引言
隨著集成電路互連線的寬度和間距接近3pm,鋁和鋁合金的等離子體蝕刻變得更有必要。為了防止蝕刻掩模下的橫向蝕刻,我們需要一個側壁鈍化機制。盡管AlCl和AlBr都具有可觀的蒸氣壓,但大多數鋁蝕刻的研究都使用Cl基蝕刻化學物質。當在等離子體放電中分解時,CCl為還原物質提供了來源,并用于去除表面氧化物和Cl,與下面的Al反應。
最近一項通過He-BC13-C12-CHC13的化學方法對鋁蝕刻的研究表明,鋁蝕刻速率隨著氯氣流的增加而增加,并且對施加的射頻功率不敏感。英思特利用BClr CI2、SiClr C12和He-SiClClcCl2的化學方法,研究了純Al薄膜的等離子體蝕刻率行為。
實驗與討論
本研究中使用的不銹鋼腔室直徑30厘米,高22厘米,蝕刻的切片位于較低的射頻供電電極上。兩個電極直徑15厘米,由6061硬質陽極氧化鋁構成。工藝氣體通過頂部“淋浴頭”模式的接地電極進入。電極間距為4 cm,電極溫度均保持在40℃。使用針閥調整流速,并從隔離室的壓力上升速率中確定。工藝壓力使用節流閥進行控制,并使用電容壓力計進行測量。
圖1中看到的鋁蝕刻速率和電壓(即離子能量)之間的密切相關性與等離子體實驗的結果形成對比,后者發現鋁蝕刻速率與離子轟擊能量無關。這種明顯不一致的原因在于是否存在蝕刻殘留物。等離子體束實驗使用純氯氣等離子體,不可能去除掩模殘余物。
圖1:AI蝕刻率,射頻峰峰電壓,發展降壓與總壓碳化硅
我們發現,總氣體流量超過200sccm導致了鋁蝕刻過程中Cl2消耗的問題。假設氯氣在AI上的粘附系數統一,最大可能的蝕刻速率等于2/3 ,Cl通量與氯氣分壓成正比。對于P(CI2)= 30fl,我們計算出最大的鋁蝕刻率為5X105A/min。參見圖2顯示,測量的蝕刻速率僅為1.5X104A/min。最大可能的蝕刻速率和實際蝕刻速率之間的差異系數為30,這進一步證實了我們的假設,即實驗結果是無載荷蝕刻條件的特征。
圖2
結論
英思特通過使用蝕刻化學物質實驗研究表明,Al的等離子體蝕刻速率由兩個因素決定:(1)蝕刻表面上形成的殘余物(例如si的濃度),(2)CI2的沖擊通量增加了離子的能量,從而在蝕刻表面減少了這些掩模殘留物的濃度,從而增加了蝕刻率。這些掩模殘留物的存在,被認為是實現可控蝕刻工藝的關鍵。
江蘇英思特半導體科技有限公司主要從事濕法制程設備,晶圓清潔設備,RCA清洗機,KOH腐殖清洗機等設備的設計、生產和維護。
審核編輯:湯梓紅
-
集成電路
+關注
關注
5381文章
11382瀏覽量
360851 -
半導體
+關注
關注
334文章
27007瀏覽量
216277 -
等離子體
+關注
關注
0文章
114瀏覽量
14207 -
蝕刻
+關注
關注
9文章
413瀏覽量
15346
發布評論請先 登錄
相關推薦
金屬蝕刻殘留物對對等離子體成分和均勻性的影響
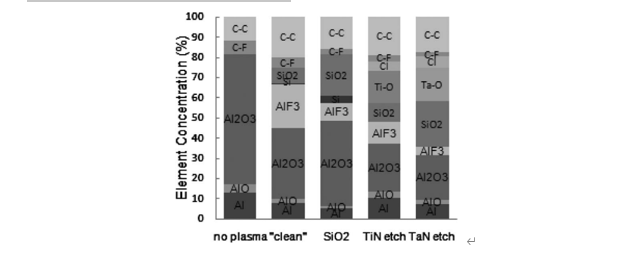
等離子體蝕刻和沉積問題的解決方案
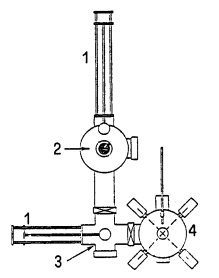
PCB電路板等離子體切割機蝕孔工藝技術
PCB板制作工藝中的等離子體加工技術
微波標量反射計可測量大范圍的等離子體密度
等離子體光譜儀的原理是什么?
