問題描述
AMB陶瓷覆銅基板是一個復合結(jié)構(gòu):銅箔/焊料/陶瓷/焊料/銅箔,不同材料之間的CTE、楊氏模量、導熱性能也存在差異。
在IGBT/SiC功率模塊的封裝制程中,尤其芯片燒結(jié)、散熱器焊接或塑封,同時有熱參數(shù)、壓力參數(shù)及其他材料CTE的條件影響, 會導致AMB覆銅陶瓷基板產(chǎn)生翹曲,進而產(chǎn)生一些通用問題,例如焊接空洞、塑封分層,嚴重情況下甚至產(chǎn)生陶瓷開裂等問題。
AMB通用技術問題-翹曲
翹曲機理?
復合材料結(jié)構(gòu)的翹曲機理:不同材料屬性各異,其模量、強度、熱膨脹系數(shù)差異很大,復合之后會存在明顯的各向異性。復合材料結(jié)構(gòu)的翹曲變形主要是由燒結(jié)反應過程中的殘余應力引起,而殘余應力又是由組分材料的熱膨脹不匹配、多層結(jié)構(gòu)線性收縮不一致引起的。
AMB翹曲示意圖
AMB翹曲T0狀態(tài)主要受三大因素影響——線路排布、材料組合、AMB單片尺寸。在客戶端焊接、燒結(jié)及塑封制程中,圖形面與非圖形面的銅材不論是體積還是Layout上必然存在差異,導致在受熱過程中釋放差異性應力,進而導致AMB翹曲。
威斯派爾解決方案?
1.圖形設計優(yōu)化或者反饋
2.燒結(jié)工藝保證(燒結(jié)工藝參數(shù)、特制燒結(jié)治具等);成品翹曲度保證(樣品初制承諾0.65%,具體以客戶圖紙為準)
3.Winspower實驗室實驗模擬(以客戶溫度曲線為基礎,平臺模擬翹曲)
威斯派爾實驗室目前擁有由研發(fā)團隊搭建的測試平臺,參考客戶端封裝的工藝參數(shù),可以模擬分析AMB的翹曲形態(tài)及翹曲數(shù)據(jù),將內(nèi)部的測試數(shù)據(jù)與客戶端測試數(shù)據(jù)相結(jié)合后,技術團隊分享最優(yōu)的解決方案:銅減薄、調(diào)整銅面積、調(diào)整材料組合、Dimpling設計等,并快速提供樣品給客戶。
撰文:Stefan
來源 :威斯派爾
審核編輯:劉清
-
散熱器
+關注
關注
2文章
1056瀏覽量
37495 -
IGBT
+關注
關注
1265文章
3762瀏覽量
248364 -
SiC
+關注
關注
29文章
2771瀏覽量
62468 -
AMB
+關注
關注
0文章
21瀏覽量
5995
原文標題:技術文章 | AMB通用技術問題——翹曲及其解決方案
文章出處:【微信號:深圳市賽姆烯金科技有限公司,微信公眾號:深圳市賽姆烯金科技有限公司】歡迎添加關注!文章轉(zhuǎn)載請注明出處。
發(fā)布評論請先 登錄
相關推薦
預防翹曲的方法
PCB元器件焊接翹曲問題研究
如何防止線路板曲翹
針對PCB板翹曲如何解決?
針對PCB板翹曲如何解決?
防止印制板翹曲的方法
如何預防PCB板翹曲?
SMT異常的原因和翹曲有關系嗎?
常見PCB弓曲扭曲翹曲撓曲分析改善方案
什么是PoP層疊封裝? 基板薄化對翹曲有什么影響?
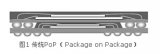
評論