從工業物聯網 (IIoT) 到網絡基礎設施設備,下一代電子系統正在注入新的智能,在不斷縮小的空間中需要更多功率,而不會影響熱預算。因此,傳統的解決方案并不合適。然而,考慮到上市時間的壓力,設計人員沒有大量的時間來設計電源,他們必須在有限的空間內努力散熱,同時滿足沖擊、振動和 EMI 要求。
可靠地為收縮設備和傳感器供電而不會過熱的最佳方法是什么?并快速創建這些電源設計?
傳感器歷來包括傳感元件和某種將傳感數據傳輸到可編程邏輯控制器(PLC)的方法。數據將是單向的,并以模擬格式傳輸。然而,模擬數據通信容易產生噪聲,控制器無法直接診斷、重新配置或重新校準傳感器。隨著時間的推移,技術不斷進步,傳感器制造商開始將更多功能集成到這些設備中,同時通過二進制傳感器降低噪聲敏感性。在二進制傳感器中,數據仍然僅限于單向通信,工廠車間仍然需要技術人員來處理手動校準等任務。
IO-Link 的出現通過允許傳感器和控制器之間的雙向通信,將智能帶到工廠車間的邊緣(圖 2)。借助此功能,系統可以實時調整、配置和診斷傳感器,這正是滿足工業 4.0 和智能工廠需求所需要的。
與為單一產品構建和優化的傳統工廠不同,智能工廠旨在快速適應市場需求的變化。實時診斷功能有助于預測性維護,并可延長工廠正常運行時間。
圖2.帶 IO 鏈路傳感器的 PLC
智能傳感器的智能功能增加了這些傳感器的功耗。與此同時,工業設備制造商也出現了小型化的趨勢。這意味著為智能傳感器供電需要解決熱量和尺寸挑戰。為了說明這些挑戰,讓我們考慮一個帶有IO-Link的智能接近傳感器(圖3)。在此應用中,微控制器從傳感元件收集數據,對其進行線性化和校準,然后將其發送到IO-Link收發器。從這里,數據被發送到系統PLC。IO-Link 連接器還提供 24V 電壓為傳感器供電。
圖3.帶 IO-Link 的智能接近傳感器示例。
傳感器電路的傳統電源解決方案涉及低壓差線性穩壓器(LDO)。讓我們看一下傳感器電路、電源和整個器件的功耗。老式模擬傳感器電路通常消耗約15mA電流。24V工業電源軌最大可達30VDC。功耗如下:
IO=15mA, Vi=30V (maximum)
PSensor=VoxIo=75mW
PSUP=PLDO=(Vi–Vo)xIo=375mW
PDevice=PSensor+PLDO=450mW
在本例中,僅使用75mW進行實際工作(為傳感器電路供電),而LDO由于效率低下而損失375mW。我們的器件總功耗必須為450mW。為傳感器添加更多智能功能將需要更多的電流,這對設備的功耗來說不是好消息。使用我們上面的計算,如果我們將傳感器電路電流增加到30mA,則:IO = 30mA, PSensor = 150mW, PSUP = 750mW, 和 PDevice = 900mW。900mW超過了大多數小型接近傳感器的功耗極限。所以,熱量是一個大問題。
傳統LDO電源解決方案的替代方案是使用小型化的DC-DC電源模塊。如圖4所示,在15mA傳感器電流和保守的75%效率下,DC-DC電源模塊的功率損耗僅為25mW。這有助于將器件總功率損耗從450mW降至100mW,功耗降低4.5倍。
圖4.電源耗散 – LDO 與 DC/DC 轉換器解決方案。
由于DC-DC電源模塊的高效率,傳感器可以支持更多的電路和功能,因為熱量最小化并支持更多的傳感器電流。Maxim的Himalaya uSLIC系列提供了幾個非常適合微型傳感器的電源模塊示例:MAXM17532,100mA超緊湊、寬輸入電壓uSLIC器件,以及MAXM17552,可以工作在高達60V的輸入電壓。這些緊湊型模塊可節省空間、減少熱量,并有助于簡化電源設計。
隨著工業 4.0 繼續推動對智能傳感器的需求,借助高度集成的 DC-DC 電源模塊,現在更容易解決為這些傳感器供電的挑戰。
審核編輯:郭婷
-
電源
+關注
關注
184文章
17594瀏覽量
249517 -
傳感器
+關注
關注
2548文章
50698瀏覽量
752051 -
IIoT
+關注
關注
3文章
230瀏覽量
26060
發布評論請先 登錄
相關推薦
貿澤電子的歐姆定律計算器上線 節約您的設計時間
無線傳感器模塊節省時間
通過節省時間和成本的創新技術降 低電源中的EMI
如何通過電源設計節省時間和空間
MSP430FR2675和MSP430FR2676器件的優勢
使用草圖布線節省時間和工作量
集電容式觸控和主機控制器功能,節約時間、成本以及電路板空間
如何在數字IP設計中節省時間

如何通過節省時間和成本的創新技術降低電源中的EMI
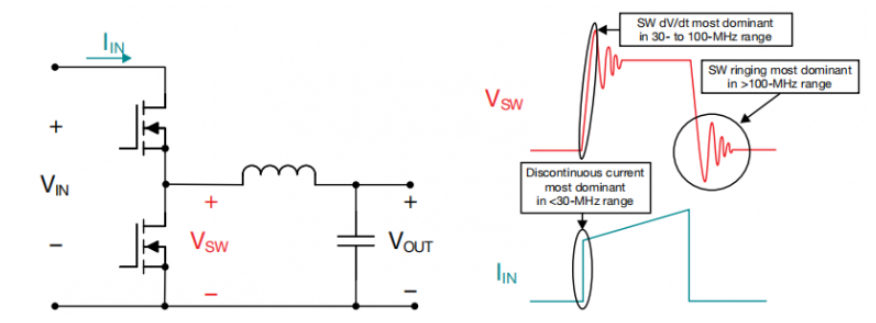
參考設計節省時間和精力
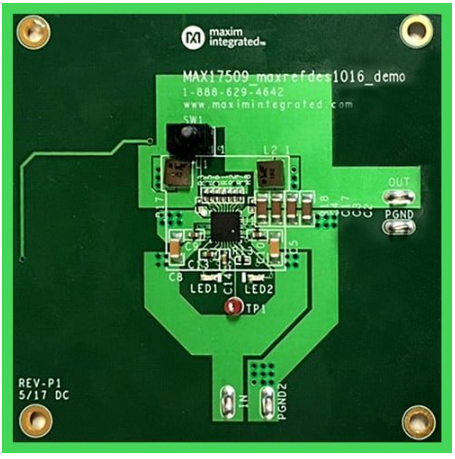
Vivado那些事兒:節省編譯時間系列文章
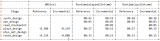
評論