工業制造正在部署最新的傳感器技術,采用新的控制架構,并開始在稱為工業4.0的過渡中發現“大數據”和分析的潛力。制造業正在增加用于跟蹤環境和過程變量的傳感器數量。這反過來又加速了向分布式控制架構的過渡,在分布式控制架構中,工廠操作員通過將可編程邏輯控制器 (PLC) 移近他們控制的過程來減少瓶頸并縮短控制回路。在本應用筆記中,我們將討論提高運營效率和產量的承諾將如何導致自PLC發明以來對工廠運營的最大改革,以及PLC和微型PLC中對更多模擬集成的需求。
介紹
在當今競爭激烈的全球經濟中,制造工藝的微小改進可以產生巨大的競爭優勢。
這種心態正在推動整個工廠車間的根本性變革。制造商正在部署最新的傳感器技術,采用新的控制架構,并開始發現“大數據”和分析的潛力。通常被稱為工業 4.0,制造業正在發生的事情簡直就是一場革命。
對于設備原始設備制造商來說,這是一個巨大的機會。用于跟蹤環境和過程變量的傳感器數量不斷增加。這加速了向分布式控制架構的過渡,在分布式控制架構中,工廠操作員通過將可編程邏輯控制器 (PLC) 移近他們控制的過程來減少瓶頸并縮短控制回路。最終,提高運營效率和產量的承諾將導致自PLC發明以來對工廠運營進行最大規模的改革。
這給PLC工程師帶來了相當大的挑戰。為了在這個市場上獲勝,系統設計人員需要在不斷縮小的機箱中集成更多的I/O和更多功能。問題在于,從微處理器的數字縮放中獲得的空間相對較少。在當今先進的PLC模塊中,模擬和無源元件占用了大約85%的電路板空間。
工程師再也不能忽視他們電路板上的明顯問題了。許多在以前的系統中運行良好的模擬和分立元件對于微型PLC和嵌入式控制器來說實在太大了。工業4.0的承諾只能通過在整個PLC系統設計中進行更高水平的集成來實現。
下一次工業革命已經到來
自 1969 年推出 Modicon 084 以來,PLC 一直處于工業轉型的紐帶。由于數字革命,它們多年來變得越來越強大,能夠處理更多的輸入、更大的單詞和更復雜的指令集。
如今,模擬和傳感器技術的創新正在幫助制造商充分利用工廠和云中可用的大量計算資源。工業 4.0 代表了將這種智能與無處不在的傳感、分布式控制和強大、無縫的連接相結合時可能實現的愿景。
PLC再次發現自己處于革命的中心。這為PLC OEM創造了新的商機,因為制造商增加了資本支出以利用這些技術。然而,這也給系統設計人員帶來了各種挑戰。
實現大數據的承諾
由于摩爾定律的穩步發展,我們現在擁有大量的處理能力。這種處理能力使企業能夠處理數 TB 甚至數 PB 的數據,以增強決策、生成新見解并優化流程。
對于制造商來說,最大的挑戰是收集和處理這些數據。為了解決這個問題,出現了三個技術趨勢:
普適傳感:傳感器及其接口的成本持續下降,使制造商能夠跟蹤更多的變量和數據類型。
分布式控制:將過程控制器移近它們控制的機器可消除瓶頸并提高制造吞吐量和靈活性。
無縫連接:制造商正在將工廠車間連接到企業網絡,以釋放大數據和分析的潛力。這帶來了許多好處,但也在系統級別引發了許多安全問題。
解決新的集成問題
PLC中最大的問題是沒有人看到的問題。最近的一項市場研究表明,大多數工程師仍然認為數字技術提供了節省空間的最佳機會。然而,數字芯片僅占用PLC模塊中15%至20%的電路板空間。
