自動駕駛的角度來看,說到近兩年哪一個主題最熱門,肯定離不開激光雷達。2021年被譽為激光雷達量產之年,不少車企都公布了裝備“車規級”激光雷達車型量產日期。然而何為“車規級”激光雷達?
激光雷達產業人士還廣泛認為激光雷達車規在這個階段誰都說不清楚。多數人都認為,只要產品通過車企相關標準且能獲得定點車型就能稱得上是“車規級”車型。但是每個車企有不同的標準,通過這個車企的標準你能通過別的車企嗎?一切都是未知數。
小編搜了一下眾多媒體的報道才知道,現在全行業對于激光雷達車規標準還沒有一個統一的回答!做為汽車電子行業的老將,最看不得這眾說紛紜,未達到底的局面了,今天小編就把這個問題掰開來好好講一下。
眾說紛紜的激光雷達車規級標準
在談到車規級標準前,首先要看看這兩個激光雷達供應商各自的宣傳口徑和各自對產品車規級的界定。
A廠商關于激光雷達可靠性的描述:
隨機性硬件失效指標<10-7/h,可完全滿足ASIL-B和SIL-2功能安全等級;
車規級系列測試包括加速度28m/s2的振動測試、-40℃的低溫和85℃的高溫測試、鹽霧測試、跌落測試、靜電放電測試、輻射抗干擾測試和工頻磁場測試等等。
B廠商的描述:
采用APQP作為項目管理工具,全面執行IATF16949質量管理體系、ISO26262功能安全標準;
從架構開始就要按照車規級可靠性設計、所有器件均按照車規級相關標準要求選型;
按照ISO及AEC-Q等國際標準以及多家頂級OEM客戶要求,進行可靠性測試;
試驗內容涉及但不僅限于高壓水沖擊,碎石沖擊,高低溫沖擊,太陽輻射,EMC,化學防腐,鹽霧,高低溫濕熱試驗。
做過汽車電子的小伙伴們看到這些宣傳術語肯定會覺得“哪里不對勁”。
我們先把上面兩家激光雷達廠家宣傳的所謂“車規級”的點給匯總一下看:
整成表格(如上圖)這樣看起來是不是就清晰多了。事實上,總體來看,這幾個宣傳口號首先提到的是功能安全問題,然后堆砌了幾個汽車零部件的測試項目并最終寫出了APQP、PPAP和IATF16949就完了。透過這張表格,各位小伙伴是否找到了某些廠商的宣傳套路呢?上來就先定調一下,把自己的產品說成“車規級”,再把術語堆出來送給大家,和你講ISO26262,什么ASIL B,什么ISO/AEC。
好啦,該為你普及汽車行業的那些“內幕”,你拿出所有的小本子,動手記筆記。
1.功能安全,這個和車規級幾乎沒啥關系,就是這幾年比較火,拿出來刷下存在感。
2.AECQ是業內對電子元器件的車規級標準;
3.ISO16750是針對汽車電子零部件的ISO標準;
4.DV指設計驗證(Design Validation),是主要用于檢驗汽車電子零部件產品硬件設計質量的一種測試手段,DV的測試項目及等級依據OEM企業標準(沒企標的按國標或ISO標準)進行,產品通過試驗后才能進入量產階段;
5.PV指產品驗證(Product Validation),是用于檢驗產品量產質量的一種測試手段,一般測試項目來自于DV,但較DV要少得多,側重于檢驗產品大批量生產的質量穩定性及一致性,產品量產后可每半年或一年就進行一次,具體根據OEM的要求;
6.DV測試要求必須是模具件,也就是“硬模件”,3D樣件或“軟模件”是不行的;PV測試要求OTS(Off tooling samples)樣件,即工裝樣件,手工件是不行的;目前汽車電子行業存在較多的DV/PV combined,也就是說兩個試驗合并一起做的意思,這樣可以節省時間,降低成本;
7.至于APQP,PPAP,IATF16949,這些都是行業慣用流程與準則,不可能說與車規級關系不大,但是只要從事汽車電子產品的制造,人人具備,不經過外審也過得去。所以非專業的小伙伴們記住了,以后誰再提這個就是耍流氓;——這就像你去買煙酒,他就必須有煙酒專賣許可,沒有就賣不了是一樣的。
定義車規級激光雷達標準
“車規級”這個詞是針對汽車電子“元器件”而言的,而汽車電子“零部件”并無所謂的“車規級”。
注:元器件(Components)是部件(Parts)的一種,一般特指電子部件(Electronics Components),是部件的最小單元;而零部件則是指可以拆分的,由各部件組成的一個總成(Assembly)。簡單來講,電子零部件是由電子元器件(電阻、電容、芯片等)及結構件(PCB、連接器、殼體、螺絲等)共同組成,元器件不可拆分,零部件是一個總成,可拆分。
在過去,行業內根本沒人把汽車電子零部件稱為“車規級”。只是到了最近幾年,在自動駕駛技術和芯片國產化日新月異的背景下,“車規級”這兩個字剛剛進入公眾的視線,可起初卻被一些廠商帶斜了眼,外行人紛紛跟在后面瞎扯。
但另一方面,由于“車規級”一詞的火爆,意味著行業需要它、廠商需要表現出產品競爭差異化、消費者想買得放心、用得安心。為此,小編主動請纓,根據近二十年的汽車電子行業經驗,嘗試定義激光雷達產品的“車規級”,其他車載電子產品也可以借鑒:
