齒輪,作為高精度產品,自古以來一直在人類的工業、技術和生產歷程中扮演著關鍵角色,象征著工匠精神、創新和技術發展。在工業領域,齒輪的地位類似于計算中的芯片。它們廣泛應用于汽車、制造設備中,具有高精度和復雜工藝的特點。
以對轉速有著極致要求的新能源汽車為例,齒輪對其而言既是安全件又是精密件,既要保證安全又要確保高速低噪。因此,新能源汽車對齒輪的精度和強度要求都特別高,長期以來,我國能夠規模化生產精鍛齒輪的企業幾乎是鳳毛麟角。
本期《行知數字中國》將走進我國杰出的齒輪制造企業之一——浙江雙環傳動機械股份有限公司(以下簡稱“雙環傳動”)。雙環傳動專注齒輪生產已經有 40 年,目前其產生的齒輪占中國 A0 級以上新能源汽車的 60%,也就是說,路上跑的每十輛新能源汽車里,大概有六輛用上了它家的齒輪。
這一亮眼成績的背后,數字化轉型功不可沒。“我們所理解的數字化是可以讓制造更簡單、讓企業管理更高效。”雙環傳動董事、副總經理李水土在接受 InfoQ 采訪時表示,優秀的企業,產品是捅上天,文化是扎下根,中間的管理應確保順暢高效。
他指出,雙環傳動在過去十年中經歷了顯著的變化,原來主要給世界 500 強做配套(代工),現在可以做自己的品牌和產品,以制造養技術、養研發,實現研發和制造兩翼齊飛。某種程度上看,雙環傳動的數字化過程可以視為一場命運之齒輪的關鍵轉動,不僅塑造著雙環傳動自身的未來,也讓我們看到了未來制造業的方向。
每個齒輪都有“身份證”
在早期,雙環傳動曾面臨產品質量控制的挑戰。比如產品在市場上出現了客戶的抱怨和投訴,內部卻難以追溯到投訴的原因,因為當時信息化條件尚未成熟,無法確定產品制造的具體時間、尺寸、機床、以及產品特性等詳細信息。而這種情況經常導致市場問題不能夠及時解決,客戶的需求無法得到滿足。
大約十年前,雙環傳動開始思考如何更好地為客戶提供服務,并借助信息化解決制造問題。同時,他們采用了豐田精益生產管理模式(TPS)管理系統,包括成品條碼系統和車間工票系統,將管理信息化與制造精益化相結合。
具體而言,雙環傳動通過數字化技術將線下生產行為從線下“遷移”到線上進行模擬,每個產品都有獨特的“身份證”(二維碼),包含了原材料、材料經銷商、加工參數,以及齒輪產品本身的尺寸、噪音表現等詳細的制造信息。
“因為每個齒輪的二維碼都是不一樣的,當它們進入到市場,我們就可以實時掌握、了解和追溯這些信息,回來隨時隨時隨地的可以去了解這些信息。”李水土強調,這使雙環傳動實現了整個產品制造過程的追溯和管理。
此外,雙環傳動還面臨另一大挑戰,即信息孤島。齒輪制造本身的工藝要求,以及汽車產業鏈的復雜性,使得產品從生產到推向市場的全生命周期過程中,信息共享的難度非常之大。無論是內部不同車間之間,還是與供應商、客戶之間,很多信息都是孤立的。“比如,在整個客戶市場,我們還有多少產品留存,車間里的生產進度如何,很多細節往往搞不清楚。”
而通過數字化平臺的構建,所有信息都可以在線上呈現,很好地解決了雙環傳動面對市場和供應商時的被動局面。對于客戶而言,可以清楚地知道所需的齒輪在哪里生產、生產到什么狀態、什么時候可以抵達汽車生產車間等等;而對于供應商而言,他們同樣可以掌握雙環傳動的產品生產進度,進而預測和安排原材料的供應。
“需要綜合的平臺,才可以把信息聚合起來,打通各環節的工作,否則信息是斷的、效率也低下。”李水土指出。
沒有精益的數字化如“空中樓閣”
