車輛采用輕型零部件可有效降低CO2排放,因此Mahle公司與FraunhoferICT公司合作開發(fā)出了1種通過高強度纖維加強的塑料凸輪軸模塊。目前,該模塊已成功地通過了零件試驗過程。通過選擇合適的材料、制造工藝和模塊結(jié)構(gòu)型式,并合理實現(xiàn)塑料的功能組合,能有效降低模塊的制造成本。
0 前言
_
降低交通運輸過程中的CO2排放是1項重要目標(biāo),而減輕整車質(zhì)量有助于實現(xiàn)該目標(biāo)。在車輛以內(nèi)燃機作為動力來源的情況下,可通過采用塑料構(gòu)件以減輕其質(zhì)量。但是,目前作為發(fā)動機重要組成部分的凸輪軸模塊始終由鋁材制成。
目前,在德國國內(nèi)開展的研究項目中,部分研究人員已開發(fā)出了1種通過高強度纖維加強的塑料凸輪軸模塊,并成功地通過了零部件試驗。除了可減輕整機質(zhì)量之外,該措施還可有效改善經(jīng)濟性。研究人員通過選用合適的材料、制造工藝和模塊結(jié)構(gòu)型式,并利用塑料的功能組合,可有效降低模塊的制造成本。
研究人員選擇由Mercedes-Benz公司量產(chǎn)的M282型發(fā)動機作為試驗載體,這種4缸汽油機的氣缸蓋采用了三角形的結(jié)構(gòu)型式(圖1)。進排氣凸輪軸被安裝在分立式軸承襯套中,并通過1個罩蓋進行密封。該項目的研發(fā)目標(biāo)是通過1種輕型結(jié)構(gòu)塑料凸輪軸模塊以替代傳統(tǒng)的結(jié)構(gòu)型式。
1 技術(shù)要求和材料選擇
_
對材料的選擇主要取決于系統(tǒng)對構(gòu)件的要求。由于材料會直接影響到發(fā)動機及整體式凸輪軸軸承的制造過程,即便在環(huán)境溫度高達(dá)180 ℃的情況下,該材料仍具有良好的強度和剛度。同時,考慮到水和機油等介質(zhì)的影響,該類部件還必須具有較高的耐久穩(wěn)定性。
根據(jù)上述要求,研究人員會優(yōu)先選用熱固性塑料以替代熱塑性塑料。熱固性塑料具有較高的溫度和介質(zhì)耐久穩(wěn)定性,具有該特點的主要原因在于熱固性塑料中的高分子通過網(wǎng)狀結(jié)構(gòu)而得以緊密連接。目前,1種經(jīng)玻璃纖維加強的酚醛樹脂模塑材料已被研究人員正式選用。
該類材料除了在較高的使用溫度下,仍能保持良好的機械性能和必要的介質(zhì)耐久穩(wěn)定性之外,同時還具有較高的抗壓強度和較小的密度,并且在長期運行后不會產(chǎn)生蠕變現(xiàn)象。
此外,該類材料的熱膨脹系數(shù)與鋁材相似,從而有助于降低發(fā)動機運行時所承受的熱應(yīng)力,因為除凸輪軸之外,其周圍大多數(shù)構(gòu)件均為鋁制件。該類材料的另1項優(yōu)點是能通過注塑方法進行制造。熱固性塑料注塑工藝能在出色的重復(fù)精度情況下制造出機械性能較為均衡的構(gòu)件,而且生產(chǎn)周期較短,制造設(shè)備使用壽命較長,并能投入大批量生產(chǎn)。
2 開發(fā)方案和結(jié)構(gòu)設(shè)計
_
研究人員針對此類凸輪軸模塊的功能和材料要求進行了全新開發(fā),同時將現(xiàn)有的發(fā)動機氣缸蓋作為開發(fā)基礎(chǔ),并已在凸輪軸安裝位置范圍內(nèi)對樣品進行了調(diào)整。
