多年來,線束制造商僅將3D打印用于基本夾具和工具、原型應用或對成品線束進行連續性測試所需的連接器。不過,現在,3D打印機供應商已經推出了機器,使公司能夠經濟地打印各種連接器和固定裝置。
“能夠定制我們3D打印的線束組件是一個很大的好處,但還有其他好處,例如糾正缺陷和更快地完成項目,”制造電線的ElectrexI工程服務總監Tim Buhler承認自1970年代后期以來,越野車和公路專用卡車的線束很難制造。
“提高線束質量的需求是我們開始3D打印零件的主要原因,包括測試夾具、將電線固定到板上的夾子,以及幫助組裝人員定位、定向和識別線束上的連接器的支架。”
3D打印還使Electrex能夠幫助其客戶。例如,去年,該公司為生產拖拉機的優先客戶打印了一種獨特的連接器,用于對線束進行功能和連續性測試。這提高了線束的質量。
直到最近,只有汽車和航空航天等成熟行業的制造商使用3D打印來發揮自己的優勢。現在,線束制造商也在做同樣的事情,鑒于影響制造的供應鏈問題,時機再好不過了。
3D打印的傳統優勢——例如節省金錢和時間,以及享受更大的設計自由度和材料靈活性——吸引裝配商與其他制造商一樣多。但是,增材制造也使線束裝配商每天減少對第三方零部件供應商的依賴。
聽Stratasys商業應用工程師Allen Kreemer說,僅使用3D打印來制作原型連接器的日子已經一去不復返了。他說,得益于2021年7月推出的StratasysH350機器,線束制造商現在可以按需生產高質量的連接器。
“H350使用的先進技術已經投入使用近15年,從本世紀初在拉夫堡大學完成的研究工作開始,”Kreemer解釋道。“但是,直到最近幾年,它才準備好用于線束和其他市場。其中包括汽車、白色家電、電子產品、重型設備和休閑車行業。”
Stratasys的商業應用工程師Alec Logeman指出,H350的關鍵是其選擇性吸收融合(SAF)技術。SAF使用反向旋轉的滾筒將粉末層涂覆到打印床上,然后使用吸收液對零件層進行成像。然后通過使紅外燈在整個印刷床跨度上通過,這些層被熔化和熔合。
工業級壓電打印頭將流體應用于指定區域,以創建每個零件的橫截面。該過程始終在整個打印床上以相同的方向執行,以提供均勻的熱體驗和零件一致性,無論它們在構建中的位置如何。
“制造商可以根據他們想要的任何引腳數定制任何形狀的打印連接器,”Logeman說。“印刷連接器主體取代了通常注塑成型的連接器,并且插針在單獨的過程中插入。
“在H350上,其大型工作范圍(315x208x293毫米)使公司能夠在13小時內3D打印多達200個標準三引腳Molex型連接器,”Logeman繼續說道。“在同一空間內可以打印近400個較小的連接器。生產量會因最終用戶而異,但無論公司是每周還是每年打印數千個連接器,打印機都具有成本效益。”
對于H350,Stratasys使用第三方認證的粉末材料PA11,而不是樹脂或燈絲。PA11是一種生物基塑料,由源自可持續蓖麻油的可再生原料制成。
“要在切換到3D打印時獲得最佳生產零件,請考慮將設計用于增材制造實踐,”Kreemer建議道。“在調整現有設計時實施這些策略可以使零件制造得更快、更便宜、更好。”
組裝人員在組裝過程中使用各種類型的固定裝置將線束安裝到電路板上。一種類型是每個連接器都插入其中的塑料支架或蓋子。
