卡扣連接器(也稱為緊固件或機構)用于將一個部件直接連接到另一個部件,在空間受限的環境中,它們通常用于組裝復雜的注塑成型零件。這種連接結構由于連接方便、加工容易、成本低,被廣泛應用于電機外殼連接鍵的設計中。
眾所周知,受擠壓機構的彎曲特性會嚴重影響電機的性能。在研究這些特性時,直接使用目標樣機進行驗證是很耗費資源的,可能會對樣機造成損壞并浪費大量資金。但是,隨著計算機技術的發展,這些問題都可以通過 CAE 模擬的方法來解決[1]。有很多關于卡扣的設計研究,但是大部分的研究仍是針對傳統卡扣,并且多數集中在塑料卡扣的設計中。一些研究表明,傳統卡扣設計的工作原理獨立于制造過程,并提出了增材制造卡扣設計指南,很多先前的方法需要適應新制造技術的制造方式[2-3]。
強度、約束、兼容性和穩健性已被確定為卡扣設計的關鍵要求,前三個在設計階段是必不可少的。通過遵循一般設計指南,可以較容易地滿足這些要求。穩定性高是指尺寸變化的容忍度。堅固性是不可預測的,尺寸會根據制造和材料特性的差異而變化。當我們模擬模型時,假設材料是各向同性的,但材料很難完全各向同性。最關鍵的尺寸變化是刀具和粘合面之間的匹配角度。過盈量決定了配合力和預緊力的質量。由于卡扣連接器的行為類似于懸臂,因此配合力會隨著干擾的增加而增加。過少的干涉會導致裝配松動,過多的干涉會導致組裝困難或可能導致零件和連接器的永久變形,從而導致廢品率高而影響效益。
與恒力機構一樣,卡扣連接器是一種封閉結構,當受到一定的輸入位移時,它會提供一定范圍的恒定反作用力。本研究的卡扣連接器是用于連接電機金屬部件,卡扣連接器的質量可以很大程度影響電機的生產以及質量。
大多數的研究主要集中在塑料材料上,很少有關于電機外殼金屬卡扣的研究。本文研究了刀具的形狀如何影響卡扣材料的變形,評估卡扣壓型的整個過程以獲得刀具的反作用力,從而調整模具進行沖壓成型。
1 材料特性及典型的封裝結構
1.1 材料特性
對于塑性材料,其變形過程有四個階段:彈性階段(O-a)、屈服階段(a-d)、應變硬化階段(d-e)和頸縮階段(e-f),分別表示在圖 1 中[14]。從O到a的階段定義為載荷隨應變線性增加,當載荷達到某個最大值a后,屈服階段開始,應力增加很小,但應變增加很大。經過b后,應力減小,應變增大,直至穩定階段,在應變增大過程中應力保持相對穩定,略有波動。試樣一部分的直徑開始減小,這種現象稱為頸縮(e-f)。頸縮開始后,稍低的載荷足以使試樣進一步伸長,直到它最終破裂。這意味著無論負載是否存在,材料都會發生永久變形。
圖1 材料的拉伸曲線
為預測不同尺寸結構的性能,采用有限元分析方法評估性能。本文使用ANSYS Workbench 用于壓縮模擬,而有些論文使用 Abaqus 進行壓縮模擬,雖然軟件不同,但都是基于有限元方法對模型進行離散化分析[15-17]。材料的力學性能如表1所示。多線性各向同性硬化參數如表2所示,本文使用表2數據進行分析。
表1 材料力學性能
表2 鍍鋅鋼板多線性各向同性硬化模型