(1)產品采用的所有電子元器件均為車規級(AEC-Q*** Qualified);
(2)產品滿足汽車電子設計開發要求;
(3)產品滿足大型車企的測試要求;
(4)產品實現批量前裝(量小的車型不算,半前裝或后裝都不算);
必須同時滿足以上四條標準,小編認為其才算真正達到了“車規級”要求。
下面分開解釋一下:
(1)器件車規級,這是最基本的可靠性要求。
(2)汽車電子設計開發要求,這個很重要,但是小編好像沒有見過哪個激光雷達供應商提過這一點。汽車行業里面的朋友也許已經習以為常,但是小編接觸到一些來自非汽車行業的工程師之后卻深有感觸,自己的設計思想與汽車行業的需求相差太遠,這就請大家后續細說。
(3)為什么是大型車企?小編在此說明。汽車電子零部件的檢測標準,有國標也有相應的國際標準,小車廠根本沒有自己的企標(或者直接照抄國標),大的車企會要求按照自己的企業標準來執行。國內車企通常參照國標(國標借鑒了國際標準)或者其合資伙伴(以一汽為例,許多標準都借鑒了馬自達),外資大廠均有自己的標準,有些測試項目在ISO/IEC標準中并不存在,如福特,大眾等相當一部分比ISO/IEC高。從整體上看,大型車企在檢測方面需要更加科學規范,小型車企就遜色了很多。
(4)一定要大批量前裝,后裝不算,前裝量小了也不算。有的車型預計到停產也賣不到幾萬輛,那激光雷達在該車型上的應用案例就沒有參考價值,給你用,你也不敢大批量上前裝。
激光雷達做為與安全有關的汽車電子零部件之一,也是一個新生事物,它要同時符合上述4條標準,小編覺得它確實符合車規級。
第四條其實很好理解,對于激光雷達這類安全相關的汽車電子產品,小編覺得,如果你對前3條不能滿足,它的可靠性與一致性以及都沒有背書的話,車企一定會懷疑它的可靠性,那基本上也不會有車企敢把它用于預計年生產十萬輛以上的量產車型,由于后期事故處理,召回成本和名譽損失車企都會難以承受。
下面,小編著重分析一下前兩條。
一、車規級電子元器件
電子元器件車規級標準無疑是AEC組織所制定的系列標準之一,它的本意在于促進汽車電子器件通用化。
AEC標準極大地促進了汽車電子器件的資格通用化,降低了零部件公司及OEM的器件選擇、使用及變更成本,極大地提高了電子零部件及車輛的可靠性,提高了電子器件的通用化水平。我們再來復習下AEC標準及其范圍:
AEC標準及其范圍(來源:左成鋼)
對于汽車電子產品來講,AEC標準幾乎覆蓋率了全部的電子元器件,但有些器件依然不在AEC-Q范圍內,如純機械結構類:開關、連接器、電線、PCB等,機電器件:電機、電磁閥、繼電器等,但這些產品都有其相應的行業標準,在此略過不談。
下面就激光雷達產品做一個分解,看看里面電子元器件能應用什么標準:
激光雷達電子元器件分析(來源:左成鋼)
從上面表格我們可以看出來,除了AEC-Q102是新標準以外,其他都是已有的標準,而AEC-Q102就是專門針對激光雷達的核心器件激光器和光電探測器而制定的新標準。
1.讓激光雷達有法可依的AEC-Q102標準
AEC目前一共有6個標準,小編整理成了表格,如下:
AEC標準匯總(整理:左成鋼)
可以看到,Q100和Q200都是近十年或十幾年沒更新了,而Q101和Q102是這兩年才更新的,其中很關鍵的一個更新就是增加了激光器件,讓激光雷達“有法可依”了。
原來的光電器件比如光電二極管、LED都是涵蓋在《AEC-Q101分立半導體元件的應力測試標準》中的,Q101在版本從D更新到E后,光電半導體全部轉到了新的AEC-Q102標準中去。
AEC-Q101 REV D規定的器件范圍(來源:aecouncil.com)
AEC-Q101 REV E規定的器件范圍(來源:aecouncil.com)
然后再對比一下AEC-Q102的范圍,專門增加了激光器件Laser components:
AEC-Q102 REV A規定的器件范圍(來源:aecouncil.com)
熟悉AEC標準的小伙伴們應該了解,耐久類測試要求起步通常是1000小時,但在AEC-Q102中,除常規測試項目外還專門規定了一個可靠性驗證Reliability Validation項目,時間從最低1000小時到最高10000小時。
大家估計對10000小時沒有直觀概念,這么說吧,一年只有8760小時,而AEC-Q102要求超長壽命的Laser器件HTOL(High Temperature Operating Life高溫使用壽命)測試時間要達到10000小時。
AEC-Q102 REV A中對可靠性驗證的規定(來源:aecouncil.com)
即對于激光雷達車外安裝的應用場景來說,超長壽命需要激光器件高溫耐久測試1萬小時。所以如果以后哪家激光雷達供應商很傲嬌的說他們家的產品經過了4000小時的測試,你就把這個標準懟到他臉上,說“最高級別為10000小時”。
