wafer--晶圓
wafer即為圖片所示的晶圓,由純硅(Si)構(gòu)成。一般分為6英寸、8英寸、12英寸規(guī)格不等,晶片就是基于這個wafer上生產(chǎn)出來的。晶圓是指硅半導(dǎo)體集成電路制作所用的硅晶片,由于其形狀為圓形,故稱為晶圓;在硅晶片上可加工制作成各種電路元件結(jié)構(gòu),而成為有特定電性功能的集成電路產(chǎn)品。
die--晶粒Wafer上的一個小塊,就是一個晶片晶圓體,學(xué)名die,封裝后就成為一個顆粒。晶粒是組成多晶體的外形不規(guī)則的小晶體,而每個晶粒有時又有若干個位向稍有差異的亞晶粒所組成。晶粒的平均直徑通常在0.015~0.25mm范圍內(nèi),而亞晶粒的平均直徑通常為0.001mm數(shù)量級。
chip--芯片一片載有Nand Flash晶圓的wafer,wafer首先經(jīng)過切割,然后測試,將完好的、穩(wěn)定的、足容量的die取下,封裝形成日常所見的Nand Flash芯片(chip)。芯片一般主要含義是作為一種載體使用,并且集成電路經(jīng)過很多道復(fù)雜的設(shè)計工序之后所產(chǎn)生的一種結(jié)果。
wafer、chip、die的關(guān)系好比下面這張圖
什么是芯片?
通俗點(diǎn)來說,芯片就是把一個電路所需的晶體管和其他器件制作在一塊半導(dǎo)體上。通常情況下半導(dǎo)體所應(yīng)用到的材料就是單晶硅(Monocrystalline Silicon),如果要制造用于處理元宇宙數(shù)據(jù)的高性能芯片,那么單晶硅的純度需要達(dá)到99.99999999999%以上。如圖所示,芯片最初的材料便是這一塊一塊的單晶硅硅錠了。
生產(chǎn)芯片的原料——單晶硅硅錠
我們不可能在這么大的硅錠上制作芯片,于是晶圓廠將硅錠按照要求裁切成一個一個的圓片,圖中那個大大的圓片便是我們說的晶圓(Wafer),而放大的部分里面包含著復(fù)雜的線路圖,這些獨(dú)立的結(jié)構(gòu)單元稱為chips,在某些場合下,芯片也指代chips。
晶圓以及圓上的chips
芯片的制造工藝
在半導(dǎo)體界有這么一種說法,“如果將制造核彈的難度設(shè)定為1,那么制造芯片的難度可能是100,制造高性能芯片的難度可能是10000。”為什么這么說呢?我們首先來看一張制造芯片的流程簡圖:
是不是已經(jīng)被嚇到了?注意,這還是一張簡圖,實(shí)際上芯片制造分為前道工藝和后道工藝,每一段工藝又分為幾十甚至上百道工序,中間只要一個環(huán)節(jié)走不通,那都是半途而廢。最后,為了讓大家能看得清楚一些,筆者將上述的圖再簡化如下所示:
芯片制造簡圖
通過上述的圖片,我們已經(jīng)初步了解了制造一枚芯片的流程,芯片制造的困難不僅僅包括設(shè)備,同時也包括材料方面的問題。接下來,筆者分別介紹芯片制造中所用到的重要材料。
單晶硅,制備芯片結(jié)構(gòu)的襯底
沒有高純度的單晶硅,就不要提芯片,更不用說構(gòu)建一個元宇宙的虛擬世界了。作為地球上第二豐度的元素,硅廣泛地存在于自然界當(dāng)中。它成本低廉,溫度穩(wěn)定性好,穿透電流低,如此優(yōu)異的性能使它代替鍺,成為了半導(dǎo)體的主流材料。
單質(zhì)硅主要有單晶、多晶以及非晶硅三類形態(tài),后兩種形態(tài)缺陷太多,若用于芯片制造,在加工過程中會引起基材的電學(xué)以及力學(xué)性能變差,因此只能用高純的單晶硅作為芯片的基元材料。
硅單質(zhì)的三種形態(tài)