為了能采用帶有封閉軸承座的凸輪軸模塊,必須銑削掉氣缸蓋上現(xiàn)有的凸輪軸軸承座,而其與氣缸蓋和正時傳動機構(gòu)殼體罩蓋的密封面則保持不變,并繼續(xù)投入使用。熱固性塑料特有的性能在設(shè)計過程中起著決定性的作用。
在原軸承座和模塊螺栓的緊固范圍內(nèi),研究人員通過對幾何形狀進行設(shè)計,可使由氣門機構(gòu)產(chǎn)生的應(yīng)力優(yōu)先轉(zhuǎn)化成壓力。為此,研究人員將配備有鋁制鑲嵌件的軸承座設(shè)定為分立式,并有足夠的空隙以用于凸輪軸的熱膨脹過程。
由于熱固性塑料具有較高的強度和剛度,因而能取消模塊與氣缸蓋及正時傳動機構(gòu)殼體罩蓋內(nèi)的鑲嵌件。為了使凸輪軸模塊能投入正常運行,其與氣缸蓋螺栓的連接區(qū)域未采用防松裝置,從而使整個凸輪軸模塊作為1類發(fā)動機組件,并投入使用。
3 模擬
_
研究人員借助于有限元模擬,以此確保了計算的精確性和對設(shè)計過程的充分優(yōu)化。臨界機械負(fù)荷和熱負(fù)荷來自于量產(chǎn)發(fā)動機,并且被用作于模型模擬過程的邊界條件。研究人員對軸承位移進行了限制,因為熱固性塑料的彈性模數(shù)比鋁更小,因此該目標(biāo)通常難以實現(xiàn)。
但是,在研究人員經(jīng)過多次優(yōu)化設(shè)計后,依然改善了整個模塊的剛度,從而使軸承位移保持在容許的誤差范圍內(nèi)(圖2)。同樣,研究人員通過設(shè)計優(yōu)化,使局部應(yīng)力的最大值降至最低程度,從而實現(xiàn)了所要求的疲勞強度(圖3)。
圖2 針對凸輪軸模塊剛度的有限元模擬
圖3 針對凸輪軸模塊疲勞強度的有限元模擬
4 模具設(shè)計和制造
_
在結(jié)構(gòu)設(shè)計得到最終認(rèn)可之前,由材料制造商對其進行充填模擬,以查明理想的澆注位置,并檢驗?zāi)>咔荒芊癖煌耆顫M。為了有效制造出該類凸輪軸模塊,需要使用由幾部分組成,并配備有鑲嵌件和自由活動模塊的注塑模具。
其中1個平均直徑為8 mm的活動模塊被拔出,并以此作為貫穿整個凸輪軸模塊的機油主油道(圖4)。該活動模塊在拔出過程期間仍支承著油道,以保持其方位。研究人員對相應(yīng)的工具與模具結(jié)構(gòu)進行了協(xié)同設(shè)計,并在注塑機上進行調(diào)試,注塑機可注塑體積約為0.6 L的構(gòu)件。
制成的樣品后續(xù)將會經(jīng)歷1個退火過程,從而使塑料分子得以結(jié)合,以釋放材料中的應(yīng)力,并改善機械性能。
圖4 機油主油道和凸輪軸軸承油孔的剖視圖
由于氣缸蓋和凸輪隨動件的接口界面上的公差范圍較小,研究人員必須對凸輪軸模塊進行機械加工。該機械加工流程通常須經(jīng)歷2次裝夾過程。研究人員在第1次裝夾過程中對密封面、基準(zhǔn)孔、長占孔、密封定位孔及機油孔進行了加工,并在第2次裝夾過程中加工全部的軸承襯套孔。
為了使軸承保有較小公差,研究人員使用了1種可實現(xiàn)自行支承的專用工具,并且在壓緊狀態(tài)下進行加工,以便使凸輪軸模塊的變形與通過螺栓壓緊時的效果相同。
