鋰離子電池原理及工藝流程
一、 原理
1.0 正極構造
LiCoO2(鈷酸鋰)+導電劑(乙炔黑)+粘合劑(PVDF)+集流體(鋁箔)
2.0 負極構造
石墨+導電劑(乙炔黑)+增稠劑(CMC)+粘結劑(SBR)+ 集流體(銅箔)
3.0工作原理
3.1 充電過程
如上圖一個電源給電池充電,此時正極上的電子e從通過外部電路跑到負極上,正鋰離子Li+從正極“跳進”電解液里,“爬過”隔膜上彎彎曲曲的小洞,“游泳”到達負極,與早就跑過來的電子結合在一起。
正極上發生的反應為
LiCoO2=充電=Li1-xCoO2+Xli++Xe(電子)
負極上發生的反應為
6C+XLi++Xe=====LixC6
3.2 電池放電過程
放電有恒流放電和恒阻放電,恒流放電其實是在外電路加一個可以隨電壓變化而變化的可變電阻,恒阻放電的實質都是在電池正負極加一個電阻讓電子通過。由此可知,只要負極上的電子不能從負極跑到正極,電池就不會放電。電子和Li+都是同時行動的,方向相同但路不同,放電時,電子從負極經過電子導體跑到正極,鋰離子Li+從負極“跳進”電解液里,“爬過”隔膜上彎彎曲曲的小洞,“游泳”到達正極,與早就跑過來的電子結合在一起。
二、 工藝流程
三、 電池不良項目及成因:
1.容量低
產生原因:
a. 附料量偏少;b. 極片兩面附料量相差較大;c. 極片斷裂;d. 電解液少;e. 電解液電導率低;f. 正極與負極配片未配好;g. 隔膜孔隙率小;h. 膠粘劑老化→附料脫落;i.卷芯超厚(未烘干或電解液未滲透)j. 分容時未充滿電;k. 正負極材料比容量小。
2.內阻高
產生原因:
a. 負極片與極耳虛焊;b. 正極片與極耳虛焊;c. 正極耳與蓋帽虛焊;d. 負極耳與殼虛焊;e. 鉚釘與壓板接觸內阻大;f. 正極未加導電劑;g. 電解液沒有鋰鹽;h. 電池曾經發生短路;i. 隔膜紙孔隙率小。
3.電壓低
產生原因:
a. 副反應(電解液分解;正極有雜質;有水);b. 未化成好(SEI膜未形成安全);c. 客戶的線路板漏電(指客戶加工后送回的電芯);d. 客戶未按要求點焊(客戶加工后的電芯);e. 毛刺;f. 微短路;g. 負極產生枝晶。
4.超厚
產生超厚的原因有以下幾點:
a. 焊縫漏氣;b. 電解液分解;c. 未烘干水分;d. 蓋帽密封性差;e. 殼壁太厚;f. 殼太厚;g. 卷芯太厚(附料太多;極片未壓實;隔膜太厚)。
5.成因有以下幾點
a. 未化成好(SEI膜不完整、致密);b. 烘烤溫度過高→粘合劑老化→脫料;c. 負極比容量低;d. 正極附料多而負極附料少;e. 蓋帽漏氣,焊縫漏氣;f. 電解液分解,電導率降低。
6.爆炸
a. 分容柜有故障(造成過充);b. 隔膜閉合效應差;c. 內部短路
7.短路
a. 料塵;b. 裝殼時裝破;c. 尺刮(小隔膜紙太小或未墊好);d. 卷繞不齊;e. 沒包好;f. 隔膜有洞;g. 毛刺
8.斷路
a) 極耳與鉚釘未焊好,或者有效焊點面積小;
b) 連接片斷裂(連接片太短或與極片點焊時焊得太靠下)
鋰離子電池的容量在很大程度上取決于負極的鋰嵌入量,其負極材料應滿足如下要求:
⑴鋰的脫嵌過程中電極電位變化較小,并接近金屬鋰;
⑵有較高的比容量;
⑶較高的充放電效率;
⑷在電極材料的內部和表面Li+均具有較高的擴散速率;
⑸較高的結構、化學和熱穩定性;
⑹價格低廉,制備容易。目前有關鋰離子電池負極材料的研究工作主要集中在碳材料和具有特殊結構的其它金屬氧化物。
一般制備負極材料的方法如下:
①在一定高溫下加熱軟碳得到高度石墨化的碳;
