摘要:分析結果表明:新能源和無人駕駛汽車快速發展使得車規芯片發揮著越來越重要的作用,也是車規芯片產業應用中的一個重要方向。對集成電路設計公司入駐車規芯片相關驗證流程和規范標準、車規芯片相關可靠性驗證、失效分析等方面進行了說明,并對車規芯片量產化過程中實現零缺陷這一目標進行了討論,分析了國產車規芯片在研制過程中所面臨的問題及其局限性,并對其研制方向進行了預測。
引言
隨著汽車電子的深入發展,以及汽車行業確立的新四化(電動化、網聯化、智能化、共享化)發展方向,這給半導體芯片在汽車領域的應用帶來新的機遇。近年來需求更有快速發展,為汽車市場帶來了新一輪產業變革。使車規芯片無論在電源控制,底盤控制,還是信息娛樂應用領域都發揮著越來越大的作用[1]。在過去5年中,全球汽車半導體市場復合增長率每年在4.8%左右,中國汽車半導體市場復合增長率更高達11.6%。其主要原因是新能源汽車電子化程度的不斷提高導致了對各種汽車半導體的需求量急劇增加[2]。據德勤預測,汽車半導體收入將在2022年突破600億美元[3],勢必會吸引更多芯片廠商參與其中。
相比消費類電子芯片,車規芯片要求更加苛刻,
(1)車規芯片是高于消費類以及工業芯片標準;
(2)車規芯片對于工作環境有著更為苛刻的要求,比如,溫度、濕度、EMC、有害氣體侵蝕等等,針對它們的不同用途有著不同的要求;
(3)車規芯片開發驗證花費多,門檻高,周期長;
(4)需要通過相應的審核標準。
車規芯片有兩個條件,
(1)符合零失效的供應鏈質量管理標準IATF 16949規范;
(2)滿足由北美汽車產業所推的AEC可靠性標準。
受車規芯片設計周期長、技術壁壘高等因素影響,汽車芯片行業整體表現為國外巨頭獨占鰲頭,比如以高端車規芯片為核心細分市場的英飛凌、瑞薩。與此同時,全國各地也出現數十家芯片設計公司作為汽車電子芯片提供商,種類涉及輔助駕駛,中控,電池管理,圖像傳感器及信號處理器[4]。
國際上傳統車企例如豐田,福特及大眾更積極致力于汽車電子芯片之開發,而國內部分主流車廠亦紛紛加入芯片開發行列,例如比亞迪、上汽等用多種形式參與芯片研發擁抱汽車芯片產業新革命的企業,更易將其應用場景和財力與芯片設計相結合,促進芯片設計快速引進。以新能源為代表的特斯拉更是推出FSD芯片,一場圍繞高級別自動駕駛的競爭也已經開始,汽車行業加速進入智能化時代。
文章結合車規芯片這個龐大的市場,針對其使用特點及進入這一領域所需要的標準,著重將討論進入這一領域所需的檢定條件——IATF 16949規范及AEC中的可靠性標準,對失效芯片進行老化篩選測試和根因分析保證車規芯片可靠性,達到零失效。最后圍繞車規芯片驗證規范的標準化,可靠性驗證的全面化,高效的老化篩選測試以及專業的失效分析進行展望。
車規芯片的相關驗證
IATF16949
在汽車行業,質量認證活動在世界各個地區均有自己的行業認證標準和要求,例如汽車制造強國德國汽車工業的 VDA6.1標準、法國的EAQF標準、意大利的AVSQ標準以及美國的QS-9000標準。成立于1997年的國際汽車特別工作組(IATF)為實現汽車行業統一的全球質量體系標準和認證,與國際標準化組織(ISO/TC 176)合作,以各國汽車工業標準為基礎,并于1999年制定并推出質量要求ISO/TS16949技術規范,《IATF16949》是當前的最新版質量管理體系標準[5]。IATF16949是國際汽車小組是以顧客為導向同時兼顧其特殊要求,針對近年汽車行業比較關注的一些問題,如汽車安全等,在標準中增加了新的條款[6,7]。IATF16949規范適用于汽車制造廠和其直接的零部件供應商,這些工廠直接關系到汽車生產,能夠進行加工制造活動和通過這類活動實現產品增值。以芯片全產業鏈為例,晶圓制造廠和封裝廠都需嚴格執行IATF16949規范進行汽車芯片生產。而僅有設計配送中心等支持功能的機構則無需取得此認證[8]。
AEC標準認證