惠普公司AMS地區業務開發經理Isabel Sanz表示,惠普的JetFusion5200和5210型號非常適合3D打印連接器支架。兩臺機器都使用Multi-JetFusion(MJF)技術進行大批量生產。MJF具有一個帶有打印頭的可拆卸構建單元,該打印頭一次將熔合劑噴射到二維層(0.003英寸厚)形狀的粉末(PA11或PA12)表面上。然后紅外燈加熱并熔化粉末,然后沉積另一層粉末,并重復該過程。
每臺打印機的工作范圍為15x11x15英寸,噴射系統每英寸每秒可精確噴射3000萬滴定影劑。根據需要,打印頭可以將細化劑涂抹在預期定影區域旁邊的區域上,以防止熱滲出并提高零件性能。該代理還產生諸如圓形邊緣之類的特征,以防止線束裝配期間電線和連接器損壞。
Stratasys商業應用工程師Alec Logeman指出,H350的關鍵是其選擇性吸收融合(SAF)技術。SAF使用反向旋轉的滾筒將粉末層涂覆到打印床上,然后使用吸收液對零件層進行成像。然后通過使紅外燈在整個印刷床跨度上通過,這些層被熔化和熔合。
“任何一種型號都可以在一個打印作業周期內打印多達184個支架,其中包括11小時的打印,然后是36小時的冷卻,”Sanz解釋道。“我們的測試和研究表明,印在5200系列上的支架可將交貨時間從2周縮短到6周,縮短到1天。當以每天250到300個的速度制造時,持有者的成本從每部分6美元到7美元不等。與CNC加工的刀柄相比,這意味著最多可節省75%。”
Electrex在其北美地區(運營著12臺2D和3D打印機堪薩斯州3臺,墨西哥9臺),以生產各種夾具和連接器支架。其主要打印機是Comgrow制造的CrealityEnder5Plus模型,該模型使用熔融沉積建模(FDM)工藝。打印機將熔化的長絲材料(逐層沉積在構建平臺上,直到部件完成。
“我們的大部分零件都使用標準的現成打印機,”Buhler指出。“它們的尺寸最大為12平方英寸,大多數部件的尺寸小于6平方英寸,小到1平方英寸。”
線束制造商Cesar-ScottInc.(CSI)也依賴基于FDM的3D打印機來生產連接器支架。他們的Atom工業打印機(來自TCCPrint)在12英寸見方的工作臺內制造PLA或丙烯腈丁二烯苯乙烯(ABS)部件。
CSI成立于1988年,從1994年開始生產線束,從2012年開始生產開關線束。這種類型的線束為燃氣灶、燒烤和燃氣烤架以及其他電器上的電子火花模塊供電。
“自2015年以來,我們一直在3D打印我們的大部分原型開關,以及連接器支架、夾具、固定裝置以及機器安全防護裝置和備件,”所有者兼聯合創始人C.Gustavo Farell解釋道。“去年,我們制造了近500,000根線束,每根線束都有4到5個開關和2到10根電線。對我們來說,使用3D打印的主要好處是它加快了失敗的速度,”Farell繼續說道。“我的意思是,我們打印錯誤零件的速度越快,我們就可以為正確的零件制造用于生產的模具,效率和成本效益就越高。平均而言,大約需要3次嘗試才能做到正確。”
Farell說CSI以多種顏色打印支架以匹配連接器的顏色。這有助于確保組裝人員將正確的連接器放置在支架中,并將正確的電線放置在連接器中。顏色包括白色、透明白色、黑色、紅色、藍色和綠色。大多數支架是一到兩平方英寸,但可以大到八平方英寸。
CSI在其線束中使用的一些開關由第三方打印并寄回。Farell表示,這些開關需要通過立體光刻(SLA)印刷工藝安裝到PCB上。
