SMT工藝 PCB布局設(shè)計(jì)參考建議
注意點(diǎn)—1:
基板上必備的設(shè)計(jì)內(nèi)容 1.基板上必須具備有MARK點(diǎn),通常采用方形或圓形設(shè)計(jì)。直徑/邊長在0.8mm-1.2mm使用較多。
2.MARK點(diǎn)通常設(shè)計(jì)為對角線。
3.MARK點(diǎn)與基板上任何元件都應(yīng)距離板邊3mm以上建議5mm,因?yàn)樵O(shè)備軌道兩側(cè)必須各留出3mm進(jìn)行基板的固定。
4. 基板加工精度 ?基板 MARK 基板原點(diǎn) 的加工精度:±0.05m
注意點(diǎn)—2:
注意點(diǎn)—3:
基板布局通孔的設(shè)計(jì)——避免在焊盤上開通孔
注意點(diǎn)—4:
焊盤尺寸的設(shè)計(jì) 通常膠水工藝元件從1608-3216(公制) 1)避免出現(xiàn)焊盤大小不一的現(xiàn)象
2)焊盤尺寸的設(shè)計(jì)一定要與元件的尺寸相匹配堅(jiān)決避免出現(xiàn)1608的元件使用2125或3216的焊盤的現(xiàn)象 例:一一對應(yīng)
注意點(diǎn)—5
基板的鍍層考慮當(dāng)前使用的有鉛類的鍍sn-pb較多,無鉛類的采用OSP和鍍純sn,最好與基板供應(yīng)商進(jìn)行溝通。
(二)SMT 基板可制造性設(shè)計(jì)基礎(chǔ)介紹
DFM設(shè)計(jì)(PCB)一般原則
1.PCB外形和尺寸應(yīng)與結(jié)構(gòu)設(shè)計(jì)一致,器件選型應(yīng)滿足結(jié)構(gòu)件的限高要求,元器件布局不應(yīng)導(dǎo)致裝配干涉
2.PCB外形以及定位孔、安裝孔等的設(shè)計(jì)應(yīng)考慮PCB制造的加工誤差以及結(jié)構(gòu)件的加工誤差
3.PCB布局選用的組裝流程應(yīng)使生產(chǎn)效率最高;設(shè)計(jì)者應(yīng)考慮板形設(shè)計(jì)是否最大限度地減少組裝流程的問題,即多層板或雙面板的設(shè)計(jì)能否用單面板代替?PCB每一面是否能用一種組裝流程完成?能否最大限度地不用手工焊?使用的插裝元件能否用貼片元件代替?
4.選用元件的封裝應(yīng)與實(shí)物統(tǒng)一,焊盤間距、大小滿足設(shè)計(jì)要求;
5.元器件均勻分布﹐特別要把大功率的器件分散開﹐避免電路工作時(shí)PCB上局部過熱產(chǎn)生應(yīng)力﹐影響焊點(diǎn)的可靠性;
6.考慮大功率器件的散熱設(shè)計(jì);
7.在設(shè)計(jì)許可的條件下,元器件的布局盡可能做到同類元器件按相同的方向排列,相同功能的模塊集中在一起布置;相同封裝的元器件等距離放置,以便元件貼裝、焊接和檢測;
8.絲印清晰可辨,極性、方向指示明確,且不被組裝好后的器件遮擋住。
元件分布
1.均勻,方向盡量統(tǒng)一
2.采用回流焊工藝時(shí),元器件的長軸應(yīng)與工藝邊方向(即板傳送方向)垂直﹐這樣可以防止在焊接過程中出現(xiàn)元器件在板上漂移或采用波峰焊工藝時(shí),無源元件的長軸應(yīng)垂直于工藝邊方向,這樣可以防止PCB受熱產(chǎn)生變形時(shí)導(dǎo)致元件破裂,尤其片式陶瓷電容的抗拉能力比較差
3.雙面貼裝的元器件﹐兩面上體積較大的器件要錯(cuò)開安裝位置﹐否則在焊接過程中會因?yàn)榫植繜崛萘吭龃蠖绊懞附有Ч?/p>