信息化 + 精益化 + 自動化,是雙環傳動的數字化轉型“鐵三角”。
談到精益生產和數字化結合的邏輯,李水土進一步闡述道,精益生產是雙環傳動一切制造活動的基礎,精益可以讓線下生產作業更有序、更規范,以減少浪費,提高效率。而數字化把規范過的作業,通過萬物互聯的技術遷移到線上,繼而收集數據、分析數據,實現對整個生產運營過程的有效管理。
他強調,數字化本身只是一個工具,它不能解決如何制造產品和組織生產的問題,這是精益制造的任務。但數字化能讓企業更好地利用數據。
過去,企業的決策結果往往是滯后的,精益管理的相關動作及其反饋時效性不足,這在很大程度上限制了其價值發揮。而通過數字化工具,制造企業可以實時了解其生產過程中的各種數據,比如生產成本、生產效率、產品質量。借此,再通過精益化手段對成本進行控制、對生產效率和質量進行提升,可以使得整個生產過程處于一個可管理和可控制的狀態,而不再需要依賴事后的監測和反饋。
“無論是供應商、客戶、生產車間、質量部門,都可以在同一個平臺上進行協作,這可以大大提高管理效率和效果。比如,對管理者來說,只要在辦公室里就可以隨時打開某個車間,查看它的生產狀態、實時的生產進度、質量情況、設備狀態等等,進而做出進一步的決策。”
換句話說,精益化是方法論,而數字化可以把這個方法論固化沉淀下來,變成標準的、可復制的。“讓工廠從無序到有序、從有序到高效的轉變需要精益化和數字化的互相促進。”李水土感慨道,“沒有精益的數字化是空的,就如空中樓閣。”
融合 40 年制造和 20 年精益管理經驗做一個系統
承載雙環傳動精益經驗的數字化平臺,是其自主研發的數字化制造運營管理平臺——D-MOM。基于精益、自動化和信息化原則構建,D-MOM 是一個公有的平臺,各部門在上面能夠高效協同工作,實現去中心化管理并共享數據。
這一平臺的獨特之處在于它融合了雙環傳動 40 年的制造經驗和 20 年的精益管理經驗,滿足了離散制造管控的需求。“大約在 10 年前,我們嘗試聯系了多家軟件公司,卻發現它們難以將我們擁有的多年制造經驗和精益管理經驗融入到一個平臺之中。”李水土回憶說,數字化轉型一直是兩層皮,搞系統的人不懂業務,搞業務的人不懂系統。
因此,面對這一情況,雙環傳動決定采取主動的方式,召集 IT 人才,將企業的運營經驗沉淀下來并寫成一套平臺。“一旦這個平臺建立起來,我們可以將這些寶貴的經驗傳授給其他離散制造領域的企業,為整個產業做出貢獻。當時,這就是我們的愿景和行動計劃。”
通過自主研發 D-MOM 數字化制造運營管理平臺,雙環傳動實現了企業制造數字化技術和數據分析應用技術的自主可控,填補了國內參數級 MES 領域的空白。這一平臺不僅涵蓋了生產、工藝、質量、能源、設備、倉儲、績效、刀具等十多個子系統,還實現了作業標準化、流程協同化、過程可視化和追溯全程化。
D-MOM 平臺采用微服務架構,可實現集團化部署,基于精益原則的構建,實現了信息技術(IT)、運營技術(OT)和企業技術(ET)的深度融合,以及與其他企業相關系統的互聯互通。此外,該系統還與 PLM、ERP、CRM、SRM、OA 等系統高度融合,同時對接大數據平臺,從而實現了數據應用、企業智能管理與決策。
雖然 D-MOM 是自主研發而來,但也吸收了來自多個合作伙伴的先進管理經驗和技術。李水土表示,在工業互聯網和數字化進程里,不是單一企業可以獨自完成所有工作的。比如在大數據分析上,雙環獲得了中科院在技術上的支持,在工業互聯網建設上得到了浙大計算機研究院的協助,企業精益管理上則有哈博特的建議。
