構,思爾芯提供基于Arm技術的創新方案
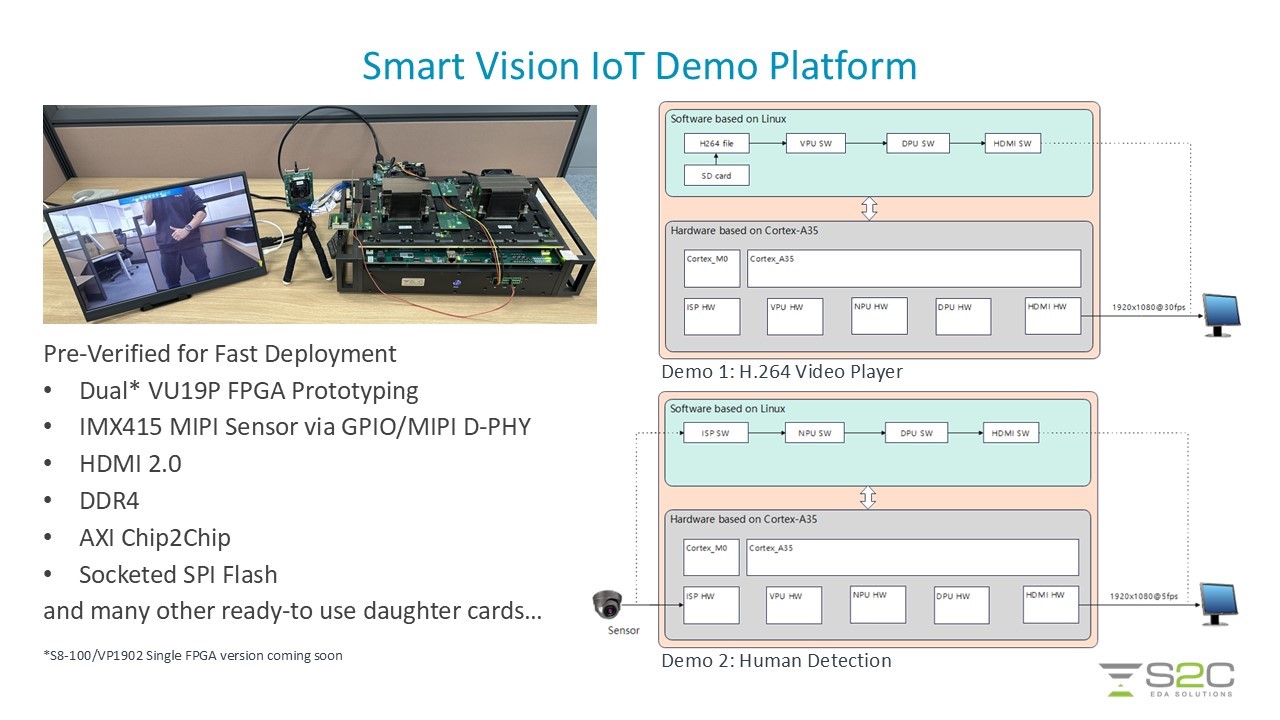
中興通訊展示創新方案與實踐成果
河南移動與中興通訊聯合發布5G-A×AI六大創新方案
中國移動智能水表創新方案正式發布
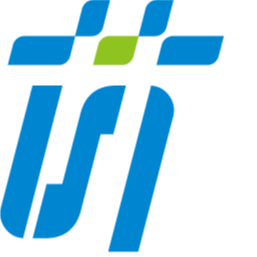
鼎陽科技展示嵌入式測量技術創新方案
兆易創新80余款創新方案亮相2024慕尼黑上海電子展