真正的問題是專用于模擬和分立元件的PCB數量。這些器件占用 PLC 模塊中高達 85% 的可用電路板空間(圖 3),但它們不像數字芯片那樣可擴展。因此,PLC現在需要更高水平的集成,以節省PCB空間,同時提供所需的功能。
圖3.在這種典型的微型PLC中,模擬和分立元件占用了80%以上的電路板空間。
解決這一PCB空間問題需要一種新的模擬設計方法。系統設計人員可以選擇具有足夠規格的目錄零件,然后在布局上執行英雄壯舉以使其適合PLC外殼的日子已經一去不復返了。當今的市場要求在空間和能源效率方面進行階梯式功能改進。為了取得成功,設計人員需要系統地尋找機會來簡化模擬電路并降低功耗。
幸運的是,隨著工業市場的發展,Maxim Integrated正在開發解決方案,以利用其集成能力。在單個IC中組合多個分立模擬功能可以為系統設計人員提供尺寸、功耗和成本方面的顯著優勢。
Maxim的Micro-PLC技術演示平臺展示了模擬集成如何使PLC占位面積縮小10倍,運行溫度降低50%,數字I/O吞吐量提高70倍。這些成就都是通過Maxim的智能集成方法和專有的工藝技術實現的。
提高微型 PLC 中的 I/O 密度
I/O是PLC與工業4.0所需的無數傳感器和執行器之間的重要環節。隨著制造商在工廠車間增加更多傳感器,設備設計人員必須將通道密度推得更高,即使PLC中的可用空間不斷縮小。
I/O隔離架構提供了顯著節省空間的機會。傳統方法是每個通道使用一個光耦合器,并將每個光耦合器輸出連接到微控制器上的數字輸入。這種方法在器件數量、電路板空間和數字I/O引腳使用方面成本高昂。
如今,像MAX31911這樣的多通道串行器可以將傳感器和開關的24V數字輸出轉換、調理和串行化至PLC微控制器所需的5V、CMOS兼容電平。這種方法將必要的隔離通道數量減少到僅三個(圖 5)。
更詳細的圖像。
圖5.MAX31911大大減少了用于數字輸入設計的光耦合器數量。
例如,MAX31911為8通道工業接口,支持SPI菊花鏈;來自多個串行器的大量輸入可以共享相同的三個隔離信號。圖6顯示了32通道實現在功耗、器件數量、整體PCB空間尺寸、光耦合器和成本方面的顯著節省。將其與非序列化方法進行比較。
圖6.MAX31911提供的流線型隔離架構為系統設計人員提供了諸多優勢。
降低電源設計中的散熱
更高的I/O密度和更小的外形尺寸也以另一種基本方式增加了設計挑戰,這是不可避免的功耗的結果。系統必須比以往任何時候都更節能,以防止PLC過熱,特別是在通常不接受風扇和通風口的應用中。 PLC中經常被忽視的熱源是I2直流配電饋電中的 R 損耗。通常,24V用于PLC背板,而12V用于板載配電。更好的方法是全板使用48V,因為這可將電流降低4倍,相應地將PCB銅損降低16倍。
使用MAX17503等高壓負載點(POL)DC-DC轉換器,無需中間DC-DC轉換級。這些轉換器直接在高達 60V 的輸入下工作,可在低電壓下實現數字、模擬和混合信號負載的單級轉換。轉換器釋放了寶貴的電路板空間,同時避免了間隙級的成本和能量損失。此外,由于其同步開關架構,它們最大限度地減少了銅損,降低了連接器接觸電流額定值,提高了可靠性,并保持了低溫運行(通常溫度降低 50%)(圖 7)。
圖7.Maxim的60V同步整流DC-DC,如MAX17503,可大幅降低熱量、尺寸和元件數量。
降低電源子系統的復雜性
