圖片來源:Bing
切割工序
SiC襯底切割是將晶棒切割為晶片,切割方式有內圓和外圓兩種。由于SiC價格高,外圓、內圓刀片厚度較大,切割損耗高、生產效率低,加大了襯底的成本。直徑較大的晶體,內圓、外圓切割會造成刀具變形和振動,影響加工質量,所以大直徑的單晶內圓和外圓不是首選。
多線切割使用的是電鍍金剛石的鋼線(又稱為鉆石線),鉆石線高速運動(500m/min),在偏轉輥、收線輥、放線輥和測量輥等 的牽引下圍繞線軸形成一張線網,對上方或者下面的晶棒切割,從而實現多線切割,其示意圖如下圖所示。
鉆石線的直徑有150-300um(一片SiC襯底的厚度在300um左右,意味著用線鋸來切,切一片就要損耗一片,這也是影響良率的關鍵因素之一),。在切割過程中需要保證鉆石線隨線軸擺動在一個非常小的角度范圍內,切割過程中減小左右振動,就可以保證切割的效率、良率以及切割過后表面的平整度。
研磨工序
除去切片過程中造成的表面損傷層,提高表面質量并盡量減少對襯底造成的表面損傷與變質。SiC硬度高,除去其表面損傷層就要用硬度更高的碳化硼或金剛石微粉。
根據工藝的不同磨削可以分粗磨和精磨,粗磨主要是提高加工效率,使用較大的磨粒; 而精磨是以提高表面質量、降低表面損傷層為目的,因此使用粒徑更小的磨粒。
在下壓力作用下,首先使工件發生塑性形變,荷載的增加會導致垂直方向微裂紋的出現,進而再產生橫向微裂紋,當作用力達到某一數值時,裂紋擴展導致表面碎屑的脫落,進而達到加工目的,如圖下圖所示。
研磨有單面磨和雙面磨,單面磨一次只能磨削襯底的一個面,雙面研磨具有上、下兩個研磨盤,可以同時研磨襯底的兩個面。單面磨、雙面磨的表面粗糙度與使用的磨粒及研磨液有關,不同加工方式導致工件翹曲度和平面度不同。
單面磨,襯底用蠟粘在鋼盤上,通過施加壓力,襯底基片發生微變形,上表面被壓平; 經過磨削過程后, 下表面被磨平; 去除壓力之后, 襯底發生微變形, 上表面基本恢復到原來的形狀, 造成被磨平的下表面也發生變形, 這就造成了兩個表面發生翹曲變形,平面度變差,變形過程如下圖。
為保證加工襯底的表面質量,進行雙面研磨之前上、下研磨盤具有非常高的平面度。雙面研磨盤首先施壓工件最高點,使該處發生變形并逐漸被磨平,高點被逐漸磨平后,襯底所受壓力逐漸減小,襯底均勻受力,使各處變形一致,這樣上、下表面都被磨平。研磨完成后去除壓力,各處由于受相同壓力作用,恢復的程度也相同,這樣能實現非常小的翹曲變形,平面度也較好,工作過程如下圖所示。雙面研磨可以改善SiC襯底的翹曲度與平面度。
拋光工序
SiC襯底一般使用化學機械拋光法(CMP:Chemical Mechanical Polishing)。在經過研磨去除量達到一定程度的情況下,微小磨粒的在加工液中產生拋光切削作用,通過工件與轉軸的相互作用,產生更細的微裂紋,滿足粗糙度要求,加工原理如下圖所示。
SiC襯底拋光的設備類同于研磨,但是使用的拋光液不同。由于SiC化學性質非常穩定,常溫下很難與其他化學物質發生反應,這使得SiC襯底在拋光過程中化學作用比較微弱, 因此拋光液中磨粒不能太過鋒利, 否則會繼續劃傷襯底, 故經常使用硬度比其小的二氧化硅溶膠。
根據需要選擇粗、精拋兩種工藝。質硬拋光墊可以獲得較好的平面度,質軟拋光墊可以獲得較好的表面質量,所以粗拋光使用聚氨酯拋光墊與金剛石拋光液, 以提高拋光效率; 精拋光使用軟質瀝青拋光墊和二氧化硅拋光液,以提高表面質量, 兩者配合使用可在獲得較高效率的同時取得納米級甚至更小的表面粗糙度。
研磨拋光液
拋光研磨液是拋光研磨技術中的重要組成部分,在加工過程中,其不僅具有磨削去除作用,還具備拋光工件的作用。拋光研磨液的組成包括:固相磨料和液相介質,其中液相介質一般包含:去離子水或油(由使用性決定)、分散劑、改性劑、表面活性劑等。研磨精度由磨料粒度決定,不同的研磨精度適用不同的加工需要。下表介紹了不同研磨精度與磨料粒度之間的關系[5]。
