自動化精密制造推動了當今許多高科技設備的發展和廣泛使用。時尚精美的手機仰賴復雜的金屬加工工藝和精細表面處理能力來生產機械元件制造所需的芯片和模具。手機中微小但強大的電子器件的生產,則要依靠自動化IC晶圓處理和精密線焊設備。大型設備同樣需要高精度和高質量表面處理。例如,現代噴氣發動機依賴精細平衡和精密匹配的渦輪葉片來實現高燃油效率和安靜工作。先進的電子控制和形狀復雜的精密發動機部件可優化燃燒過程,提高汽車發動機的燃油效率。
銑床沿預定路徑移動高速旋轉的切割工具,對固體金屬塊進行切削,從而生產金屬制品部件。精密加工是一個多步驟過程,先是粗略切削,然后經過多道精細切削才能達到要求。多個電機驅動進給主軸和多個絲杠來定位工具頭。電機位置與速度伺服驅動器的功率和剛度決定了支持特定表面處理精度水平的最大切削速率。因此,高性能電機驅動器可提高切削速率或減少切削次數,從而直接影響到銑削過程效率。每次操作都選擇最佳運動方案,以及盡量縮短刀具更換時間,同樣可以提高生產率和能效。生產質量取決于絲杠的精度和電機驅動軸位置與速度控制。最新銑床有五個或更多的控制軸,支持以最少的工件設置操作次數加工出復雜的形狀。大批量生產線所用的專用加工中心甚至包括更多的伺服驅動器,支持多個金屬加工并行操作和類機器人功能,使加工過程實現完全自動化。機器設計人員面臨的挑戰是如何讓多個伺服驅動軸的操作和運動方案同步,從而在維持產品質量不變的同時,使機器吞吐效率大化。
精密運動控制
控制現代工廠所用自動化機器的各種元件,中央數字控制器(CNC)或可編程邏輯控制器(PLC)管理機器操作,并且為機器中每個伺服電機軸產生運動軌跡規劃。每個伺服驅動器包括多個控制環路來管理機械系統動態特性、電磁扭矩產生和電路動態特性。各控制元件的性能對機器吞吐效率和表面處理質量至關重要。計算機輔助制造(CAM)工具根據產品圖紙、材料特性、機器和刀具能力,產生成品所需的機加工操作組合運動方案。然后,由自動化機器執行這些方案來制造產品。
完整的機器控制功能包括多個級聯控制環路。考慮絲杠(用于將旋轉轉變為線性運動)提供的傳動裝置,CNC將機器空間(x、y和z)運動配置轉換為每個電機軸的(θ或ω)運動配置。每種運動配置由時間中的位置或速度集合來定義。軸間的時序同步非常重要,因為時序誤差對一個軸的影響與位置和速度誤差相同。
伺服驅動速度環路的功能是計算跟隨目標速度曲線所需的電機扭矩指令(T*)。成品的精度和表面質量取決于機器能否精確地引導切削工具沿目標路徑移動。機加工操作的挑戰在于金屬切削過程是非連續的,因為材料以碎片形式脫落,因此,伺服驅動負載也會迅速變化。速度環路必須能夠在切削操作中維持恒定的速度而不受負載變化的影響,并且在刀具更換操作中能夠迅速響應速度指令。低速時的控制質量高度取決于位置反饋的分辨率,因為需要高采樣速率微分器來產生高動態速度信號。機床驅動所用的精密編碼器采用快速模數轉換器在編碼器計數之間插值,以提供更高的分辨率。例如,一個4096線編碼器采用簡單的數字接口時,可提供14位/轉的位置分辨率,而采用插值方法時,其分辨率至少可擴展至22位/轉。位置分辨率提高到22位之后,在4位速度分辨率和1 RPM的條件下,采樣速率可達4 kHz,而之前在4位速度分辨率和60 RPM的條件下,采樣速率只有1 kHz。
在永磁交流伺服電機中,為了高效率、高動態地產生扭矩,要求正弦定子電流與轉子磁體角位置對齊。電流和磁場對齊控制確保電機扭矩滿足速度環路的動態要求。PWM和逆變器反饋隔離模塊包括在電路控制功能中。三相功率逆變器將所需的電壓施加于電機繞組以驅動目標繞組電流。電流反饋功能將繞組電流測量與高壓逆變器隔離,并向磁場對齊模塊提供反饋信號。電流反饋的精度決定扭矩產生的質量,因為反饋中的增益、失調或非線性誤差會產生紋波扭矩,進而表現為對速度控制器的負載干擾。在某些精密伺服驅動中,有一個附加環路也會補償定子繞組線槽與轉子磁鐵相互作用所引起的伺服電機內部扭矩紋波。所有這些都能改善電機的低速性能,最終增強成品的精度和表面質量。
