摘要:為了減少環(huán)境污染、打造綠色經濟,高效地利用電力變得越來越重要。電力電子設備是實現這一目標的關鍵技術,已被廣泛用于風力發(fā)電、混合動力汽車、LED 照明等領域。這也對電子器件中的散熱基板提出了更高的要求,傳統(tǒng)的陶瓷基板如 AlN、Al2O3、BeO 等的缺點也日益突出,如較低的理論熱導率和較差的力學性能等,嚴重阻礙了其發(fā)展。相比于傳統(tǒng)陶瓷基板材料,氮化硅陶瓷由于其優(yōu)異的理論熱導率和良好的力學性能而逐漸成為電子器件的主要散熱材料。
然而,目前氮化硅陶瓷實際熱導率還遠遠低于理論熱導率的值,而且一些高熱導率氮化硅陶瓷(>150 W/(m·K))還處于實驗室階段。影響氮化硅陶瓷熱導率的因素有晶格氧、晶相、晶界相等,其中氧原子因為在晶格中會發(fā)生固溶反應生成硅空位和造成晶格畸變,從而引起聲子散射,降低氮化硅陶瓷熱導率而成為主要因素。此外,晶型轉變和晶軸取向也能在一定程度上影響氮化硅的熱導率。如何實現氮化硅陶瓷基板的大規(guī)模生產也是一個不小的難題。
現階段,隨著制備工藝的不斷優(yōu)化,氮化硅陶瓷實際熱導率也在不斷提高。為了降低晶格氧含量,首先在原料的選擇上降低氧含量,一方面可選用含氧量比較少的 Si 粉作為起始原料,但是要避免在球磨的過程中引入氧雜質;另一方面,選用高純度的 α-Si3N4或者 β-Si3N4作為起始原料也能減少氧含量。其次選用適當的燒結助劑也能通過減少氧含量的方式提高熱導率。
目前使用較多的燒結助劑是 Y2O3-MgO,但是仍不可避免地引入了氧雜質,因此可以選用非氧化物燒結助劑來替換氧化物燒結助劑,如 YF3-MgO、MgF2-Y2O3、Y2Si4N6C-MgO、MgSiN2-YbF3等在提高熱導率方面也取得了非常不錯的效果。研究發(fā)現通過加入碳來降低氧含量也能達到很好的效果,通過在原料粉體中摻雜一部分碳,使原料粉體在氮化、燒結時處于還原性較強的環(huán)境中,從而促進了氧的消除。此外,通過加入晶種和提高燒結溫度等方式來促進晶型轉變及通過外加磁場等方法使晶粒定向生長,都能在一定程度上提高熱導率。為了滿足電子器件的尺寸要求,流延成型成為大規(guī)模制備氮化硅陶瓷基板的關鍵技術。
本文從影響熱導率的主要因素入手,重點介紹了降低晶格氧含量、促進晶型轉變及實現晶軸定向生長三種提高實際熱導率的方法;然后,指出了流延成型是大規(guī)模制備高導熱氮化硅陶瓷的關鍵,并分別從流延漿料的流動性、流延片和漿料的潤濕性及穩(wěn)定性等三方面進行了敘述;概述了目前常用的制備高導熱氮化硅陶瓷的燒結工藝現狀;最后,對未來氮化硅高導熱陶瓷的研究方向進行了展望。
00
引言
隨著集成電路工業(yè)的發(fā)展,電力電子器件技術正朝著高電壓、大電流、大功率密度、小尺寸的方向發(fā)展。因此,高效的散熱系統(tǒng)是高集成電路必不可少的一部分。這就使得基板材料既需要良好的機械可靠性,又需要較高的熱導率。圖 1 為電力電子模塊基板及其開裂方式。研究人員對高導熱系數陶瓷進行了大量的研究,其中具有高熱導率的氮化鋁(AlN)陶瓷(本征熱導率約為320 W/(m·K))被廣泛用作電子器件的主要陶瓷基材。
圖 1 電力電子模塊基板及其開裂方式
但是,AlN 陶瓷的力學性能較差,如彎曲強度為 300~400 MPa,斷裂韌性為 3~4 MPa·m1/2,導致氮化鋁基板的使用壽命較短,使得它作為結構基板材料使用受到了限制。另外,Al2O3陶瓷的理論熱導率與實際熱導率都很低,不適合應用于大規(guī)模集成電路。電子工業(yè)迫切希望找到具有良好力學性能的高導熱基片材料,圖 2 是幾種陶瓷基板的強度與熱導率的比較,因此,Si3N4陶瓷成為人們關注的焦點。
圖 2 幾種陶瓷基板的強度與熱導率的比較
與 AlN 和 Al2O3陶瓷基板材料相比,Si3N4具有一系列獨特的優(yōu)勢。Si3N4屬于六方晶系,有 α、β 和 γ 三種晶相。