然而自然界中別說單晶硅,就連硅單質(zhì)也是不存在的,硅元素主要以硅酸鹽以及硅的氧化物形式存在,想從原料中獲取單晶硅并不是一個簡單的過程,要經(jīng)過西門子法提純以及CZ法制備單晶硅兩大步驟,這兩大步驟具體包括:二氧化硅原料→金屬硅→HCl提純→氫氣還原→多晶硅→熔融→拉制單晶硅→切片。
首先,利用焦炭,在1500℃的條件下,將二氧化硅原料還原成金屬硅,此時的金屬硅純度僅僅為97%,具有雜質(zhì);隨后,利用氯化氫(HCl)在300℃的低溫下將金屬硅變?yōu)?span style="color:rgb(230,46,46);">三氯硅烷,而氯化氫也會將金屬硅中的雜質(zhì)溶解,由于雜質(zhì)和三氯硅烷蒸汽壓較大的差異,此時,雜質(zhì)的氯化物會受熱蒸發(fā),硅的純度得到進(jìn)一步提高。
接下來,利用高純度氫氣將高純度的三氯硅烷通入爐中,在1100℃的高溫下,爐子內(nèi)部的硅芯棒上會逐漸長出多晶硅晶體,此時多晶硅的純度可達(dá)99.999999999%。
西門子法制備高純多晶硅
最后一步便是利用多晶硅制備單晶硅,首先將多晶硅加熱熔化,隨后加入單晶硅的籽晶(Seed),觸碰多晶硅的熔體,此時界面處的硅便會沿著同一個晶面方向生長,通過調(diào)控合適的工藝參數(shù),便可得到硅單晶棒。
CZ法制備單晶硅流程
單晶硅硅棒經(jīng)過打磨,拋光,外延,切片等工藝,就形成晶圓了。別急,這只是做芯片的第一步。
光刻膠,轉(zhuǎn)印芯片電路的媒介
當(dāng)制備好的晶圓經(jīng)過氧化處理后,便進(jìn)入了芯片前道工藝的光刻工序,大家應(yīng)該都知道光刻機(jī),如果將光刻機(jī)比作芯片行業(yè)的引擎,那么光刻膠就是助推引擎的燃料。
光刻流程簡圖
光刻膠就是圖中橙色的部分,也有人將其稱為光阻劑。光刻膠分為正膠和負(fù)膠,正膠經(jīng)過曝光后會溶解于顯影液,負(fù)膠則是相反的。按照曝光光源的波長分類,光刻膠分為g線,i線,KrF,ArF以及EUV光刻膠,由左到右,光刻膠對應(yīng)的曝光波長逐漸變短,先進(jìn)的EUV光刻膠對應(yīng)曝光波長只有13.5nm,可用于10nm以下的芯片制程,但目前EUV光刻機(jī)只有荷蘭ASML能制造。
光刻膠分類
光刻膠的組分一直是國外廠商的機(jī)密,很難通過逆向解析的手段還原。一般而言,光刻膠的組分包括光引發(fā)劑,樹脂基體,單體以及助劑。當(dāng)光刻膠經(jīng)過紫外光照射后,發(fā)生一系列的物理化學(xué)變化,電路圖形就從掩膜版上轉(zhuǎn)移到光刻膠上面,經(jīng)過刻蝕后,晶圓片上就形成了對應(yīng)的圖案。
光刻膠反應(yīng)機(jī)理簡圖
我國目前28nm工藝制程使用的光刻膠為KrF型號,目前正在積極開發(fā)ArF型光刻膠,而更為高端的產(chǎn)品已經(jīng)被美國與日本所壟斷。
成膜,分隔芯片結(jié)構(gòu)的骨架
經(jīng)過刻蝕,我們已經(jīng)得到了芯片的基本平面形貌,為了防止各個器件之間的干擾,同時賦予芯片三維結(jié)構(gòu),我們就需要薄膜(<1μm)沉積工藝。
芯片薄膜沉積工藝
薄膜沉積工藝分為化學(xué)氣相沉積(CVD)以及物理氣相沉積(PVD)兩種方式。
典型的CVD工藝是將晶圓(基底)暴露在一種或多種不同的前驅(qū)物下,在基底表面發(fā)生化學(xué)反應(yīng)或化學(xué)分解來產(chǎn)生所需的沉積薄膜。CVD 的基本流程如圖所示:
CVD基本流程