研究人員借助于傳統(tǒng)的熱壓配合方法以實現(xiàn)凸輪軸的套裝接合過程。為此,在凸輪位置傳感輪和軸向軸承襯套有效接合在芯軸上之前,研究人員必須使其角度方位實現(xiàn)有效對中,緊接著對上述套裝件進行加熱,并將其接合在芯軸上。
在套裝接合的過程期間,因接合時間較短,熱固性塑料不會出現(xiàn)過熱的風(fēng)險。待套裝接合好后,采用機油潤滑軸承,以此可避免軸承部位和凸輪軸頸因運轉(zhuǎn)而損壞。為此,研究人員要對凸輪軸的重要特性進行測量和驗證,此外還要測試凸輪軸在軸承襯套中的轉(zhuǎn)動靈活性,在沒有對螺栓壓緊狀態(tài)進行查明時,應(yīng)使其轉(zhuǎn)動力矩小于3 N·m。
5 試驗臺驗證
_
研究人員在試驗臺上進行驗證之前,就已對樣品的品質(zhì)和機械性能進行過試驗,其中重點對熱固性塑料及其與鑲嵌件的接口界面進行了檢測,并借助于計算機掃描軟件檢查出了構(gòu)件塑料中的缺陷并將其妥善解決,以此有效避免了重大問題的產(chǎn)生。
此外,研究人員還對螺紋鑲嵌件從外側(cè)進行了拉拔試驗,并對周圍注塑的凸輪軸軸承襯套進行了扭轉(zhuǎn)和壓出試驗。試驗取得了令人滿意的結(jié)果,凸輪軸軸承襯套的扭轉(zhuǎn)力矩大于186 N·m,軸向壓出力大于9.9 kN,螺紋鑲嵌件的平均拉出力為4.3 kN。
繼預(yù)試驗后,研究人員隨即在倒拖發(fā)動機試驗臺上對凸輪軸模塊進行了驗證,將尚未配裝曲柄連桿機構(gòu)的量產(chǎn)發(fā)動機(Mercedes-Benz公司M282型發(fā)動機)安裝在氣缸蓋試驗臺上,并在氣缸蓋排氣側(cè)換裝了量產(chǎn)的凸輪軸模塊。同時,在當(dāng)前的螺栓緊固條件下,配裝在模塊中的凸輪軸轉(zhuǎn)動力矩同樣應(yīng)小于3 N·m。圖5詳細(xì)描述了試驗臺的結(jié)構(gòu)。
圖5 倒拖發(fā)動機試驗臺
圖6示出了用于運行過程的試驗程序。試驗期間,機油溫度為100±5 ℃,機油最高壓力為0.30±0.05 MPa,并且發(fā)動機機體側(cè)的84 ℃冷卻水循環(huán)可用于調(diào)節(jié)機油溫度,試驗程序中的最高轉(zhuǎn)速約為6 250 r/min。試驗進行100 h后即告暫停,研究人員首次對凸輪軸模塊的狀況進行了檢查。如果所有構(gòu)件均未出現(xiàn)明顯的異常狀況,隨即開展時長為500 h的后續(xù)試驗過程。
圖6 倒拖發(fā)動機試驗臺的試驗程序
這種凸輪軸模塊成功地完成了超過600 h的耐久試驗過程。在該試驗過程的前后,研究人員均采用光學(xué)三維(3D)測量系統(tǒng)對該模塊進行了變形分析,同時后續(xù)的試驗過程仍顯示出良好的結(jié)果。將凸輪軸從模塊中解體就能檢查出耐久運行后的軸承部位狀況。如圖7所示,所有軸承部位均未出現(xiàn)明顯的異常狀況,因此成功地展示和證實了新開發(fā)的輕型凸輪軸模塊的工作能力。
圖7 在進行耐久運行后的軸承部位狀況
6 減輕質(zhì)量并節(jié)約成本
_
除了成功地展示出輕型凸輪軸模塊的工作能力之外,該項技術(shù)改良也充分實現(xiàn)了減輕質(zhì)量和降低成本的目標(biāo)。與量產(chǎn)發(fā)動機上的傳統(tǒng)結(jié)構(gòu)型式相比,采用熱固性塑料模塊的氣缸蓋的質(zhì)量減輕了0.6 kg。一方面是因為采用了模塊結(jié)構(gòu)型式,另一方面則是由于使用了塑料材質(zhì)。