低溫等離子體廢氣處理系統
TDK|低溫等離子體技術的應用
等離子體應用
精確跟蹤芯片蝕刻過程,用高分辨率光譜儀監測等離子體
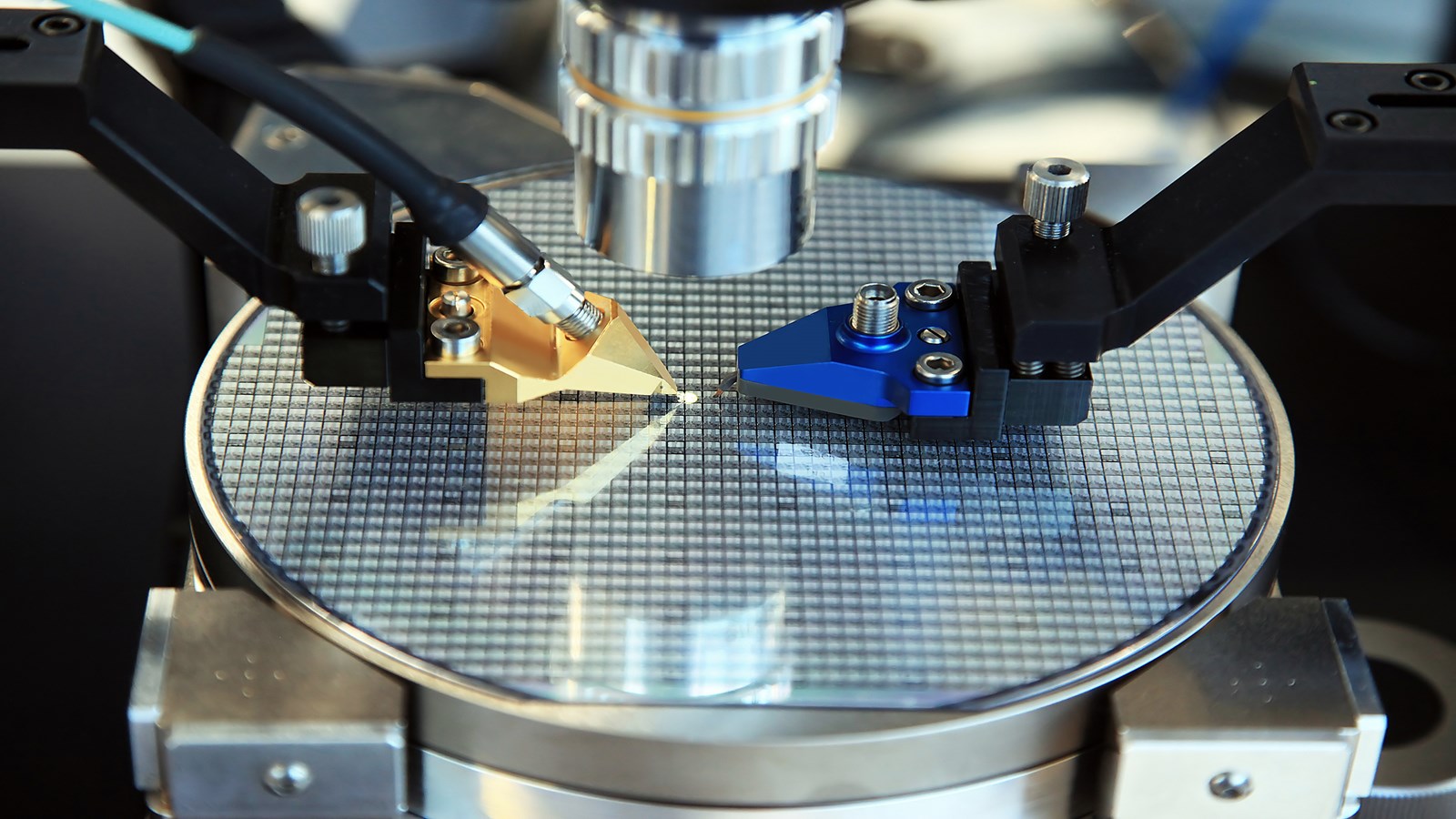
低溫等離子體技術的應用
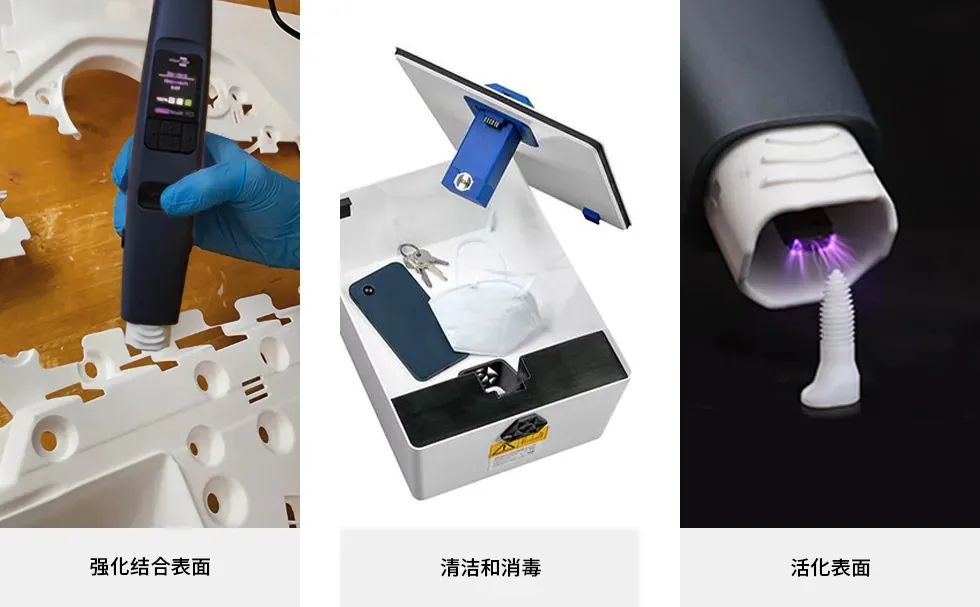
真空等離子清洗機的制造商正在引入氧和氫等離子體來蝕刻石墨烯