上述的流程包括反應(yīng)物傳輸,先驅(qū)體反應(yīng),氣體擴(kuò)散,襯底吸附,CVD主要用在芯片的氮化層成膜。而PVD的方式包括蒸鍍與濺射,主要用于芯片的金屬層,目前多用離子濺射的方式成膜。離子濺射的基本原理是通過氣體等離子轟擊靶材,將靶材原子“打”出來,并使它沉積在襯底上成膜。
PVD基本流程
封裝,連接芯片電路的外衣
封裝屬于后道工藝,但也是至關(guān)重要的一步。芯片封裝是半導(dǎo)體開發(fā)的最后一個階段,不僅僅是為了保護(hù)芯片的內(nèi)部結(jié)構(gòu)和提高芯片的性能,更是為芯片內(nèi)部結(jié)構(gòu)與外部電路建立了一道溝通的橋梁。
2.5D芯片封裝工藝
芯片的封裝材料主要包括封裝基板、引線框架、鍵合絲、塑封料等四類材料。這四類材料的市場份額在芯片封裝材料里占70%以上。
封裝材料市場占有率
封裝基板是芯片的內(nèi)外承載和保護(hù)結(jié)構(gòu)。對于高端芯片,會選擇環(huán)氧樹脂,聚苯醚樹脂,聚酰亞胺樹脂作為基板材料,相比于金屬基板和陶瓷基板,有機(jī)基板具有密度小,生產(chǎn)成本低以及加工簡單的優(yōu)勢。而引線框架則是連接內(nèi)外電路的媒介,它需要較高的導(dǎo)電導(dǎo)熱性能,一定的機(jī)械強(qiáng)度,良好的熱匹配性能,同時環(huán)境穩(wěn)定性要好。一般采用銅基引線框架材料。鍵合絲是芯片內(nèi)部與引線框架的內(nèi)引線,對于高端產(chǎn)品而言,要求化學(xué)穩(wěn)定性和導(dǎo)電率更高,因此高端芯片一般采用鍵合金絲作為鍵合材料,但是缺點(diǎn)是成本過高,因此在一些較為低端的產(chǎn)品,一般用鍵合銀絲以及鍵合銅絲。塑封料則是對芯片和引線架構(gòu)起保護(hù)作用。塑封料有金屬,陶瓷,高分子塑封料三種方式。相比于前兩者,高分子環(huán)氧塑封具有低成本,小體積,低密度等優(yōu)點(diǎn),目前絕大多數(shù)的集成電路都采用高分子環(huán)氧塑封。
封裝材料示意圖
展望
在經(jīng)過封裝測試之后的其它工藝,一枚小小的芯片就這么誕生了。強(qiáng)大的算力是支持元宇宙運(yùn)行的基礎(chǔ),根據(jù)半導(dǎo)體的摩爾定律:
集成電路上可以容納的晶體管數(shù)目在大約每經(jīng)過18個月到24個月便會增加一倍。換言之,處理器的性能大約每兩年翻一倍,同時價格下降為之前的一半。
但是隨著芯片制成的不斷縮小,甚至到現(xiàn)在網(wǎng)傳的1.4nm,摩爾定律的適用性在面臨挑戰(zhàn)。那么,我們不禁要問,能否在原材料上有所突破呢?答案是肯定的,科學(xué)家們曾經(jīng)說石墨烯是下一代芯片材料,但是石墨烯的量產(chǎn)與提純又是一大問題。近期,科學(xué)家們發(fā)現(xiàn)二維二硫化鉬這種新型半導(dǎo)體:
二硫化鉬結(jié)構(gòu)圖
相比于單晶硅,它具有的優(yōu)勢:
- 沒有單晶硅表面的“懸掛鍵”,性能比單晶硅更穩(wěn)定;
- 很薄,單層的二硫化鉬只有6.5埃的厚度,比現(xiàn)在的3nm制程小了5倍,芯片的制程可以進(jìn)一步縮小,獲得更高的算力;
- 若能批產(chǎn),可以減少芯片的制作流程。
但是,需要說明的是,作為一種二維材料,它與石墨烯一樣很難穩(wěn)定批產(chǎn),這就需要材料學(xué)家進(jìn)一步去探索新的制備工藝和新的合成方法了,希望那一天能夠早日到來。