驅動架構
如上所述,驅動系統性能由多個方面決定,例如控制架構、電機設計、功率電路、反饋傳感器和控制處理器。面對日益提高的驅動性能、靈活性和成本要求,以及模擬和數字電子控制元件的進步,控制架構在不斷發展。基于模擬電路的傳統伺服控制已被使用嵌入式處理器的數字控制所取代。另外,CNC的速度指令信號原先是精密模擬信號,現已變為數據包通過實時(RT)工業網絡發送。因此,除了控制和功率電路以外,現代伺服驅動系統還包括通信接口。
驅動系統永遠存在的電路設計挑戰是如何將高壓功率電路與用戶連接的控制和通信電路安全地隔離。有一個常見架構可降低逆變器信號隔離困難,即功率電路與控制處理器接地直連,控制處理器與通信接口之間使用隔離柵。伺服驅動應用更常見的架構選擇是將安全隔離柵放在功率級與控制處理器之間,而控制處理器與通信接口直連。還有一種不那么常見的架構,即把安全隔離柵分散在功率、控制和通信之間。這會降低每個隔離柵的隔離標準要求,而且可以縮小系統的整體尺寸。
一個隔離控制架構實例,其中逆變器柵極驅動、電壓反饋和電機電流反饋信號與控制處理器相隔離,但直連位置反饋傳感器、用戶和通信接口。這種架構不僅為控制電路提供安全隔離,還能抑制高壓開關電源逆變器所產生的電路噪聲。電機電流反饋由繞組分流器和隔離式Σ-Δ調制器產生,這些調制器提供增益匹配、非常低的失調和非常高的線性度。完整的電流反饋信號路徑還包括控制處理器,其上的可編程sinc3濾波器還具有輸出短路檢測功能。模擬信號隔離器提供逆變器總線電壓隔離,此信號由嵌入式采樣ADC獲得。控制處理器上的正交編碼器外設(QEP)支持簡單的數字編碼器接口,但帶插值電路的更高分辨率編碼器通常使用高速串行接口,以便按需發送位置和速度信息。
上例中的實時(RT)以太網接口由一個FPGA電路提供,以便能夠靈活地支持自動化市場上的多種工業網絡協議。FPGA管理來自網絡的實時數據包,而控制處理器則具備帶寬和存儲器來支持協議棧的管理。許多此類協議支持抖動要求小于1 μs的同步實時控制,這會給通信接口帶來非常重的處理負擔。如前所述,這種對伺服驅動同步的要求,與伺服驅動性能一樣重要。在現代自動化機加工系統中,為了實現高生產率和高質量成品,以上二者不可或缺。自動化系統的一個新興趨勢是利用單個處理器控制兩到三個伺服電機并依賴單個實時通信接口。現在,高速專用信號處理器(ASSP)便支持這種趨勢,例如ADPS-CM408,其包括一個高速浮點內核和多組電機控制與通信外設。
工業電機驅動應用展現出來的多種多樣的架構,突出說明了許多重要的電機驅動系統設計挑戰仍然存在這一事實。隨著可用控制處理和傳感器反饋信號帶寬的增加,自動化行業對更高精度和動態響應的需求不斷提高。新材料、傳感器、控制、通信電路架構,甚至更多的算法和軟件,很可能會繼續滿足自動化生產行業對更高生產率和更高質量的需求。
參考文獻
Will Dalrymple,“高速移動的機械。”Machinery.co.uk,第173卷,第4232期,2015年1月。
Ferrari C.B.,“無與倫比的精度。”運動世界,第9卷,第2期,2010年。
作者簡介
Aengus Murray是ADI公司汽車、能源和傳感器部門的電機和電源控制應用經理。他負責工業電機和電源控制的整個ADI信號鏈產品。Murray博士擁有愛爾蘭都柏林大學電氣工程學士和博士學位。他在功率電子行業擁有超過30年的豐富經驗,曾先后在International Rectifier、Kollmorgen IndustrialDrives和都柏林城市大學工作。
審核編輯 黃昊宇
-
電機
+關注
關注
142文章
8940瀏覽量
145136 -
伺服控制系統
+關注
關注
1文章
54瀏覽量
12241
發布評論請先 登錄
相關推薦
閉環伺服控制系統原理及特點
運動控制系統的組成與作用
基于S3C2440和專用DSP的嵌入式四軸運動控制器
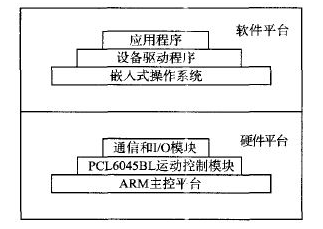
評論