狀態監測的智能方法
預測性維護的第一步是創建一個系統來監控設備的狀況。通常,機器會隨著時間的推移而磨損;這導致可測量的規格或參數逐漸變化。原則上,我們越早發現缺陷,維護成本就越低,生產時間損失的風險也就越低。直到最近,設備專家和維護人員幾乎完全使用基于壓電或超聲波傳感原理的離散便攜式傳感器探頭來監測振動和聲音發射等故障指標。然而,基于這些技術的診斷設備相對復雜且昂貴,并且在可重復性、數據管理和分析方面也存在局限性。
最先進的電子設備和先進的算法使一種新方法成為可能。我們現在可以直接在機器上應用小型、低功耗傳感設備來監控多個參數,對獲取的信號數據進行預處理,并將數據發送到本地、遠程或基于云的分析和控制設施。這些緊湊型智能傳感器節點通常由傳感器、微控制器、電源管理電路和有線或無線連接組成,與傳統的狀態監測設備相比具有顯著優勢。
智能傳感器節點的優勢
首先,有一個很好的經濟論據。具有自主操作的智能傳感器節點的成本遠低于便攜式壓電探頭和操作它們所需的熟練技術人員。其次,具有可重復、可靠和及時的數據的優勢。這要歸功于機器運行期間的持續測量和分析,并且不僅限于可能錯過早期或嚴重故障跡象的維護計劃。下一個好處是能夠使用智能算法在節點本地分析數據并立即觸發本地操作以保護設備并確保工人安全。傳感器節點還可以配置為通過隨時間自動調整監控參數來解決老化設備的容差增加。
除了本地傳感器節點在監控單個機器方面提供的優勢之外,當傳感器節點連接到云并能夠收集大量數據以進行更深入的預測維護分析時,還有更多好處。
開始使用預測系統
建立基于智能傳感器系統的預測性維護解決方案可能需要一到兩年的時間,包括幾個重要步驟:
定義系統架構。
以合適的成本和可用性尋找具有合適精度和穩定性的傳感器。
定義微控制器所需的規范,包括計算能力、內存和接口。
選擇連接技術。
設計電源管理級和合適的外形尺寸。
實施所需的分析以及表征系統。
在真實的應用場景中驗證一切。
ST 設計了一個專門的生態系統,以促進對預測性維護系統設計人員可能需要的產品的評估,并使用預先驗證的工具加快現場測試表征的部署。意法半導體為有線傳感器節點參考設計套件和與云數據連接的無線傳感器節點提供振動分析工具。
具有 IO-Link 功能的有線傳感器節點參考設計套件
STEVAL-BFA001V1B是一款小型工業參考設計套件,用于基于有線連接的狀態監測和預測性維護。
硬件開發套件包括一個帶有多個傳感器的工業傳感器板、一個微控制器和一個用于通過有線連接發送數據的設備控制器、一個用于 ST-LINK/V2-1 編程和調試工具的適配器,以及必要的電纜和連接器。
固件包 STSW-BFA001V1在 STM32F4 微控制器上運行。它包含基于 3D 加速度計庫的完整演示示例,具有用于預測性維護的高級信號處理,包括時間分析(速度 RMS、加速度峰值)、頻率分析(可編程 FFT 大小、平均、重疊和開窗)、聲音分析(PDM 到 PCM ,聲壓,音頻 FFT)。該軟件包包括氣壓傳感器驅動程序以及相對濕度和溫度傳感器。
具有云連接的無線傳感器節點
軟件包 ( X-CUBE-WATSON ) 在無線連接的 IoT 節點上運行,數據傳輸到 IBM Watson IoT,可用于傳輸傳感器數據和接收來自遠程應用程序的命令。
該軟件包讓開發人員能夠快速啟動端到端物聯網開發,讓他們專注于附加功能,而不是開發基本功能。
該軟件包進一步擴展了用于處理加速度計數據的預集成算法,可用于檢測來自電機、風扇和泵等設備的振動。被測設備的最大頻率和磨損狀況與原始傳感器數據一起傳輸到 IBM Watson IoT,從而能夠快速開發用于工業狀態監測和預測性維護的解決方案。
預測性維護是智能工廠的關鍵推動因素之一,實現它的技術已經在這里:傳感、連接、安全、電源管理和具有人工智能功能的嵌入式處理。添加云計算和連接,您就擁有了創建復雜、高性能系統的所有要素,這些系統可以提供預測性維護應用程序的全部優勢。
審核編輯:郭婷
-
微控制器
+關注
關注
48文章
7490瀏覽量
151062 -
傳感器
+關注
關注
2548文章
50698瀏覽量
752064 -
電機
+關注
關注
142文章
8935瀏覽量
145114
發布評論請先 登錄
相關推薦
一些常見的動態電路
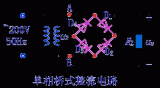
工業數據采集平臺在預測性維護中的作用
Tekvpi探頭接口的一些好處是什么?
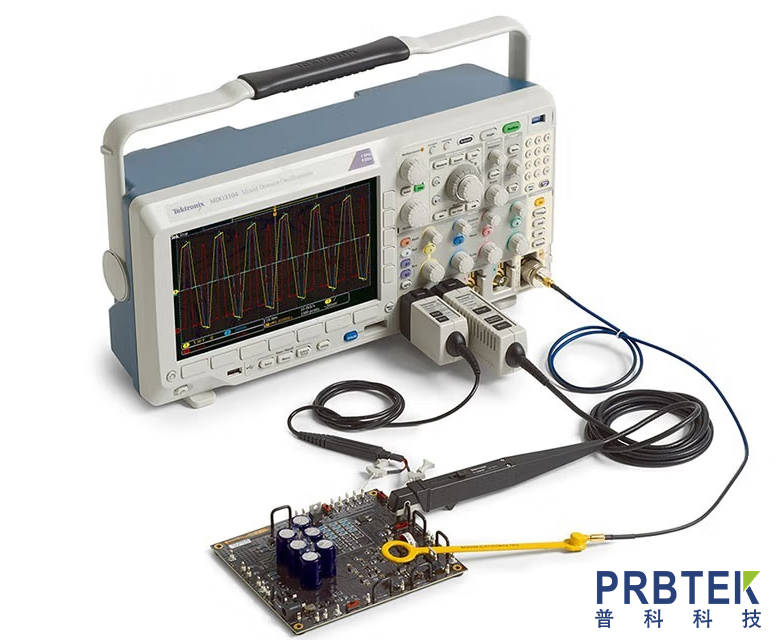
為什么振動監測對物聯網預測性維護至關重要
對于大模型RAG技術的一些思考
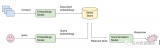
評論