4.小、低元件不要埋在大、高元件群中,影響檢修
5.0603以下、SOJ、PLCC、BGA、0.6mm Pitch以下的SOP、本體托起高度(Standoff)>0.15mm的器件不能放在波峰面;QFP器件在波峰面要成45°布局
6.安裝在波峰焊接面上的SMT大器件(含SOT23器件)﹐其長軸要和焊錫波峰流動的方向(即工藝邊方向)平行﹐這樣可以減少引腳間的焊錫橋接
7.波峰焊接面上的大、小SMT元器件不能排成一條直線,要錯(cuò)開位置,較小的元件不應(yīng)排在較大的元件之后,這樣可以防止焊接時(shí)因焊料波峰的 “陰影”效應(yīng)造成的虛焊和漏焊
8.較輕的THT器件如二級管和1/4W電阻等,布局時(shí)應(yīng)使其軸線和波峰焊方向垂直,以防止過波峰焊時(shí)因一端先焊接凝固而使器件產(chǎn)生浮高現(xiàn)象
9.SMD元件間隔應(yīng)滿足設(shè)計(jì)標(biāo)準(zhǔn),THT元件間隔應(yīng)利于操作和替換
10.經(jīng)常插拔器件或板邊連接器周圍3mm 范圍內(nèi)盡量不布置SMD,以防止連接器插拔時(shí)產(chǎn)生的應(yīng)力損壞器件
11.為了保證可維修性,BGA 器件周圍需留有3mm 禁布區(qū),最佳為5mm 禁布區(qū)。一般情況下BGA 不允許放置在背面;當(dāng)背面有BGA 器件時(shí),不能在正面BGA 5mm 禁布區(qū)的投影范圍內(nèi)布器件
12.可調(diào)器件周圍留有足夠的空間供調(diào)試和維修;應(yīng)根據(jù)系統(tǒng)或模塊的PCBA安裝布局以及可調(diào)器件的調(diào)測方式來綜合考慮可調(diào)器件的排布方向、調(diào)測空間。
焊盤設(shè)計(jì)
1.SMT焊盤設(shè)計(jì)遵循相關(guān)標(biāo)準(zhǔn),如IPC782標(biāo)準(zhǔn)
2.波峰面上的SMT元器件,其較大元件的焊盤(如三極管﹑插座等)要適當(dāng)加大,如SOT23之焊盤可加長0.8-1mm,這樣可以避免因元件的 “陰影效應(yīng)”而產(chǎn)生的空焊
3.焊盤大小要根據(jù)元器件的尺寸確定,焊盤的寬度等于或略大于元器件引腳的寬度,焊接效果最好
4.對于通孔來說,為了保證焊接效果最佳,引腳與孔徑的縫隙應(yīng)在0.25mm~0.70mm之間。較大的孔徑對插裝有利,而想要得到好的毛細(xì)效果則要求有較小的孔徑,因此需要在這兩者之間取得一個(gè)平衡
5.在兩個(gè)互相連接的SMD元件之間﹐要避免采用單個(gè)的大焊盤﹐因?yàn)榇蠛副P上的焊錫將把兩元器件拉向中間﹐正確的做法是把兩元器件的焊盤分開﹐在兩個(gè)焊盤中間用較細(xì)的導(dǎo)線連接﹐如果要求導(dǎo)線通過較大的電流可并聯(lián)幾根導(dǎo)線﹐導(dǎo)線上覆蓋綠油
6.SMT元件的焊盤上或其附近不能有通孔,否則在回流焊過程中,焊盤上的焊錫熔化后會沿著通孔流走,會產(chǎn)生虛焊﹐少錫﹐還可能流到板的另一面造成短路
7.軸向器件和跳線的引腳間距(即焊盤間距)的種類應(yīng)盡量減少,以減少器件成型的調(diào)整次數(shù),提高插件效率
8.需波峰焊的貼片IC各腳焊盤之間要加阻焊漆,在最后一腳要設(shè)計(jì)偷錫焊盤