Lightfoot 和 Haggerty 根據Si3N4結構提出氮化硅的理論熱導率在200~300 W/(m·K)。Hirosaki 等通過分子動力學的方法計算出 α-Si3N4和 β-Si3N4的理論熱導率,發(fā)現Si3N4的熱導率沿 a 軸和 c 軸具有取向性,其中 α-Si3N4單晶體沿 a軸和 c軸的理論熱導率分別為105 W/(m·K)、225W/(m·K);β-Si3N4單晶體沿a軸和c軸方向的理論熱導率分別是 170 W/(m·K)、450 W/(m·K)。
Xiang 等結合密度泛函理論和修正的 Debye-Callaway 模型預測了 γ-Si3N4陶瓷也具有較高的熱導率。同時Si3N4具有高強度、高硬度、高電阻率、良好的抗熱震性、低介電損耗和低膨脹系數等特點,是一種理想的散熱和封裝材料。
近年來國內的一些研究機構和高校相繼有了成果,北京中材人工晶體研究院成功研制出熱導率為 80 W/(m·K)、抗彎強度為 750 MPa、斷裂韌性為 7.5MPa·m1/2的Si3N4陶瓷基片材料,其已與東芝公司的商用氮化硅產品性能相近。
中科院上硅所曾宇平研究員團隊成功研制出平均熱導率為 95 W/(m·K),最高可達 120 W/(m·K)且穩(wěn)定性良好的氮化硅陶瓷。其尺寸為 120 mm×120 mm,厚度為 0.32 mm,而且外形尺寸能根據實際要求調整。
目前我國的商用高導熱Si3N4陶瓷基片與國外還是存在差距。因此,研發(fā)高導熱的Si3N4陶瓷基片必將促進我國 IGBT(Insula-ted gate bipolar transistor)技術的大跨步發(fā)展,為步入新能源等高端領域實現點的突破。
近年來氮化硅陶瓷基板材料的實際熱導率不斷提高,但與理論熱導率仍有較大差距。目前,文獻報道了提高氮化硅陶瓷熱導率的方法,如降低晶格氧含量、促進晶型轉變、實現晶粒定向生長等。本文闡述了如何提高氮化硅陶瓷的熱導率和實現大規(guī)模生產的成型技術,重點概述了國內外高導熱氮化硅陶瓷的研究進展。
01
晶格氧的影響
氮化硅的主要傳熱機制是晶格振動,通過聲子來傳導熱量。晶格振動并非是線性的,晶格間有著一定的耦合作用,聲子間會發(fā)生碰撞,使聲子的平均自由程減小。另外,Si3N4晶體中的各種缺陷、雜質以及晶粒界面都會引起聲子的散射,也等效于聲子平均自由程減小,從而降低熱導率。圖 3 為氮化硅的微觀結構。
圖 3 氮化硅燒結體的典型微觀結構
研究表明,在諸多晶格缺陷中,晶格氧是影響氮化硅陶瓷熱導率的主要缺陷之一。氧原子在燒結的過程中會發(fā)生如下的固溶反應:
2SiO2→ 2SiSi+4ON+VSi (1)
反應中生成了硅空位,并且原子取代會使晶體產生一定的畸變,這些都會引起聲子的散射,從而降低Si3N4晶體的熱導率。
Kitayama 等在晶格氧和晶界相兩個方面對影響Si3N4晶體熱導率的因素進行了系統(tǒng)的研究,發(fā)現Si3N4晶粒的尺寸會改變上述因素的影響程度,當晶粒尺寸小于 1μm時,晶格氧和晶界相的厚度都會成為影響熱導率的主要因素;當晶粒尺寸大于 1μm 時,晶格氧是影響熱導率的主要因素。而制備具有高熱導率的氮化硅陶瓷,需要其具有大尺寸的晶粒,因此通過降低晶格氧含量來制得高熱導率的氮化硅顯得尤為關鍵。下面從原料的選擇、燒結助劑的選擇和制備過程中碳的還原等方面闡述降低晶格氧含量的有效方法。
1.1 原料粉體選擇
為了降低氮化硅晶格中的氧含量,要先得從原料粉體上降低雜質氧的含量。目前有兩種方法:一種是使用低含氧量的 Si 粉為原料,經過 Si 粉的氮化和重燒結兩步工藝獲得高致密、高導熱的Si3N4陶瓷。將由 Si 粉和燒結助劑組成的 Si的致密體在氮氣氣氛中加熱到 Si熔點(1414℃)附近的溫度,使 Si 氮化后轉變?yōu)槎嗫椎腟i3N4燒結體,再將氮化硅燒結體進一步加熱到較高溫度,使多孔的Si3N4燒結成致密的Si3N4陶瓷。另外一種是使用氧含量更低的高純 α-Si3N4粉進行燒結,或者直接用 β-Si3N4進行燒結。
Park 等研究了原料Si 粉的顆粒尺寸對氮化硅陶瓷熱導率的影響,發(fā)現 Si 顆粒尺寸的減小能使氮化硅孔道變窄,有利于燒結過程中氣孔的消除,進而得到致密度高的氮化硅陶瓷。研究表明,當 Si 粉減小到 1μm 后,氮化硅陶瓷的相對密度能達到 98%以上。但是在 SRBSN 這一工藝減小原料顆粒尺寸的過程中容易使原料表面發(fā)生氧化,增加了原料中晶格氧的含量。
