先進半導體封裝的凸塊技術已取得顯著發展,以應對縮小接觸間距和傳統倒裝芯片焊接相關限制帶來的挑戰。該領域的一項突出進步是 3D Cu-Cu 混合鍵合技術,它提供了一種變革性的解決方案。
隨著焊料凸點間距縮小,會出現一些問題。凸塊高度和接合表面積的降低使得建立可靠的電氣連接變得越來越困難,因此需要精確的制造工藝來避免錯誤。關鍵的共面性和表面粗糙度變得至關重要,因為即使是微小的不規則性也會影響成功的粘合。
制造面臨一些障礙,例如由于銅柱和凸塊直徑較小而導致蝕刻困難,從而更有可能發生底切。隨著有效確保均勻性和控制共面性變得更加困難,電化學沉積 (ECD) 電鍍變得更加復雜。此外,隨著凸塊尺寸不斷縮小,接合質量對凸塊共面性、表面粗糙度和硬度等因素的敏感性使得對溫度、時間和壓力等參數的調整變得復雜。
傳統的倒裝芯片接合方法僅限于 50μm 或 40μm 的間距,由于熱膨脹不匹配導致翹曲和芯片移位,因此會遇到可靠性問題。為了應對這些挑戰,半導體行業正在轉向熱壓接合 (TCB),以實現先進的細間距接合應用,包括小至 10μm 的間距。TCB 為實現不斷發展的半導體封裝領域所需的精度和可靠性提供了一條有前途的途徑,從而突破了電子設備小型化和性能的界限。
然而,當接觸間距減小到 10 微米左右時,出現了一些問題。焊球尺寸的減小會增加金屬間化合物 (IMC) 形成的風險,從而降低導電性和機械性能。此外,在回流焊過程中,焊球接觸并導致橋接故障的可能性可能會導致芯片故障。這些限制在高性能組件封裝場景中變得越來越成問題。
為了克服這些問題,銅-銅混合鍵合技術成為了游戲規則的改變者。這項創新技術涉及在介電材料之間嵌入金屬觸點,并使用熱處理來實現銅原子的固態擴散,從而消除與焊接相關的橋接問題。
混合鍵合相對于倒裝焊接的優點是顯而易見的。
首先,它實現了超細間距和小觸點尺寸,有利于高 I/O 數量。這對于現代半導體封裝至關重要,因為設備需要越來越多的連接來滿足性能需求。
其次,與通常依賴底部填充材料的倒裝焊接不同,銅-銅混合鍵合不需要底部填充,從而減少了寄生電容、電阻和電感以及熱阻。
最后,銅-銅混合鍵合中鍵合連接的厚度減小,幾乎消除了倒裝芯片技術中 10-30 微米厚度的焊球,為更緊湊、更高效的半導體封裝開辟了新的可能性。
銅-銅混合鍵合技術為先進半導體封裝帶來了巨大的前景,但它也帶來了一系列挑戰,需要創新的解決方案來實現未來的發展。
目前Cu-Cu混合鍵合有三種方式。晶圓到晶圓(W2W)工藝是最常用的,而芯片到晶圓(D2W)或芯片到晶圓(C2W)工藝正在深入研究開發中,因為它可以滿足更多需要集成不同尺寸的應用。
對于所有這三種方式,制造中的一個關鍵方面是鍵合環境,其中通過化學機械拋光 (CMP) 優化實現平坦且清潔的電介質表面至關重要。此外,開發能夠承受較低退火溫度和較短持續時間的介電材料對于最大限度地減少鍵合過程中晶圓變形和翹曲的可能性至關重要。優化的銅溶液電化學沉積 (ECD) 還可以減少退火時間并降低退火溫度,從而提高效率。
就 D2W/C2W 工藝而言,解決與芯片分割和邊緣效應相關的挑戰以及最大限度地減少芯片和晶圓上的污染將是關鍵。需要高精度貼片機來確保精確的芯片貼裝,并將公差縮小至低至 0.2μm。為了適應潛在的放置錯誤,必須使用更大的銅焊盤。此外,先進的薄晶圓處理技術將在確保銅-銅混合鍵合的成功實施方面發揮重要作用。
銅-銅混合鍵合的未來發展可能會集中在改進和優化工藝的這些關鍵方面。這包括 CMP、介電材料、ECD 解決方案和拾放機械方面的進步,以及處理薄晶圓方面的創新。克服這些挑戰將為先進半導體封裝中更廣泛采用銅-銅混合鍵合鋪平道路,從而能夠創建更小、更強大且節能的電子設備。
審核編輯:湯梓紅
-
半導體
+關注
關注
334文章
27003瀏覽量
216265 -
3D
+關注
關注
9文章
2862瀏覽量
107324 -
封裝
+關注
關注
126文章
7778瀏覽量
142718 -
焊接
+關注
關注
38文章
3057瀏覽量
59587
原文標題:3D cu-cu鍵合,封裝新革命?