②將具有特殊結構的交聯樹脂在高溫下分解得到硬碳;
③高溫熱分解有機物和高聚物制備含氫碳。
碳負極材料要克服的困難就是容量循環衰減的問題,即由于固體電解質相界面膜(Solid electrolyte interphase,簡稱SEI)的形成造成不可逆容量損失。因此制備高純度和規整的微結構碳負極材料是發展的一個方向。
電池基本知識及生產控制
一、電芯原理
鋰離子電芯的反應機理是隨著充放電的進行,鋰離子在正負極之間嵌入脫出,往返穿梭電芯內部而沒有金屬鋰的存在,因此鋰離子電芯更加安全穩定。
二、電芯的構造
電芯的正極是LiCoO2加導電劑和粘合劑,涂在鋁箔上形成正極板,負極是層狀石墨加導電劑及粘合劑涂在銅箔基帶上,目前比較先進的負極層狀石墨顆粒已采用納米碳。
根據上述的反應機理,正極采用LiCoO2、LiNiO2、LiMn2O2,其中LiCoO2本是一種層結構很穩定的晶型,但當從LiCoO2拿走XLi后,其結構可能發生變化,但是否發生變化取決于X的大小。通過研究發現當X》0.5時Li1-XCoO2的結構表現為極其不穩定,會發生晶型癱塌,其外部表現為電芯的壓倒終結。所以電芯在使用過程中應通過限制充電電壓來控制Li1-XCoO2中的X值,一般充電電壓不大于4.2V那么X小于0.5 ,這時Li1-XCoO2的晶型仍是穩定的。負極C6其本身有自己的特點,當第一次化成后,正極LiCoO2中的Li被充到負極C6中,當放電時Li回到正極LiCoO2中,但化成之后必須有一部分Li留在負極C6中,心以保證下次充放電Li的正常嵌入,否則電芯的壓倒很短,為了保證有一部分Li留在負極C6中,一般通過限制放電下限電壓來實現。所以鋰電芯的安全充電上限電壓≤4 .2V,放電下限電壓≥2.5V。
三、電芯的安全性
電芯的安全性與電芯的設計、材料及生產工藝生產過程的控制等因素密切相關。在電芯的充放電過程中,正負極材料的電極電位均處于動態變化中,隨著充電電壓的增高,正極材料(LixCoO2)電位不斷上升,嵌鋰的負極材料(LixC6)電位首先下降,然后出現一個較長的電位平臺,當充電電壓過高( 》4.2V)或由于負極活性材料面密度相對于正極材料面密度(C/A)比值不足時,負極材料過度嵌鋰,負極電位則迅速下降,使金屬鋰析出(正常情況下則不會有金屬鋰的的析出),這樣會對電芯的性能及安全性構成極大的威脅。電位變化見下圖:
在材料已定的情況下,C/A太大,則會出現上述結果。相反,C/A太小,容量低,平臺低,循環特性差。這樣,在生產加工中如何保證設計好的C/A比成了生產加工中的關鍵。所以在生產中應就以下幾個方面進行控制:
1.負極材料的處理
1)將大粒徑及超細粉與所要求的粒徑進行徹底分離,避免了局部電化學反應過度激烈而產生負反應的情況,提高了電芯的安全性。
2)提高材料表面孔隙率,這樣可以提高10%以上的容量,同時在C/A 比不變的情況下,安全性大大提高。處理的結果使負極材料表面與電解液有了更好的相容性,促進了SEI膜的形成及穩定上。
2.制漿工藝的控制
1)制漿過程采用先進的工藝方法及特殊的化學試劑,使正負極漿料各組之間的表面張力降到了最低。提高了各組之間的相容性,阻止了材料在攪拌過程“團聚”的現象。
2)涂布時基材料與噴頭的間隙應控制在0.2mm以下,這樣涂出的極板表面光滑無顆粒、凹陷、劃痕等缺陷。
3)漿料應儲存6小時以上,漿料粘度保持穩定,漿料內部無自聚成團現象。均勻的漿料保證了正負極在基材上分布的均勻性,從而提高了電芯的一致性、安全性。
3.采用先進的極片制造設備