1.2 典型的封裝結構
圖 2 顯示了典型的電機卡扣結構。四位槽對稱分布在一個空心圓柱體上,相鄰槽之間間隔90°。R1和R2分別是內半徑和外半徑,H1和h1分別是圓柱和孔的高度,b1是刀具的寬度。L1為凹槽寬度,L2為最大夾鉗寬度,L3為刀具寬度,L4為夾鉗高度,L5為最大凹槽寬度。α是內刀角,β是外刀角。四個孔對稱分布在一個空心圓柱體上,相鄰兩個孔之間的間距為110°。
圖2 電機外殼結構示意圖
在刀具壓縮卡扣結構過程中,壓縮位移S可以表示:
(1)
式中:V0是壓縮開始時壓縮工具的速度;Fc是壓縮過程中的壓縮力;m是工具的質量;t是壓縮時間。根據圖1的材料特性,初始階段不可避免地存在一個載荷階段a-c,其中受力大于穩定階段。本研究認為,當穩定階段的持續時間占壓縮持續時間的 70% 以上時,階段(a-c)可以忽略不計[18]。在這個假設下,壓縮力被認為是恒定的,并且接近于穩定階段的平均力。然后,假設壓縮結束時,速度下降到0,式(1)可簡化:
(2)
式中:是壓縮過程中的平均力;S是總位移;t是壓縮過程的整個時間。通過推導可以得出,在壓縮過程中,可以按照位移約束的方式進行載荷加載在ANSYS軟件中。
1.3 刀具角度的不同參數
刀具的穩定位移是在壓縮過程中表現出來的。在壓縮過程中,變形主要發生在卡扣鎖緊部分處,如圖 3 所示。
圖3 卡扣鎖緊部分凸起筋條
壓縮過程中鐵殼的變形主要受刀具角度的影響。刀具角度α會影響圖3中鎖緊部分的變形,影響電機外殼的預緊力。本研究確定了鎖緊部分和刀具的尺寸。本研究介紹了95°、100°、105°這三個不同的角度來尋找最合適的α角度,壓縮過程中的最大壓縮為1 mm,確保刀具能夠剛好碰到L4的底部并且不會破壞電機外殼。整個過程耗時為 1 s,包含20 個子步。
枚舉法通過枚舉問題的所有可能答案,找到滿足給定條件的合理解。它通常計算量大、效率低,但是,當用于小規模問題時,它無需復雜的計算和推導就能更快地達到解。本研究引入ANSYS Workbench 2021R1,比較不同刀具角度的性能。在 Mechanical Workbench 中,通過 User Defined Result 獲取變形后的節點坐標:LOC_DEFX、LOC_DEFY、LOC_DEFZ。通過坐標計算,得到空間中兩個端點(圖3中紅色星狀標識)的距離。
刀具角度列于表3,唯一不同的是角度α,三個仿真模型的其他參數均相同。L1取值為5.2 mm,卡扣鎖緊部位的寬度為2 mm。使用式(3)計算表4中的數據,得到卡扣鎖緊后兩個端點的空間距離,從而對比差異。
兩個節點的空間距離公式:
(3)
通過對比如表4所示的結果,可以得到在刀具作用的過程中,卡扣向內變形,鎖緊端蓋,α=100°時變形后距離最小,變形效果最好。
表3 不同的刀具角度的模型參數
表4 不同刀具角度對應的變形值
1.4 網格無關性驗證