先進(jìn)封裝開始嶄露頭角,以蘋果和臺積電為代表,開啟了一場新的革命,其主要分為兩大類,一種是基于XY平面延伸的先進(jìn)封裝技術(shù),主要通過RDL進(jìn)行信號的延伸和互連;第二種則是基于Z軸延伸的先進(jìn)封裝技術(shù),主要通過TSV進(jìn)行信號延伸和互連。前者為2D先進(jìn)封裝,代表為FOWLP和FOPLP等,而后者即為3D封裝,代表為SoIC和Foveros等,目前還有兼具兩種封裝特點(diǎn)的2.5D封裝,代表為CoWoS和EMIB等。
目前3D 封裝大多應(yīng)用于提升HPC 芯片的性能,常見于HBM與CPU、GPU、FPGA、或NPU 等處理器彼此間的芯片整合。如臺積電提出的SoIC 整合封裝架構(gòu),其主要利用W2W 及C2W 的混合鍵合技術(shù),實(shí)現(xiàn)10um 以下I/O 節(jié)點(diǎn)互連、減少寄生效應(yīng)、并使芯片更薄等優(yōu)勢。
三星則于2020 年推出名為X-Cube 的3D 封裝技術(shù),將4 顆SRAM 堆疊在邏輯核心運(yùn)算芯片上,并通過TSV 結(jié)構(gòu)進(jìn)行連接。
英特爾于2018 年底推出名為Foveros的3D 邏輯芯片封裝技術(shù),通過TSV 與Micro Bumps 將不同芯片以Face-to-Face 方式堆疊連接,目前Foveros 技術(shù)能使凸點(diǎn)間距達(dá)到50um,未來有望縮減到10um,讓凸點(diǎn)數(shù)量達(dá)到每平方毫米10,000 個。
在這幾種封裝方式里,其主要目的都是將不同類型的芯片,通過3D立體堆疊的形式整合在一起,從而實(shí)現(xiàn)高性能、小體積、低耗電等目標(biāo)優(yōu)勢,也即異構(gòu)集成。
混合鍵合革命
封裝中最早采用的引線鍵合(Wire Bonding),由于其接點(diǎn)僅能以周列形式排列在芯片周圍,接點(diǎn)的I/O 數(shù)量有限,而IBM 提出的倒裝接合(Flip Chip Bonding),利用焊錫微凸塊(Solder Bump)當(dāng)作接點(diǎn)將芯片與芯片接合在一起,接點(diǎn)為陣列式排列,可以分布于整個芯片上,可以提高接點(diǎn)I/O 數(shù)量,不過這項技術(shù)在 50μm 或 40μm 的間距時表現(xiàn)尚可,人們很快發(fā)現(xiàn),這種方式由于熱膨脹不匹配,會出現(xiàn)翹曲和芯片移位。
事實(shí)上,微凸塊一旦做到 10 微米以下的間距時,暴露的問題就愈發(fā)增多,當(dāng)凸塊結(jié)構(gòu)較大時,電鍍微凸塊高度的極小不均勻性或回流焊過程中的變化可能可以忽略不計,但對于細(xì)間距微凸塊,這些微小的變化可能會導(dǎo)致接合處形成不良,并影響電氣良率,最終導(dǎo)致晶粒和封裝出現(xiàn)缺陷。
銅─銅混合鍵合(Cu-Cu Hybrid Bonding)技術(shù)應(yīng)運(yùn)而生,將金屬接點(diǎn)鑲嵌在介電材料(Dielectric Material)之間,并同時利用熱處理接合兩種材料,利用銅金屬在固態(tài)時的原子擴(kuò)散來達(dá)到接合,故不會有Bridging 問題。銅制程是半導(dǎo)體業(yè)非常成熟的技術(shù),銅─銅接點(diǎn)的間距可以微縮到10μm以下,因此在1×1cm2 的晶片內(nèi),能夠制作出超過一百萬的接點(diǎn),因此金屬的直接接合變得非常重要。
混合鍵合此前在業(yè)界通常被稱為DBI(Direct Bond Interconnect,直接鍵合),20世紀(jì)80年代中期,Paul Enquist,Q.Y. Tong和Gill Fountain在三角研究所(RTI)的實(shí)驗室首次提出了這一技術(shù),2000年,三人成立了Ziptronix公司,并于2005年推出了一種稱為低溫直接鍵合互連 (DBI) 的技術(shù),這是混合鍵合的第一個版本。
