點膠技術概述
根據點膠原理不同,點膠技術大致可分為接觸式點膠和無接觸式點膠,如圖1所示。接觸式點膠依靠點膠針頭引導膠液與基板接觸,延時一段時間使膠液浸潤基板,然后點膠針頭向上運動,膠液依靠和基板之間的黏性力與點膠針頭分離,從而在基板上形成膠點。這項點膠技術的最大特點是需要配置高精度的高度傳感器,以準確控制針頭下降和抬起的高度。無接觸式點膠則以一定方式使膠液受到高壓作用,由此獲得足夠大動能后以一定速度噴射到基板上,噴射膠液過程中,針頭無Z軸方向的位移。
點膠技術正在經歷一場由接觸式向無接觸式的轉變
接觸式點膠
1
大量式點膠
大量式點膠包括針轉移式點膠和絲網印刷式點膠,如圖2所示。這種傳統的點膠方式點膠速度快,主要用于印刷電路板(PCB)大規模生產線上,但其缺乏柔性,點膠精度不高,一致性差,并且膠液直接暴露在空氣中,容易吸水和揮發。針轉移式點膠適應性較差,不同膠點樣式須更換針板,并且點膠過程中,膠液反復加熱,使用壽命短。絲網印刷式點膠只適用于比較平整的表面,遺憾的是集成電路一般表面都是凹凸不平的,這使其應用受到了限制。
針頭式點膠
1
計量管式點膠和活塞式點膠
繼大量式點膠之后,經過長期探索和研究,相繼出現了計量管式點膠和活塞式點膠等新型點膠方式。如圖3a、圖3b所示,它們都是通過壓力驅動膠液流出,可獲得直徑較小的膠點。計量管式點膠由螺桿旋轉提供連續壓力,迫使膠液從針頭流出,能容易地畫出線和圓等連續圖案,但點膠量大小與螺桿幾何參數有關,不易控制;活塞式點膠靠活塞推動腔體內膠液的流出,該裝置點膠一致性好,但膠量也難控制,且清洗復雜,密封要求高。
2
時間/壓力型點膠
目前,應用最廣泛的點膠方式是時間/壓力型點膠,其最早是被應用于SMT(表面貼裝技術)中,它通過脈動的氣壓擠壓針筒內活塞,將流體通過底部針頭擠出至基板,如圖3c所示。
該點膠技術適用于中等黏度的流體,膠點的大小取決于氣體壓力和作用時間。這種設備便宜、操作簡單、維護方便、適用性好、方便清洗。但它對流體黏度敏感,氣壓反復壓縮釋放過程易使流體溫度升高,影響流體流變特性,點膠速度難以提高,同時影響形成的膠液直徑大小的一致性,相對其他點膠方式一致性差(表1)。另外,隨著針筒內的膠量改變,膠點的大小會隨著變化,響應速度變慢。
無接觸式點膠
電子封裝將向高密度、超小型、超高集成度和三維封裝的方向發展;流體分配的速度需要大于45000點/h;使用的流體材料黏度范圍越來越大,種類也越來越多,尤其是開始應用非牛頓流體材料,非牛頓流體材料復雜多變的特性使得點膠的性能和品質難以保證。這些原因使得傳統的接觸式點膠已不能適用于未來的電子封裝產業,并在其應用過程中逐漸暴露出各種缺陷:針頭與元件靠得很近而容易損傷元件;針頭需做Z向位移運動,影響了點膠速度,且設備需配置高度傳感器精確控制Z向位移;針頭點膠無法到達空間狹小的地方等。因此,探索和研究新型點膠方式,使其更適應電子封裝行業的發展與應用,已成為當前的熱門課題。
最近20年,點膠技術在控制流體沉積、針頭定位和膠點一致性方面都得到很大進步,點膠速度也得到了較大提高,最新點膠方式(由Mydata提出)的速度最高可達400點/s,點膠技術也正逐漸從接觸式點膠轉化為能高度自動化操作的無接觸噴射點膠。噴射點膠技術由噴墨技術演變而來,它的出現為電子封裝行業帶來了深遠影響。