當然10000小時還很嚴格,下面我們就來科普下汽車電子零部件常年的溫度分布情況吧,由此可見最高溫或最低溫約占1/4,而且這段時間并不具有持續性。
汽車電子零部件全年溫度分布(來源:英飛凌)
再參考一下我們之前多次提過的乘用車生命周期維度,車輛生命周期內的總運行時間大約是10000小時(按每天2小時計算),綜合來看,零部件承受最高溫度的時間約在1/4也就是2500小時左右,所以高溫10000小時耐久測試是非常嚴苛的了,可以滿足用戶每天8小時、全年無休地開15年。
整車生命周期維度對比(來源:英飛凌)
我們來看兩個已通過AEC-Q102認證的器件信息,大家感受一下:
歐司朗2019年9推出了一顆應用于激光雷達的激光器件SPL S1L90A_3,我們看下它的datasheet信息,量產時間是2022年2月,晚了兩年多。
歐司朗SPL S1L90A_3激光器手冊(來源:osram.com)
激光雷達的內核除激光器外,實際上還包括激光探測系統中所使用的光電探測器。激光射出,反射回又有誰能收到呢?光電探測器Photomultipliers將在此使用(SiPM)。讓我們來看看符合AEC-Q102要求的光電探測器是什么樣子的。
2. AEC標準對器件可靠性的支撐
我們又看了一下AEC標準中關于器件失效率方面的規定。眾所周知,汽車是由數以萬計的零部件和電子模塊構成的,例如ECU就是作為零部件使用的。那么,你是否知道,一只ECU由幾個電子元器件構成?答案也許讓人始料未及,也許有成千上萬種之多。
1ppm缺陷對一百萬量車意味著什么(來源:MPS)
所以,如果一個器件有1ppm(百萬分之一)的缺陷,對于一百萬輛車按WCCA(最差情況分析)來講,就有一千輛車的ECU存在的缺陷,是不是很恐怖?要知道一輛車上可是有50個以上的ECU的。
下面我們就來看看AEC標準如何求解器件可靠性。電子元器件在車型全生命周期和車輛全生命周期中要實現高可靠性,涉及到許多要點,但是歸納如下:
1.器件本身質量的高可靠性是器件長使用壽命的基礎;
2.器件長達15年以上的供貨周期中,器件批次間品質的一致性,是實現器件長生命周期的保證;
3.器件生命長周期內的變更及重新認證,是解決器件一致性及可靠性的重要手段;
4.IATF16949、AEC-Q、PPAP等標準及流程體系對產品設計及制造的支撐功不可沒;
以上4點共同構成了汽車電子產業鏈對車型及整車長生命周期可靠性要求的支撐,我們分開來講。
先來看可靠性方面,浴盆曲線通常作為一個可視化的模型,大家都很熟悉了,我就不再贅述,針對器件的早期失效率ELFR(Early life failure rate)及正常生命周期失效率問題,AEC標準都有相應要求。
比如IC類器件,AEC-Q100-008 ELFR就有詳細規定。
AEC-Q100-008 ELFR早期失效率(來源:aecouncil.com)
如果測試中有失效的情況,測試就不能通過,且必須通知用戶,并告知即將執行的糾正和預防措施。在客戶批準,且糾正和預防措施被正確實施的情況下,器件才可以被認為具備了再次進行AEC-Q認證的資格。
大家感受一下,標準要求是不是很嚴苛?我們再來看下英飛凌是怎么處理ELFR問題的:
Zero defect mindset零缺陷理念(來源:英飛凌)
由英飛凌“零缺陷的概念”這張圖片可以看出,AEC標準在浴盆曲線中把早期失效那一條拉得筆直,即AEC標準杜絕電子元器件早期失效。
解決了ELFR問題后,那么中后期失效問題怎么解決呢?答案是:壽命測試、現場數據和壽命分布分析,數據從怎么來呢?這不,瞌睡了AEC就送枕頭來了,這個就是標準里的generic data(通用數據)。為了講清楚這個問題,我們來看下ACE-Q100里面對通用數據的描述。
AEC-Q100通用數據時間線(來源:aecouncil.com)
通俗地說,通用數據是設備的海量數據,它覆蓋設備從設計,驗證,批量生產,應用,更改到再驗證等生命周期維度。認證數據加上變更認證數據和可靠性監控數據一起構成“通用數據。因此,可利用的通用數據是對設備可靠性的證明,它覆蓋浴盆曲線中前期階段,能夠支持并證明設備生命周期中(從生產到劣化周期)可靠性與失效率。通用數據的部分比較豐富,囿于篇幅,建議您仍應閱讀原文,這里就不做詳細介紹。
講清楚了器件本身的可靠性問題,我們再來看下器件長期的一致性問題,這個非常重要。汽車作為大批量的工業品,以中國為例,僅2021年產量就超過了2000萬臺,銷量超過10萬輛的乘用車共有62款。乘用車車型生命周期一般在3~5年,更長的比如大眾高爾夫和豐田卡羅拉,車型生命周期都能達到幾十年。
在這漫長的數十年車型生命周期中,汽車不斷更新換代,汽車上ECU不斷翻新,相應的電子元器件自然也不斷翻新。例如改變晶圓產地、更新生產工藝、替換邦線材料等等,AEC標準如何確保器件長期一致性?