過多的網格會導致計算量的增加,過少的網格也會導致計算精度的降低,本文對電機模型進行網格無關性驗證,以保證在滿足精度的前提下盡量縮小計算量。測試在DELL 工作站Precision 5820 Tower上測試,處理器Intel(R) Xeon(R) W-2275 CPU @ 3.30 GHz并帶有256 GB內存,測試軟件平臺為Windows 10 專業工作站版,版本號20H2,測試仿真軟件平臺為ANSYS Workbench 2021R1 帶有8核HPC, 最大算力可以調用12個CPU物理內核,所有軟件皆在正版授權軟件中進行測試。測試模型的刀具角度為95°,分別進行三種單元密度網格無關性驗證[19-22],網格劃分方法為全局網格,采用1.5 mm網格尺寸,在卡扣部分采用局部加密方式進行加密,加密網格尺寸及驗證結果如表5所示。根據表5所示的數據,選擇網格尺寸為0.5 mm時的單元尺寸進行計算。
表5 網格無關性驗證
1.5 邊界條件
為了獲得整個壓縮過程中殼體的變形情況,首先通過建模將刀具與電機殼體位置對應,刀具內側與殼體卡扣凸起部分相接觸,由于有潤滑的存在,所以刀具與殼體部分的接觸設置為無摩擦接觸。在實際加工過程中,殼體固定在操作臺上,將殼體下表面進行約束處理,約束6個方向自由度。刀具在下壓過程中,電機端蓋是蓋在電機殼體上的,并且沒有添加其他約束,端蓋只與電機卡扣凹槽部分進行接觸,在電機殼體周向移動,徑向無法移動,設置好的邊界條件如圖4所示。端蓋釋放Z方向的自由度,約束X、Y兩個方向的平動自由度,刀具運動方向如圖5所示。
圖4 電機殼體端蓋約束
圖5 刀具運動方向
1.6 不同刀具角度導致的殼體變形情況
刀具在下壓過程中共耗時1 s,分20個載荷步進行施加,在進行鎖緊工藝時,整體應力開始變大,材料產生塑性變形,圖6~圖14列出了100°刀具角度情況下殼體的塑性變形情況。本文的分析在滿足殼體平面度要求以及總體變形要求的情況下,盡可能地鎖緊端蓋,以免端蓋出現松動。通過仿真分析可以直觀地看出,卡扣卡口部分已經有明顯的變形,但是變形只在卡扣鎖緊部位,并未傳遞到電機殼體的其他部位,這正是加工生產所要的效果,符合預期的設計。這樣既可以保證卡扣卡位的精準鎖緊,又不會影響電機殼體的其他部位的變形,從而影響電機的性能。
圖6 100°刀具加工殼體變形情況
圖7 100°刀具加工殼體局部變形情況
圖8 100°刀具加工殼體端蓋變形情況
圖9 95°刀具加工殼體變形情況
圖10 95°刀具加工殼體局部變形情況
圖11 95°刀具加工殼體端蓋變形情況
圖12 105°刀具加工殼體變形情況
圖13 105°刀具加工殼體局部變形情況
圖14 105°刀具加工殼體端蓋變形情況
1.7 不同刀具角度壓縮卡扣結構的壓力
通過軟件計算,可以得到刀具在下壓卡扣的過程中需要多大的下壓力,才可以將卡扣鎖緊,用于指導實際加工生產中,相關工藝的下壓力完成裝配。本文對刀具的三個角度的模型進行分析,并得出下壓力的精確值,如表6所示。不同刀具角度的下壓力是不同的,當刀具角度為105°時,下壓力最大。較大的下壓力并不是生產中最理想的狀態,有可能導致殼體的其他部位變形。而較小的下壓力會有壓不到位的風險。100°的刀具角度是三種刀具中最優的。