Guo等分別用 Si 粉和 α-Si3N4為原料進行了對比試驗。研究發(fā)現,以 Si 粉為原料經過氮化后能得到含氧量較低(0.36%,質量分數)的Si3N4粉末,通過無壓燒結制得熱導率為 66.5W/(m·K)的氮化硅陶瓷。而在同樣的條件下,以 α-Si3N4為原料制備的氮化硅陶瓷,其熱導率只有 56.8 W/(m·K)。
用高純度的 α-Si3N4粉末為原料,也能制得高熱導率的氮化硅陶瓷。Duan 等以 α-Si3N4為原料,制備了密度、導熱系數、抗彎強度、斷裂韌性和維氏硬度分別為 3.20 g·cm-3、60 W/(m·K)、668 MPa、5.13 MPa·m1/2和 15.06 GPa的Si3N4陶瓷。Kim 等以 α-Si3N4為原料制備了熱導率為78.8 W/(m·K)的氮化硅陶瓷。
劉幸麗等以不同配比的 β-Si3N4/α-Si3N4粉末為起始原料,制備了熱導率為108 W/(m·K)、抗彎強度為 626 MPa的氮化硅陶瓷。結果表明:隨著 β-Si3N4粉末含量的增加,β-Si3N4柱狀晶粒平均長徑比的減小使得晶粒堆積密度減小,柱狀晶體積分數相應增加,晶間相含量減少,熱導率提高。
彭萌萌等研究了粉體種類(β-Si3N4或 α-Si3N4)及 SPS 保溫時間對氮化硅陶瓷熱導率的影響。研究發(fā)現,采用 β-Si3N4粉體制備的氮化硅陶瓷的熱導率比采用相同工藝以 α-Si3N4為粉體制備的氮化硅陶瓷高 15% 以上,達到了 105W/(m·K)。不同原料制備的Si3N4材料的熱導率比較見表1。
表 1 不同原料制備的Si3N4材料的熱導率比較
綜合以上研究可發(fā)現,采用 Si 粉為原料制得的樣品能達到很高的熱導率,但是在研磨的過程中容易發(fā)生氧化,而且實驗過程繁瑣,耗時較長,不利于工業(yè)化生產;使用高純度、低含氧量的 α-Si3N4粉末為原料時,由于原料本身純度高,能制備出性能優(yōu)異的氮化硅陶瓷,但是這樣會導致成本增加,不利于大規(guī)模生產;雖然可以用 β-Si3N4取代 α-Si3N4為原料,得到高熱導率的氮化硅陶瓷,但是 β-Si3N4的棒狀晶粒會阻礙晶粒重排,導致燒結物難以致密。
1.2 燒結助劑選擇
Si3N4屬于共價化合物,有著很小的自擴散系數,在燒結過程中依靠自身擴散很難形成致密化的晶體結構,因此添加合適的燒結助劑和優(yōu)化燒結助劑配比能得到高熱導率的氮化硅陶瓷。在高溫時燒結助劑與Si3N4表面的 SiO2反應形成液相,最后形成晶界相。然而晶界相的熱導率只有 0.7~1 W/(m·K),這些晶界相極大地降低了氮化硅的熱導率,而且一些氧化物燒結添加劑的引入會導致Si3N4晶格氧含量增加,也會導致熱導率降低。
目前氮化硅陶瓷的燒結助劑種類繁多,包括各種稀土氧化物、鎂化物、氟化物和它們所組成的復合燒結助劑。稀土元素由于具有很高的氧親和力而常被用于從Si3N4晶格中吸附氧。目前比較常用的是鎂的氧化物和稀土元素的氧化物組成的混合燒結助劑。
Jia 等在氮化硅陶瓷的燒結過程中添加復合燒結助劑 Y2O3-MgO,制備了熱導率達到 64.4W/(m·K)的氮化硅陶瓷。Go 等同樣采用 Y2O3-MgO為燒結助劑,研究了燒結助劑 MgO 的粒度對氮化硅微觀結構和熱導率的影響。研究發(fā)現,加入較粗的 MgO 顆粒會導致燒結過程中液相成分分布不均勻,使富 MgO 區(qū)周圍的Si3N4晶粒優(yōu)先長大,從而導致最終的Si3N4陶瓷中大顆粒的Si3N4晶粒的比例增大,熱導率提高。
然而,加入氧化物燒結助劑會不可避免地引入氧原子,因此為了降低晶格中的氧雜質,可以采用氧化物 + 非氧化物作為燒結助劑。Yang 等以 MgF2-Y2O3為燒結添加劑制備出性能良好的高導熱氮化硅陶瓷,發(fā)現用 MgF2可以降低燒結過程中液相的粘度,加速顆粒重排,使粉料混合物能夠在較低溫度(1600℃)和較短時間(3 min)內實現致密化,而且低的液相粘度與高的 Si、N 原子比例有助于Si3N4的 α→β 相變和晶粒生長,從而提高Si3N4陶瓷的熱導率。