我們以針對芯片的AEC-Q100標準來舉例看一下。
如果器件發生了變更,那么就需要重新進行認證測試,這部分內容AEC-Q100規定得特別詳細,限于篇幅,標準原文就不放了,我在這里挑重點給大家解讀一下:
有變化就需要重新進行認證,不管是產品還是制程變化;
供應商的變更需要滿足客戶使用需求;
即使最微小的變更,也需要根據標準規定進行相應的認證測試;
如果測試失敗,必須找到根本原因(root cause),并在執行了相應的糾正和預防措施的情況下,器件才可以被認為具備了再次進行AEC-Q認證的條件。
從整體上看,無論出于何種原因,只要器件發生了變化,無論是產品還是過程,凡是可能對其物理特性,用途,功能,品質和可靠性產生影響的都會發生改變的(3F原則:Fit,Form,Function),都必須重新進行認證測試。AEC-Q100中專門為器件變更的測試項目給出了指導原則:
AEC-Q100對器件變更的測試項指導原則(來源:aecouncil.com)
以上就是測試項目,另外小編還為大家準備了一個極其復雜的多維表Table 3,規定了哪些更改需要做哪些測試,這里就不多說了。
我們以更換晶圓廠(FAB Site Transfer)來舉個例子。如果芯片的晶圓工廠換了個地方,重新認證要做哪些測試:
16項必做測試,包括溫濕度,溫度循環,邦線相關、電遷移、ESD等;
4項選做測試,比如H就是針對密封性。
注意,這里說的是換晶圓工廠的情況。當然了,如果封裝工廠換地方了,同樣需要再次做認證測試,但是認證的項目會少一些。
我們最后做個總結:
對激光雷達而言,除核心器件激光器和探測器需要通過AEC-Q102認證外,所有電子元器件都要通過AEC-Q認證,這個激光雷達才有了車載應用的基礎,才有了整體去過零部件試驗及滿足車輛長達15年嚴苛應用的可靠性基礎,自動駕駛車輛的安全才有保障。
2.汽車電子零部件的設計開發要求
汽車電子產品設計與研發需要的是業內人士、如水、如魚、如空氣、久而久之便養成一種習慣,繼而“無感”,而當小編接觸到一些來自非汽車行業的工程師時,發現除了航天軍工以外,汽車電子對于產品設計的需求應該都是各行業中最高的了,一個也不能少!在此不予受理駁斥,小編從多個層面進行分析,大家自然會理解。
行業特點不同維度對比(來源:左成鋼)
對比完大家就能發現,放到航天軍工之外的各行各業,應該沒有比汽車電子更高的,這里不單指一個技術點,而是綜合所有維度來看。
下面我就簡單列舉一下汽車電子產品設計的一些基本要求,小伙伴們感受一下:
耐溫要求
(1)汽車使用環境的溫度范圍從最熱的沙漠到最冷的極地,汽車電子也需要在各種狀況下正常工作。
(2)汽車研究表明,汽車的駕駛艙工作溫度范圍要從-40度到+85度。
(3)發動機艙從-40度到+125度,某些低溫區域也要求做到105度。
耐濕度及防水要求
(1)相對濕度一般從10%到100%;
(2)汽車電子要求在所有的濕度范圍能夠工作;
(3)高相對濕度會導致水汽進入某些電子器件內部導致損壞;
(4)某些電子產品要求完全防水,即使高壓水槍沖洗,或浸入水中,亦能正常工作。
耐灰塵、污垢及鹽霧
防塵和防水不是一個概念,這里給大家科普一下,規定防護等級的國際標準IP代碼(IP code)分兩部分,前一位代表防異物,包括防塵;第二位代表防水。比如常說的最高防護等級IP69(IP6K9K,9K及帶K的都是ISO20653標準,國標和IEC沒有K,也沒有9K這個等級),6代表防塵,9代表能承受高壓噴水。
耐機械振動、沖擊
這句話更容易讓人明白,小編附帶說個插曲,說是某個自動駕駛礦卡生產企業把激光雷達安裝到汽車上做試驗,沒想到用不了多久全壞掉了,最終發現,是激光雷達抗振動沖擊性能不合格。
我拿國內某乘用車OEM的振動測試標準舉個例子,標準從輕度、中度、劇烈到極度劇烈,共分了9個等級,極度劇烈的最高加速度為294 m/s2,近30個G,喜歡看空戰片的小伙伴們應該了解戰斗機飛行員最大可以承受10個G的加速度,30個G是什么概念,大家感受一下。
嚴苛的電氣環境
(1)電壓:12V系統:9V-16V,24V系統:16-32V
(2)反壓:12V系統:-14V,24V系統:-28V
(3)瞬斷:12V系統:4.5V/100ms,24V系統:9V/100ms
(4)跳線啟動:12V系統:24V/1min.
