α-氧化鋁(下稱氧化鋁)導熱粉體因來源廣,成本低,在聚合物基體中填充量大,具有較高性價比,是制備導熱硅膠墊片最常用的導熱粉體。氧化鋁形貌有球形、角型、類球形等,不同形貌對熱界面材料的加工性能、應用性能、成本等有不同影響,加之不同粒徑的影響,在體系中會形成一定的孔隙,影響導熱界面材料的導熱系數。本文將從以下幾個方面探討不同形貌、不同粒徑的氧化鋁導熱粉體的搭配工藝,為制備高導熱硅膠墊片提供參考。
1、同等粒徑相同添加量下,不同形貌
選取5μm和45μm的球形、類球形氧化鋁形、角形氧化鋁在添加量75%下測試其對導熱硅膠墊片加工粘度的影響,相同粒徑球形氧化鋁的加工粘度最小,角形氧化鋁加工粘度最大;相同形貌粒徑越大,加工粘度越低。主要是因為同等粒徑下,球形氧化鋁表面能越小,球的表面流動性越好,與基體攪拌成膜均勻,體系粘度就越低,而角形氧化鋁形貌不規則,其顆粒的表面能大,顆粒之間越易粘附在一起,粘度就越大;而在相同相貌下,粒徑越大,吸油值越小。
2、同等粒徑不同形貌下,不同添加量
選取45μm類球形氧化鋁形、球形、角形氧化鋁,分別在75%、80%、85%添加量下測試對導熱硅膠墊片導熱系數的影響,在同等添加量下,75%添加量時角形氧化鋁制備的導熱硅膠墊片的導熱系數較高。添加量在80%和85%時,類球形氧化鋁形氧化鋁制備的導熱硅膠墊片導熱系數較高。在添加量較少時,隨著添加量增加,三種形貌氧化鋁制備的墊片導熱系數不斷升高。由于角型氧化鋁比表面積大,在基體中形成的導熱網絡會更多,因此墊片的導熱效果較好。當添加量增加,由于類球形氧化鋁是單晶顆粒、轉化率高、顆粒表面光滑,導熱系數最高,雖然球形氧化鋁球形度好,但是轉化率較低并且顆粒表面粗糙,導致導熱系數較低。
3、同等形貌不同添加量氧化鋁導熱粉體,在不同復配比例
考慮最佳性價比和粉體顆粒堆積原理,選取45μm球形氧化鋁、45μm類球形氧化鋁和5μm角型氧化鋁以2:2:1,2:1:1,1:2:1,1:1:1復配分別在80%、85%、90%的添加量下對導熱硅膠墊片導熱系數的影響。相同復配比例,隨著添加量增加,四種復配粉體填充的墊片導熱系數不斷增加,這是由于隨著粉體添加量增加,顆粒之間的接觸點越多,逐漸形成致密導熱網絡,因此導熱系數增加。另外,由于類球形氧化鋁的轉化率高,導熱系數高,因此其比例較大,導熱硅膠墊片導熱系數的提升越明顯。
4、同等添加量及不同復配比例對復配氧化鋁導熱粉體堆積性能的影響
選取45μm球形氧化鋁、45μm類球形氧化鋁和5μm角型氧化鋁以2:2:1、2:1:1、1:2:1、1:1:1比例復配,球形氧化鋁、類球形氧化鋁與角形氧化鋁比例1:2:1時堆積密度最大,這是因為顆粒之間的縫隙被相互填充,空隙小,密度大。
另外制作導熱硅膠墊片時,常常會遇到粘膜、表面掉粉問題。造成這一問題原因之一是粉體與硅油相容性差,油粉粘度高、混合不均勻,使得墊片內聚強度低,分子間作用力小于墊片表面與離型膜的吸附力,導致墊片剝離時出現粘膜、表面掉粉現象。如何解決這個問題?
