本應用筆記討論了Maxim Integrated的uSLIC?封裝,并提供了PCB設計和電路板組裝工藝指南。
介紹
uSLIC? 封裝是一種基于基板的無引線開放式框架封裝,在基板中嵌入芯片,并在頂部組裝無源元件。
uSLIC封裝具有以下幾個優點:
每個 I/O 占用空間小,可顯著節省 PCB 空間。
與側對側 SIP 封裝相比,具有卓越的電氣性能。
使用標準表面貼裝組裝技術。
圖1.uSLIC封裝的封裝外形圖(具體示例(MAXM17532):A = 1.5mm ±0.15mm, A1 = 1.2mm(最大), b = 0.25mm ±0.05mm, c = 0.05mm ±0.05mm, D = 3.00mm ±0.05mm, E = 2.60mm ±0.05mm, e = 0.50mm ±0.05mm, F = 2.50mm ±0.20mm, G = 2.00mm ±0.20mm, L = 0.40mm ±0.05mm)。
印刷電路板設計指南
建議使用 FR-4 或 BT 層壓材料的 PCB。建議使用常見的表面光潔度,例如有機可焊性防腐劑(OSP)和化學鍍鎳/沉金(ENIG)。
為了獲得最佳的制造良率和產品性能,需要精心設計和制造的 PCB.對于0.5mm的間距尺寸,Maxim建議使用NSMD焊盤,因為它提供了更大的金屬面積 使焊料固定在金屬焊盤的邊緣。NSMD提高了焊點的可靠性。請參考Maxim的90-100027進行焊盤模式設計。 在封裝邊界外適度延伸焊盤圖案(約0.15mm)有助于減少焊錫空隙,因為用于除氣和檢查單元和PCB之間的焊接連接的表面積更長;因此,擴展 建議以這種方式使用焊盤模式。SMD模式以及免清洗焊料可能會導致焊珠留在PCB上;因此,不建議使用 SMD 模式。
對于非 SMD 焊盤模式,SM 開路區域中的 Cu 走線應為 75μm 至 100μm,以避免器件間距減少,并應在電路板上沿不同方向進行平衡,以避免器件偏移。
圖2.推薦的“擴展焊盤圖案”設計顯示 (a) 良好的焊料空洞水平和 (b) 可側面檢查。
處理
Maxim不建議在PCB上手動表面安裝器件,因為器件的尺寸和配置不同。如果需要手動處理,建議執行以下操作:
使用帶軟頭的真空拾取手動工具
拿起和放置模塊時用最小的力。停在上方約 1 毫米處,然后將設備釋放到其容器中
模版
模板厚度和圖案幾何形狀決定了沉積到器件焊盤圖案上的焊膏的精確體積。鋼網對準精度和一致的焊接量 轉移對于均勻的焊料回流至關重要。
建議使用不銹鋼激光切割模板。方形模板開口優于圓形開口,方形孔的角可以圓角 促進焊料脫模。為了進一步改善焊料釋放,開口的底部開口應大于頂部,以形成~5°C的正夯錘。馬克西姆建議使用 4mil至5mil的模板厚度。與PCB焊盤尺寸相比,每側設計為-1mil至~+1mil(-25μm至~+25μm)的模板開口顯示出良好的焊接效果。這 模板孔徑必須滿足行業標準面積比(孔徑開口面積/孔徑壁面積)>0.66。
貼片組裝
標準SMT設備和工藝用于uSLIC組裝。流程如下:
圖3.推薦的uSLIC組裝工藝。
焊膏或助焊劑印刷和助焊劑浸漬方法均可提供可接受的裝配質量和可靠性。
焊膏
Maxim建議使用具有NSMD焊盤圖案的III型或IV型免清洗焊膏。低殘留、免清洗焊膏 (共晶Sn63/Pb37或無鉛SAC305合金SnAgCu)是常用的。免清洗焊料, 然而, 與具有 SMD 焊盤圖案的 PCB 一起使用在我們的研究中顯示了焊珠,不建議使用. 如果設備下方的殘留物可以充分清潔,則可以使用水溶性糊劑。
圖4.使用SMD焊盤圖案在PCB上使用免清洗焊料來觀察焊珠(黑色箭頭)。
自動組件拾取和放置
建議使用貼裝精度優于 ±0.05mm 的拾取和放置機。常規貼裝 可以使用uSLIC輪廓或焊盤的位置作為貼裝指南來使用系統。使用焊盤位置的貼裝指南往往更準確,但速度較慢,并且需要復雜的視覺處理系統。封裝輪廓放置方法運行速度更快,但精度較低。合同PCB組裝商可以確定用于此過程的最可接受的方法.建議使用較低的安裝速度,以防止漿料擠出。建議使用以下拾取和放置參數:
拾音區域是電感器的頂部,為2mm x 2.5mm。拾取位置必須位于電感器的中央。
使用1.3mm或更小的噴嘴。在噴嘴拾取區外拾取會導致電感器破裂。
使用最小力或不超過 3N (0.305kgf)。離型力應該是工藝優化的一部分,以便將單元壓入焊料中,但不會導致焊珠或橋接問題。過多不必要的力也會導致設備損壞,應避免使用。
將設備移入其容器時,停在設備上方 1mm 處以拾取部件并將部件釋放到托盤中。