它驗證了低溫直接鍵合(Direct Bond Interconnection, DBI)的可行性,首先準(zhǔn)備好晶片具有SiO 2(介電材料)與銅(接點(diǎn)金屬),此時銅部分將會有點(diǎn)略低于介電材料厚度,利用電漿(Plasma)做表面活化處理,將晶片面對面在室溫下進(jìn)行對位接合,由于凡德瓦力作用已具有一定的接合強(qiáng)度,接著在100℃ 下持溫讓SiO 2與SiO 2之間進(jìn)行縮合反應(yīng),形成強(qiáng)力共價鍵提高接合強(qiáng)度 。接著再將溫度提高到300℃ 至400℃ 持溫,此時由于銅金屬的熱膨脹系數(shù)較SiO 2來的大,銅表面將會碰觸在一起,并自然受到一壓應(yīng)力,促使銅接點(diǎn)進(jìn)行擴(kuò)散接合。
有研究學(xué)者指出,想要達(dá)到低溫鍵合,介電材料層與金屬層在經(jīng)過化學(xué)拋光研磨后造成的高度差異將會是關(guān)鍵,研磨液與研磨參數(shù)的選擇是導(dǎo)致不同厚度的主因,厚度差越小,便可于較低溫度使銅表面接觸并開始進(jìn)行接合。
混合鍵合與倒裝接合比,它帶來了三大新優(yōu)勢,第一為可以達(dá)到超細(xì)間距與超小接點(diǎn)尺寸,實(shí)現(xiàn)更高I/O 數(shù)量;第二,由介電材料接合取代底部填充劑,進(jìn)一步節(jié)省填充成本;第三,倒裝技術(shù)會讓芯片與基板或芯片片間存在約10 至30 μm的厚度,而混合鍵合幾乎沒有厚度,在多層堆疊的情況下可以大幅減少總體厚度。
目前銅─銅混合鍵合主要分為了三種方式,分別為最常見的晶圓到晶圓(W2W)工藝,芯片到晶圓(D2W)和芯片到晶圓(C2W)工藝,后兩種工藝目前還在研發(fā)當(dāng)中。
其中,W2W 雖然已經(jīng)實(shí)現(xiàn)量產(chǎn),但它對于上下芯片的大小限制須為一樣大小,否則將有區(qū)域浪費(fèi);D2W是將切割好的Die用臨時鍵合的方式粘到晶圓上,然后整片地和另一片產(chǎn)品晶圓整片鍵合再解鍵,這項技術(shù)容易累計誤差,且成本高,對Die的厚度變化范圍也有較高要求;C2W將切好的Die分別放置晶圓的對應(yīng)位置上,位置精度雖然提高且厚度變化要求不在嚴(yán)苛,但顆粒控制也是影響它繼續(xù)普及的問題。
2015年,發(fā)明混合鍵合技術(shù)的Ziptronix被Xperi收購,2019年,Xperi 完成了混合鍵合技術(shù)的最終專利布局,而在此之前,這項技術(shù)已經(jīng)授權(quán)給了包括索尼在內(nèi)的多家廠商。
從20世紀(jì)80年代的構(gòu)想,到2005年的初步驗證,再到2015年之后的技術(shù)授權(quán),混合鍵合歷經(jīng)三十余年,終于為先進(jìn)封裝鋪平了道路,解決了芯片廠商對封裝未來的最大疑慮,此后混合鍵合領(lǐng)域更是呈現(xiàn)出了一篇千帆競逐的景象。
群雄決戰(zhàn)封裝
2016 年,索尼首先將混合鍵合技術(shù)應(yīng)用在三星Galaxy S7 的背照式CMOS 影像傳感器(Backside-illuminated CMOS Image Sensor, BI-CIS)中,大幅提高了鏡頭解析度。目前索尼每年出貨數(shù)百萬個采用 6.3 微米間距混合鍵合技術(shù)的 CMOS 圖像傳感器,并堆疊了 3 個芯片,而其他公司采用的間距密度要低得多,出貨量也要小得多。
