隨著電子電氣產品向著小型化、輕量化方面發展,電子元器件制造及電子產品 PCBA 裝聯也隨之進入高密集、高集成化時代。為防止器件由于濕氣導致的芯片內部腐蝕引起的器件失效及高溫焊接過程“爆米花”效應產生的橋連, IPC-A-600 、PC/JEDEC-STD-020C、IPC/JEDEC-STD-033C, 包括GB、GJB、QJ1693ESDS 等國家行業標準及行業“禁限用工藝規范”均對靜電敏感器件、濕敏器件、塑封器件、PCB 裸板等上線焊接前進行烘干除潮提出了嚴格規定及要求。
目前在電子行業制造過程中對靜電敏感、濕敏器件、塑封器件、PCB 裸板等采用普通烘箱烘干已經成為行業通用做法,但實際上,采用普通烘箱對含靜電敏感及精密器件產品以及易燃易爆的化工品等進行烘干工藝過程中存在極大的安全隱患。具體表現如下:
1、靜電損傷
普通烘干箱對靜電敏感器件在烘干除潮過程中由于缺乏專業、安全的靜電安全防護措施,一般直觀靜電損傷測試現象為器件由于靜電擊穿從而導致貴重器件功能失效而直接報廢;隱性故障為器件因靜電損傷常規環境下測試正常,但在某些環境溫度或振動工作條件下因性能降低從而導致組件甚至整機產品功能失效, 此種不易排查的隱性故障導致產品靠性降低、危害性及損失更為巨大。
2、溫沖損傷
精密器件(貼片阻容)在不具備溫升梯度控制功能的烘干設備自然溫升下, 器件金屬非金屬材料密封連接位置因溫沖導致的熱膨脹系數失配易產生微裂紋(加溫焊接過程中回流焊爐升溫及傳送速度過快、手工焊接未采用預熱臺避免器件不同材料間熱膨脹系數失配),空氣環境中水汽、硫等物質經損傷裂紋進入與器件內部金屬進而發生濕腐蝕與硫化銀腐蝕,該現象往往在兩年或四年后逐漸顯現出 PCBA組件數據漂移或功能失效等故障,此種故障滯后現象對系統危害性巨大,且工藝問題往往是批次性的,質量及售后損失巨大。
3、烘干工藝效率問題
由于不同器件在烘干過程中對不同器件的烘干溫度、時間要求也各自不同, 一臺或數臺烘干設備難以同時滿足批量生產中數十種元器件制造周期內的烘干 需求。
4、職業健康及環保
電子器件制造過程中應用了各種化工產品完成內部粘接、外部封裝保護等。在器件烘干除潮過程高溫條件下,這些化工產品極易揮發帶有異味的有害氣體污染環境、危害操作人員身體健康。
附表國際電子工業聯接協會 IPC/JEDEC-STD-033C 電子器件烘干標準
電子元器件為何要烘干除潮?
電子元器件焊接裝配前必須烘干除潮原因:
①電子元器件日常或超期存儲受潮后不 經烘干工藝處理,器件內部金屬材料易因潮濕產生腐蝕現象(二年左右阻值、容值明顯 出現變化,嚴重的產生斷路現象);對因設備機械貼片及焊接過程中溫沖產生的器件密 封失效未及時采取密封防護工藝措施,空氣環境中水汽、硫等物質經密封裂紋(損傷) 進入與器件內部金屬進而發生濕腐蝕與硫化銀腐蝕,該現象往往在兩年或四年后逐漸顯 現出 PCBA 組件數據漂移或功能失效等故障,此種故障滯后現象對整機危害性巨大,損失往往是批次性的
②隨著電子器件向高集成、小型化發展,線路日益密集,在電子行業制造過程中受 潮器件在加溫焊接過程中焊料飛濺造成短路,要求器件焊接(手工、再留焊、波峰焊) 前必須要進行器件除濕烘干處理。尤其 BGA、QFP 等隱藏焊點或密間距器件,將因無法返修而報廢
③電子組件焊后清洗及三防涂敷前后均需要按標準、工藝要求進行安全烘 干處理。
靜電敏感元器件烘干除潮工序中如何靜電防護?