9.未做特別要求時(shí),元件孔形狀、焊盤與元件腳形狀必須匹配,并保證焊盤相對于孔中心的對稱性(方形元件腳配方形元件孔、方形焊盤;圓形元件腳配圓形元件孔、圓形焊盤),以保證焊點(diǎn)吃錫飽滿
10.需要過錫爐后才焊的元件,焊盤要開走錫位,方向與過錫方向相反,寬度視孔的大小為0.5~1.0mm,以防止過波峰后堵孔
11.增大銅皮,增大邊引腳的引力,便于回流焊自對中
12.插件元件每排引腳較多時(shí),以焊盤排列方向平行于進(jìn)板方向布置器件時(shí),當(dāng)相鄰焊盤邊緣間距為0.6mm~1.0mm 時(shí),推薦采用橢圓形焊盤或加偷錫焊盤,受PCB LAYOUT限制無法設(shè)置竊錫焊盤時(shí),應(yīng)將DIP后方與焊盤鄰近或相連的線路綠漆開放為裸銅,作為竊錫焊盤用
13.為防止過波峰時(shí)焊錫從通孔上溢到上板,導(dǎo)致零件對地短路或零件腳之間短路,設(shè)計(jì)多層板時(shí)要注意,金屬外殼的元件,插件時(shí)外殼與印制板接觸的,頂層的焊盤不可開,一定要用綠油或絲印油蓋住(例如兩腳的晶振、3只腳的LED)
走線要求
1.板面布線應(yīng)疏密得當(dāng),當(dāng)疏密差別太大時(shí)應(yīng)以網(wǎng)狀銅箔填充
2.為了保證PCB加工時(shí)不出現(xiàn)露銅的缺陷,要求所有的走線及銅箔距離板邊:V-CUT邊大于0.75mm,銑槽邊大于0.3mm(銅箔離板邊的距離還應(yīng)滿足安裝要求)
3.考慮到PCB加工時(shí)鉆孔的誤差,所有走線距非安裝孔都有最小距離要求。
o1)孔徑<80mil(2mm),走線距孔邊緣>8mil;
o2)80mil(2mm)<孔徑<120mil(3mm),
o走線距孔邊緣>12mil;
o3)孔徑>120mil(3mm),走線距孔邊緣>16mil
4.金屬外殼器件下不可有過孔和表層走線
5.滿足各類螺絲孔的禁布區(qū)要求
6.所有的走線拐彎處不允許有直角轉(zhuǎn)折點(diǎn)
7.SMT焊盤引出的走線,盡量垂直引出,避免斜向拉線
8.當(dāng)從引腳寬度比走線細(xì)的SMT焊盤引線時(shí),走線不能從焊盤上覆蓋,應(yīng)從焊盤末端引線
9.當(dāng)密間距的SMT焊盤引線需要互連時(shí),應(yīng)在焊盤外部進(jìn)行連接,不允許在焊盤中間直接連接
PCB尺寸及外形要求
1.圓角:為方便單板加工,不拼板的單板板角應(yīng)為R型倒角,對于有工藝邊和拼板的單板,工藝邊應(yīng)為R型倒角,一般圓角直徑為Φ5,小板可適當(dāng)調(diào)整。有特殊要求按結(jié)構(gòu)圖表示方法明確標(biāo)出R大小,以便廠家加工
2.工藝邊:板邊5mm范圍內(nèi)有較多元器件影響PCB加工時(shí),可以采用加輔助邊(工藝邊)的方法,工藝邊一般加在長邊
3.Mark點(diǎn):基準(zhǔn)點(diǎn)用于錫膏印刷和元件貼片時(shí)的光學(xué)定位。根據(jù)基準(zhǔn)點(diǎn)在PCB板上的用途,可以分為全局基準(zhǔn)點(diǎn)、單元板基準(zhǔn)點(diǎn)、個(gè)別器件基準(zhǔn)點(diǎn)
4.有表貼器件的PCB 板對角至少有兩個(gè)不對稱基準(zhǔn)點(diǎn)
5.形狀:基準(zhǔn)點(diǎn)的優(yōu)選形狀為實(shí)心圓
6.大小:基準(zhǔn)點(diǎn)的優(yōu)選尺寸為直徑40mil±1mil
