伴隨著更多承載MinLED的新產品推出,該技術正處于落地的關鍵時點,在包括芯片、封裝和基板選擇等方面,均出現諸多新技術與新變量。本文將從這幾個角度詳細闡明。
MinLED芯片:僅需通過優化工藝來提升良率和產量即可實現從常規尺寸到Mini尺寸的跨越
LED芯片制造流程主要包括前道外延片制造、中道磊晶和后道晶片切割,涉及具體流程多達數十項,制造難度較高。
但由于LED產業的多年的發展,傳統LED芯片制造設備與工藝已經較為成熟,且MiniLED對切割精度和轉移設備的要求還未達到MicroLED那么嚴苛的程度,因此MiniLED芯片制造難度相對MicroLED較低,芯片廠僅需通過優化工藝來提升良率和產量即可實現從常規尺寸到Mini尺寸的跨越。
在轉移技術方面,相比于Micro LED,MiniLED有較大的尺寸和更加硬質的襯底。
因此其轉移過程有更高的精度容忍度和更多的靈活性。
當前主流廠商均有開發Mini LED相關的轉移技術,主要包括以下三種:
1)方案一是對現有的抓取設備進行改進,通過設置多個的手臂來增加拾取和放置的效率。這種方案技術難度較低,因此更容易實現量產,不過其存在產能上的限制,無法實現數量級上的增加。
2)方案二是將芯片和背板相對放置,再使用頂針將芯片頂出,從而放置于基板上。相比于方案一,這種方案減免了擺臂的反復移動,從而提升了轉移效率。而且,若芯片在藍膜上放置位置同最終背板的控制電極位置一致,再配合多頂針,即可實現巨量轉移,從數量級上提升轉移效率。
3)方案三類似于方案二,芯片放置于UV膜上,通過UV光把LED芯片選擇性地轉移到背板上。該方案能實現真正的巨量轉移,但是對芯片分選及其在UV膜上的擺放精度有較高的要求。
MinLED封裝:全倒裝+COB的新封裝趨勢
LED封裝技術正在經歷從傳統的支架型封裝(如SMD技術)向新型無支架型集成封裝(如COB技術)的過渡。傳統的LED封裝技術主要為SMD(Surface Mounted Devices)技術,意為表面貼裝器件。
SMD技術采用平面支架+點膠成型,并用表面貼裝技術進行組裝,采用合金銅材質扁平引腳,可組裝在鋁基板或PCB上。其工藝流程包括固晶、焊線、成型、切割、分光和帶裝入庫。
SMD技術最小可以做到穩定像素間距在1.2-1.5mm區間,擁有技術成熟穩定、制造成本低、散熱效果好和維修方便等優勢,是十分成熟的LED封裝技術。
不過,隨著LED向Mini/Micro方向發展,SMD技術應用開始受限。其技術防護等級低、壽命短等缺陷開始暴露出來,尤其是在制造像素間距P1.2以下的顯示產品時,SMD封裝技術開始出現諸多無法克服的技術瓶頸。例如SMD技術無法滿足Mini LED顯示產品的面板級像素失控率要求。
COB(Chip On Board)封裝技術是一種無支架型集成封裝技術,這種技術通過將LED芯片直接貼裝于PCB板上,在PCB板的一面做無支架引腳的COB高集成度像素面板級封裝,在PCB板的另一面布置驅動IC器件,而不需要任何支架和焊腳。
與傳統的SMD技術相比,COB技術能顯著地降低LED顯示面板的像素失效問題,同時還可以做到更小的點距,擁有更高的排列密度。
因此COB技術可以顯著提升LED顯示屏系統的像素密度和整體可靠性,為LED顯示的4K、8K超高清視頻顯示產品、Mini LED顯示產品提供底層高階面板制造技術,是當前LED顯示走向百萬級的必然選擇。
此外,在SMD和COB之間,還有多種支架型有限集成封裝技術,主要包括2in1、4in1、Nin1封裝技術。這種技術本質是SMD和COB的混合體封裝技術,減少了支架引腳的數量,體現COB封裝集成化的思想,但無法真正擺脫萬級或十萬級的面板級像素失控,在Mini LED 的1.2-0.9mm像素區間,會遇到與SMD封裝技術相同的技術瓶頸問題。
圖28:傳統SMD封裝與COB封裝對比
除了COB技術外,封裝端還創新性的引入了倒裝工藝來實現更高發光效率、排列密度和可靠性。