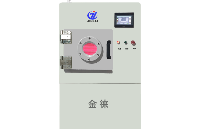
等離子體清洗工藝的關鍵技術 等離子體清洗在封裝生產中的應用
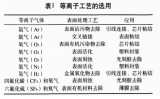
針對氧氣(O2)和三氯化硼(BCl3)等離子體進行原子層蝕刻的研究
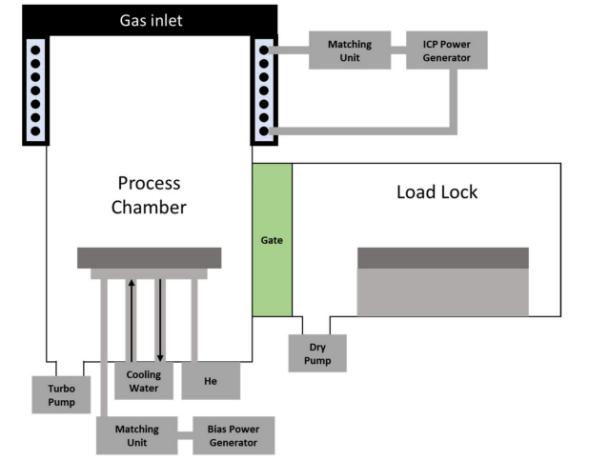
評論