(5)啟動波形:12V系統:3V/4.5V,24V系統:6V/8V
(6)拋負載:12V系統:87V/400ms,24V系統:174V/350ms
(7)傳導抗擾:12V系統:+150V/-150V,24V系統:+300V/-600V
(8)電磁輻射抗干擾及大電流注入抗干擾
(BCI),頻率從KHz級別到GHz級別,電場強度高達200V/m。
(9)靜電(ESD):高達25KV
汽車電子產品電氣環境(來源:英飛凌)
假如您是從事汽車電子產品有關工作的工程師,您認為這種設計有多困難?如果接觸過非汽車行業工程師的話,想必你們一定會驕傲嬌氣,將來就算不干汽車行業,但要說汽車這個行業經歷到別的行業就是“碾壓式”存在,要說“降維打擊”也很輕巧。
1.汽車電子對產品確認的極高要求
我們先來看下業內人士都聽過的汽車電子產品開發的V模型,感受下汽車電子產品開發的高要求:
簡化的V模型(來源:左成鋼)
我用老百姓聽得懂的一句話來說明汽車電子產品設計區別于一般電子產品的關鍵點在于:汽車電子產品不只是按照設計要求進行設計,還必須按照設計要求進行真正的檢驗,以證實是否符合設計要求。
它的含義是什么?也就是說,其他行業基本上只要求過程驗證,而汽車行業的要求是過程驗證+產品確認。形象地說,甲方若要求建一座抗8級地震建筑,根據建筑行業的規定,只需按抗8級地震施工,工序無誤即可接受;但是根據汽車行業的規定,建筑完工后要模擬8級的大地震,建筑沒有壞才算是符合要求。因此,才會發現車廠取了不少車進行碰撞測試,這個就是確認(Validation)。
2.要求極高的汽車電子設計分析過程
接下來,我們通過一個業內常用的計算分析方法,管中窺豹,來感受下汽車電子產品對設計分析的高要求。汽車電子產品開發過程中有一個WCCA(最差情況分析Worst Case Circuit Analysis)環節,這是業內很通用的一種設計分析方法,大名鼎鼎的NASA也在使用,非汽車行業的小伙伴們可以打聽下看你們行業有沒有用,筆者接觸下來似乎行業外的人都沒聽說過WCCA。
簡單舉個例子,大家感受下這種分析方法的特點。
我取了個電阻分析,初中物理沒有還體育老師,應該能看得清。根據參數的不同,電阻可簡單地劃分為阻值,精度,功率和封裝4個維度。我們比較一下不同產業在設計上的側重:
其他行業:阻值正確,精度夠用,功率沒問題,封裝大小合適,挑便宜的直接用就行了,其他不管。
汽車行業:除其他行業那些基本要求外,還需要考慮:
(1)精度隨溫度、濕度范圍的變化因素,比如1%精度,高溫時可能就不是1%了,遇到高濕可能就廢掉了;
(2)精度隨時間的變化因素,就是老化因素,比如在長達15年的生命周期內,精度可能就偏移到3%了(WCCA中1%精度按3%進行計算,就是考慮到了老化)。
(3)功率隨溫度變化產生的降額,比如超過70度,功率需要按1.25%每度進行降額使用。
(4)功率根據電流脈沖需要考慮的額度調整,比如脈沖關斷時間在4μs~100us之間,占空比≤700時,就需要按公式進行計算,公式太復雜,我就不放了。
(5)涉及到外部信號檢測的電路,還需要根據CSPR25標準,進行不同電壓脈沖的耐壓及功率計算;
在此僅就電阻而言,具體地說就是電阻所構成的電路和它所發揮的作用,同時還要考慮較多層面的因素,如檢測電路要考慮檢測電壓波動幅度,開關阻抗模型、接口電路漏電流、車身搭鐵地漂移等(GND offset)等。
小伙伴們看到這里的心情如何呢?大家都知道ECU中電阻的個數通常用幾百來算,電阻正是電子元器件中最簡單的元件之一,其他元件參數維度就更多了。小編了解到的一個歐洲電子模塊項目,WCCA工作在國內做,2個人專職做了3年才做完,文檔數量達到了幾萬個,近10個G,你感受下這個工作量。
因此,汽車電子零部件高可靠性在一定意義上說就是被設計好了,而過程驗證與最終證實只是手段。
最后得出如下結論:汽車電子零部件在設計和研制過程中的高度需求,是確保汽車全生命周期可靠性的決定因素。
3.汽車電子零部件的測試要求
前面講了到激光雷達核心器件需使用符合AEC-Q102標準的激光器和光電探測器,除這些器件外所有電子元器件都要符合各自相應的AEC標準要求,否則,即使激光雷達產品自身已經通過汽車行業零部件標準測試的相應要求,但在汽車年產量數十萬輛和車輛長達15年的苛刻應用中,激光雷達在一致性和長期可靠性方面可能仍達不到汽車行業要求
