在產品設計生命周期中,大規模制造是在產品發布的最后階段完成的。有幾個因素,如良好的設計,最少的PCB組裝重新操作和迭代,更少的材料開銷和勞動力成本,在這個階段要考慮為OEM和企業制造有價值的產品。
為了實現這一目標,可制造性設計(DFM)和裝配設計(DFA)技術以集成和受控的方式被廣泛使用。有時,也稱為DFMA(制造和裝配設計),用于通過設計和流程改進來最小化產品成本和時間。
在制造服務中,DFM是用于易于制造的過程,而DFA是用于產品設計中易于組裝的設計方法。適用于PCB制造或PCB組裝或產品組裝。良好的DFMA實踐可以加速制造過程,并提供降低成本,材料浪費,提高可用資源產量的額外優勢,并最終節省時間并擴大生產規模。
DFT是一種設計方法,旨在通過板上的測試點確保PCBA級別的操作和功能測試。一旦物理制造過程完成,DFT幫助驗證電路板的組裝,并確保產品硬件制造無缺陷。
在本文中,我們將仔細研究DFA/DFT/DFM指南及其對生產過程的重要性。讓我們開始吧。
DFM指南
消除昂貴、復雜或不必要的功能,輕松制造
避免嚴格的公差,適應制造工藝能力(例如PCB堆疊,走線寬度間距,厚度和通孔/孔/切口工具)
PCB面板化是PCB制造成本中非常重要的因素
最好避免有鋒利邊緣和點的零件,最好使用徑向倒角
盡量避免在設計中出現笨重的部件,以減少疲勞和提升挑戰
避免剛柔結合PCB設計(如果不是強制性的)
避免腳印中出現不均勻的焊盤和不規則形狀,以獲得更好的蝕刻效果
最大限度地減少阻焊層偏移,以便在回流過程中獲得足夠的焊點
使用更多的熱通孔(而不是更大的通孔)
DFA指南
最大限度地減少零件數量和零件類型,以減少庫存處理,采購,庫存和組裝時間
使用具有自定位/對齊功能且無法正確安裝的部件
設計具有自緊固功能的零件,以支持機械挑戰
使用單面 PCB 進行零件放置
遵循“自上而下”的組件方法以獲得重力優勢
在產品設計時考慮不同的參數,以實現平穩的裝配過程,如系統分區、互連類型及其在產品內部的組裝、尺寸和零件包裝、組裝零件之間的最小距離等。
考慮到裝配工藝能力,為零件提供足夠的PCB邊緣間隙,并在密集電路板中保持兩個組件之間的最小間隙
對稱排列相似的組件,便于安裝
注意配接連接器、電纜方向/高度和面積要求
避免使用在組裝過程中容易纏結且難以拾取/處理的零件
避免焊盤中的不均勻焊盤和不規則性,因為表面貼裝技術后需要手動修飾才能實現最佳可焊性
大尺寸熱通孔會影響GND焊盤的可焊性,因此通過帳篷/填充/堵塞(通常是樹脂填充或導電/非導電材料)使用。
DFT指南
從開發或原型階段開始實施產品可測試性
覆蓋所有關鍵信號以實現可測試性
應具有單側測試點,以增加使用釘床 (BoN) 進行測試設置的優勢
從設計階段開始就考慮測試點的大小和測試點的最小間距,以便在能力范圍內實現釘床 (BoN) 設置
確保TAP信號(例如xJTAG)和具有電壓電平分離的緩沖TAP信號之間的低偏斜(在TestFixture接線內部)
考慮將多板面板作為一個單元進行測試
測試點應有足夠的間隙到焊盤/組件/PCB邊緣
為了實現完整的ICT(在線測試)覆蓋,每個設計網絡都應該有測試點
強調測試流程以隔離與組件故障和制造錯誤相關的問題
選擇正確的彈簧加載探頭(引腳)以促進正確的電氣連接
避免使用笨重和加高的組件 飛針測試
每個單元的測試時間至關重要,目標應該是盡可能少地實現
測試自動化應由易于測試、有限的測試點、簡單的系統反饋機制驅動
設計測試夾具,以涵蓋半自動化或全自動化的功能驗證
審核編輯:郭婷
-
連接器
+關注
關注
98文章
14326瀏覽量
136170 -
PCB
+關注
關注
1文章
1777瀏覽量
13204
發布評論請先 登錄
相關推薦
PCBA加工中的靈魂:揭秘芯片燒錄的重要性
元器件在電路設計中的重要性
DFM在實際應用中的關鍵考慮和策略
使用xtr111應用在產品設計中,運行一段時間過后設備不工作怎么解決?
IoT網關在工業應用中的重要性及應用
論RISC-V的MCU中UART接口的重要性
什么是DFM?DFM檢查在SMT貼片加工生產中的重要性
蜂鳴器的用途和重要性
請問DFM是如何高效PCB/PCBA可制造性設計分析的?
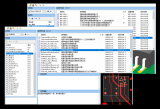
DFM引領電子行業變革,智能制造助力高效生產
淺談產品電磁兼容性設計培訓的重要性
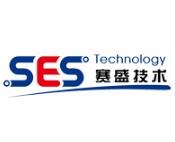
評論