汽車 電 子 委 員 會 ( A E C : A u t o m o t i v e Electronics Council)由三大北美汽車公司(克萊斯勒、福特和通用汽車)在1994年為建立一套通用的質量系統標準而設立[9]。AEC制定了產品質量控制方面的準則,在促進汽車零部件通用性落實的前提下,也為迅速的市場發展奠定了良好基礎。其規范標準主要包括AEC-Q100(集成電路IC)、AEC-Q101(離散組件)、AEC-Q102(離散光電LED)、AEC-Q104(多芯片組件)、AEC-Q200(被動組件)。其中AEC-Q100是專門針對IC集成電路的驗證規范,其目的是要確定器件在應用中能夠通過應力測試達到某種要求的品質和可靠度[10]。
車規芯片設計
通過對該產品使用功能、工況(電壓、頻率范圍等)和芯片所采用單元設計庫技術的驗證,確定了電路設計原則以達到車規芯片的要求。所實施的流程可查明潛在故障模式及其給系統和用戶帶來的后果,并查明故障的嚴重性和可能造成故障的因素。考慮了冗余設計問題,這種設計能夠以糾錯碼方式避免可能出現的數據預留錯誤和更換存在缺陷單元。設置了自我檢測機制,利用芯片的合理檢測時間為電路添加部分路徑節點來檢測,發現存在問題的單元并對其做出相應處理以減少因工藝波動而造成的損失。
在芯片設計階段,就要開始著手芯片可靠性實驗的考量,使用計算機輔助工程分析和仿真工具可以更短的時間內提高產品可靠性。有限元分析,熱分析以及可靠性預測模型等工具正在得到越來越廣泛的應用,這樣車規芯片在設計之初主動來提高器件可靠性和穩定性。
芯片晶圓制造
晶圓的制作主要環節為離子注入、光刻、蝕刻、鍍膜的工藝流程。每個過程都要借助數學統計研究分析工具來尋找最優參數來滿足芯片良率與質量的改善。fab廠通過檢測每道工序具體測試參數,芯片數量,頻率等信息,可以保證制程的穩定性。
盡量使測試覆蓋率達到最短時間內預先甄別不良品以免流向客戶端。芯片測試更快速高效的重要途徑之一就是通過對芯片進行自測設計,同時還能降低對外部ATE的資源依賴性。良品測試limit標準設定可以采用AEC_Q004文檔中的建議,基于一定的數據量標準差公式來設定,Static PAT Limits=Robust Mean±6 Robust Sigma。通過大數據分析,管控工藝波動,保證產品質量穩定性,該方法可以定期進行Review和更新。產品在使用前的故障是良率,而在產品使用時的故障是可靠性,所以芯片的試驗直接關系著芯片的可靠性。
浴盆曲線是由三部分組成,早妖期、穩定期和損耗期。老化篩選測試(Burn in)是ATV(Automotive)芯片測試很重要的一個步驟,它的主要功能就是去除了芯片出貨時產品早期失效的芯片,達到用戶端的高可靠性。早妖期指失效率比較高的時期,芯片失效的原因一般都是由于芯片先天存在的瑕疵或者問題造成的,比如設計上的瑕疵、工藝制造上的不正常或者材質上的內在缺陷。這些缺陷可誘發與時間和應力有關的失效,故障率一般用Dppm來表示。具體方法是先對芯片進行一定時間的100%老化測試,例如加偏壓,加高溫等,然后再進行正常的ATE 測試進行篩選[11]。浴盆曲線(圖1)中的穩定期代表著芯片在使用壽命期間失效率是相對穩定的,通常按FIT(failure in time)或MTBF(Mean Time Between Failure)小時數來描述其失效。損耗階段表明芯片的失效率開始因為芯片內在電路損耗而上升,代表已到達了芯片的極限使用壽命。
AEC-Q100芯片可靠性驗證
AEC-Q100作為汽車電子可靠性驗證的標準,其主要目的:
(1)客戶有可以參考的標準規范;
(2)芯片供貨商可以排除芯片可能存在的潛在故障。
表1是AEC-Q100根據器件工作環境溫度分為不同的產品等級,這與芯片具體應用有關,其中最嚴格最高等級標準的工作溫度范圍是-40~150℃之間。芯片供應商需不斷地對產品設計進行不斷地優化,使用先進且穩定的制造及封裝工藝,并在此基礎上使用嚴格的測試程序進行篩選,以滿足車規芯片在工作溫度及可靠度等方面的高水準。
AEC-Q100明確了芯片在設計,制造,封裝,測試和量產等各個階段所需要的驗證以及相關的卡控標準。從其內容來看,具體包含7大類別共41項的測試,如圖2所示即為AEC-Q100 Rev-H 的驗證流程及規范內容[12]。大致分為:Group A(加速環境應力測試)、Group B(加速工作壽命測試)、Group C(封裝完整性測試)、Group D(晶圓級可靠性測試)、Group E(電性驗證測試)、Group F (可篩選性測試)、Group G(密封型封裝完整性測試)。