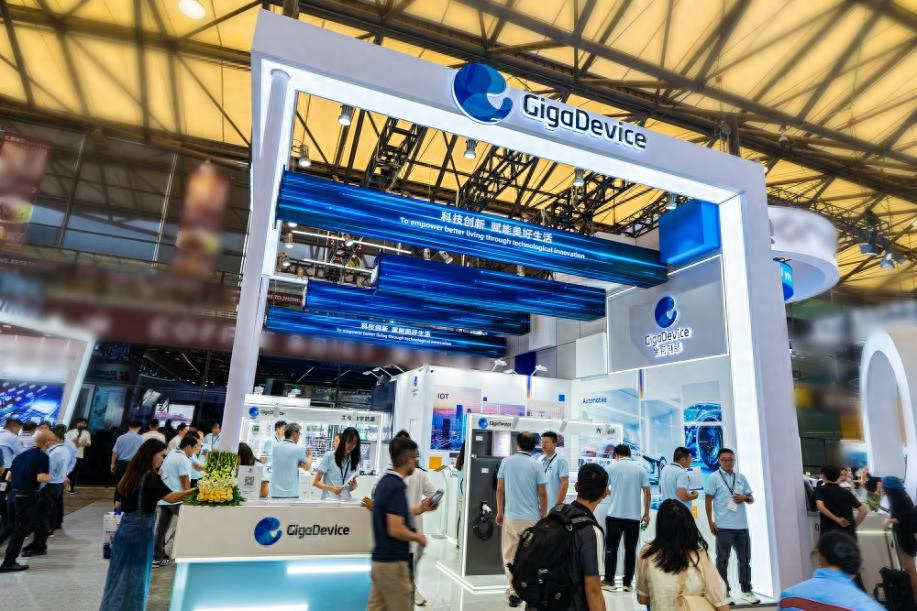
兆易創新閃耀2024慕尼黑上海電子展,以80余款創新方案引領智能未來
MWCS 2024 | 廣和通榮獲邊緣AI計算最佳創新方案
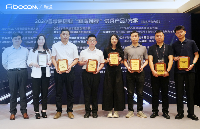
MWCS 2024 廣和通榮獲邊緣AI計算最佳創新方案
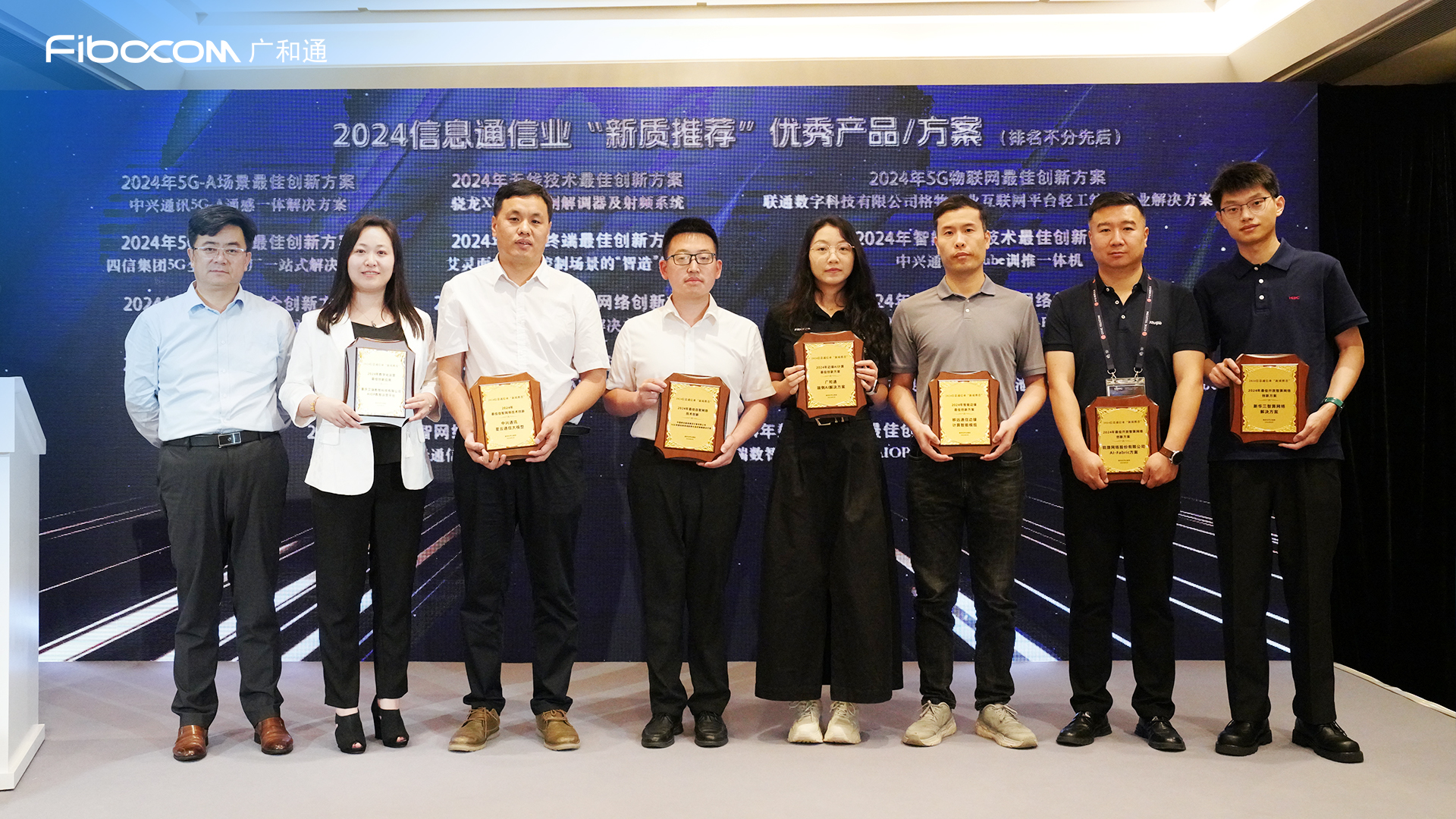
評論