圖5.(a) 建議的噴嘴拾取區域(綠色圓圈);(b) 將噴嘴放置在拾取區外可能會引起電感器頂部裂紋(示例顯示使用直徑為 1.48mm 的噴嘴偏離中心放置)。
回流焊曲線
Maxim建議使用8區或更大的烤箱。氮氣氣氛烘箱是首選,因為它提供更好的潤濕性能并減少 焊點空隙。
與所有表面貼裝器件一樣,作為整體工藝開發的一部分,對回流曲線進行優化和測試非常重要。此外,配置文件 必須在電路板上的不同位置進行檢查,以確保最熱和最冷的溫度仍在回流曲線的推薦溫度范圍內。 元件溫度可能會因周圍元件、器件在 PCB 上的位置和封裝密度而異。
回流曲線指南基于PCB焊盤焊點位置的實際引線溫度。 焊點的實際溫度通常與回流系統中的溫度設置不同。 重要的是,在實際焊點位置使用熱電偶完成回流特定型材,并且 使用下面圖 6 中概述的“無鉛”焊料回流指南進行表征。
區 | 1 | 2 | 3 | 4 | 5 | 6 | 7 | 8 |
返回頁首 | 89 | 142 | 180 | 201 | 259 | 253 | 201 | 139 |
底 | 89 | 142 | 180 | 201 | 259 | 253 | 201 | 139 |
輸送速度(厘米/分鐘): 56.0 |
圖6.根據 JEDEC JSTD-020 推薦的無鉛焊料回流曲線。
焊點檢測
PCB上uSLIC的回流焊后檢測通常通過使用目視檢測和透射型X射線來完成。 X 射線可用于回流焊過程監控和故障分析工具。斜二維 X 射線系統 建議以最高放大倍率 (OVHM) 查看,因為它可以檢測焊橋、開路和空隙。
濕氣敏感性
所有Maxim uSLIC模塊均符合JEDEC規范JSTD3D.020的MSL1標準。零件以卷帶形式運輸。 所有部件均經過烘烤和干燥包裝,并帶有干燥劑和濕度指示卡。如果濕度指示卡變成粉紅色,或者部件暴露的時間超過其地板壽命,請將包裝在 125°C 下烘烤 48 小時。
重做
請參閱 JEDEC 規范 J-STD-033C 了解濕氣和回流焊敏感表面貼裝器件的返工。建議返工 使用自動熱風返修站。建議局部加熱以去除uSLIC組件。建議在返工過程之前在 125°C 下烘烤安裝了 uSLIC 的 PCB.
從多氯聯苯中去除uSLIC
PCB的底部應使用對流加熱器加熱,同時在組件的頂部使用熱空氣或氣體(以防止翹曲)。 噴嘴應僅用于將空氣引導至組件,以減少相鄰組件的加熱。噴嘴尺寸應遵循 “自動組件拾取和放置”部分中推薦的拾取和放置噴嘴尺寸。還應避免過多的氣流。風速 每分鐘15升至20升是一個很好的起點。應在頂部和底部使用熱電偶來監測零件的實際溫度。 零件最高溫度應高于217°C的液體溫度,但不應超過245°C。 接頭回流后,在從回流焊到冷卻以移除零件的過渡期間,真空提離應自動接合。
更換 uSLIC
如果使用特定于組件的微型模板,則可以實現均勻和精確的沉積。模板孔徑應與 放大倍率為 50 倍至 100 倍的焊盤。然后將模板降低到PCB上,并用小金屬刮刀沉積糊劑。 遵循原始 PCB 組裝提供的模板厚度、模板設計、焊接建議和絲網印刷指南。
由于引線位于封裝的底部,因此應使用分束光學系統對準主板上的組件。對齊方式應 以 50 倍至 100 倍放大倍率完成。貼片機應具有允許在 X、Y 和旋轉軸上進行微調的能力。拿起 單元在推薦的拾取區域內,并將其對準焊膏區域。然后,放置設備。在原始連接期間形成的回流曲線或 應使用移除來連接新組件。
沖擊和振動數據
機械沖擊
標準:JESD22-B111 和 JESD22-B104 條件 B
測試條件:
峰值電平 – 1500G(半正弦波形)
持續時間 – 0.5 毫秒
振動
標準:JESD22-B103,條件-3
測試條件:
峰值加速度 – 3G
峰峰值位移 – 0.75mm
交叉頻率 – 45Hz
最小頻率 – 5Hz
最大頻率 – 500Hz
審核編輯:郭婷
-
pcb
+關注
關注
4318文章
23022瀏覽量
396430 -
電路板
+關注
關注
140文章
4911瀏覽量
97456 -
SiP
+關注
關注
5文章
500瀏覽量
105266
發布評論請先 登錄
相關推薦
QFN封裝的組裝和PCB布局指南
MEMS麥克風封裝的組裝指南和建議
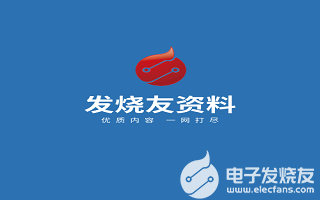
0.5mm層疊封裝應用處理器的PCB組裝指南,第II部分
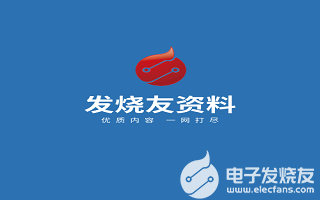
0.4mm層疊封裝(PoP)封裝的PCB組裝指南,第二部分
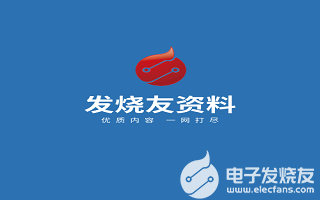
評論