本文介紹了三種SMT(Surface Mount Technology,表面貼裝技術)焊接工藝,包括回流焊、波峰焊、通孔回流焊。
一、回流焊(Reflow Soldering)
1.定義
通過加熱融化預先涂布在焊盤上的焊錫膏,實現預先貼裝在焊盤上的電子元器件引腳與焊盤電氣互聯,以達到將電子元器件焊接在PCB板上的目的。
具體來說,回流焊是將元器件焊接到PCB板材上,對表面貼裝器件進行焊接。它通過依靠熱氣流對焊點的作用,使膠狀的焊劑在一定的高溫氣流下進行物理反應,從而達到焊接SMD(表面貼裝器件)的目的。
回流焊的焊接全部流程如下:
2.回流焊的焊接順序
單面回流:預涂錫膏→貼A面→過爐流焊→上電測試
雙面回流:預涂A面錫膏→貼片→過爐回流焊→涂抹B面錫膏→過爐回流焊→上電檢測。
原則上先小器件后大器件,先低重量后高重量。如需烘烤的器件需按照烘烤溫度、時間要求進行爐前烘烤。
3.回流焊的結構
回流焊分為升溫區(預熱區,Pre-heat zone)、吸熱區(Soak zone)、回流區(回焊區,Reflow zone)、冷卻區(Cooling zone)。
預熱區:其目的是將印刷線路板的溫度從室溫提升到錫膏內助焊劑發揮作用所需的活性溫度(135℃以上),溫區的加熱速率應控制在每秒 1~3℃,時間為90s左右。
在預熱區,焊膏中的溶劑、氣體蒸發掉,同時,焊膏中的助焊劑潤濕焊盤、元器件端頭和引腳,焊膏軟化、塌落、覆蓋了焊盤、元器件端頭和引腳與氧氣隔離。
吸熱區:其目的是將印刷線路板維持在某個特定溫度范圍并持續一段時間,使印刷線路板上各個區域的元器件溫度相同,減少他們的相對溫差,并使錫膏內部的助焊劑充分發揮作用,去除元器件電極和焊盤表面的氧化物,從而提高焊接質量。進入保溫區時,PCB和元器件得到充分的預熱,以防PCB突然進入焊接高溫區而損壞PCB和元器件。
一般普遍的活性溫度范圍是 135-170℃,時間通常在60-90s區間,保溫區不超過217℃。如果活性溫度設定過高會使助焊劑過早失去除污的功能,溫度太低助焊劑則發揮不了除污的作用?;钚詴r間設定的過長會使錫膏內助焊劑的過度揮發,致使在焊接時缺少助焊劑的參與使焊點易氧化,潤濕能力差,時間太短則參與焊接的助焊劑過多,可能會出現錫球,錫珠等焊接不良。從而影響焊接質量。
回流區:其目的是使印刷線路板的溫度提升到錫膏的熔點溫度以上并維持一定的焊接時間,使其形成合金,完成元器件電極與焊盤的焊接。在回流區時,溫度快速上升使焊膏達到熔化狀態,液態焊錫對PCB的焊盤、元器件引腳潤濕、擴散、漫流或回流混合形成焊錫接點→PCB進入冷卻區,使焊點凝固。此時完成了回流焊。
回流溫度通常在 183℃以上(有鉛錫膏<錫和鉛>熔點183℃,無鉛錫膏<錫、銀和銅>熔點217℃),時間30-90s。爐溫可設置,回流焊爐溫與選用的錫膏類型有關,一般最高不高于260℃?;亓鲿r間如果不足,會使錫層較薄,焊點的強度不夠,時間較長則錫層較厚使焊點較脆。
冷卻區:其目的是使印刷線路板降溫、焊點凝固,通常設定為每秒 3-4℃,時間為70秒左右。如速率過高會使焊點出現龜裂現象,過慢則會加劇焊點氧化。理想的冷卻曲線應該是和回流區曲線成鏡像關系,越是靠近這種鏡像關系,焊點達到固態的結構越緊密,得到焊接點的質量越高,結合完整性越好。
4.回流焊爐溫曲線(SN63PB37有鉛錫膏)
二、波峰焊(Wave Soldering)
1.定義
波峰焊用于焊接雙列直插封裝(DIP)類型的器件。
波峰焊利用電動泵或電磁泵噴流成設計要求的焊料波,將熔融的液態焊料在焊料槽液面形成特定形狀的焊料波;最后PCB上的插裝器件通過傳送鏈以特定的角度和浸入深度穿過此焊料波峰而實現焊點焊接的過程。
2.波峰焊的結構
波峰焊機主要由噴霧系統、預熱系統、焊接系統、冷卻系統、運輸系統組成。
運輸系統:將電路板固定在治具后,通過傳送鏈將治具送入波峰焊機,并在過程中平穩運送PCB。運輸系統由傳送帶與馬達、調速器組成。傳送鏈有個傾斜角度,其目的是為了方便脫錫,角度越小,焊點越大。
噴霧系統:為待焊接的DIP器件焊接區添加助焊劑,常用發泡劑、噴霧等。噴霧系統由光電傳感器、桿氣缸、噴霧器(噴頭)、PLC組成。
預熱系統:由發熱管組成,目的是提供足夠的溫度,以便形成良好的焊點。預熱時間通常<3min。
焊接系統:市面上應用最普遍的是雙波峰系統。