表6 不同刀具角度的下壓力
1.8 鎖緊結構尺寸的影響
圖2中,L1的尺寸與端蓋配合,無法進行更改;L2的尺寸為加工后的凹槽,可以通過更改L2的尺寸來調整鎖緊結構的變形,從而影響鎖緊的效果。同時,調整L2的尺寸,也會影響刀具的壓力,較大的壓力會對整個結構的變形產生不穩定的作用,壓力要盡可能控制在一個合理的范圍內。在刀具角度為100°的情況下,L2的初始尺寸為9.2 mm,此時,L1的尺寸為5.2 mm,單個鎖緊結構的寬度T為2 mm,寬度的計算公式如下:
T=(L2-L1)/2
(4)
不同的鎖緊寬度對壓力的影響如表7所示。通過整理表8數據,并根據式(4)計算得到在三種寬度分別為1.7 mm,2 mm,2.3 mm的情況下,相同的刀具角度,不同的寬度值T,卡扣鎖緊部位表現的性質不同,當寬度為2 mm時,鎖緊效果最好。
表7 不同的寬度對壓力的影響
表8 刀具角度100°對應的變形值
2 實驗驗證
根據仿真結果,確定刀具角度為100°,L2為9.2 mm時的殼體在所有模型中是最優的,此時卡扣鎖緊部分的寬度T為2 mm。下面對此參數下的模型制作樣機,來驗證仿真的精確性。
實驗通過兩個測試來確定仿真方案是否可行,首先是壓力測試,而后是端蓋的平面度測試。
2.1 刀具鎖緊卡扣實驗
卡扣鎖緊實驗主要進行壓力的評估,通過限定力學試驗機的位移進行,通過傳感器測量壓入過程中的壓力大小。實驗中按照仿真數據,加工了五個樣件,每個樣件隨機編號,將樣件放到夾具上,放穩并確定電機殼體沒有翹曲。
實驗后的數據如圖17所示。從圖17中可以得出,實驗過程中,材料沒有表現出非線性變形,殼體在壓縮過程中表現出較為一致的線性,而仿真數據表現出一定的非線性。刀具位移為1 mm時的仿真和實驗數據結果如表9所示,實驗的壓力值分布范圍為3 215~4 783 N,實驗分布范圍較大。用相同位移的結果進行對比顯然產生較大的誤差。對實驗數據進行整理,將初始的非線性段刪除,取線性較好的一段數據進行擬合,在Excel中可以得到擬合曲線的線性公式,并得出斜率,就是實際位移1 mm對應的近似壓力值。取斜率的平均值,通過數據分析可以得出,實際殼體下壓1 mm,需要5 964.92 N的壓力。仿真與實驗的誤差為8.5%。
圖17 實驗數據與仿真數據
表9 實驗數據和仿真數據壓力對比
2.2 平面度測量
平面度測量用于檢測電機殼體在進行端蓋鎖緊的過程中,是否發生了其他部位的變形,導致殼體扭曲或者端蓋軸心偏心,影響電機質量。在實驗樣本中,取三個樣本作為測量對象,通過對電機殼體進行四個點的平面度測量,平面度測量位置如圖18,測試結果表10、表11所示。分析結果表明,鎖緊卡扣前后的平面度差值在0.02~0.10 mm之間。
圖18 殼體平面度測量位置
表10 實驗前后殼體的平面度測量
表11 實驗前后的殼體變形情況
2.3 端蓋推出力測量