Hu 等分別以 MgF2-Y2O3和 MgO-Y2O3為燒結助劑進行了對比試驗,并探究了燒結助劑的配比對熱導率的影響。相比于 MgO-Y2O3,用 MgF2-Y2O3作為燒結助劑時Si3N4陶瓷熱導率提高了 19%,當添加量為 4%MgF2-5%Y2O3時,能達到最高的熱導率。
Li 等以 Y2Si4N6C-MgO 代替 Y2O3-MgO 作為燒結添加劑,通過引入氮和促進二氧化硅的消除,在第二相中形成了較高的氮氧比,導致在致密化的Si3N4試樣中顆粒增大,晶格氧含量降低,Si3N4-Si3N4的連續(xù)性增加,使Si3N4陶瓷的熱導率由 92 W/(m·K)提高到 120 W/(m·K),提高了 30.4%。
為了進一步提高液相中的氮氧比,降低晶格氧含量,通常還采用非氧化物作為燒結助劑。Lee 等研究了氧化物和非氧化物燒結添加劑對Si3N4的微觀結構、導熱系數和力學性能的影響。以 MgSiN2-YbF3為燒結添加劑,制備出導熱系數為 101.5 W/(m·K)、彎曲強度為822~916 MPa 的Si3N4陶瓷材料。經研究發(fā)現,相比于氧化物燒結添加劑,非氧化物 MgSiN2和氟化物作為燒結添加劑能降低氮化硅的二次相和晶格氧含量,其中稀土氟化物能與 SiO2反應生成 SiF4,而SiF4的蒸發(fā)導致晶界相減少,同時也會導致晶界相 SiO2還原,降低晶格氧含量,進而達到提高熱導率的目的。不同燒結助劑制備的氮化硅陶瓷熱導率比較見表 2,顯微結構如圖 4所示。
表 2 不同燒結助劑制備的Si3N4材料的熱導率比較
圖 4 氧化物添加劑(a)MgO-Y2O3和(d)MgO-Yb2O3、混合添加劑(b)MgSiN2-Y2O3和(e)MgSiN3-Yb2O3、非氧化物添加劑(c)MgSiN2-YF3和(f)Mg-SiN2-YbF3的微觀結構
目前主流的燒結助劑中稀土元素為 Y 和 Yb 的化合物,但是有些稀土元素并不能起到提高致密度的作用。Guo等分別用 ZrO2-MgO-Y2O3和 Eu2O3-MgO-Y2O3作為燒結助劑,制得了氮化硅陶瓷,經研究發(fā)現 Eu2O3-MgO-Y2O3的加入反而抑制了氮化硅陶瓷的致密化。
綜合以上研究發(fā)現,相比于氧化物燒結助劑,非氧化物燒結助劑能額外提供氮原子,提高氮氧比,促進晶型轉變,還能還原 SiO2起到降低晶格氧含量、減少晶界相的作用。
1.3 碳的還原
前面提到的一些能高效降低晶格氧含量的燒結助劑,如Y2Si4N6C和 MgSiN2等,無法從商業(yè)的渠道獲得,這就給大規(guī)模生產造成了困擾,而且高溫熱處理也會導致高成本。因此,從工業(yè)應用的角度來看,開發(fā)簡便、廉價的高導熱Si3N4陶瓷的制備方法具有重要的意義。研究發(fā)現,在燒結過程中摻雜一定量的碳能起到還原氧雜質的作用,是一種降低晶格氧含量的有效方法。
碳被廣泛用作非氧化物陶瓷的燒結添加劑,其主要作用是去除非氧化物粉末表面的氧化物雜質。在此基礎上,研究者發(fā)現少量碳的加入可以有效地降低 AlN 陶瓷的晶格氧含量,從而提高 AlN 陶瓷的熱導率。同樣地,在Si3N4陶瓷中引入碳也可以降低氧含量,主要是由于在氮化和后燒結過程中,適量的碳會起到非常明顯的還原作用,能極大降低 SiO 的分壓,增加晶間二次相的 N/O 原子比,從而形成雙峰狀顯微結構,得到晶粒尺寸大、細長的氮化硅顆粒,提高氮化硅陶瓷的熱導率。
Li 等用 BN/石墨代替 BN 作為粉料底板后,氮化硅陶瓷的熱導率提升了 40.7%。研究發(fā)現,即使 Si 粉經球磨后含氧量達到了 4.22%,氮化硅陶瓷的熱導率依然能到達 121 W/(m·K)。其原因主要是石墨具有較強的還原能力,在氮化的過程中通過促進 SiO2的去除,改變二次相的化學成分,在燒結過程中進一步促進 SiO2和 Y2Si3O3N4二次相的消除,從而使產物生成較大的棒狀晶粒,降低晶格氧含量,提高Si3N4-Si3N4的連續(xù)性。研究表明,雖然摻雜了一部分碳,但是氮化硅的電阻率依然不變,然而最終的產物有很高的質量損失比(25.8%),增加了原料損失的成本。