該過程及其設備可確保開關滿足機構批準的更高溫度和分辨率要求。低端設備可能并不總是滿足這些要求。這項工作由多家公司以及德克薩斯大學埃爾帕索分校的3D工程和增材制造技術中心完成。
Stratasys的H350和OriginOne打印機都可以3D打印連接器支架。后一種型號支持高達192x108x370毫米的零件尺寸,并可打印尺寸小于50微米的細節。
經認證的第三方材料包括工業樹脂,以及耐高溫、耐用的彈性體、通用和醫療級材料。OriginOne的可編程PhotoPolymerizationP3軟件精確地協調光、溫度、拉力和氣動,以優化零件質量。
幫助線束安裝的配件也可以進行3D打印。其中包括夾具、支架、安裝支架和布線輔助工具。
最近,電纜管理專家Hellermann Tyton(HT)聘請Fast Radius來3D打印自定義布線輔助設備,HT工作人員將這些輔助設備連接到成品線束上,以便于安裝在車輛中。輔助設備的大尺寸和復雜性迫使HT工程師將設計分成多個較小的部分,然后在HPJetFusion機器上打印。
HT的產品設計師Ethan Fish表示,FastRadius僅在六周內就為第一次運行提供了3,000多個部分。HT工人隨后將這些零件組裝成1,235個零件。每個打印部分的長度接近13英寸,最終組裝出來的長度接近46英寸。
為該項目雇用FastRadius幫助HT為其汽車客戶消除了注塑模具和試驗的前期成本。HT還節省了近兩個月的項目交付時間和近100萬美元的項目總成本。
一些組件供應商更喜歡自己進行3D打印。例如,TEConnectivity最近應航空制造商的要求為其D369連接器設計并3D打印了一個原型安裝支架。支架與安裝在飛機外殼內的連接器正確且牢固地匹配。
除了快速需要支架外,制造商還要求它由航空級材料制成,精度為±0.002英寸。持有人還必須通過行業標準的適航性和環境測試,以防止在各種操作條件下發生故障。
由于過去的經驗,TEConnectivity的工程師在該項目中使用了Stratasys OriginOne。與此同時,Stratasys的專家與Henkel Loctite合作開發了一種用于該應用的阻燃光聚合物。
審核編輯 :李倩
-
連接器
+關注
關注
98文章
14345瀏覽量
136205 -
線束
+關注
關注
7文章
972瀏覽量
25947 -
3D打印
+關注
關注
26文章
3544瀏覽量
108884
原文標題:工高芯城 | 線束裝配商正在使用3D打印定制連接器
文章出處:【微信號:工高連城連接器商城,微信公眾號:工高連城連接器商城】歡迎添加關注!文章轉載請注明出處。
發布評論請先 登錄
相關推薦
3D打印汽車零部件模型定制服務,多種材料、快速打印-CASAIM

3D掃描技術醫療領域創新實踐,積木易搭3D掃描儀Mole助力定制個性化手臂康復輔具
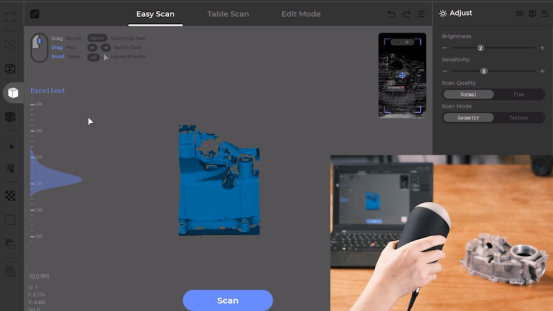
3D打印技術應用的未來
物聯網行業中的模具定制方案_3D打印技術分享
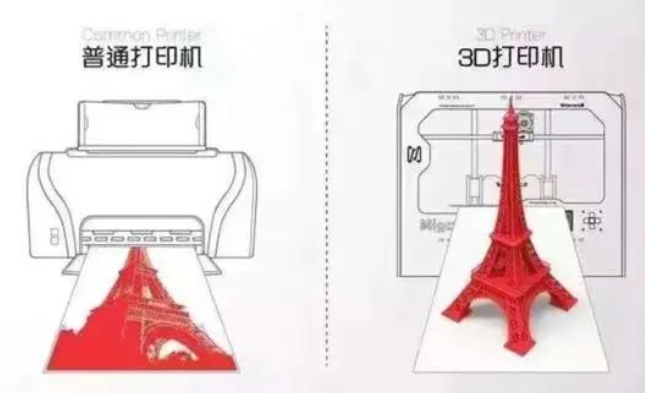
應用在3D打印機的BD系列金屬連接器
3D打印汽車零部件建模設計3D打印服務
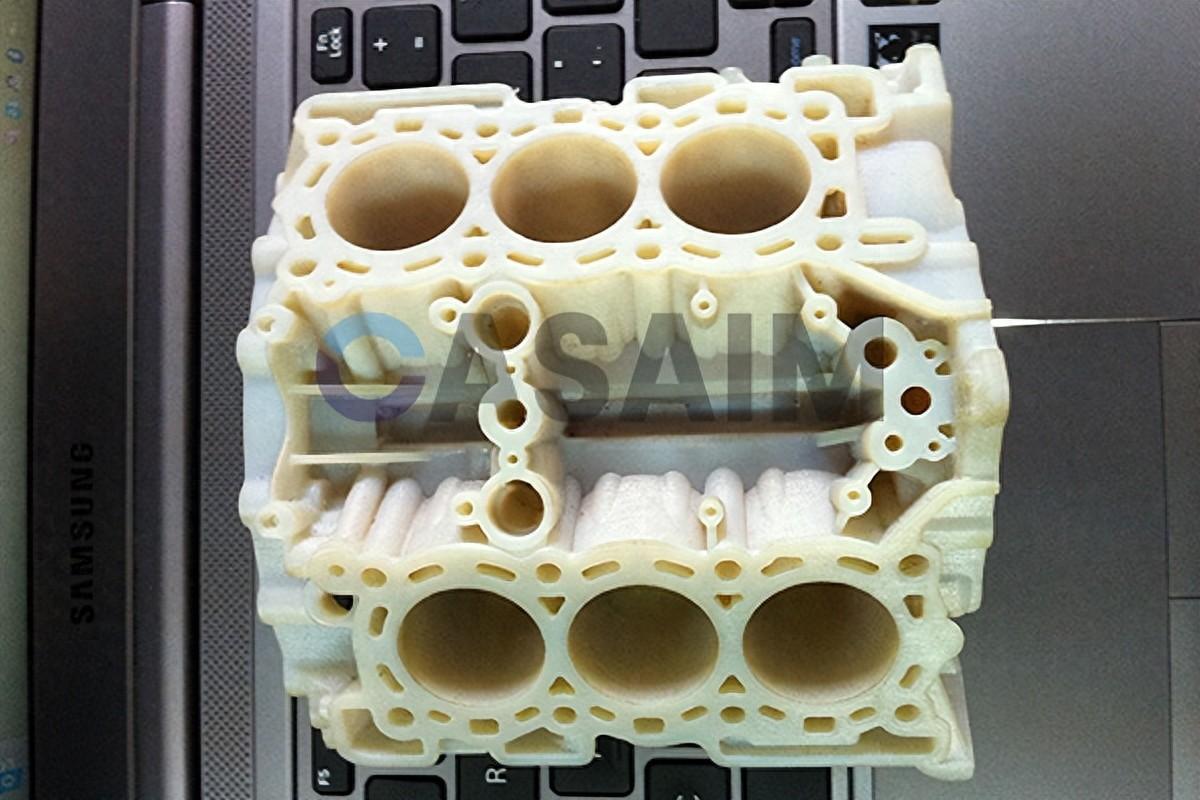
什么是EdgeLock 線對信號卡連接器?-赫聯電子
能入3D打印機法眼,BD系列工業級連接器究竟有哪些獨特之處?