做一個全世界最好的齒輪制造工廠
去年 11 月,雙環傳動位于浙江臺州的新能源汽車零部件工廠,被浙江省評為“未來工廠”。可以說,這是其數字化與精益化融合成果的“集大成者”。
據介紹,該“未來工廠”項目以雙環傳動本部六分公司為建設點,占地面積 24000 平方米,總投資高達 4.2 億元。未來工廠項目的年產能達 150 萬套新能源汽車齒輪,年銷售額 9.6 億元,人均年產值超 150 萬元。
“當時建廠時,我們的出發點就是要做一個全世界最好的齒輪制造工廠。而衡量‘最好’的關鍵標準之一,就是生產出能夠滿足市場精度需求的產品。”李水土指出。
如今,在這個工廠里,平均每 20 秒就會有一個齒輪產品被生產出來,整個生產過程都實時在線上記錄和呈現,實現了可管可控。并且加工精度最高達到了 2μm(1μm 相當于頭發絲直徑的 1/60),適用轉速最高達 19000rpm(燃油車轉速平均 3000rpm-6000rpm),突破國際短板。
李水土介紹道,未來工廠從投入到量產大概用了近一年時間,項目采用“1+5”的新模式,即一個企業智能大腦 + 數字化設計、智能化生產、安全化管控、數字化管理、綠色制造五大平臺。技術層面以 5G、邊緣計算、工業物聯網、數字孿生、大數據與人工智能等新一代信息技術為支撐,達到 IT、ET、OT 的高度融合。
“背后的這套邏輯和思路在工廠籌建之初的論證階段,就已經有了基本雛形,但是在工廠建完之后,我們還會回頭進行復盤,重新審視哪些地方還可以進一步完善,并形成文檔,讓后來的員工也可以通過文檔進行學習。”
李水土總結了雙環傳動未來工廠項目在實施過程中的四大策略牽引:
以精益驅動、實現卓越運營。運用精益思想,采用數字化手段,分析現狀、確立目標、制定改善、確認效果、固化標準,構建結構化、可持續改進的閉環管理。
全面實現自動化。尤其在生產上突破現有效率瓶頸。基于工藝流程的自動化單元建設,并與物流系統對接,實現物料、工裝夾具、刀具等自動更換。
數據流通流程管理引擎。以全業務流程優化為目標的全面信息化建設,業務主導數據流程,數據反推業務進步。
橫向拉通,縱向協同,全面連全通。內部各生產單元之間實現全局資源分配、產品的全生產周期管理。面向供應商,實時數據共享,實現外協能力、工廠計劃、資源的實時協同,以實現準時交付。
“一把手工程”是從董事長到部門長所有一號位的責任
在十多年的數字化轉型探索歷程里,雙環傳動無可避免面臨過一系列挑戰和經驗教訓。其中,李水土認為有兩大挑戰是最棘手的。
首先是確保數字化策略與企業戰略的一致。數字化領域近些年涌現了許多新概念、新思路和領先的技術。然而,在缺乏深入理解的情況下,業務團隊可能不熟悉數字化領域的具體技術和應用場景,因此可能盲目追求聽起來很好的名詞。
比如雙環傳動曾經推進一個 APS 項目(自動排程系統),被“自動排程”這個概念吸引后就匆忙上項目,上完后卻發現這個概念與自家的業務場景融合效果不好,反而增加了工作量,導致項目失敗。
李水土坦言,這樣的案例并不罕見,數字化轉型的成功與否在很大程度上依賴于業務的融合。如果業務無法與數字化概念相融合,就會導致失敗。
第二,人才匹配也是關鍵因素。傳統制造型企業中缺乏數字化人才,這些人才需要同時了解制造、業務和數字化流程。因此,招聘和培養這些人才是另一大挑戰。