當今的信號調理、處理和通信電路需要一組不同的電源軌,通常相差幾伏或只有幾分之一伏。這加劇了本已復雜的電氣環境。除此之外,通過各種功率控制方法實現的日益復雜的節能方法以及電源子系統的成本和復雜性只會進一步增加。
Maxim的Beyond the Rails?產品簡化了信號鏈,使設計(圖8)允許±10V雙極性輸入多路復用、放大、濾波和數字化,全部采用5V單電源供電。這種方法消除了對額外 ±15V 電源的需求;從而減少元件數量、系統成本、功耗和占位面積。
圖8.Beyond the Rails產品通過采用+5V單電源支持高達±10V的電源軌,簡化了電源子系統設計。
集成針對新安全威脅的保護措施
當工廠網絡對外部關閉時,IT安全問題通常涉及流氓員工和內部數據盜竊。那些“美好的過去”已經一去不復返了。當今的互聯網連接 PLC 必須受到保護,以抵御多種威脅,包括黑客、惡意軟件和病毒。
系統級軟件提供初始級別的保護,但在許多情況下,這還不夠。需要基于硬件的安全性來防止:
克隆或偽造組件:假冒的現場傳感器和I/O模塊對您的底線構成了真正的威脅。但還有一個更大的危險:假冒現場傳感器可能被用來對工業環境進行攻擊。使用安全認證IC是保證傳感器讀數從關鍵組件發送到PLC的唯一方法。
惡意軟件注入:Stuxnet給行業敲響了警鐘。系統操作員必須確保構建監控和數據采集(SCADA)或分布式控制(DCS)系統的所有設備都運行正版軟件。安全啟動和安全更新管理是保護設備免受惡意軟件注入的最佳方法。安全協處理器可用于實現加密設計,以最少的設計工作完全解決這些問題。
竊聽:隨著對工業間諜活動的擔憂增加,制造商必須確保未經授權的用戶無法從工業網絡中竊取商業機密。加密和身份驗證IC可以防止此類竊聽,并進一步提供主動篡改檢測,以防止對硬件組件的暴力攻擊。
Maxim在ATM、銷售點(POS)系統和打印機墨盒等耗材的硬件安全實施方面有著悠久的歷史。安全產品組合范圍從簡單的身份驗證引擎到實現基于標準的高級加密算法的復雜、安全的微控制器。
圖9.Maxim提供完整的硬件安全產品組合,以滿足各種安全需求和價位。
抓住PLC的集成優勢
工業 4.0 正在從根本上改變在 PLC 市場中獲勝所需的條件。當今的成功需要新的戰略來管理對在更小空間內實現更多功能的競爭需求 - 更小的外形尺寸、更高的 I/O 密度和高級功能。
這個問題不能用摩爾定律來解決。這些系統中的大量模擬內容意味著PLC工程師不能再忽視擺在他們面前的集成問題 - 當成功取決于您可以在每厘米的空間中容納多少功能時。系統地尋求更高水平的組件集成的工程師將在制造商追求工業4.0承諾的好處時處于有利地位。
審核編輯:郭婷
-
傳感器
+關注
關注
2548文章
50668瀏覽量
751981 -
控制器
+關注
關注
112文章
16198瀏覽量
177399 -
可編程邏輯
+關注
關注
7文章
514瀏覽量
44072
發布評論請先 登錄
相關推薦
PLC可編程邏輯控制器的設計原則
可編程邏輯控制器是什么_可編程邏輯控制器原理
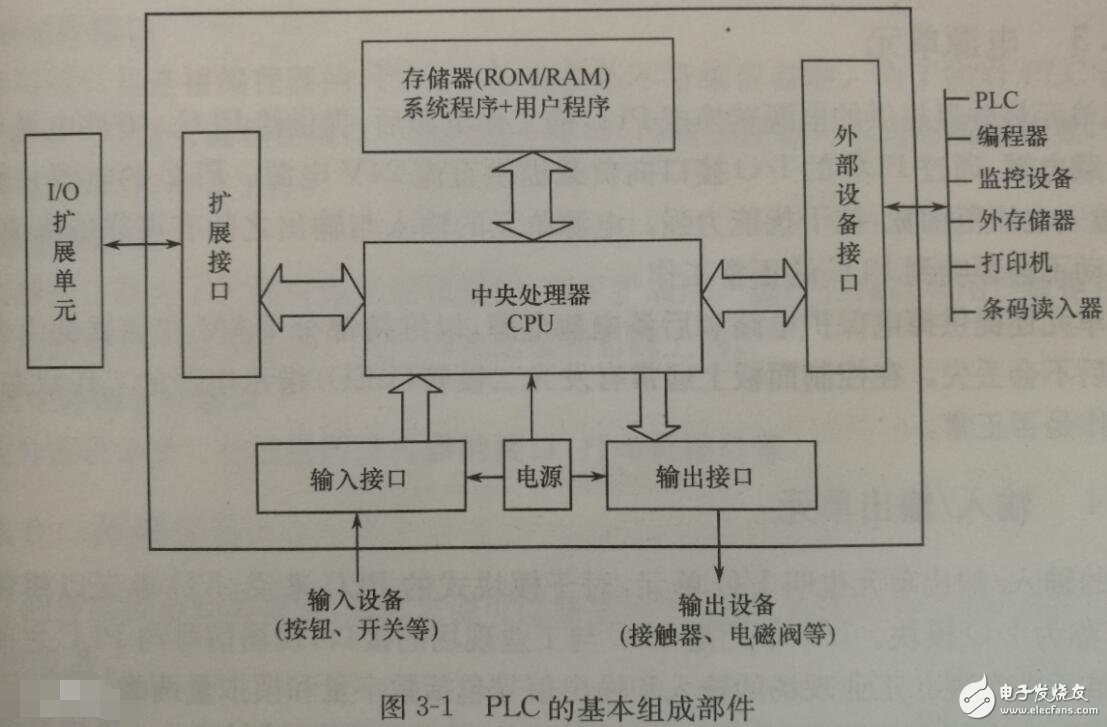
可編程邏輯控制繼電器
可編程控制器PLC概述
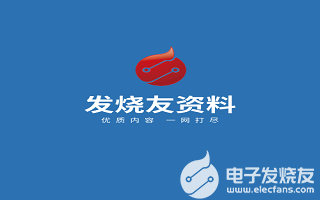
評論