傳統的正裝技術存在著電極遮擋影響發光效率以及焊線較多工藝流程復雜等缺點。而倒裝技術通過將芯片倒置,使發光層激發出的光直接從電極的另一面發出,在封裝工藝上實現無電極遮擋、無焊線,因而可以最大程度提高發光面積、散熱面積,并能夠避免金屬虛焊和接觸不良引起的問題。同時,無焊線還可以提升芯片排列密度,助力LED進一步提升顯示像素密度。
目前在1.2mm以上像素間距范圍,還可以使用正裝芯片,在1.2-0.7mm像素間距范圍內,有紅光正裝、藍綠光倒裝的解決方案,在0.7-0.3mm像素范圍內,RGB都要使用倒裝芯片。
未來隨著LED向Mini/Micro方向加速演進,倒裝技術將迎來快速滲透。
綜上,對MiniLED產業來講,SMD封裝技術是目前工藝較為成熟、成本更低的封裝搭配,其將在中低端MiniLED產品推廣中使用。而倒裝COB技術,則是面向未來的新型封裝技術,長期來看,其發光效果優勢、可靠性優勢和高密度排列優勢將被進一步放大,有望實現對SMD技術的替代。
MiniLED基板選擇:PCB VS 玻璃基
基板是LED芯片的載體,MiniLED基板包括PCB方案和玻璃基方案。
其中,PCB是最常用的LED基板,具有技術成熟、成本低等優勢,主要由LED產業鏈廠商推廣使用。
而玻璃基板是LCD的關鍵物料之一,后經面板廠推廣至LED基板。
隨著MiniLED應用不斷深化,基板被提出了更高的要求,相關產業格局也有望迎來轉變。
1. 成本方面,從材料角度來看,PCB基板的價格是玻璃基板的幾倍,因此如果規模化生產,玻璃基板的物料成本其實更低。
但是從綜合成本來看,由于玻璃基板走線需要開光罩,所以前期投入成本較高,若是規模化程度不高,可能平均成本反而會超過PCB基板。
此外,從良品率來看,我國目前封裝廠對于PCB基板的技術要更加成熟、可靠性更強,良品率也更高,因此成本的可控性更強。而玻璃基板由于玻璃的易碎性,良品率較低。
因此綜合來看,當前PCB基板仍具成本優勢,但長期來看,隨著玻璃基板規模化程度和良品率提升,玻璃基板成本有望大幅下降,甚至低于PCB基板。
2. 性能方面,PCB基板散熱性弱于玻璃基板,且在芯片焊接中由于熱量密度較高,所以容易導致翹曲變形的問題,尤其在大尺寸的應用中,在多組背光單位拼接過程中容易產生拼縫問題。
而玻璃基板受熱膨脹率低,散熱性強,因此平坦性更高,更有利于Mini LED的焊接,因此玻璃基板可以滿足高精度需求。
3. 應用前景方面,PCB基板是國內目前技術工藝條件下的首選,其被當前絕大部分LED產品使用。
而對于散熱要求更高、平坦度要求更高或者高密度組裝的情況,玻璃基板將是更好的選擇。
2020年CES展上,TCL正式推出了采用玻璃基MiniLED方案的“MLED星曜屏”。
該產品擁有超高亮度,在逆光情況下也能出眾地成像;其對比度高達100萬比1,相比傳統LCD有指數級的提升;同時其在HDR及動態背光分區等細節也有不俗表現。
綜上,我們認為現階段對于Mini LED產品,PCB基板是終端廠商在市場需求量較小時,綜合成本和性能后的選擇。放眼未來,隨著MiniLED需求放量,玻璃基板有望形成規模化出貨,其成本也將被攤薄。屆時,玻璃基板競爭優勢將充分展現,并有望實現對PCB基板的替代。
本文綜合整理自未來智庫官網 電子技術設計
責任編輯:pj
-
芯片
+關注
關注
454文章
50460瀏覽量
421971 -
pcb
+關注
關注
4318文章
23022瀏覽量
396424 -
LED封裝技術
+關注
關注
0文章
15瀏覽量
6737
發布評論請先 登錄
相關推薦
揭秘LED三大封裝技術:SMD、COB、IMD的全面解析
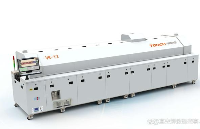
ai大模型和傳統ai的區別在哪?
什么是PWM和SPWM波形?兩者的區別在哪?
傳統封裝和先進封裝的區別
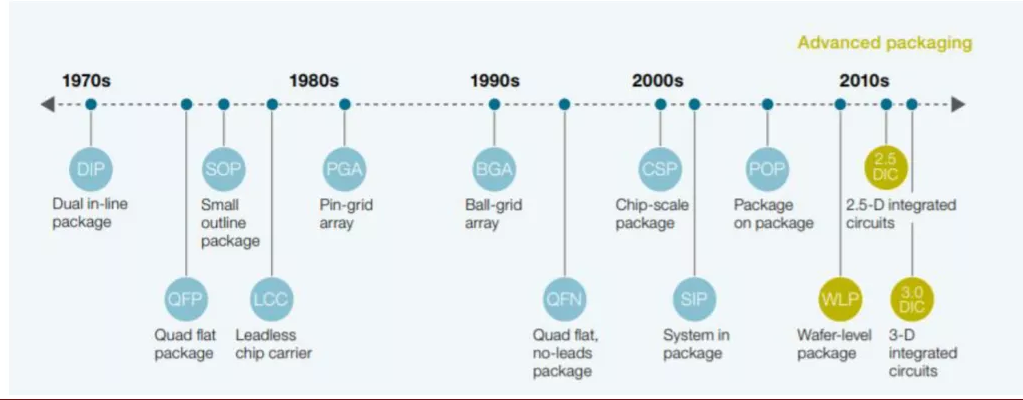
COB與SMD到底有什么不同?