接下來我們詳細講一下汽車行業對汽車電子零部件的試驗要求,首先我們先來看下相關的行業標準。
汽車行業電子零部件相關標準(來源:左成鋼)
試驗標準涵蓋了電氣性能、EMC(電磁兼容)、ESD(靜電)、機械性能(振動、沖擊、跌落)、氣候(溫濕度類耐久、交變、沖擊)、環境(化學品、鹽霧、陽光)、防護等級等,所有的電子零部件試驗要求全部都是按這些維度進行分類進行的,業內對電子零部件的試驗要求一般稱為DVP(設計驗證計劃Design Validation Plan),我舉個例子大家感受下:
某ECU 設計驗證計劃DVP的一部分(來源:左成鋼)
圖中測試分為6組,每組2個樣品,測試項目共計44個。而這僅僅是機械、溫度類測試計劃,還不包含電性能及EMC類,大家應該能感受到這個測試的復雜度和難度了吧。
按照小編的經驗,零部件DV測試一般耗時半年以上,即使最順利的情況下也要3個月以上,如果有問題還要反復整改調試,甚至更改設計,那時間就沒譜了(改硬件1個月以上,模具可能要2個月以上)。比如EMC測試,有些項目可能要花上一兩天時間,如果出現了問題也許一星期也搞不定,試驗室按小時計費,通常1小時1000元左右。此外,復雜產品自動化DV測試臺架價格極高,可能往往要幾十到幾百萬臺,而且往往一下子要做兩臺才能縮短測試周期,使很多測試能夠并行進行,但費用昂貴。
一汽、大眾、福特、GM、Volvo EMC標準舉例(來源:左成鋼)
我們再來聊下各個OEM的企標。前面講過,各大OEM都是要求Tier 1采用自家標準及等級進行產品測試的,而非直接按照ISO/IEC標準來,所以一般Tier 1是沒有自己家獨有的測試標準的。
從整體上看,各標準對測試項目的名稱,分類,分組,測試順序和要求等級的規定還相差不小,有些測試項目甚至為ISO/IEC標準中所沒有,如福特標準、大眾相當一部分標準超過ISO/IEC,一些三方試驗室如無專用設備部分試驗項目無法測量。各家標準比較這件事就復雜多了,寫到這估計你都看不過去了,這里就省略不說了。
1.福特認可大眾的測試標準嗎?
有一個問題不知各位小伙伴有沒有想過,AEC標準最初的目的就是器件資格通用化,大大減少了OEM器件的選擇、使用和更改費用,AEC標準從此真正在業界通用電子器件資格。那么,電子零部件怎么辦?假如一款ECU達到大眾測試標準福特能否承認?就作者的體會來說基本上是不行的。
這其中涉及兩個問題,一是ECU本身的非通用化設計,每家Tier 1的ECU都是給OEM定制的,這就決定了其很難通用,那么有通用的案例嗎?有,小編見過某Tier 1給某OEM定制開發的一個ECU,后來就用到了另一個OEM的項目上。這就要說第二個問題了,就是各OEM之間的零部件資格通用化問題,上面講過,因為各OEM企標不同,零部件資格通用化問題基本上是無解的,大眾不可能認可福特,通用也不認可現代,只有一種情況可能可以,就是小OEM認可大OEM的標準,或者Tier 1擁有話語權且通用性很高的ECU,比如網關、安全氣囊控制器等,Tier 1就可以一魚多吃。
至于為什么OEM之間電子零部件不能通用化,這個其實也很好理解。我們拿整車電源環境來舉例,比如不同OEM的車,其整車電壓環境可能就存在差異,福特針對地漂(Ground offset)測試就和ISO16750-2標準要求差異較大,福特要求在GND上加脈沖,而ISO16750-2只要求加固定幅度的電壓偏移即可。
福特地漂測試要求(來源:福特電氣測試標準)
印度由于電網電壓不穩等原因,到目前居民家里仍需安裝穩壓器,以確保家電安全使用,不然空調和電視都有被燒毀的危險。換成汽車道理亦是如此,有些汽車電源環境較好,OEM測試要求不一定有對應電壓脈沖測試項目,與之對應,Tier 1在ECU端的“穩壓器”上并不加裝,也就是業內講的TVS(瞬變電壓抑制二極管Transient Voltage Suppressors)器件,以降低成本。但是若將該ECU直接安裝在其他OEM的模型中,對方汽車電源環境又不是很好時,ECU可能會受損。
那么小伙伴們是否發現電子元器件更容易實現資格通用化呢,而且零部件涉及具體應用與費用,對于不同應用會有不一樣的設計方案與測試標準呢,因此,電子零部件在不同OEM間實現資格通用化是非常困難。當然并非絕對不可能,通用化產品是沒有問題的,但是通用化產品需要在產品設計上存在一些設計冗余和性能增強,這些都會牽涉到成本問題,大家省略不提,反正魚和熊掌是不能兼得的。