靜電放電對電子產品的損傷具有隱蔽性、潛在性、(損傷的)隨機性和(失效分析) 復雜性等特點,在芯片微組裝、SMT、電子制造車間、危險化工品、火工品倉庫等根據標準及工藝要求必須采取有效的靜電防護措施。PCB裸板及電子元器件上線焊接前要求烘干除潮、PCBA組件清洗及三防漆涂敷后均需要烘干,但目前市場烘干設備均為普通烘干箱,不具備靜電防護功能。一旦發生靜電擊穿其隱形損傷一般從外觀上或現階段無法直接發現,除在測試階段出現功能喪失外,更嚴重的是在產品性能使用過程內振動或 溫度變化條件時的性能降低,產品可靠性無法保障。
耐高溫防靜電涂層
對于靜電敏感芯片或對器件可靠性要求高的重要產品為防止在制造過程中靜電敏 感器件的靜電損傷,則從器件存貯、轉運、烘干、成型、焊接、檢測等全過程實現靜電 防護,ESD智能分屜式實驗烘箱則是其中元器件上線焊接前烘干除潮工序中重要的烘干靜電防護設備!該型設備采用雙靜電防護通,即采用“整機保阻硬接地+軟接地”結合 方式。其中軟接地采用石墨烯耐高溫耗散性導電材料制成,粘接強度高;軟硬接地并 設計,這樣的設計結構無論器件取放還是設備工作過程通斷瞬間及設備移動過程中均 能保證設備中靜電的安全泄放,符合 GJB3007-97 以及歐盟 EN61340防靜電標準,確保靜電敏感產品烘干全過程的靜電防護安全、可靠。
如何防止不同材料(金屬/非金屬)制成精密元器件烘干除潮工藝中由于熱膨脹 系數失配密封失效?
精密元器件一般由金屬、非金屬材料制成。在烘干除 潮過程中傳統工藝一般采用普通的熱風烘箱進行烘干除 潮工作,升溫過程自室溫自然快速升溫到設定烘干溫度(40℃/90/125),這樣不受控的自然斜率升溫曲線對由 金屬、非金屬材料共同制成的精密元器件易由于金屬、 非金屬材料不同的熱膨脹系數失配造成精密器件溫度應力損傷,尤其由陶瓷、玻璃釉等非金屬封裝的器件在快速升溫條件下金屬、非金屬連接 部位出現裂紋,損傷率極高。
初期故障表現為為 PCBA板級組件數據漂移,最終 PCBA板級組件功能失效,一方面起始于空氣中水汽經損傷裂紋進入器件內部與金屬發生濕腐蝕,故障一般在兩年左右 方才顯現可測;另外空氣中硫與器件中金屬銀發生的硫化銀腐蝕,往往在四年后才逐漸 顯現。這種隱性制造缺陷滯后的現象對電子產品制造廠商危害極大,一旦出現就是批量質量問題,造成的直接及售后損失巨大。
因此,針對此類器件 ESD 智能分屜式實驗烘箱采用專業安全的升溫梯度控制措施, 除九點測溫保證溫度精度 at200℃,無負荷狀態下(測溫 ±1.0℃),at100℃,無負荷狀態下(測溫 ±0.5℃,控溫±2.0℃)、均勻度±2℃等指標要求嚴格外,升溫速率應控制在 5~10℃/min。
PCB 裸板烘干除潮形變(平面度)如何控制?