Li 等發(fā)現過量的石墨會與表面的Si3N4發(fā)生反應,這是導致氮化硅陶瓷具有較高質量損失比的關鍵因素。于是他們改進了制備工藝,采用兩步氣壓燒結法,用 5%(摩爾分數) 碳摻雜 93%α-Si3N4-2%Yb2O3-5%MgO 的粉末混合物作為原料進行燒結實驗。結果表明,碳的加入使 Si3N4 陶瓷的熱導率從 102 W/(m·K)提高到 128 W/(m·K),提高了 25.5%。在第一步燒結過程中,碳熱還原過程顯著降低了氧含量,增加了晶間二次相的N/O比,在半成品Si3N4樣品中,有Y2Si4O7N2第二相出現,β-Si3N4含量較高,棒狀 β-Si3N4晶粒較大。在第二步燒結過程中,第二相Y2Si4O7N2與碳反應生成了 YbSi3N5,極大降低了晶格氧含量,得到了較粗的棒狀晶粒和更緊密的Si3N4-Si3N4界面,使得Si3N4陶瓷的熱導率有了顯著的提升,所制備的Si3N4的 SEM 圖如圖 5 所示。
圖 5 最后的Si3N4陶瓷樣品拋光表面和等離子刻蝕表面的 SEM 顯微照片:(a)SN 和(b)SNC 的低倍圖像;(c)SN 和(d)SNC 的高倍圖像
在制備高導熱氮化硅陶瓷中加入碳是降低晶格氧含量的有效方法,該方法對原料含氧量和燒結助劑的要求不高,降低了高導熱氮化硅陶瓷的制備成本,隨著技術的不斷改進,有望在工業(yè)化生產中得到應用。
02
晶型轉變、晶軸取向的影響
2.1 晶型轉變對熱導率的影響及改進方法
β-Si3N4因為結構上更加對稱,其熱導率要高于 α-Si3N4。在高溫燒結氮化硅陶瓷的過程中,原料低溫相 α-Si3N4會經過溶解-沉淀機制轉變?yōu)楦邷叵?β-Si3N4,但是在燒結過程中晶型轉變并不完全,未轉變的 α-Si3N4會極大地影響氮化硅陶瓷的熱導率。為了促進晶型轉變,得到更高的 β/(α + β)相比,目前比較常用的方法是:(1)在燒結制度上進行改變,如提高燒結溫度和延長燒結時間及后續(xù)的熱處理等;(2)在α-Si3N4中加入適量的 β-Si3N4棒狀晶粒作為晶種。圖6為加入晶種后氮化硅陶瓷的雙模式組織分布。
圖 6 加入晶種后 β-Si3N4陶瓷的雙模式組織分布
Zhou 等探究了不同的燒結時間對氮化硅陶瓷熱導率、彎曲強度、斷裂韌性的影響。由表 3 可見,隨著燒結時間的延長,氮化硅陶瓷的熱導率逐漸升高。這主要是由于隨著溶解沉淀過程的進行,晶粒不斷長大,β-Si3N4含量不斷增加,晶格氧含量降低。童文欣等研究了燒結溫度對Si3N4熱導率的影響,發(fā)現經 1600℃燒結后的樣品既含有 α 相又含有 β 相。在燒結溫度升至 1700℃及 1800℃后,試樣中只存在 β 相。隨著燒結溫度的升高,樣品熱導率呈現增加的趨勢,可能是晶粒尺寸增大、液相含量降低以及液相在多晶界邊緣處形成獨立的“玻璃囊”現象所致。
表 3 不同燒結時間下Si3N4的性能比較
Zhu 等發(fā)現在燒結過程中加入 β-Si3N4作為晶種,能得到致密化程度和熱導率更高的氮化硅陶瓷。為了進一步促進晶型轉變,得到大尺寸的氮化硅晶粒,可以采用 β-Si3N4代替α-Si3N4為起始粉末制備高導熱氮化硅陶瓷。梁振華等在原料中加入了 1%(質量分數)的棒狀 β-Si3N4顆粒作為晶種,氮化硅陶瓷的熱導率達到了 158 W/(m·K)。劉幸麗等探究了不同配比的 β-Si3N4/α-Si3N4對氮化硅陶瓷熱導率和力學性能的影響,結果表明,當原料中全是 β-Si3N4時氮化硅陶瓷有最高的熱導率,達到了108 W/(m·K),但是抗彎強度也降低。
綜合以上研究發(fā)現,適當提高燒結溫度和延長燒結時間都能在一定程度上促進晶型轉變;加入適量的 β-Si3N4晶種用來促進晶型轉變可以在較短的時間內提高 β/(α+β)相比,使晶粒生長更加充分,得到高熱導率的氮化硅陶瓷。
2.2 晶軸取向對熱導率的影響及改進方法
由于 c 軸的生長速率大于 a 軸,各向異性生長導致了 β-Si3N4呈棒狀,也導致了其物理性質的各向異性。前面敘述了氮化硅晶粒熱導率具有各向異性的特征,β-Si3N4單晶體沿a 軸和c 軸的理論熱導率分別為170 W/(m·K)、450 W/(m·K),因此在成型工藝中采取合適的方法可以實現氮化硅晶粒的定向排列,促進晶粒定向生長。目前能使晶粒定向生長的成型方法有流延成型、熱壓成型、注漿成型等。