2.拋開等級談測試就是耍流氓
我們再談一下具體測試項目中相應測試等級的問題,這個沒做過產品測試的小伙伴們可能不了解,吃瓜群眾就更不清楚了。其實每項測試里面都是有相應的測試等級及產品功能狀態等級要求的,我們就拿常用的ISO16750來講,對于12V系統,供電電壓就分了四個等級,從A到D。產品的功能狀態又分了5級,從A到E。
ISO16750測試要求(來源:ISO16750-1,2)
我大概解釋一下:
A級:試驗過程中及做完都正常,等級最高;
B級:試驗過程中有偏差;
C級:試驗過程中不滿足要求,結束后自動回復正常;
D級:試驗過程中不滿足要求,結束后需重啟;
E級:試驗過程中不滿足要求,結束后損壞;
小伙伴看到了什么感覺呢?難道撇開等級來談論實驗就等于耍流氓嗎?正如我們常說的水喝多了也能毒死人,撇開用量不說毒性是耍流氓。我們再回到一開始那個激光雷達廠商所說的其產品已經過加速度為28m/s2振動測試那么我們就按照一個OEM測試標準來看看這個測試參數到底屬于什么級別。
國內某OEM的振動測試標準-部分(來源:左成鋼)
這家OEM標準中的振動測試從輕度、中度、劇烈到極度劇烈,共分了9個等級,極度劇烈的最高加速度為294 m/s2,還有9個測試維度,包含安裝方式、頻率、加速度、掃頻類型等,而A廠家僅提到了一個28m/s2的加速度,是高還是低,測完以后樣品啥狀態?一句話都沒提,這就等于啥也沒說啊。
AEC-Q102標準在激光雷達的應用進度
以上我們就來說說對于激光雷達器件級車規標準和零部件級行業標準吧,下面就讓我們來看看AEC標準是如何運用到激光雷達中的以及車規級激光雷達上車速度。
如前所述,AEC-Q102于2020年4月6日正式推出,此前并未對Laser器件制定AEC標準。那么,問題就來了,此前公布的聲稱已經實現“車規級”或“車規級”激光雷達?我們對此進行了分析。
歐司朗作為全球光電器件的巨頭,在2019年9月宣布了其符合AEC-Q102的四通道激光器。注意,這是宣布,離實際量產能用,還有很長的時間。這一點沒做過工程設計的小伙伴們可能不太有感覺,就比如新聞上發布了某項新技術,大家就認為馬上就能用上了,其實上還差得遠呢。這中間大概的關系是這樣的:實驗室—Tier2企業à—Tier1企業—OEM—用戶,大家可以看到,從實驗室到用戶,中間還隔著很多道,其中可能還有Tier n企業,產業鏈很長且很復雜。
司朗宣布世界上首款符合AEC-Q102的四通道激光器(來源:osram.com)
根據上圖及器件datasheet可以提取到幾個關鍵信息:
(1)此激光器可以用于激光雷達;
(2)器件通過了AEC-Q102認證;
(3)SPL S1L90A_3器件手冊初版發布時間是2022年2月。
做過汽車電子產品的朋友應該都知道以上資料的含義了吧,筆者在此不妨科普下,帶領您學習汽車電子產品的設計流程。
做過汽車電子產品的朋友應該都知道以上資料的含義了吧,筆者在此不妨科普下,帶領您學習汽車電子產品的設計流程。另一種是為減少BOM的費用,畢竟新鮮的產品剛剛量產就已經很昂貴了,由于沒有上量,所以費用還是不能減少。
接下來我就從一顆芯片開始,講一下一個新技術從發布到量產的流程。
芯片供應商Tier 2制定芯片規劃(Roadmap),各Tier 1及OEM調研;
芯片供應商確定芯片開發時間;
Tier 2提供免費工程樣片,Tier 1預演(advance)項目設計導入;
Tier 2提供量產芯片,Tier 1采用量產芯片進行DV(Design Validation設計驗證);
采用新器件的Tier 1的項目SOP,產品量產;
OEM采用此Tier 1產品的車型量產。
新器件導入項目流程(來源:左成鋼)
從以上新器件導入流程中可以看出,一個新器件批量生產需要1年多的時間,而Tier 1的設計也要1年,這幾乎需要2年或者3年的時間,這個速度已經算比較快了,大家都知道普通汽車電子零部件中,一個工程從立項到SOP大約需要3年。若以芯片供應商的推廣為起點,其間少說也要3年。從歐司朗的那顆激光器量產時間我們也能看出來,器件從發布到量產,期間經過了2年零5個月的時間,并且器件發布時間還稍早于AEC-Q102標準發布時間。
那么能不能再快一點呢?可以!