這些年,雙環傳動主要通過培訓、輪崗和擴招人才等舉措應對數字化人才短缺的難題。目前,雙環傳動已經有專門負責推動數字化建設的人才,包括軟件開發人員、產品經理以及執行各種數字化項目的團隊成員,一共有 60 多人。
但對于公司老員工而言,轉型和變革往往會觸及到部分利益,這可能導致他們不愿意接受改變。“40 年經驗,是好事情也是壞事情,這使得數字和業務的融合是個挑戰。有時候要打破固有的習慣和觀念。”
比如,在中國制造型企業中,許多部門長可能已經年過四十。這些人面臨數字化有可能會感到擔憂和不安,但如果他們不愿改變,整個部門的數字化轉型也將受到阻礙。
李水土強調,“但數字化是大勢所趨,一定要轉變他們的觀念,讓大家意識到不做數字化就沒有效率,同時要相應地制定一些新的‘規則’,讓更多人接受和擁抱數字化。”
在他看來,要解決以上問題,關鍵在于把數字化轉型視為“一把手工程”,但值得一提的是,“一把手工程”不僅僅是董事長或總經理的責任,而需要從董事長到每個業務部門的一號位部門長等更多一把手角色的廣泛參與。
總結而言,一方面,從公司的集團層面來看要明確數字化戰略,明確在幾年內要達到什么目標,這需要有清晰的認知,以及對資源投入的決策;另一方面,還需要中層部門領導對部門的傳統業務進行梳理,使其更加規范、合乎邏輯,并通過數字化手段將部門內積累的豐富經驗轉化為可見、可觸摸的知識,然后將這一知識沉淀到系統中,從而實現數字化轉型。
寫在最后:數字化是傳統制造業的再生力量
數字化不是顛覆的力量,而是一種再生的力量,能實現傳統產業的再生,使傳統的制造業不斷提升創造價值的能力。
在近三年時間里,雙環傳動公司每年用于數字化轉型的硬件和軟件以及人才投入大致在 3000 萬元左右。
李水土直言,數字化的投入和回報是一個從隱性到顯性的過程,一開始肯定是投入大于回報,要實現質的飛躍,通常需要三到五年的時間。因此在前期,內部可能只是逐步解決一些具體的問題,點對點地改進,雖然沒有整體效益的明顯改變,但也有立竿見影的效果,比如設備的效率會立即提高,或者質量管理得到改善,穩定性和平均質量水平都有所提高。
整體來看,雙環傳動未來工廠在過去三年里的整體綜合降本累計 5500 萬元,在設備利用率、產品研制周期和產品生產效率、能源利用率等指標上獲得 20%~30% 的提升。
“看了我們工廠以后,很多人都會有很多的想法,其實制造可以用換種眼光去看,工廠可以想象成另外一種工廠去做。制造還是很有前途的,數字化是傳統制造業的再生力量。”李水土感慨道,很多企業家常說企業很難辦、很操心,苦惱怎么樣才能讓制造更簡單一點,讓制造更高效,對雙環傳動來說,唯一的答案就是數字化轉型。
-
新能源汽車
+關注
關注
141文章
10427瀏覽量
99284 -
自動化
+關注
關注
29文章
5519瀏覽量
79124 -
數字化
+關注
關注
8文章
8628瀏覽量
61648
原文標題:A0級以上新能源汽車市占率60%,全球齒輪制造大廠的數字化實踐
文章出處:【微信號:AI前線,微信公眾號:AI前線】歡迎添加關注!文章轉載請注明出處。
發布評論請先 登錄
相關推薦
全球新能源汽車市場快速增長,2024年前八月銷量占比達16.1%
中國新能源汽車7月滲透率首次突破50%
工業路由器在新能源數字化中的應用:重塑能源行業的未來
全面推進新能源產業數字化提質,微創軟件再獲殊榮
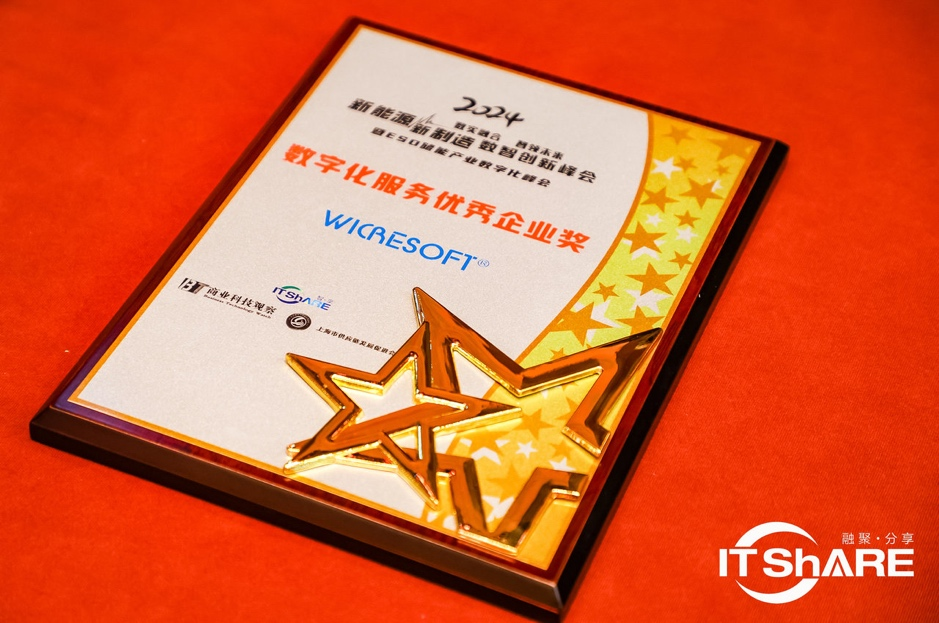
評論