什么是COB封裝工藝?COB封裝工藝的優勢 COB封裝工藝流程有哪些?
毫米波雷達物位計與傳統雷達液位計區別在哪里呢?
LED顯示屏SMD和COB封裝技術有何不同?
異步電路和同步電路區別在哪?
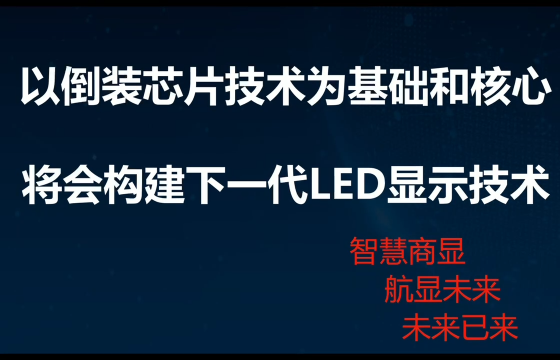
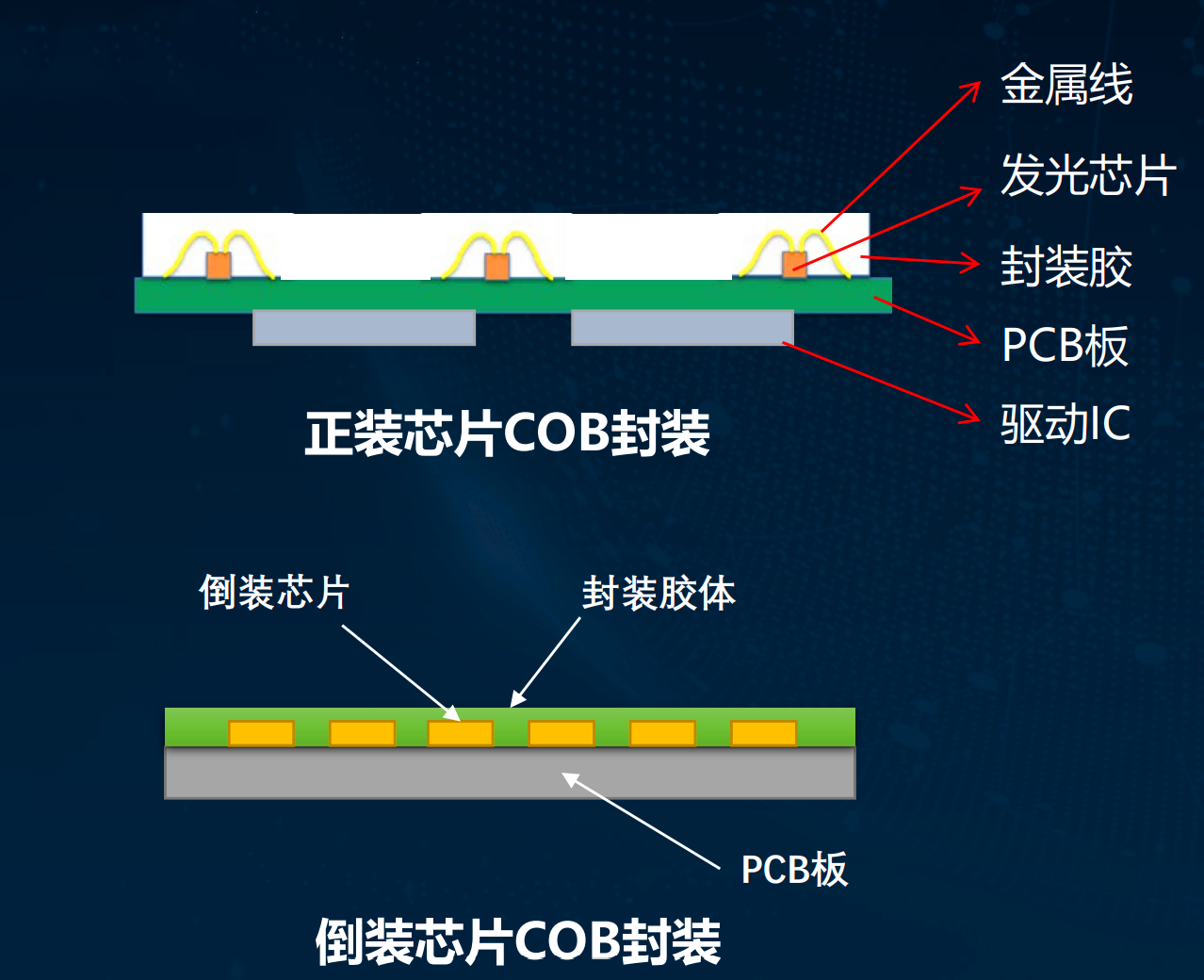
評論