PCB裸板長期存放由于應力、溫度變化導致的板面彎曲、變形,烘干除潮過程中 PCB 裸板的多層不同材質結構應力在溫度作用下形變及殘存應力等均會使 PCB裸板的平面度無法保證。電子行業標準要求 PCB 裸板保證平面度是應為:采用自動化焊膏印刷及貼片的設備對 PCB裸板平面度要求較高,因 PCB裸板一旦產生翹曲形變對焊膏印刷壓力控制、貼片精度及焊接可靠性將無法保證。尤其注意近年來一些典型案例表明,這種板 面翹曲甚至對 PCB裸板自身線路連接產生應力損傷(內部蝕刻線路斷路),這種內部線路損傷在制造過程甚至調試階段都難以發現。
采取設備焊接工藝時或 PCB 存放在相對濕度大于 70%~80%的工作場地時,裝焊前無論是設備焊接還是手工焊接都必須進行去濕預烘處理,對于未拆封的原包裝裸板可不進行預烘處理。
PCB 的去濕需要釆用階梯式緩慢升溫(梯度升溫),而不是急速升溫。這不僅僅是為了順應環氧樹脂對水分子的釋放特性,更重要的是為了避免急速升溫造成 PCB 翹曲。同樣,經過烘烤排潮完畢以后,板子的降溫也必須釆用緩慢降溫(斜度降溫)的方式, 以避免“急冷”在 PCB 基材內部形成局部應力,從而導致板子翹曲。PCB 經過高溫烘烤, 特別是烘烤溫度接近或超過基材的玻璃態轉化溫度(Tg)后,基材中的樹脂處高度柔軟的彈性狀態,此時,如果采用急速冷卻,板面有、無銅箔電路(或板芯內層電路)的環氧玻璃布絕緣基材之間,經歷的降溫速度就會產生較大的差異。這種降溫速度差,會使烘烤過程中已經軟化了的樹脂,在有和無銅箔部位的冷卻硬化速度不一致,從而形成局部應力。取板操作時烘箱溫度與室溫之間的溫差越大,降溫速度差異導致的這種應力也會越大,板面翹曲的后果也越嚴重!因此,PCB 裸板在實驗烘箱內必須采用緩慢或自然降溫,待溫度降至 60°C 以下后,方可取出。
僅就排除潮氣而言,PCB 組件制造過程不建議把烘板的溫度提升到基板的玻璃態轉化溫度(Tg)或 125℃以上,除非需要在排潮烘板的過程中,同時去除板子內的殘余應力。通常,去應力烘板必須將溫度提升到基板(例如環氧玻璃布層壓板)的 Tg溫度再加 20℃以上的范圍內,并嚴格執行梯度升溫(有恒溫平臺)和斜度(℃/min)降溫(不需要設置恒溫平臺)的操作規范。如果板子有輕度翹曲需要在去應力烘板過程中加以校 平,還必須對板子作平放加壓,或使用夾持工裝壓緊。顯然,“去應力”烘板,也同時 就完成了“排潮”烘板。
通常,我們把 Tg≤130℃的印制板基材稱作低 Tg 板;把 Tg=150℃±20℃的印制板基材稱作中 Tg 板;把 Tg≥170℃的印制板基材稱作高 Tg 板。無論何種類型 Tg 值的印制板,在其 Tg 溫度以下,由于基材環氧樹脂始終保持著堅硬的剛性狀態,因而冷卻時形成局部內生應力的幾率很低,其板子發生翹曲的幾率也就很低。高 Tg 板子不僅吸水率低,而且熱膨脹收縮率(CTE)幾率也很低。這也正是為什么手機板等高密度印制板(HDI),和芯片封裝用印制板(COB)要選用高 Tg基材,及高 Tg板焊接前很少需要烘板排潮的原因之一。當然,由于手機生產周期短,一般情況下 PCB從出廠到完成焊裝, 大多都在幾十個小時以內,“吸潮”的可能性幾乎可以忽略不計。
PCB 裸板烘干除潮工藝操作要求:
去濕預烘必須在焊接前 8h 內進行,并設置好烘烤溫度、升溫速率及時間。對這一過程及 PCB 進出烘箱的溫度均應有記錄
PCB 裸板預烘條件:(80~100℃)±5℃,升溫速率 5℃~10℃/min 的烘箱里烘8h±2h,取出時采取烘箱內自然降溫至 60℃以下方可安全取出。烘烤完成的 PCB 要求在半個工作日內完成裝焊,暫時不能裝焊的需包裝好保存在干燥柜或防潮功能的包裝材 料內。為消除 PCB 裸板烘干除潮過程中板面的翹曲、形變,ESD 智能分屜式實驗級別烘箱配套了 PCB 裸板專用壓板以控制烘干過程板面的形變,其次通過自然降溫等工藝措施釋放板面殘存應力以保證 PCB 裸板烘干除潮后的板面平面度;對于要求嚴格的產品,PCB 裸板烘烤時必須豎立放置在夾緊裝置上,夾緊裝置必須能在烘烤周期內為 PCB 提供足夠的支撐,以防止 PCB 翹曲。
如何滿足批次不同種類元器件不同溫度、不同時間安全烘干需求?