7.材料:基準(zhǔn)點(diǎn)的材料為裸銅或覆銅,為了增加基準(zhǔn)點(diǎn)和基板之間的對比度,可在基準(zhǔn)點(diǎn)下面敷設(shè)大的銅箔
8.為了保證印刷和貼片的識別效果,基準(zhǔn)點(diǎn)范圍內(nèi)應(yīng)無其它走線及絲印
9.基準(zhǔn)點(diǎn)中心距板邊大于5mm,并有金屬圈保護(hù),基準(zhǔn)點(diǎn)中心1.5mm(60mil)直徑范圍內(nèi)開阻焊窗
10.需要拼板的單板,每塊單元板上盡量保證有基準(zhǔn)點(diǎn)
11.對于引線間距≤0.5mm的QFP和球間距≤0.8mm的BGA封裝的器件,為提高貼片精度,要求在IC兩對角設(shè)置基準(zhǔn)點(diǎn)
拼板:當(dāng)PCB尺寸小于50mm×50mm的PCB應(yīng)進(jìn)行拼板
1、采用拼板的目的
1)單元板面積太小,無法單獨(dú)在設(shè)備上加工
2)為了提高生產(chǎn)效率
2、單元板間的連接方式主要有V-CUT槽和銑槽
1)常用于單元板和單元板的直接直線連接,為直通型,不能在中間停止或轉(zhuǎn)彎
2)銑槽常用于單元板間需要留有一定距離或某一部分需要與板分離的
情況,一般和V-CUT槽配合使用
3)采用V-CUT槽拼板時(shí),若拼板后板邊元器件能滿足生產(chǎn)設(shè)備的工藝邊要求,可以不加額外的工藝邊,若不能滿足生產(chǎn)設(shè)備的工藝邊要求,必須加工藝邊
4)采用銑槽拼板時(shí),必須加輔助邊(工藝邊),否則單元板之間無法連接。
5)當(dāng)較小尺寸單元板由于結(jié)構(gòu)安裝上的要求需要作圓角或斜角時(shí),拼板方式必須是銑槽加工藝邊
3、拼板方式:縱橫拼板、對拼、正反拼板。對拼適合兩塊不規(guī)則的電路板,正反拼適合采用雙面回流焊工藝的電路板;
絲印要求:清晰可辨且與BOM清單中一致,極性方向標(biāo)記易于辨認(rèn)
審核編輯 :李倩
-
pcb
+關(guān)注
關(guān)注
4318文章
23022瀏覽量
396428 -
焊接
+關(guān)注
關(guān)注
38文章
3069瀏覽量
59609 -
smt
+關(guān)注
關(guān)注
40文章
2885瀏覽量
69069 -
SMT工藝
+關(guān)注
關(guān)注
2文章
26瀏覽量
13112
原文標(biāo)題:SMT工藝&PCB 布局設(shè)計(jì)參考建議
文章出處:【微信號:現(xiàn)代電子裝聯(lián)工藝技術(shù)交流平臺,微信公眾號:現(xiàn)代電子裝聯(lián)工藝技術(shù)交流平臺】歡迎添加關(guān)注!文章轉(zhuǎn)載請注明出處。
發(fā)布評論請先 登錄
相關(guān)推薦
SMT基本工藝
誠聘PCB 工藝工程師
MT2492的PCB布局設(shè)計(jì)建議
PW2162的PCB布局設(shè)計(jì)的建議是什么
SMT焊接工藝解讀
關(guān)于PCB布局和SMT表面貼裝技術(shù)
分享一些焊接角度下的PCB布局設(shè)計(jì)建議
SMT組裝工藝流程的應(yīng)用場景
PCB板的SMT組裝工藝與焊接工藝介紹
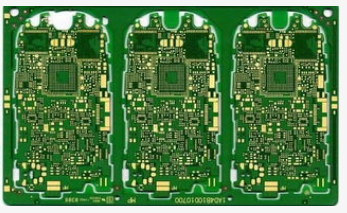
如何對PCB設(shè)計(jì)進(jìn)行合理的布局,有哪些要求
SMT無鉛錫膏印刷的PCB工藝要求有哪些?
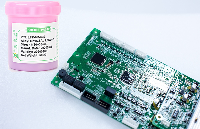
評論