1)可以保證極片質量的穩定和一致性,大大提高電芯極片均一性,降低了不安全電芯的出現機率。
2)涂布機單片極板上面密度誤差值應小于±2%,極板長度及間隙尺寸誤差應小于2mm。
3)輥壓機的輥軸錐度和徑向跳動應不大于4μm,這樣才能保證極板厚度的一致性。設備應配有完善的吸塵系統,避免因浮塵顆粒而導致的電芯內部微短路,從而保證了電芯的自放電性能。
4)分切機應采用切刀為輥刀型的連續分切設備,這樣切出的極片不存在荷葉邊,毛刺等缺陷。同樣設備應配有完善的吸塵系統,從而保證了電芯的自放電性能。
4.先進的封口技術
目前國內外方形鋰離子電芯的封口均采用激光(LASER)熔接封口技術,它是利用YAG棒(釔鋁石榴石)激光諧振腔中受強光源(一般為氮燈)的激勵下發出一束單一頻率的光(λ=1.06mm)經過諧振折射聚焦成一束,再把聚焦的焦點對準電芯的筒體和蓋板之間,使其熔化后親 合為一體,以達到蓋板與筒體的密封熔合的目的。為了達到密封焊,必須掌握以下幾個要素:
1)必須有能量大、頻率高、聚焦性能好、跟蹤精度高的激光焊機。
2)必須有配合精度高的適用于激光焊的電芯外殼及蓋板。
3)必須有高統一純度的氮氣保護,特別是鋁殼電芯要求氮氣純度高,否則鋁殼表面就會產生難以熔化的Al2O3(其熔點為2400℃)。
四、電芯膨脹原因及控制
鋰離子電芯在制造和使用過程中往往會有腫脹現象,經過分析與研究,發現主要有以下兩方面原因:
1.鋰離子嵌入帶來的厚度變化
電芯充電時鋰離子從正極脫出嵌入負極,引起負極層間距增大,而出現膨脹,一般而言,電芯越厚,其膨脹量越大。
2.工藝控制不力引起的膨脹
在制造過程中,如漿料分散、C/A比離散性、溫度控制都會直接影響電芯電芯的膨脹程度。特別是水,因為充電形成的高活性鋰碳化合物對水非常 敏感,從而發生激烈的化學反應。反應產生的氣體造成電芯內壓升高,增加了電芯的膨脹行為。所以在生產中,除了應對極板嚴格除濕外,在注液過程中更應采用除濕設備,保證空氣的干燥度為HR2%,露點(大氣中的濕空氣由于溫度下降,使所含的水蒸氣達到飽和狀態而開始凝結時的溫度)小于-40℃。在非常干燥的條件下,并采取真空注液,極大地降低了極板和電解液的吸水機率。
五、鋁殼電芯與鋼殼電芯安全性比較
鋁殼相對于鋼殼具有很高的安全優勢,以下是不同的壓力實驗:
注:壓力是電芯壓力為電芯內部之壓力(單位:Kg),表內數據為電芯之厚度(單位:mm)由此可見鋼殼對內壓反映十分遲鈍,而鋁殼對內壓反應卻十分敏銳。因此從厚度上就基本能判斷出電芯的內壓,而鋼殼電芯往往隱含著內壓帶來的不安全隱患。其中鋼殼電芯型號為063448。
六、 各工序控制重點
(一) 配料:
1.溶液配制:
a) PVDF(或CMC)與溶劑NMP(或去離子水)的混合比例和稱量;b) 溶液的攪拌時間、攪拌頻率和次數(及溶液表面溫度);c) 溶液配制完成后,對溶液的檢驗:粘度(測試)溶解程度(目測)及擱置時間;d) 負極:SBR+CMC溶液,攪拌時間和頻率。
2.活性物質:
a) 稱量和混合時監控混合比例、數量是否正確;b) 球磨:正負極的球磨時間;球磨桶內瑪瑙珠與混料的比例;瑪瑙球中大球與小球的比例;c) 烘烤:烘烤溫度、時間的設置;烘烤完成后冷卻后測試溫度。d) 活性物質與溶液的混合攪拌:攪拌方式、攪拌時間和頻率。e) 過篩:過100目(或150目)分子篩。f) 測試、檢驗:
對漿料、混料進行以下測試:固含量、粘度、混料細度、振實密度、漿料密度。
(二)涂布
1.集流體的首檢:
a) 集流體規格(長寬厚)的確認;b) 集流體標準(實際)重量的確認;c) 集流體的親(疏)水性及外觀(有無碰傷、劃痕和破損)。