ESD 智能分屜式實驗烘箱采用單機多溫、多屜設計,標準每屜 30~40L, 不同零件、組件取放靈活,無干擾;不同類型產品可通過分屜計時 0~99~999h,復位自動計時、定時聲光提示。
ESD 智能分屜式實驗烘箱單機設備通過不同元器件分屜計時、單機分單元不同溫控、升溫梯度精密制技術及熱空氣流量仿真對結構進行 了優化設計。不同的加熱、隔熱單元,獨立可流量控制的進氣、排氣通道可專業安全的將每單 元、每屜的溫度均勻度控制在±2℃以內,在提高 試驗、生產過程中烘干工藝效率同時,將設備單元實際溫控精度達到實驗級水平。
如何防止元器件烘干過程中有害物質揮發對人體健康產生危害及環境影響?
ESD 智能分屜式實驗烘箱針對電子器件、化學品高溫烘干設計有可拆卸式獨立封閉單元的單路進出通風及高效的多重過濾系統。活性炭過濾有害氣體,高效過濾器過濾0.3um 以上粒子,過濾有效率高達 99.97,有效的保護室內操作人員免受有害氣體的侵害。
多臺分屜式實驗烘箱不同位置如何實現集中智能管控?
ESD智能分屜式實驗烘箱預留 RS485(或以太網)數據通訊接口,設備單機或多組、多地可方便接入企業網絡進行系統監測;智能升級版可定制網絡多模組軟件實現智慧監控。
ESD 智能分屜式實驗烘箱安全性問題
ESD 智能分屜式實驗烘箱單機設計有漏電保護、過載保護(本體內部加熱回路、風機回路、控制回路都有獨立的過載保護 )、過熱防止回路(獨立溫度過升控制儀,當溫度異常過升時,加熱器電源斷開、電機風葉動作) 、開始與復位(抽屜開時,風機、加熱不停、計時復位;抽屜關閉,開始計時),自珍斷功能 (加熱器斷線,SSR 短路、自動過升防止,傳感器損壞),鎖鍵功能、環保功能等。
審核編輯:劉清
-
ESD
+關注
關注
48文章
2012瀏覽量
172733 -
pcb
+關注
關注
4317文章
23006瀏覽量
396302 -
濕敏器件
+關注
關注
0文章
4瀏覽量
5718 -
PCBA
+關注
關注
23文章
1506瀏覽量
51347
原文標題:元器件烘干除潮的必要性(ESD智能分屜式試驗烘烤箱)首選
文章出處:【微信號:現代電子裝聯工藝技術交流平臺,微信公眾號:現代電子裝聯工藝技術交流平臺】歡迎添加關注!文章轉載請注明出處。
發布評論請先 登錄
相關推薦
SMT貼片貼裝工藝流程 SMT貼片焊接技術解析
激光焊錫工藝在精密光學元器件中的應用
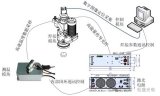
評論