導熱劑等產品可較好解決這樣問題。與普通導熱粉體不同的是,這類導熱粉體采用我司獨有的改性技術制備而成,增強了粉體與硅油之間的相容性,確保硅膠中即使填充了大量該導熱粉體,仍能分散均勻,使導熱硅膠墊片具有較高的內聚強度,從而改善墊片撕膜時粘膜、表面掉粉現象。
導熱硅膠墊片時,由于粒徑太粗,導致墊片有針眼。怎么辦?
通過限制高導熱粉體最大粒徑,同時配以復合搭配和表面改性技術,研發了一款高性能導熱粉體。該產品堆積密度大,應用時可以降低復合體系的空隙,不僅能避免體系出現針眼,還能提高材料導熱系數。另外,改性技術降低了粉體表面極性,改善了粉體與樹脂的相容性,使體系易排泡。
綜上,要制備高導熱率導熱硅膠墊片,需要尋求合適的導熱粉體原料、粉體形貌,確認粒徑級配等,非一步即可完成。東超新材料在氧化鋁、氫氧化鋁等的應用研究已經有10+年的經驗,可根據客戶具體的產品指標、工藝特色、應用目標,提供個性化的導熱阻燃高分子材料解決方案。
審核編輯黃宇
-
導熱
+關注
關注
0文章
303瀏覽量
12969 -
硅膠
+關注
關注
0文章
44瀏覽量