2.敷料量(標準值、上、下限值)的計算:
a) 單面敷料量(以接近此標準的極片厚度確定單面厚度);b) 雙面敷料量(以最接近此標準的極片厚度確定雙面的極片厚度。)
3.漿料的確認:是否過稠(稀)流動性好,是否有顆粒,氣泡過多,是否已干結。
4.極片效果:
a) 比重(片厚)的確認;b) 外觀:有無劃線、斷帶、結料(滾輪或極片背面)是否積料過厚,是否有未干透或烤焦,有無露銅或異物顆粒;
5.裁片:規格確認有無毛刺,外觀檢驗。
(三)制片(前段):
1.壓片:
a) 確認型號和該型號正、負極片的標準厚度;b) 最高檔次極片壓片后(NO.1或NO.1及NO.2)的厚度、外觀有無變形、起泡、掉料、有無粘機、壓疊。c) 極片的強度檢驗;
2.分片:
a) 刀口規格、大片極片的規格(長寬)、外觀確認;b) 分出的小片寬度;c) 分出的小片有無毛刺、起皺、或裁斜、掉料(正)。
3.分檔稱片:
a) 稱量有無錯分;b) 外觀檢驗:尺寸超差(極片尺寸、掉料、折痕、破損、浮料、未刮凈等)。
4.烘烤:
a) 烤箱溫度、時間的設置;b) 放N2、抽真空的時間性效果(目測儀表)及時間間隔。
(四)制片后段
1.鋁帶、鎳帶的長度、寬度、厚度的確認;
2.鋁帶、鎳帶的點焊牢固性;
3.膠紙必須按工藝要求的公差長度粘貼;
4.極片表面不能有粉塵。
(五)蓋帽
1.裁連接片:測量尺寸規格、檢查有無毛刺、壓傷;
2.清洗連接片:檢查連接片是否清洗干凈;
3.連接片退火:檢查有無用石墨粉覆蓋,烤爐溫度,放入取出時間;
4.組裝蓋帽:檢查各種配件是否與當日型號相符,裝配是否到位;
5.沖壓蓋帽:檢查沖壓高度及外觀;
6.全檢:對前工序員工自檢檢查的效果進行復核,防止不良品流入下一工序;
7.折連接片:檢查有無漏折、斷裂、有無折到位;
8.點蓋帽:檢查有無漏點、虛點、點穿;
9.全檢:對前工序員工自檢檢查的效果進行復核,防止不良品流入下一工序;
10.套套管:檢查尺寸、套管位置;
11.烘烤:烘烤溫度、時間、烘烤效果。
(六)卷繞
1.各型號的識別、隔膜紙、卷尺的規格、鋼(鋁)殼的卷繞注意事項;
2.結存極片的標識狀態;
3.點負極的牢固度(鋼、鋁殼);鋁殼正極的牢固性、負極的外觀;
4.絕緣墊片的放置;
5.折、壓合蓋帽(鋁殼)注意雜物外露和鋁殼外觀的維護;
6.定蓋工位:偏移度。
注意先下拉先生產。
(七)焊接
1.鋼、鋁殼電池焊接時注意沙孔;
2.焊接鋁殼的調試、焊接時抽查的測試;
3.檢漏工位;
4.打膠。
5.注意先下拉先生產。
(八)注液
1.各種型號注液量;
2.手套箱內的濕度和室內濕度;
3.電池水分測試及放氣和抽真空時間;
4.烘烤前電池在烤箱放置注意事項;
5.烘烤12小時后電池上下層換位;
6.電池注液前后的封口。
(九)檢測
1.分容、化成參數的設置;
2.化成時電解液流出員工有沒有及時擦掉;
3.監督生產部新員工的操作;
4.注液組下來的電芯上注液孔是否有膠紙脫落;
5.各種實驗電池是否明顯標識區分;
6.提前亮燈的點要查明原因;
7.爆炸后該點的校對;
8.鋼、鋁殼柜的區分;
9.封口時哪些型號要倒轉來擠壓
10.封口擠壓是否使鋁電芯變形;
11.封口后上否及時清洗;
12.夾具頭是否清潔,是否有銹蝕;
13.連接電腦的柜子爆炸后電壓的查詢,該點電壓電流曲線的情況匯的;
14.擱置、老化和封口區的環境溫濕度。
(十)包裝
1.對有的客戶抱怨過容量低的要加2分鐘容量;
2.對天宇這個客戶要控制尺寸的下限;