目前AEC-Q100已成為車規芯片的重要規范,通常車規芯片供應商需要完成其項目的驗證,然后以“自我宣告”的方式說明其產品通過了其相關的驗證結果,AEC不會給予供應商任何認證。由于樣本數量較小,上述檢驗為必要的不足檢驗,體現了該方法存在局限性。測試項目可應用于否認器件可用性,但是無法判斷大批量量產芯片是否符合特定場景下的使用標準。因此對量產車規芯片進行老化篩選測試就變得非常重要,使供給用戶的芯片在穩定期內工作,增加其可靠度。同時對其進行失效分析一方面能夠確定導致芯片發生故障的根因并采取相應的措施來根治這一問題,另一方面對于固有缺陷問題也能解決,可通過優化和加嚴測試篩除以達到車規芯片的零失效率。
失效
半導體在其開發,生產,使用等各個環節都不可避免地存在著失效問題。通過有的放矢地進行失效分析:
(1)可以協助設計人員找出芯片設計上的缺陷,例如通過FIB電路修補的方式亦可驗證該結果。
(2)可以找出芯片在制造,封裝等工藝中存在的缺陷,提出切實可行的改善方案。
(3)評估不同測試向量的有效性,為生產測試提供必要的補充。芯片的故障分析主要以微觀世界為背景,通過電性、物理、化學及材料等多角度的觀察與分析,從根本上尋找導致芯片故障的因素[13],主要分析工具及試驗方法如圖3。
半導體芯片工藝制程的復雜度不斷提高,也給失效分析造成較大困難,如降低線寬需要電鏡較高分辨率,降低金屬層間距給樣品制備造成困難。透過失效現象并在結合芯片設計及工作原理的前提下,把握精確的芯片信息資料及數據,從而做出正確分析判斷。
一般半導體芯片使用后的失效機理可分為以下幾類[14]。
(1)芯片設計存在缺陷,主要體現芯片功能不能實現。
(2)本體類的相關失效,如半導體材料缺陷或封裝中所用基板本身存在的問題。
(3)工藝波動造成的失效。
芯片介質層相關失效,如柵氧,金屬間介質層等缺陷;
硅襯底和SiO2界面間存在缺陷,如Dislocation等;
芯片后端金屬互聯層由于金屬的電遷移或含鹵素及鹵化物的污染造成的金屬腐蝕等;
封裝工藝參數不合理導致的管腳連線造成的短路或者開路等。
(4)測試引入的失效,主要是測試向量電壓設置不合理等造成芯片的Overkill。
分析
車規芯片安全性與可靠性為第一考量,不僅響應于芯片設計與開發階段,測試篩選與可靠性驗證更顯重要。它巨大的市場前景讓越來越多的芯片供應商進入這一領域并加入到車規芯片產業規劃中來。結合供應鏈質量管理標準IATF16949規范以及AEC-Q100可靠性的要求,當前車規芯片驗證的流程和體系需要更加完善。
(1)車規芯片標準化系統的建立,應由技術專家(汽車整機,芯片設計、制造,封裝以及芯片測試等領域)來建立一套更加專業化,規范化,流程化的標準是必要的。
(2)芯片可靠性驗證需更加全面,產品的可靠性是需要考慮設計進去以及制造出來。
(3)老化測試需要更有效,車規芯片可以通過100%老化除去早期失效器件,對服從威布爾Weibull分布的參數β在1以下,也就是前期故障率呈顯著降低趨勢,這將突出老化測試。在實現杜絕芯片早期失效的同時,盡可能縮短老化測試的時間;
(4)對于失效芯片根因進行分析,需構成閉環。尤其是要發現因工藝制造參數卡控不盡合理或試驗覆蓋不完全而遺漏的失效芯片,否則會造成批次性問題。不同失效案例需從芯片設計,工藝制造,封裝測試,器件使用等方面進行數據收集與綜合分析以發現失效根因,然后反饋并形成解決方案。同時芯片制造產線需要應用更多主動的專業監控技術,例如,CPK技術、SPC技術和PPM技術,可以對生產能力、工藝穩定性進行分析和預測[15]。
結語
在實踐中,我們常常會碰到TSP數據準備和TSP數據可視化的問題,文章運用實踐經驗總結了以上兩種TSP數據可視化制作的兩種方法來解決TSP數據的處理。
-
芯片
+關注
關注
454文章
50460瀏覽量
421968 -
車規芯片
+關注
關注
0文章
170瀏覽量
7307
發布評論請先 登錄
相關推薦
車規芯片變更如何通過AEC-Q100驗證
長電科技首座大規模生產車規級芯片成品的先進封裝基地即將落地
年度車規級MCU芯片行業發展綜述與展望
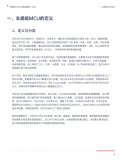
評論