在外加強磁場的作用下,氮化硅晶體沿各晶軸具有比較明顯的生長差異。這主要是由于氮化硅晶體沿各晶軸方向的磁化率差異,在外加強磁場的作用下,氮化硅晶體會受到力矩的作用,通過旋轉一定的角度以便具有最小的磁化能,氮化硅晶粒旋轉驅動能量表達式如下:
Δχ= χc-χa,b (2)
? (3)
式中:V 是粒子的體積,B 是外加磁場,μ0是真空中的磁導率,χc和 χa,b 分別表示氮化硅晶體沿 c 軸和 a,b 軸的磁化率,|Δχ |是晶體沿各晶軸方向的磁化率差值的絕對值。而粒子的熱運動能量 U 的表達式為:
U=3nN0kB(4)
式中:n 是物質粒子的摩爾數,N0是阿伏伽德羅常數,kB是玻爾茲曼常數,T 是溫度。當 ΔE 大于 U 時,粒子可以被磁場旋轉。由圖 7 可知,若 c 軸具有較高的磁化率,棒狀粒子將與磁場平行排列;若 c 軸的磁化率較低,棒狀粒子將垂直于磁場排列。
圖 7 磁場對晶格中六邊形棒狀粒子排列的影響示意圖:(a)χc > χa,b ;(b) χc<χa,b
在弱磁性陶瓷成型過程中引入強磁場,可以制備出具有取向微結構的樣品。由于氮化硅晶粒沿各軸的磁化率 χc<χa,b可以在旋轉的水平磁場中通過注漿成型等技術制備具有 c 軸取向的氮化硅陶瓷,制備原理如圖 8 所示。
圖 8 磁場中制備具有晶軸取向的陶瓷
楊治剛等用凝膠注模成型取代了傳統(tǒng)的注漿成型,在6T 縱向磁場中制備出具有沿 a 軸或 b 軸取向的織構化氮化硅陶瓷,并研究了燒結溫度和保溫時間對氮化硅陶瓷織構化的影響規(guī)律。結果表明,升高燒結溫度促進了氮化硅陶瓷織構化,而延長燒結時間對織構化幾乎沒有影響。Liang 等在使用熱壓燒結制備氮化硅陶瓷時,發(fā)現氮化硅晶粒{0001}有沿 z 軸生長的跡象,有較強的取向性。這有利于制備高導熱的氮化硅陶瓷。Zhu 等在 12T 的水平磁場中進行注漿成型,得到熱導率為 170 W/(m·K)的高導熱氮化硅陶瓷。研究發(fā)現,在注漿成型的過程中模具以 5 r/min 的轉速旋轉形成一個旋轉磁場,從而導致 β-Si3N4在凝結過程中具有與磁場垂直的 c 軸取向,c 軸取向系數為0.98。圖9 為磁場和模具旋轉對棒狀氮化硅晶粒取向的影響。
圖 9 磁場和模具旋轉對棒狀氮化硅晶粒取向的影響
現階段,在大規(guī)模生產中很難實現氮化硅晶粒的取向生長,目前文獻報道的定向生長的氮化硅陶瓷僅限于實驗室階段,需要通過合適的方法,在工業(yè)化生產中實現氮化硅晶粒的取向生長,這對制備高導熱氮化硅陶瓷是極具應用前景的。
03
陶瓷基片制備工藝
3.1 成型工藝
由于電力電子器件的小型化,對氮化硅陶瓷基板材料的尺寸和厚度有了更加精細的要求,商業(yè)用途的氮化硅陶瓷基板的厚度范圍是 0.3~0.6 mm。為了實現大規(guī)模生產氮化硅陶瓷基板材料,選擇一種合適的成型方法顯得尤為重要。目前制備氮化硅陶瓷的成型方法很多,如流延成型、熱壓成型、注漿成型、冷等靜壓成型等。但是為了同時滿足小型化、精細化的尺寸要求和實現氮化硅晶粒的定向生長,流延成型無疑是實現這一目標的關鍵。圖 10 是流延成型工藝的流程圖,下面對流延成型制備氮化硅陶瓷基板材料進行敘述。
圖 10 流延成型工藝流程圖
流延成型的漿料是決定素坯性能最關鍵的因素,漿料包括粉體、溶劑、分散劑、粘結劑、增塑劑和其他添加劑,每一種成分對漿料的性能都有重要影響,并且漿料中的各個組分也會互相產生影響。雖然流延成型相比于其他成型工藝有著獨特的優(yōu)勢,但是在實際操作中由于應力的釋放機制不同,容易使流延片干燥時出現彎曲、開裂、起皺、厚薄不均勻等現象。為了制備出均勻穩(wěn)定的流延漿料和干燥后光滑平整的流延片,在保持配方不變的情況下,需要注意漿料的潤濕性、穩(wěn)定性和坯片的厚度等因素。
通過流延成型制備氮化硅流延片時,Otsuka 等和Chou 等分別提出了理論液體的流動模型,流延成型過程中流延片厚度 D 與各流延參數的關系如式(5)所示:
(5)
式中:α 表示濕坯干燥時厚度的收縮系數,漿料的粘度和均勻性對其影響較大;h 和 L 分別表示刮刀刀刃間隙的高度和長度;η 表示漿料的粘度;ΔF 表示料斗內壓力,一般由漿料高度決定;v0表示流延裝置和支撐載體的相對速度。為了制備超薄的陶瓷基片,需要在保持漿料的粘度適中和均勻性良好的情況下,適當地調整刮刀間隙和保持漿料的液面高度不變。