針對區(qū)分效果的分析表明,應(yīng)用熱固性塑料能使模塊的質(zhì)量比同款的鋁制件減輕約20%。與傳統(tǒng)量產(chǎn)發(fā)動機的結(jié)構(gòu)型式相比,在使用批量生產(chǎn)的輕型凸輪軸模塊的情況下,與成本密切相關(guān)的軸承襯套、凸輪軸相位調(diào)節(jié)器和傳感器也應(yīng)考慮在內(nèi)。
7 結(jié)語和展望
_
正如新開發(fā)的輕型凸輪軸模塊所示,在動力總成系統(tǒng)中使用塑料可有效減輕質(zhì)量,充分降低成本。目前,研究人員正計劃在實際運轉(zhuǎn)的發(fā)動機上試驗該類模塊,并且還對其聲學(xué)特性開展了相關(guān)研究。試驗表明,應(yīng)用熱固性塑料能充分改善整機聲學(xué)性能,并能相應(yīng)降低噪聲輻射。
除此之外,最佳的制造工藝和模具在批量應(yīng)用方面有著廣闊前景,以致于構(gòu)件在無需刀具加工的前提下,即可棄用常規(guī)的后處理流程。
同樣,將溫室氣體排放降至最低程度的研究也勢在必行。在后續(xù)使用過程期間,研究人員需要對其環(huán)保效果開展評估,同時也應(yīng)對其技術(shù)潛力進行分析及驗證。
編輯:jq
-
傳感器
+關(guān)注
關(guān)注
2548文章
50698瀏覽量
752040 -
3D
+關(guān)注
關(guān)注
9文章
2863瀏覽量
107330 -
調(diào)節(jié)器
+關(guān)注
關(guān)注
5文章
832瀏覽量
46368
原文標(biāo)題:干貨 | 輕型高強度纖維加強塑料凸輪軸模塊
文章出處:【微信號:汽車與新動力,微信公眾號:汽車與新動力】歡迎添加關(guān)注!文章轉(zhuǎn)載請注明出處。
發(fā)布評論請先 登錄
相關(guān)推薦
玻璃光纖線有什么不同
激光塑料焊接系統(tǒng)在PPS材料上的應(yīng)用
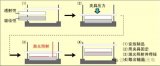
測徑儀:提升低合金高強度鋼軋制品質(zhì)的關(guān)鍵設(shè)備
曲軸傳感器和凸輪軸傳感器的區(qū)別
碳纖維阻抗和玻璃纖維阻抗的區(qū)別
功率與速度的最佳配合下 980nm半導(dǎo)體激光器成為塑料焊接利器
雙向納米玻璃氫化物解決稀土基非晶合金強度-塑性問題和磁熱性能
意法半導(dǎo)體推出一款LSM6DSV32X 6軸慣性模塊(IMU)
熔纖機放電強度多少合適
凸輪軸位置傳感器在哪個位置 凸輪軸位置傳感器三根線怎么測量
凸輪軸位置傳感器的作用 凸輪軸位置傳感器壞了有什么影響
汽車發(fā)動機cvvt、dvvt、vvt、VVT-i都是什么意思?
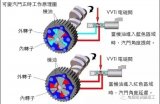
單向碳纖維強化的柔性壓電納米復(fù)合材料的原理、結(jié)構(gòu)設(shè)計及應(yīng)用
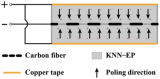
汽車產(chǎn)業(yè)10大關(guān)鍵材料盤點
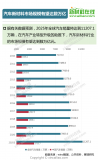
評論