在壓緊端蓋后,為了保證端蓋的結構穩定,對端蓋進行推出力測試。通過推力計穿過電機殼體推出端蓋,從而測試卡扣結構的強度。固定電機殼體,而后沿著殼體軸向施加載荷,端蓋和卡扣失效瞬間會伴隨“嘭”的一聲聲響,得到數據如表12所示。根據表12數據,可以直觀地看出,端蓋在鎖緊后較為堅固。
表12 端蓋推出力測量
3 結 語
本文建立電機殼體鎖緊卡扣的仿真模型,通過ANSYS Workbench有限元軟件分析,確定了合適的刀具角度以及卡扣部分結構的尺寸,闡明了電機殼體加工過程中的重要尺寸及其影響,進行了網格無關性驗證,確定合適的網格尺寸以及數量,用于快速計算求解結果,以適應工程需要。
研究結果發現:
1)電機殼體封裝端蓋的過程中,刀具的角度以及卡扣的尺寸對鎖緊效果影響較大,材料在受到刀具壓縮后,開始呈現出屈服硬化現象,并沿著設計好的方向進行塑性變形。變形過程中,變形只出現在卡扣部位,未傳到電機殼體的其他部位,保證了加工的精確性。
2)雖然材料參數和實際使用鍍鋅鋼板材料一致,但是在實際的仿真和實驗中,二者也表現出了不同的性質。仿真中,材料表現出較為明顯的非線性性質,并且曲線弧度較為平滑,與理想的材料力學拉伸實驗曲線較為接近;實驗中,材料隨著刀具的下落位移增加,表現出接近線性關系的性質。且隨著位移的增大,仿真的壓力趨近于平緩,而實驗的壓力趨勢仍然呈現原有線性性質。二者在相同位移的情況下,實驗與仿真誤差較大,對實驗數據進行線性擬合后,誤差在可接受范圍內。由于實驗中很難確定凹槽部分的具體尺寸并保證一致性,在壓縮的過程中也存在其他因素干擾,無法達到仿真的理想情況。并且刀具的初始位置直接影響了實驗結果,按照仿真曲線所表現出來的趨勢,仿真1 mm的位移情況對應實驗的位移會在1.2 mm~1.6 mm位移之間。
3)根據仿真數據進行樣件制作并實驗,仿真中,殼體除卡扣部分外皆無變形情況;實際的實驗中,在對殼體進行端面平面度測量時,檢測的三個殼體均有少量變形,變形量非常小,最大只有0.1 mm,仿真和實驗有一點差異,差異在可接受范圍內。端蓋鎖緊后的強度較高,滿足生產要求。
審核編輯:郭婷
-
連接器
+關注
關注
98文章
14345瀏覽量
136208 -
電機
+關注
關注
142文章
8940瀏覽量
145144
原文標題:電機殼體封裝工藝研究
文章出處:【微信號:EDC電驅未來,微信公眾號:EDC電驅未來】歡迎添加關注!文章轉載請注明出處。
發布評論請先 登錄
相關推薦
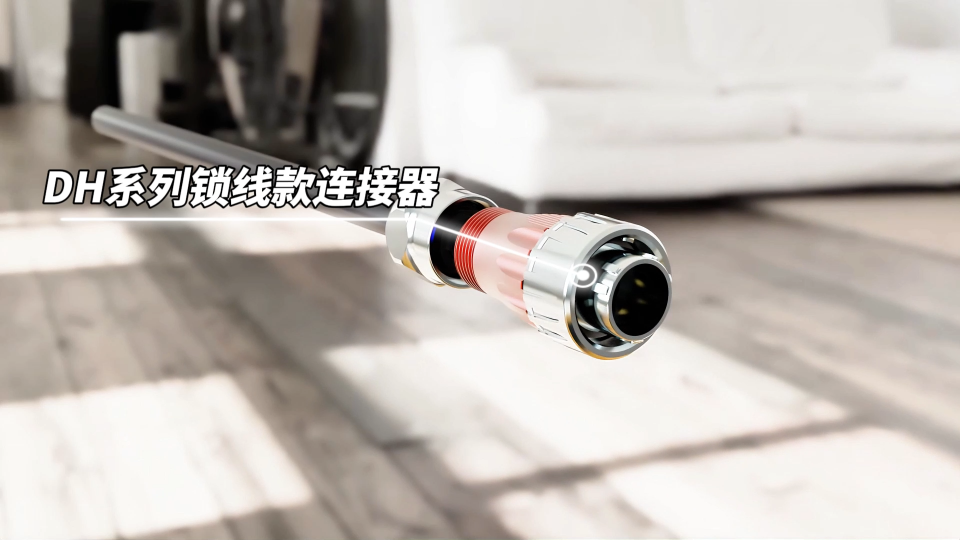
I-PEX連接器,內置鎖扣功能的新款射頻連接器-行業中的創舉
TE Connectivity 三重鎖扣式電源連接器
為您介紹:三重鎖扣式電源連接器
重載連接器能廣泛應用于需要進行電氣和信號連接的設備
卡扣設計的排針和母連接器更適用于汽車測試設備
連接器外殼的作用是什么
康瑞連接器--KR2014 單排-帶扣-線對板連接器
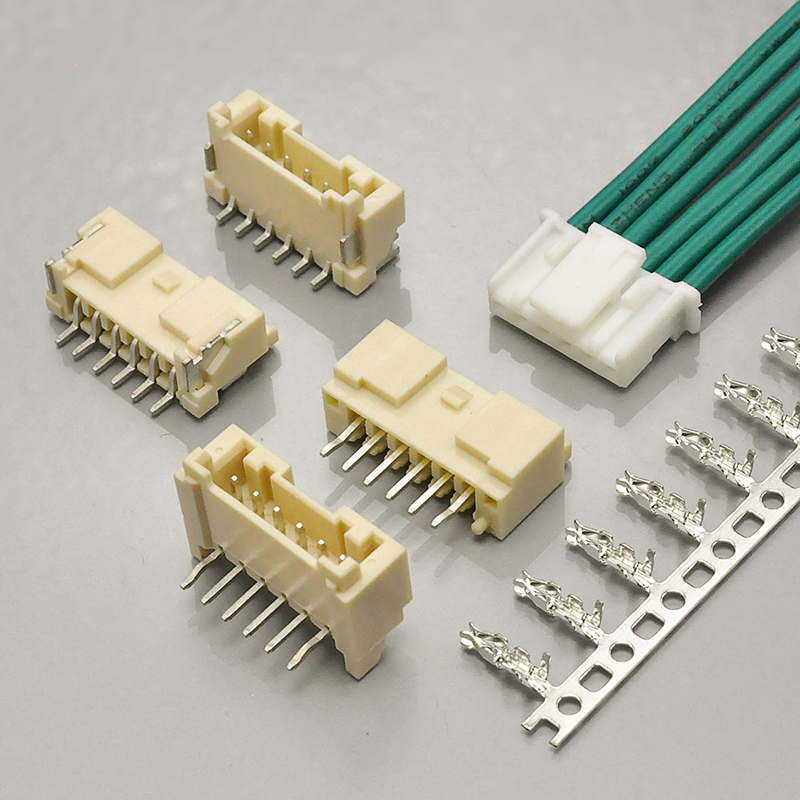
評論