在有機流延成型中,一般使用共沸混合物作為溶劑,溶解效果更佳,這樣就需要保證溶劑對粉體顆粒有很好的潤濕性,這與溶劑的表面張力有關,可以用式(6)解釋:
(6)
式中:θ 為潤濕角;γsv、γsl、γlv分別表示固-氣、固-液、液-氣的表面張力。由式(6)可知,γlv越小,則 θ 越小,表明潤濕性越好。潤濕作用如圖 11 所示。
圖 11 潤濕作用示意圖
為了保證流延漿料均勻穩(wěn)定,需要加入分散劑,其主要作用是使粉體顆粒表面易于潤濕,降低粉體顆粒表面勢能使之更易分散,并且使顆粒之間的勢壘升高,從而使?jié){料穩(wěn)定均勻。漿料的穩(wěn)定性可以通過 DLVO 理論來描述:
UT=UA+UR (7)
式中:UA為范德華引力勢能;UR為斥力勢能。當UR大于UA時,漿料穩(wěn)定。為了保證漿料的均勻穩(wěn)定,分散劑的用量也要把控。若用量過多,則產生的粒子很容易粘結,不利于獲得珠狀顆粒;若用量過少,容易被分散成小液滴,單體不穩(wěn)定,隨著反應的進行,分散的液滴也可能凝結成塊。
Duan 等先采用流延成型工藝制備了微觀結構均勻、相對密度達 56.08%的流延片,然后經過氣壓燒結得到了相對密度達 99%、熱導率為 58 W/(m·K)的氮化硅陶瓷。Zhang等采用流延成型工藝和氣壓燒結工藝制備了熱導率為 81W/(m·K)的致密氮化硅陶瓷。研究發(fā)現分散劑(PE)、粘結劑(PVB)、增塑劑/粘結劑的配比和固載量分別為 1.8%(質量分數)、8%(質量分數)、1.2、33%(體積分數)時能得到最高的熱導率。張景賢等先通過流延成型制備 Si 的流延片,然后通過脫脂、氮化、燒結制備出熱導率為 76 W/(m·K)的氮化硅陶瓷。
目前關于流延成型制備的氮化硅陶瓷熱導率還不高,遠低于文獻報道的水平(>150 W/(m·K)),通過改善工藝、優(yōu)化各組分的配比,制備出均勻穩(wěn)定、粘度適中、潤濕性良好的漿料,是大規(guī)模制備高導熱氮化硅陶瓷的關鍵。
3.2 燒結工藝
目前,制備氮化硅陶瓷的主要燒結方法有氣壓燒結、反應燒結重燒結、放電等離子燒結、熱壓燒結等,每種方法各有優(yōu)劣,下面對一些常用的燒結方法進行簡要概述。
氣壓燒結(GPS)能在氮氣的氛圍中通過加壓、加熱使氮化硅迅速致密,促進 α→β 晶型的快速轉變,有助于提高氮化硅陶瓷的熱導率。Li 等以 α-Si3N4為原料,通過兩步氣壓燒結法,制備了高導熱的氮化硅陶瓷。先將混合粉末在1 MPa的氮氣壓力下加熱到 1500℃ 燒結 8h,然后在 1900℃下燒結 12h,通過兩步氣壓燒結的反應,極大促進了 α→β-Si3N4的晶型轉變,氮化硅陶瓷的熱導率達到了128 W/(m·K)。Kim 等采用氣壓燒結的方法在 0.9 MPa 的氮氣氛圍中加熱到 1900 ℃,保溫 6h,最后得到的氮化硅陶瓷的熱導率為 78.8 W/(m·K)。Li 等用 Y2Si4N6C-MgO 為燒結助劑,采用氣壓燒結方法制備了熱導率為 120 W/(m·K)的氮化硅陶瓷。
放電等離子燒結(SPS)工藝是一種實現壓力場、溫度場、電場共同作用的試樣燒結方式,具有升溫速率快、燒結溫度低、燒結時間短等優(yōu)點。Yang 等以 MgF2-Y2O3為燒結添加劑,采用 SPS 工藝制備了熱導率為 76 W/(m·K)、抗彎強度為 857.6 MPa、硬度為 14.9 GPa、斷裂韌性為 7.7 MPa·m 1/2的Si3N4陶瓷。實驗表明,由于外加電場的作用,顆粒之間容易滑動,有利于顆粒間的重排,從而得到大晶粒顆粒,使Si3N4在較低溫度下達到較高的致密化。
Hu 等通過 SPS工藝,以 MgF2-Y2O3和 MgO-Y2O3為燒結添加劑,制備了熱導率為 82.5 W/(m·K)、彎曲強度為(911±47) MPa、斷裂韌性為(8.47±0.31) MPa·m1/2的Si3N4陶瓷材料。SPS 工藝還可以解決上文提到的以 β-Si3N4為原料制備氮化硅陶瓷難燒結致密的問題。彭萌萌等采用 SPS 工藝在 1600℃ 下燒結5 min,然后在 1900℃ 下保溫 3h,獲得了致密的氮化硅陶瓷,其熱導率高達 105 W/(m·K)。Liu 等以不同配比的β-Si3N4/α-Si3N4粉末為起始原料,采用 SPS 和熱處理工藝成功制得致密度高達 99%的高導熱氮化硅陶瓷。