1
噴墨技術
噴墨技術是將墨水噴涂到基底上的技術,有熱氣泡式和壓電式兩種(圖4),主要用于印刷、壓電式噴墨,還運用于藥劑生產。熱氣泡式噴墨通過熱敏電阻加熱墨水產生氣泡,氣泡爆破使墨水噴出形成墨滴;壓電式噴墨利用壓電材料的壓電效應產生機械力,并以機械動作將墨水“擠”或“推”出去。早期,人們已經意識到噴墨技術可應用于電子封裝工業,獲得小至10pL的液滴,且可控制噴射速度,在基底上可噴射得到各種樣式的圖案。但電子封裝中使用的流體黏度較高(1~100Pa·s),如圖5所示,而噴墨技術只能噴射像墨水這樣的低黏度流體(通常是0.03Pa·s以下),很難應用于除墨水之外的其他流體材料。
2
噴射點膠技術
噴射點膠的研究還在起始階段,技術相對還不成熟,這項技術主要是采用瞬間高壓驅動膠液噴出,使流體材料沉積到基底的固定位置上(圖6),每次噴射只能得到一個膠點,通過逐次疊加可以得到其他形式的圖案,其應用的流體黏度范圍廣,幾乎可以運用于電子封裝中的各種流體,而且噴射速度快、膠點一致性好、適應性強。噴射式點膠成功克服了接觸式針頭點膠的缺陷,沒有Z向位移,使得點膠品質不受噴頭與基板距離的影響,提高了膠點一致性,同時,點膠速度也有很大提高,噴射頻率可達50000點/h以上(表1),而且噴射式點膠可以適應很復雜的封裝環境,實現液滴的準確定位,但噴射不同大小的液滴需更換噴嘴,操作柔性較差,噴射較高黏度流體時須配置溫控器。近年來,出現了一些能控制液滴大小的噴射點膠系統,使得噴射點膠的性能得到了進一步改善。
由于未來電子封裝密度將會大幅度提高,傳統的接觸式針頭點膠已不能滿足應用要求,相對其他點膠技術,噴射點膠技術更能適應這樣的發展趨勢,具有更好的應用前景,它正快速發展成為電子集成、半導體封裝和平板顯示集成點膠的標準方式。目前,噴射點膠技術有機械式和壓電式兩種,壓電式點膠主要應用于低、中黏度流體,機械式點膠則可以噴射黏度較高的流體。當配置溫控器時,兩種方式基本上都能應用于電子封裝中的各種流體材料。
3
機械式噴射點膠
機械式噴射點膠在電子制造業中已得到很好發展,主要用于噴射高黏度流體。在此種噴射方式下,流體只需要用相對較低的壓力引入到料腔中。通常芯片下填充料粘結劑的壓力小于0.1MPa,液晶之類的低黏度材料需要的壓力在0.01MPa左右。如圖7所示,料筒中的流體通過供料系統壓力作用流入閥腔,當閥桿向上運動時,流體流入閥腔內,由于噴嘴非常小且供料系統提供的壓力足夠,故空氣無法從噴嘴位置抽入到系統中。隨后,閥桿以設定的速度快速向下運動,同時帶動流體流動,當閥桿與閥座接觸時,迫使一束流體從噴嘴噴射出去。
這種噴射方式中,閥桿前端與閥座恰好接觸時,一定體積的流體被卡在兩者之間的間隙里,并只能經過閥座上的噴嘴才能流出,閥桿運動很快從而使這部分流體受到的瞬時壓力非常大。如圖8所示,此時,噴嘴處流體的動能急速增加,使得這部分流體可獲得足夠速度而噴出,并到達基板固定位置上。該技術的優點在于液體在噴嘴位置可以獲得很大的瞬時壓力,因此可以噴射那些黏度很高的流體;缺點是所噴射出的膠點尺寸比壓電式或熱氣泡式大很多,結構復雜,且噴射頻率比壓電式的低。國內一些研究機構)對這類噴射設備研究較多。其中,華中科技大學張鴻海等開發的氣缸式噴射點膠系統的最高工作頻率為30Hz,最小膠點直徑為0.7mm。