在雙波峰系統中,波的湍流部分能夠防止虛焊,它保證穿過電路板的焊料分布適當,焊料以電路板行進的相同方向、較高速透入窄小間隙。僅湍流波本身并不適合焊接元件,它給焊點上留下不平整和過剩的焊料,因此需要第二個波。第二個波為層流波或平滑波,能夠消除了由湍流波產生的毛刺和焊橋。層流波實際上與傳統的通孔插裝組件使用的波一樣,因此,當傳統組件在一臺機器上焊接時,就可以把湍流波關掉,用層流波對傳統組件進行焊接。波峰焊的焊接時間=波峰寬度/運行速度,通常<5s。
冷卻系統:使用外部降溫設施,對完成焊接后的PCB冷卻,減少電子器件熱應力,并提高焊點的可靠性。
3.波峰焊的特點
省工省料,相比手工焊接,提高了生產效率,降低了生產成本。
電路板接觸高溫焊錫時間短,可以減輕電路板的翹曲變形。
消除了人為因素對產品質量的干擾和影響,提高了焊點質量和可靠性。
波峰焊機的焊料充足,有利于提高焊點質量。
三、回流焊與波峰焊的區別
1.焊接設備不同
回流焊與波峰焊使用不同的機器完成焊接。
2.焊接工藝、流程不同
回流焊工藝是通過設備內的循環氣流融化焊料,在進回流爐前需要先隔著鋼網,涂抹錫膏(要求涂抹均勻,保證受熱均勻),進爐后融化基板上的錫膏后,實現器件與焊錫的接觸;而波峰焊是通過加熱機器內部的焊條,使器件與焊料(液態錫)接觸后進行焊接。
3.適用范圍不同
回流焊為SMT貼裝工藝,適用于SMD貼裝器件;波峰焊屬于DIP插件工藝,適用于插裝器件。
4.焊接順序不同
先回流焊后波峰焊。通常貼裝器件的尺寸小于插裝器件,線路板組裝按照從小到大的順序完成焊接。雙面貼裝器件完成貼片后,制作工裝治具固定單板,并遮蓋貼裝器件,進爐,實施波峰焊。
一般貼裝器件的焊盤與插裝期間的焊盤邊緣間距要求≥2.5mm。出于成本考慮,一般將插裝器件的焊接面放在同一面,一次過爐。
四、通孔回流焊(PIHR,Pin-in-Hole Reflow)
1.定義
通孔回流焊工藝并不常用,它是指把有電子元器件的引腳插入填滿錫膏的插件孔中,并且使用回流焊的工藝,可實現對通孔器件和表面貼裝元件同時進行回流焊。再通過回流焊接制程,將通孔件和SMT表貼器件過一次回流同時焊接到PCB板上。
2.主要特點
相比波峰焊,通孔回流焊具有以下優勢:
PCB板面干凈,外觀明顯比波峰焊好。
簡化了工序、降低了勞動強度。
虛焊、連錫等焊接缺陷少,修板的工作量減少。
波峰焊特別適用于表面貼裝器件很多而插裝器件特別少的場景。但要實現通孔焊回流焊,插裝器件須滿足以下要求:
耐熱材料。多數通孔焊接器件是為波峰焊接設計,只需要在底部承受不超過150℃(電路板溫度)的高溫小于3S(錫點250℃左右)。但通孔回流焊接需要器件承受260℃大于等于10S。絕緣體材料必須能夠承受有鉛和/或無鉛回流焊的高溫。
焊腳長度。焊點外觀的關鍵影響因素之一,推薦焊腳超出板面長度不超過1.5mm。太長會把錫膏推出太遠,無法潤濕回位,也需求更多的錫量形成潤濕角。太短,如不超出板面也不利于焊點形成潤濕角,影響外觀檢驗判斷。
焊腳良好的潤濕性。插件針腳優選鍍錫,銅鍍、1U金不利于潤濕回位。
需足夠的空間給錫膏印刷。器件的塑膠部分懸空高度=印刷錫膏厚度+0.15mm。因為通常會根據PCB孔徑、焊環寬度加大開口,以保證回流焊接后通孔內有足夠的焊料填充。當加大鋼網開口后,熔融的焊料回縮時不能受阻擋。也就是開口大。
適合自動貼片。包裝方式滿足全自動貼片機自動供料條件,總高度不超過16mm。如不滿足需手工放料。
引腳周圍的垂直和水平間隙必須足夠大,以提供足夠的印刷錫膏的空間。該垂直和水平空間需要允許熔融漿料從PCB表面無阻礙地轉移到電鍍通孔中。
審核編輯:湯梓紅
-
電子元器件
+關注
關注
133文章
3311瀏覽量
104987 -
smt
+關注
關注
40文章
2885瀏覽量
69068 -
焊接工藝
+關注
關注
3文章
84瀏覽量
13022 -
回流焊
+關注
關注
14文章
461瀏覽量
16724 -
波峰焊
+關注
關注
12文章
306瀏覽量
18595
原文標題:SMT焊接工藝介紹
文章出處:【微信號:海馬硬件,微信公眾號:海馬硬件】歡迎添加關注!文章轉載請注明出處。
發布評論請先 登錄
相關推薦
回流焊 VS波峰焊
通孔回流焊簡述
一分鐘教你如何辨別波峰焊和回流焊
波峰焊和回流焊順序
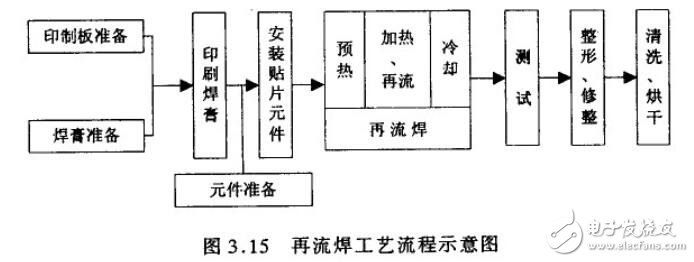
評論