燒結反應重燒結(SRBSN)由于是以 Si 粉為原料經過氮化得到多孔的Si3N4燒結體,進而再燒結形成致密的氮化硅陶瓷,比一般以商用 α-Si3N4為原料制備的氮化硅陶瓷具有更低的氧含量而受到研究者的青睞。Zhou 等采用 SRBSN工藝制備了熱導率高達 177 W/(m·K)的Si3N4陶瓷。結果表明,通過延長燒結時間,進一步降低晶格氧含量,可以獲得更高的導熱系數。此外,他們還研究了高導熱性Si3N4陶瓷的斷裂行為,發(fā)現其具有較高的斷裂韌性(11.2 MPa·m1/2)。Zhou 等采用 SRBSN 工藝,以Y2O3和 MgO 為添加劑制備了Si3N4陶瓷。研究發(fā)現Y2O3-MgO 添加劑的含量和燒結時間都會影響Si3N4的熱導率。當添加劑的含量為 2%Y2O3-4%MgO 時,在燒結 24 h 后,得到熱導率為 156 W/(m·K)的Si3N4陶瓷,相比于燒結時間 6h 得到的Si3N4陶瓷(128 W/(m·K)),熱導率提升了21%。Li 等采用 SRBSN 工藝,以Y2O3-MgO 為燒結助劑制備了熱導率高達 121 W/(m·K)的Si3N4陶瓷。
采用其他燒結方式也能制備出高導熱的氮化硅陶瓷。Jia 等采用超高壓燒結制備出熱導率為 64.6 W/(m·K)的氮化硅陶瓷。Duan 等以 10%的 TiO2-MgO 為燒結添加劑,在1780℃下低溫無壓燒結,制備了熱導率為60 W/(m·K)的氮化硅陶瓷。Lee 等采用熱壓燒結工藝制備出熱導率為 101.5 W/(m·K)的氮化硅陶瓷。
綜合上述研究可發(fā)現,雖然燒結方式不一樣,但都可以制備出性能優(yōu)異的氮化硅陶瓷。在實現氮化硅陶瓷大規(guī)模生產時,需要考慮成本、操作難易程度和生產周期等因素,因此找到一種快速、簡便、低成本的燒結工藝是關鍵。
04
結語
Si3N4陶瓷由于其潛在的高導熱性能和優(yōu)異的力學性能,在大功率半導體器件領域越來越受歡迎,有望成為電子器件首選的陶瓷基板材料。但是有諸多限制其熱導率的因素,如晶格缺陷、雜質元素、晶格氧含量、晶粒尺寸等,導致氮化硅陶瓷的實際熱導率并不高。
目前,就如何提高氮化硅的實際熱導率從而實現大規(guī)模生產還存在一些待解決的問題:
(1)原料粉體的顆粒尺寸對制備性能優(yōu)異的氮化硅陶瓷有著重要影響,但是在減小粉末粒度的同時也會使顆粒表面發(fā)生氧化,引入額外的氧雜質,因此需要在減小粒度的同時避免氧雜質的滲入。
(2)目前,燒結助劑的非氧化、多功能化成為研究的熱點,選用合適的燒結助劑不僅能促進燒結,減少晶界相,還能降低晶格氧含量,促進晶型轉變。因此,高效的、多功能的燒結助劑也是重要的研究方向。
(3)為了降低晶格氧含量,在制備過程中加入具有還原性的碳能起到不錯的效果。故在氮化或燒結中制造還原性的氣氛或添加具有還原性的物質是將來研究的熱點。
(4)實現氮化硅基板的大規(guī)模生產,流延成型是一個不錯的選擇。可是由于有機物的影響,氮化硅基體的致密度不高,而且流延成型的氮化硅晶粒定向生長不明顯,如何實現流延片中的氮化硅顆粒定向生長和提升其致密度必將成為研究熱點。
審核編輯 :李倩
-
線路板
+關注
關注
23文章
1195瀏覽量
47033 -
FPC
+關注
關注
70文章
950瀏覽量
63256 -
熱導率
+關注
關注
0文章
40瀏覽量
9257
發(fā)布評論請先 登錄
相關推薦
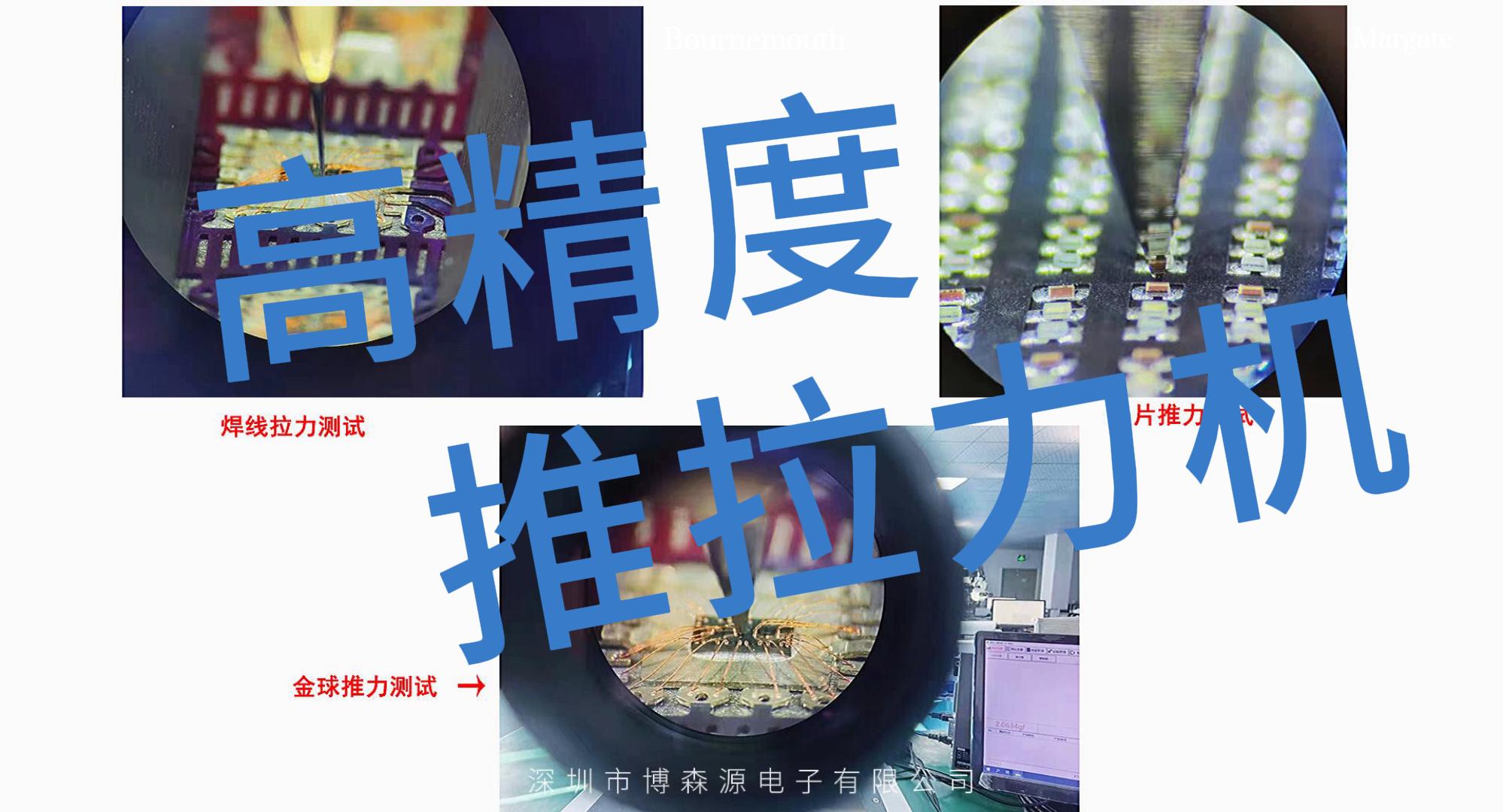
hdi線路板生產工藝流程
HDI線路板和高多層板的區(qū)別
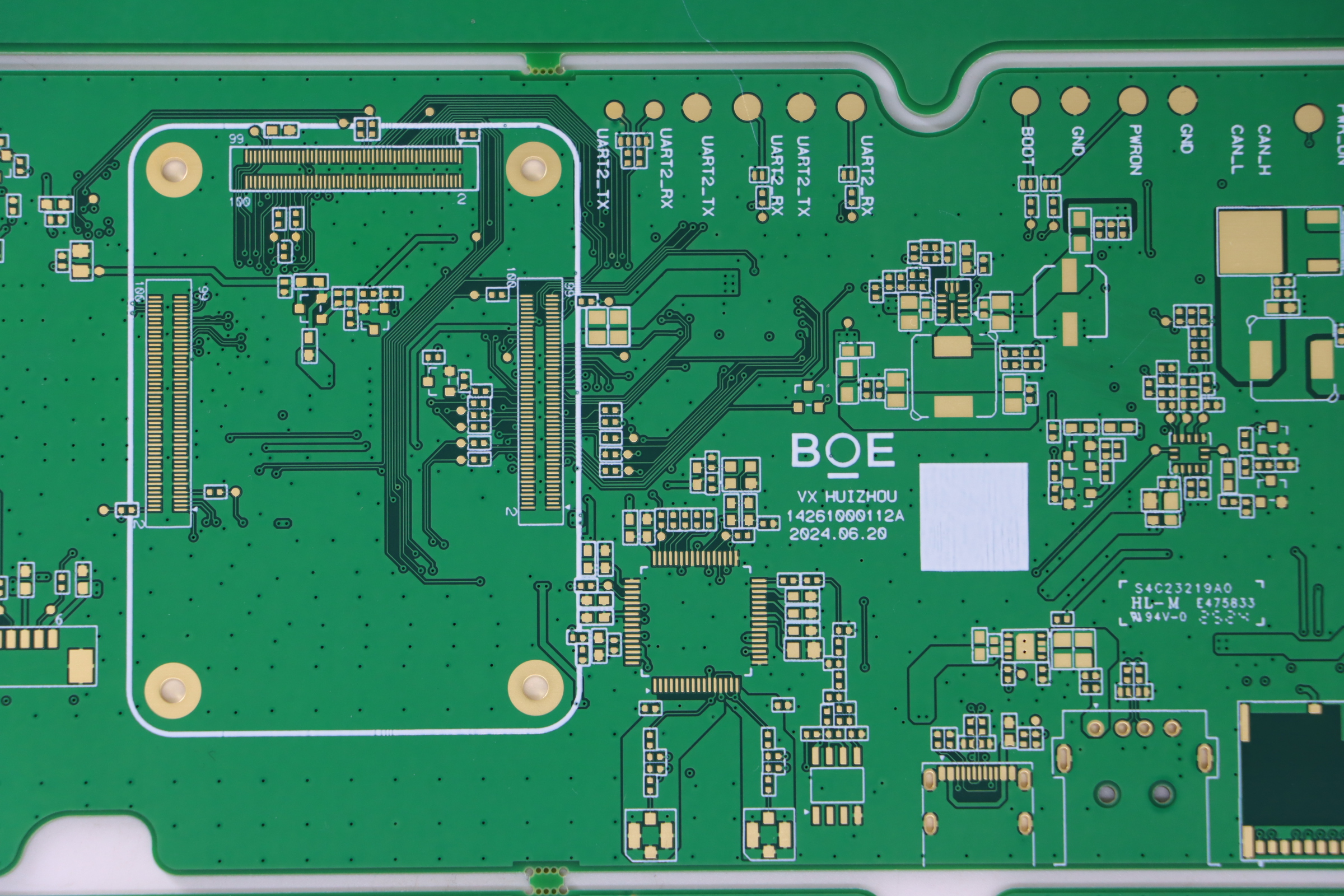
激光焊錫技術在R-FPC線路板制造領域的應用
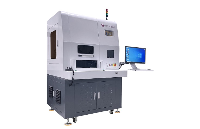
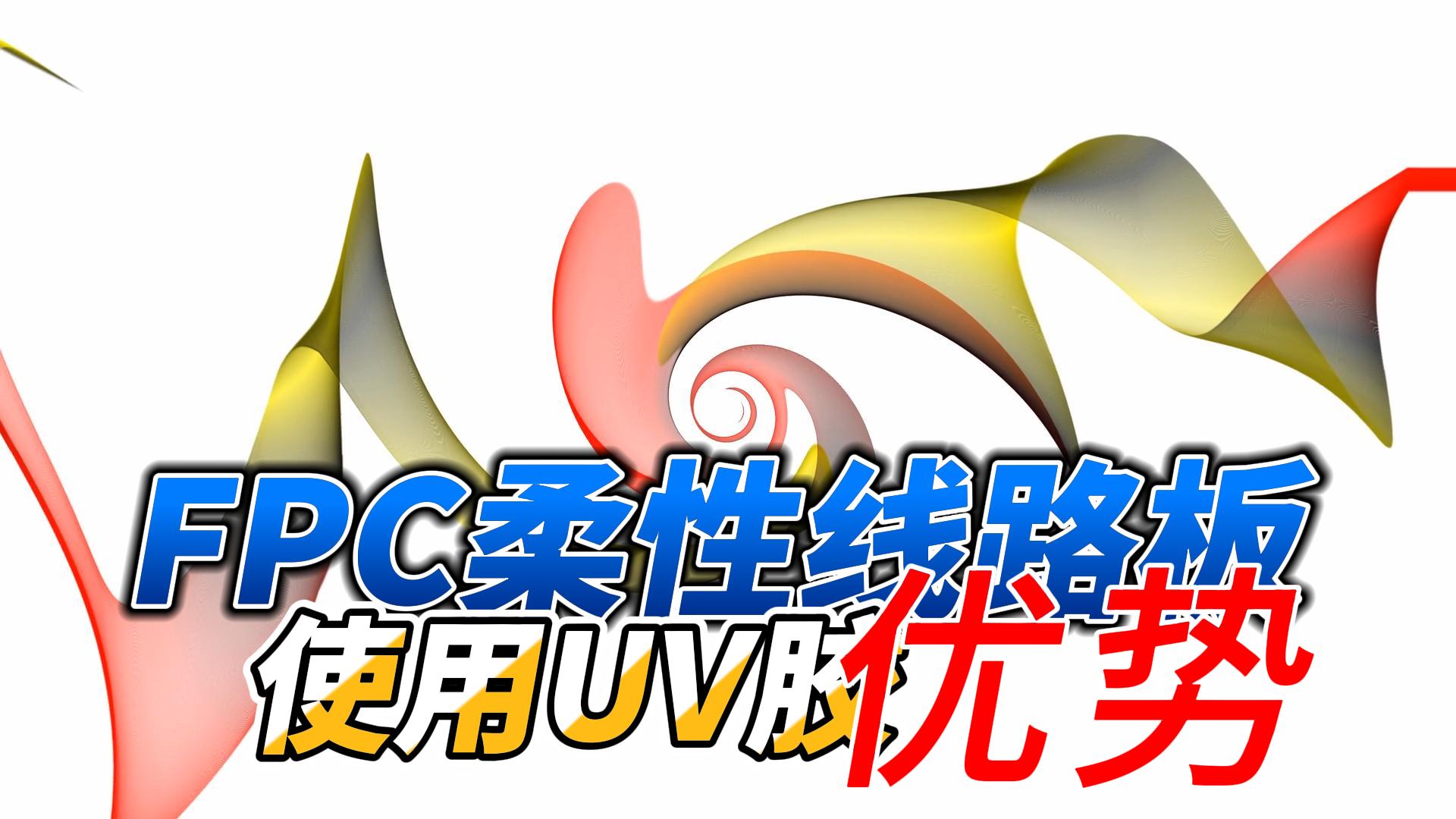
評論