3.型號電池更改時是否清理整條拉,防止混料;
4.檢出的不良品是否用紅色周轉盒子裝,是否明顯標識;
5.訂單上有特別要求的是否得到員工的理解和執行;
6.噴碼內容是否正確,噴碼方向和位置是否正確;
7.壓板和鉚釘上是否有膠;
8.檢測儀器是否在有效期內,防止失準儀器在線上使用(針對所有工位)。
化學電源的組成 化學電源在實現能量的轉換過程中,必須具有兩個必要的條件:
一。 組成化學電源的兩個電極上進行的氧化還原過程,必須分別在兩個分開的區域進行,這一點區別于一般的氧化還原反應。
二。 兩電極的活性物質進行氧化還原反應時所需電子必須由外線路傳遞,這一點區別于金屬腐蝕過程的微電池反應。
為了滿足以上的條件,任何一種化學電源均由以下四部分組成:
1、 電極電池的核心部分,它是由活性物質和導電骨架所組成。活性物質是指正、負極中參加成流反應的物質,是化學電源產生電能的源泉,是決定化學電源基本特性的重要部分。對活性物質的要求是:
1) 組成電池的電動勢高;
2) 電化學活性高,即自發進行反應的能力強;
3) 重量比容量和體積比容量大;
4) 在電解液中的化學穩定性高;
5) 具有高的電子導電性;
6) 資源豐富,價格便宜。
2、 電解質電池的主要組成之一,在電池內部擔負著傳遞正負極之間電荷的作用,所以勢一些具有高離子導電性的物質。對電解質的要求是:
1) 穩定性強,因為電解質長期保存在電池內部,所以必須具有穩定的化學性質,使儲藏期間電解質與活性物質界面的電化學反應速率小,從而使電池的自放電容量損失減小;
2) 比電導高,溶液的歐姆壓降小,使電池的放電特性得以改善。對于固體電解質,則要求它只具有離子導電性,而不具有電子導電性。
3、 隔膜也叫隔離物。置于電池兩極之間。隔膜的形狀有薄膜、板材、棒材等。其作用是防止正負極活性物質直接接觸,造成電池內部短路。對于隔膜的要求是:
1) 在電解液中具有良好的化學穩定性和一定的機械強度,并能承受電極活性物質的氧化還原作用;
2) 離子通過隔膜的能力要大,也就是說隔膜對電解質離子運動的阻力要小。這樣,電池內阻就相應減小,電池在大電流放電時的能量損耗減小;
3) 應是電子的良好絕緣體,并能阻擋從電極上脫落活性物質微粒和枝晶的生長;
4) 材料來源豐富,價格低廉。常用的隔膜材料有棉紙、微孔橡膠、微孔塑料、玻璃纖維、水化纖維素、接枝膜、尼龍、石棉等。可根據化學電源不同系列的要求而選取。
編輯:jq
-
鋰電池
+關注
關注
259文章
8034瀏覽量
169532 -
化學電池
+關注
關注
0文章
20瀏覽量
9023 -
導電性
+關注
關注
0文章
151瀏覽量
9824
原文標題:收藏|鋰電錦囊從設計至分析大全
文章出處:【微信號:Recycle-Li-Battery,微信公眾號:鋰電聯盟會長】歡迎添加關注!文章轉載請注明出處。
發布評論請先 登錄
相關推薦
18650鋰電池容量分析 18650鋰電池與其他電池的對比
反射式-超窄帶寬濾光片(FWHM可低至20pm)
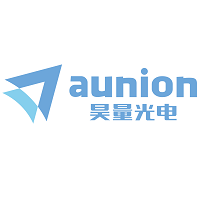
超透鏡的設計與分析
COMSOL Multiphysics在超材料與超表面仿真中的應用
\"鋰電池充電、保護與放電:從基礎到高級的全面解析\"
GGII:2023年國內儲能鋰電池出貨量超200GWh
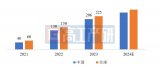
YB5212A是一種支持單節和雙節鋰電池的同步Buck鋰離子電池充電器IC
三元鋰電池和磷酸鐵鋰電池哪個好?