4
壓電式噴射點膠
壓電式噴射點膠利用了壓電材料的逆壓電效應,噴射頻率高、設備結構簡單,而且噴射可以獲得直徑小至10μm的膠點;另一方面,壓電結構的控制精度高,可提高噴射點膠品質。但壓電式噴射點膠的流量小,若要提高噴射流量需要采用放大機構或增大噴射裝置的體積;另外,使用的壓電材料都比較脆,容易老化。目前壓電式噴射裝置分為以下兩種類型。
第一類壓電式噴射點膠作為熱噴墨印刷技術的主要競爭對手出現,應用于LED中有機顏料的注入,工作頻率可達20kHz。壓電式噴射器應用壓電材料的變形,直接推動流體運動,流體在內外壓力差的作用下加速從噴嘴噴出,形成液滴。這項技術最大的優點在于可以采用噴射器陣列,并且可以以很高的速度噴射材料的小液滴。但只能用于噴射黏度小于0.03Pa·s的流體材料,而且流體中存在的氣泡會導致噴射困難。
第二類壓電式噴射點膠實現噴射的方法是快速的打開和關閉噴嘴,其噴射頻率最高可達200點/s。如圖所示,在閥桿與噴嘴貼合時,噴射閥處于關閉狀態,此時噴射閥中流體處于相對較大的壓力下(黏度為0.03Pa·s的流體受到的壓力超過0.2MPa,黏度更大的材料所受壓力則會更高),然后打開噴嘴,一束流體在壓力驅動下從噴嘴迅速流出,然后關閉噴嘴,快速的關閉將使流體切斷,這一束流體所獲得的動能可以使其以一定速度飛離噴嘴而到達基板上。其中,開關閥動作由壓電致動器控制,壓電致動器與一個杠桿系統或位移放大機構配合使用,可以實現精確快速的閥門開啟和關閉動作。為了精確控制從噴嘴飛出液體的量,噴嘴打開和關閉的動作必須快速且重復性好。要獲得更小的液滴,須要采用尺寸較小的噴嘴,使流體控制壓力更高,并且開關閥動作更快。該噴射技術在電子器件包封的紫外固化粘結劑上的應用非常成功。
噴射式點膠關鍵技術
如前所述,點膠速度、品質以及操作性是評價點膠系統性能好壞的關鍵,其中點膠品質是其評價的重點。噴射點膠具有速度快、操作性好和適應性強等優點。
由于電子封裝過程各個工藝之間相互關聯,而且最終的產品性能也不單單取決于點膠,因點膠品質評定也不存在一個統一的標準。根據點膠技術在微電子封裝中的應用,本文評價點膠品質指標是膠點的準確性與一致性。準確性指膠點大小符合所需要的尺寸,以及液滴的定位準確;一致性指噴射一系列膠點直徑和質量誤差大小。合格的膠點大小合適,形狀為均勻的正圓,并且膠點一致性好;噴射出的膠點出現大小不合格、“衛星滴”或氣泡等都說明點膠品質差(圖10)。影響最終噴射點膠品質的因素有很多,主要有流體黏度及控制溫度、供料壓力、噴嘴形狀、閥桿行程、脈沖寬等。
1
流體黏度及控制溫度
黏度是流體流動性的一種量度,它決定著流體所需要推力的大小,是流體能否形成噴射的關鍵因素,低黏度的流體容易被噴射出去。當流體材料的黏度過大時,流體噴射所需動量增大,會出現流體材料無法噴射出去的現象。因而,一般噴射裝置都會配置溫度控制器,針對黏度較大的流體,可以通過加熱使其黏度下降以達到噴射的條件,噴射出的膠點大小隨溫度升高而增大(圖11)。溫度控制不當會影響最終膠點的品質,過低的溫度使得液滴無法噴射,流體堆積在噴嘴附近,以致影響后續的噴射;過高的溫度則會導致出現“衛星滴”,降低噴射點膠準確度,還會改變流體性能,因此,研究流體材料流變特性及其適宜的噴射溫度很重要。