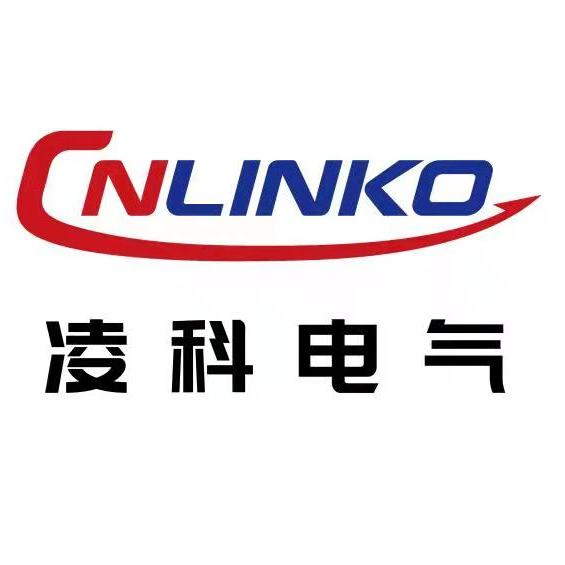
CASAIM沙盤模型3D打印的優勢和應用
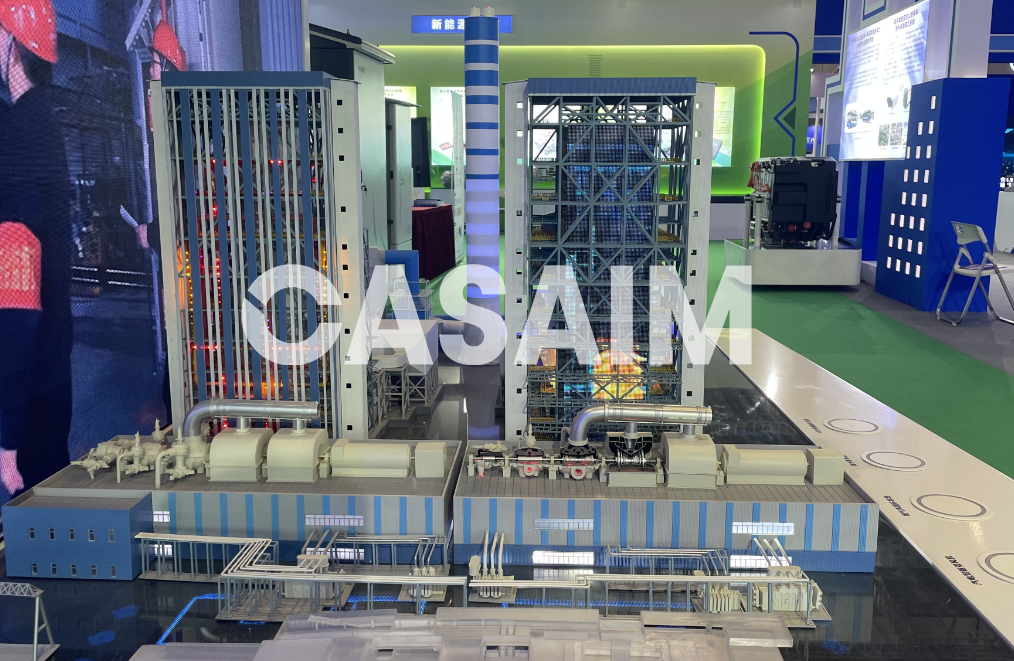
評論