磷酸鐵鋰電池和三元鋰電池的差異點分析
鋰電池熱失控氣體產生原因、分析方法
助力鋰電池材料的“升華和蛻變”,蔡司掃描電鏡全流程深度研究
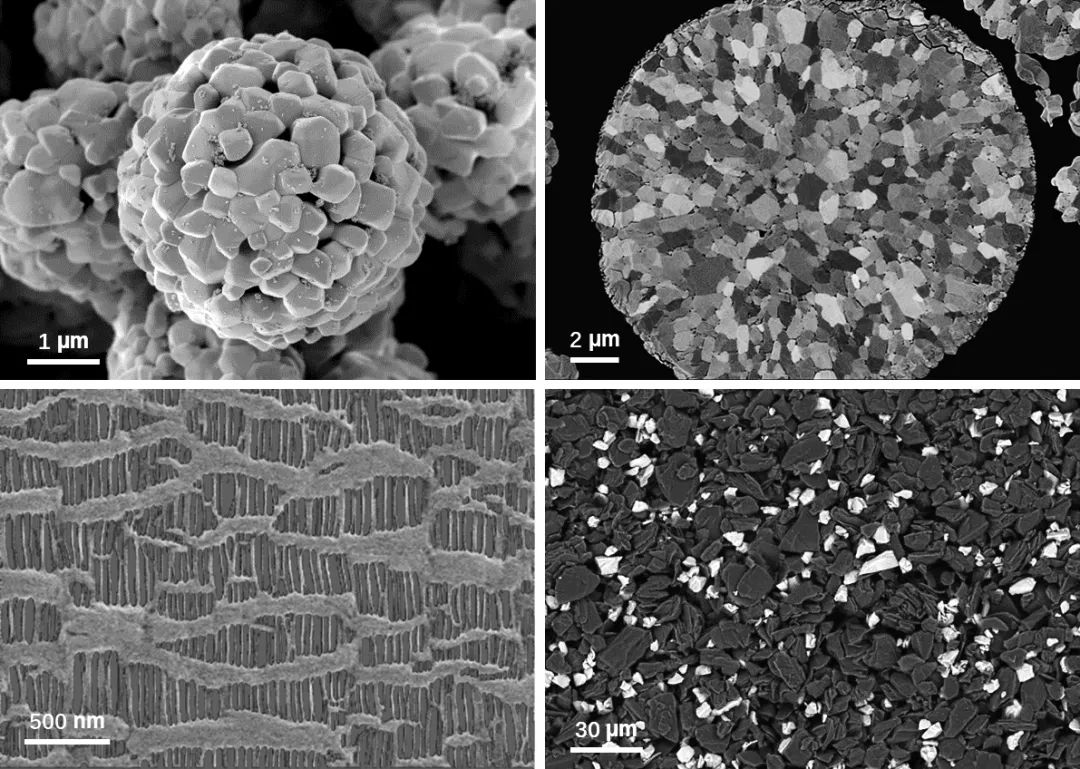
評論