2
供料壓力
供料壓力的作用是使料筒中的流體材料及時補充至噴嘴附近。通常,黏度大的流體材料需要更大的壓力才能使其流動,因此,針對不同的噴射方式和流體黏度,應當設置不同的供料壓力。一般情況下,壓電式噴射比機械式噴射所需的供料壓力大。
供料壓力影響噴射膠點品質及膠點尺寸。當供料壓力不足時,會出現噴射斷斷續續或是無膠液噴出的現象;供料壓力過大將導致得到的膠點過大,甚至會有多余的膠液在噴嘴周圍堆積,導致噴嘴不能正常工作。另外,隨著供料壓力增大,相應噴射膠點也會增大(圖12)。
3
噴嘴形狀
噴嘴形狀及大小直接影響噴射膠點的品質。噴嘴形狀應當為正圓形,否則將影響點膠的一致
性,而且容易導致流體在噴嘴外部堆積,造成無法繼續噴射;噴嘴尺寸與噴射膠點直徑密切相關,噴嘴越小,膠點越小,但過小的膠點容易導致固定不牢,而太大的膠點會對鄰近元件形成干擾。因此,設計加工合格噴嘴是獲得品質良好、大小合適的膠點的必要前提。
4
閥桿行程
噴射點膠工藝中,閥桿行程大小決定著閥桿推力的大小,小行程能獲得尺寸較小的膠點(圖13),但過小的行程則會導致閥桿推力小,流體因此不能獲得足夠的動量克服表面張力而噴射出去,而在噴嘴外部形成堆積,故機械式噴射點膠中,閥桿行程一般不小于0.5mm;行程大時,膠液獲得的動量較大,膠點噴射出去的速度很高,甚至會出現霧化現象,容易在膠點形成許多的“衛星滴”。
壓電式噴射點膠中,閥桿行程大小還與流體材料黏度有關,黏度大的流體應設置較大的閥桿行程,使流體能夠及時補充以維持連續噴射;黏度小的流體流動性能好,只需設置較小的行程。
5
脈沖寬
機械式噴射點膠中,脈沖寬指驅動氣壓作用使閥桿抬起時間的長短;在壓電式中則是指壓電陶瓷導通脈沖寬,即一個周期內閥門開啟時間。通常,通過控制脈沖寬時間可以得到尺寸合適、一致性良好的膠點。脈沖寬決定著膠液的補充時間,一方面,它影響噴射膠點的大小,并且與膠點尺寸大小成正比(圖14),另一方面,它影響了噴射膠點的品質,脈沖寬時間太短,會出現膠液堆積在噴嘴處而無法噴射的現象;脈沖寬時間過長會由于膠液補充量大而引起多余膠液滲出。
除了以上參數,影響點膠品質的還有操作電壓、噴嘴孔徑、脈沖頻率等。噴射點膠工藝實際應用中,可以通過調整以上參數來改善噴射膠點品質。膠點品質的好壞一般與多個因素相關,任何一個參數的變化都可能會導致膠點其他方面的改變。當噴射點膠過程中出現有缺陷的膠點時,調整過程要按由點及面的方式進行,應對這種可能的因素逐項檢查,進而排除。總之,在生產中應該按照實際情況來調整各參數,既要保證生產質量,又能提高生產效率。
審核編輯:郭婷
-
pcb
+關注
關注
4317文章
23004瀏覽量
396251 -
封裝
+關注
關注
126文章
7780瀏覽量
142722 -
微電子
+關注
關注
18文章
376瀏覽量
41166
原文標題:【半導光電】微電子封裝點膠技術的研究進展及特點分析
文章出處:【微信號:今日光電,微信公眾號:今日光電】歡迎添加關注!文章轉載請注明出處。
發布評論請先 登錄
相關推薦
微電子封裝無鉛焊點的可靠性研究進展及評述
CAD技術在電子封裝中的應用及其發展
微電子封裝的概述和技術要求
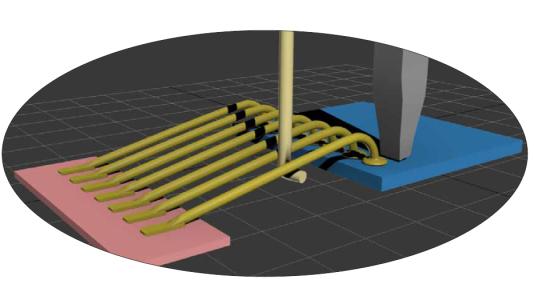
評論