文章出處:【微信號:深圳市賽姆烯金科技有限公司,微信公眾號:深圳市賽姆烯金科技有限公司】歡迎添加關注!文章轉載請注明出處。
發布評論請先 登錄
相關推薦
3D顯示技術的發展現狀及未來趨勢
研發的銅混合鍵合工藝正推動下一代2.5D和3D封裝技術
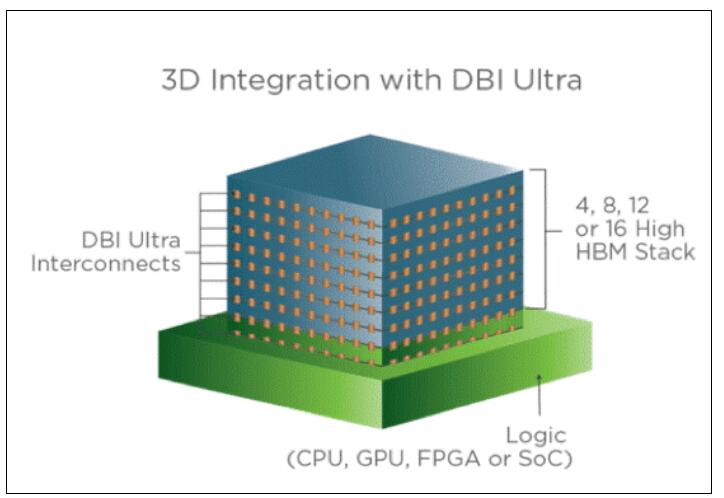
BOE濕蝕對三維集成中銅模式直接鍵界面特性的影響
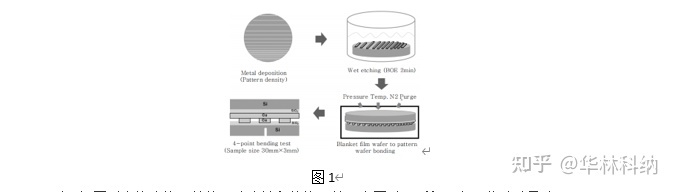
先進封裝中銅-銅低溫鍵合技術研究進展
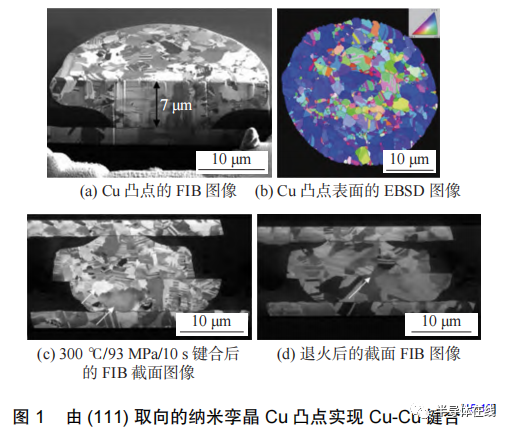
評論