芯片在工程樣片階段就導入量產項目,如圖中紅色虛線箭頭所示,跳過驗證階段。待芯片一量產,馬上進入DV,少則三個月,多則半年就可以達到臨近SOP狀態(指產品硬件凍結,軟件大概率還在更新)。
那么,這可以做到什么程度的快捷?這要看芯片供應商以及項目本身,如果進展順利,可能1年SOP,但是真的沒有多少人看到這樣玩過,特別是安全功能零部件方面,OEM都敢做,Tier 1大概都不敢做,因為出現問題都會承擔責任。
我們來總結一下:
1.AEC-Q102正式發布時間是2020年4月6日;
2.全球第一款滿足AEC-Q102的激光器件量產時間在2022年2月;
3.激光器件上車大概需要1~2年的時間;
總結
最后我們做個總結:
1. 汽車電子零部件目前沒有統一的行業資格認可。
2.在小編看來,車規級激光雷達需同時達到的4項標準分別為:裝置全車規,符合行業設計開發需求,符合大型車企試驗標準,做到批量前裝;
3. 器件全車規是車型及整車長生命周期可靠性及一致性的基礎;
4. 對汽車電子設計提出了更高的要求,這是確保汽車全生命周期可靠運行的一個決定因素;
5. 滿足車企測試標準是達到車載應用可靠性要求的基礎;
6. 實現批量前裝是對激光雷達可靠性及一致性的背書;
7. 車規級激光器件從發布到量產需要2年左右的時間;
8. 車規級激光雷達從車規級器件量產到激光雷達量產需要1~2年的時間;
-
激光雷達
+關注
關注
967文章
3943瀏覽量
189625 -
自動駕駛
+關注
關注
783文章
13694瀏覽量
166165
發布評論請先 登錄
相關推薦
激光雷達企業圖達通與宇稱電子攜手合作,打造車規級ASIC芯片
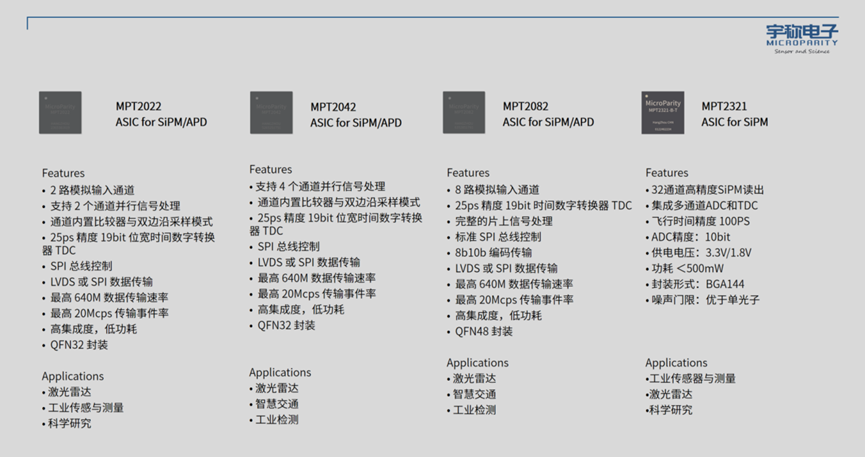
車規級振蕩器為激光雷達提供解決方案
九識智能發布新款無人車Z5 2024,搭載禾賽AT128激光雷達
亮道智能:發布全新一代激光雷達,未來主攻固態激光雷達低價市場
速騰聚創車規級激光雷達銷量領跑全球
行業首款256線高性能車規級激光雷達產自廣州,3分鐘下線一臺激光雷達
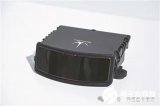
廣州推出首款256線高性能車規級激光雷達
汽車激光雷達:競爭格局和技術演進
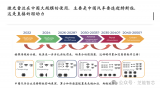
速騰聚創發布首款超長距激光雷達M3
探維科技:引領智能駕駛激光雷達技術的突破與創新
英諾賽科發布100V車規級GaN推進汽車激光雷達市場
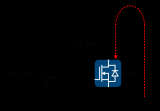
禾賽科技激光雷達累計交付突破30萬臺 全球首個創下此里程碑的車載激光雷達公司
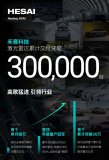
評論