加工工件在液體加工液中進行,促使磨料顆粒與加工工件作用,從而達到去除表面微量金屬的目的,最終使工件達到符合要求的加工精度與粗糙度。傳統的研磨拋光通常是根據不同的加工條件選擇不同的磨料(性質、粒度等不同),將加工工件置于研磨墊或拋光盤上,用夾具裝置固定工件,再對工件施加一定的壓力,機床的主軸旋轉從而帶動磨盤進行行星轉動,磨盤與加工工件間的相對運動以及游離磨料的切削作用會使工件表面去除微薄量的材料,從而達到加工的目的,拋光過程的加工示意圖如下圖所示。
材料的去除率主要取決于游離的磨料作用,因此選擇合適的磨料是制備精密拋光研磨制品的關鍵因素。磨料相對加工工件的硬度對磨料在磨削過程中的作用機制有著重要影響,因此磨料大多選擇具有高強度和高硬度的SiC、金剛石、立方氮化硼(CBN)等。
磨料的粒徑大小直接影響磨粒的壓強及其切入工件的深度,大粒徑磨粒壓強大,機械去除作用強,材料去除率較高,因此粒徑較大的磨粒容易在拋光表面產生殘留劃痕甚至裂紋;小粒徑磨粒,去除率較小容易獲得較好的拋光表面質量。因此在研磨段的粒徑相對于拋光的粒徑要大,粗磨>精磨>粗拋>精拋,不同的加工精度有不同的要求。相關文獻指出:當磨料粒度在小范圍內呈正態均勻分布時,所制備漿料的懸浮穩定性和分散穩定性會提高,因此合理的顆粒級配也是制備精密拋光研磨液的重要參數。
拋光研磨液具備以下幾點作用:
懸浮作用:游離磨料的加入要求研磨液具有良好的懸浮性,保證磨料分布均勻并在一定使用時間內不產生絮凝或沉淀,從而大大提高研磨加工的質量和效率。加工過程中,研磨液會吸附在固體顆粒表面上,進而產生足夠高的位壘,使顆粒均勻分散以達到分散、懸浮的特性。
潤滑作用:研磨液提供的液體環境能減少磨粒、磨屑與工件表面之間的摩擦,起到潤滑的作用。通過在研磨液中添加部分活性元素硫、氯等極壓添加劑來提高耐高壓能力。類似含極壓元素的化合物適合在邊界條件潤滑狀態較好的情況下,進行高溫、高壓的研磨加工,能夠有效的防止工件的表面粗糙度的惡化,從而降低損傷程度。
冷卻作用:研磨液在加工過程中能滲入高溫研磨區域內,有效降低研磨區溫度,防止工件表面燒傷和裂紋的產生。研磨液的冷卻性能與它的導熱性能、對工件表面潤濕性以及供液方式緊密相關。實際加工過程中,努力降低研磨液表面張力,提高滲透性和潤滑性,可獲得比較理想的液體。
清洗作用:在研磨加工時,會產生大量細碎的磨屑和磨粒粉末,容易粘附在磨床工件臺表面上,從而影響研磨墊表面質量,降低機床精度。研磨液的液體環境,可以通過其流動性帶走多余的碎屑,又同時保證了工件與磨床接觸面的光潔程度。
防銹功能:研磨設備多為金屬材質,在空氣中或者溶液中會發生氧化生銹的現象。所以要求研磨液具備一定的防銹蝕能力,因此制備研磨液時,需要考慮其本身的防銹性能以及加入表面活性劑的防銹作用。
抗氧化安定性:對于油基磨削液中,需要考慮所用基礎油的氧化安定性能。通常情況下,油品與空氣接觸容易導致氧化,這種變化是不可逆的,會影響酸度、粘度、顏色,導致沉淀的產生大大影響使用性能。
-
半導體技術
+關注
關注
3文章
237瀏覽量
60683 -
SiC
+關注
關注
29文章
2765瀏覽量
62457 -
CMP
+關注
關注
6文章
141瀏覽量
25944
發布評論請先 登錄
相關推薦
半導體切割專用樹脂墊條
半導體切割用的樹脂墊條
剖面/晶背研磨 (Cross-section/Backside)
《炬豐科技-半導體工藝》III-V/SOI 波導電路的化學機械拋光工藝開發
關于硅晶片研磨之后的清洗工藝介紹
兩種標準的半導體制造工藝介紹
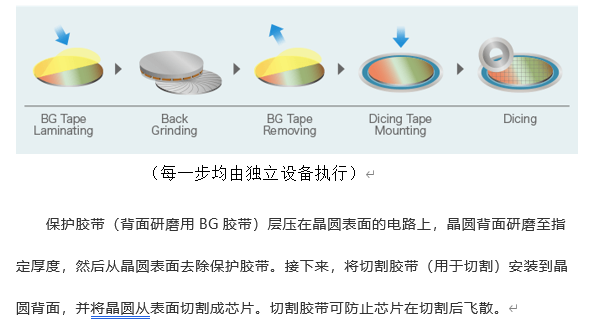
評論