3651
發布評論請先 登錄
相關推薦
氧化鋁隔斷粉在氧化鋁陶瓷基板的應用
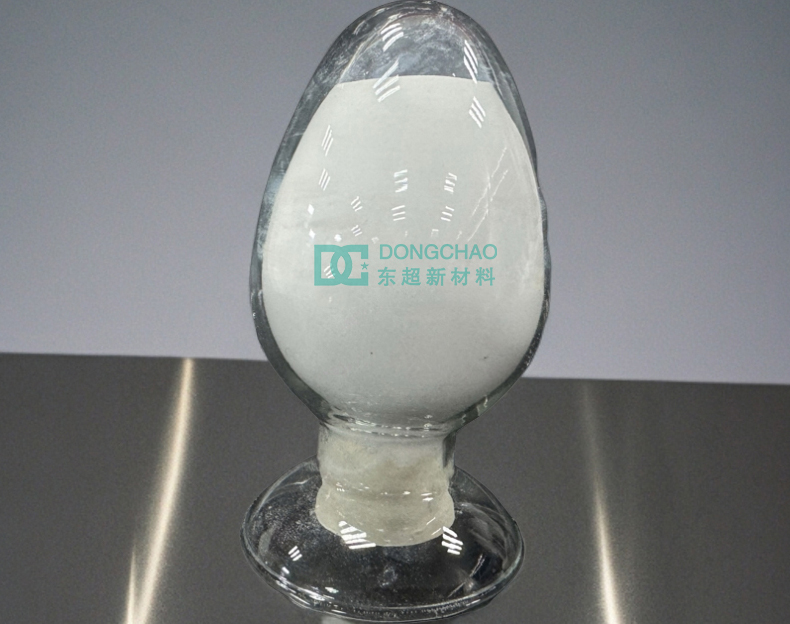
汽車ADAS系統高效散熱,球形氧化鋁導熱粉體解決方案
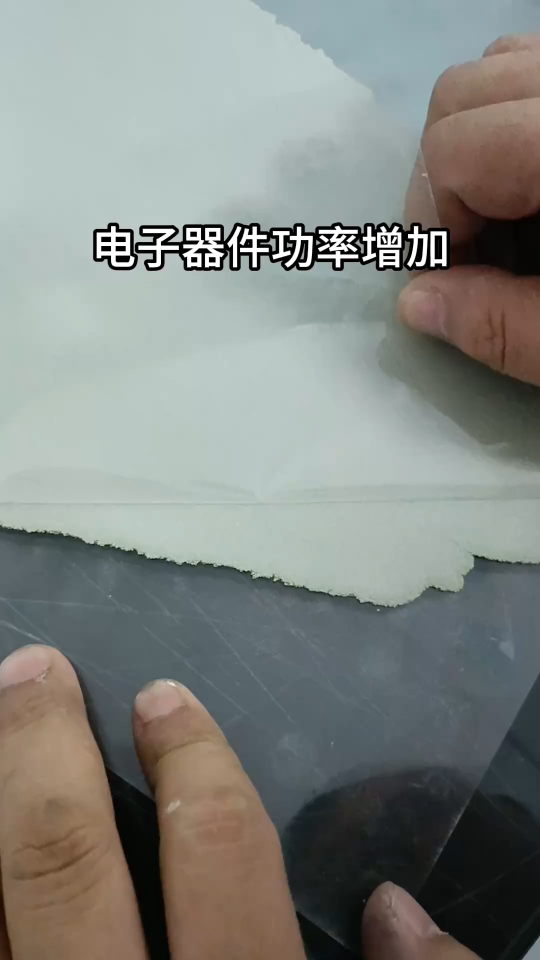
探索新能源汽車電池三大散熱方案及氧化鋁導熱粉導熱界面材料的應用
5G時代下,無機填料氧化鋁導熱粉在覆銅板市場的發展趨勢與重要性
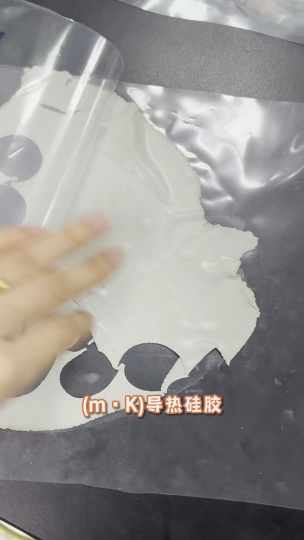
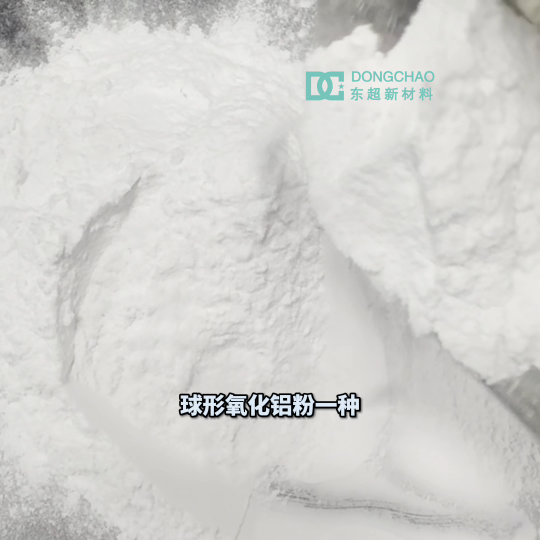
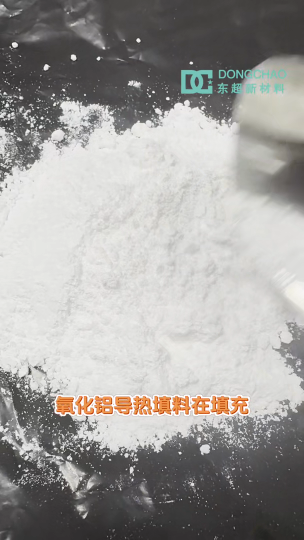
導熱氧化鋁粉用在動力電池中的作用
導熱氧化鋁陶瓷基板:推動5G技術發展的關鍵材料
氧化鋁導熱粉在新能源汽車上的應用
半導體劃片機助力氧化鋁陶瓷片切割:科技與工藝的完美結合
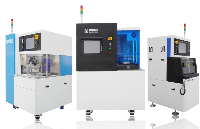
評論