作為這項技術(shù)的急先鋒,索尼在2022年展示了 1 微米間距的面對面混合鍵合和 1.4 微米的背對背混合鍵合,而它之所以如此激進(jìn),就是希望通過這項技術(shù)繼續(xù)分解和堆疊圖像傳感器像素的功能,以此捕捉更多光線和數(shù)據(jù),將其轉(zhuǎn)化為實(shí)際的照片和視頻。
SK海力士最早將于2025年量產(chǎn)混合鍵合,并準(zhǔn)備將其用于HBM4產(chǎn)品,與現(xiàn)有工藝相比,混合鍵合提高了散熱效率并減少了布線長度,從而實(shí)現(xiàn)了更高的輸入/輸出密度,能夠把當(dāng)前的最大12層堆疊增加到 16 層。而SK 海力士 PKG 技術(shù)開發(fā)負(fù)責(zé)人Ki-il Moon 表示:“我們正在專注于該技術(shù)的開發(fā)(與混合鍵合相關(guān)),并且實(shí)際上已經(jīng)獲得了有意義的產(chǎn)量,該技術(shù)將于2025~2026年實(shí)現(xiàn)商業(yè)化。”
三星在2020年8月,就對外展示了其自己的3D封裝技術(shù)——X-Cube,全稱為“eXtended-Cube”,將SRAM層堆疊在邏輯層之上,允許多層超薄堆疊,其表示三星代工廠正在開發(fā)超細(xì)間距銅-銅混合鍵合,其已經(jīng)實(shí)現(xiàn)了小于 4微米的間距。
英特爾在2022年12月的IEEE國際電子器件會議上,宣布了全新的混合鍵合技術(shù),gaijishu將互連間距繼續(xù)微縮到3微米,英特爾實(shí)現(xiàn)了與單片式系統(tǒng)級芯片(system-on-chip)連接相似的互連密度和帶寬,與IEDM 2021上公布的成果相比,英特爾在IEDM 2022上展示的最新混合鍵合技術(shù)將功率密度和性能又提升了10倍。
此外,2002年6月,CEA-Leti 和英特爾宣布了一種全新的混合鍵合自對準(zhǔn)工藝,使用水滴的毛細(xì)力(capillary forces)來對齊目標(biāo)wafer上的die,該工藝有可能增加校準(zhǔn)精度以及每小時數(shù)千個芯片的制造吞吐量,采用取放工具后鍵合的最先進(jìn)的對準(zhǔn)是 1μm,最好的情況是 700nm,而新工藝提供低于 500nm 甚至小于 200nm 的后鍵合對準(zhǔn)。
imec高級研究員、研發(fā)副總裁兼3D系統(tǒng)集成項目主任Eric Beyne在IEDM的一篇論文中表示,目前imec的研究已經(jīng)證明了在7微米間距實(shí)現(xiàn)混合鍵合的可行性。imec官方表示,利用這項技術(shù),芯片之間或芯片與硅中介層之間的 3D 互連密度比現(xiàn)有技術(shù)高出十六倍以上其開發(fā)間距小至3μm且具有高公差拾放精度的芯片間混合鍵合。
臺積電無疑是混合鍵合的集大成者,其SoIC 封裝技術(shù)依靠混合鍵合,在芯片 I/O 上實(shí)現(xiàn)了強(qiáng)大的接合間距可擴(kuò)展性,實(shí)現(xiàn)了高密度的芯片到芯片互連,其鍵合間距從 10 微米以下開始,臺積電表示與目前業(yè)界最先進(jìn)的封裝解決方案相比,短芯片到芯片連接具有外形尺寸更小、帶寬更高、電源完整性和信號完整性更好以及功耗更低的優(yōu)點(diǎn)。此前,臺積電已經(jīng)展示了其第四代混合鍵合技術(shù)的研究成果,該技術(shù)可實(shí)現(xiàn)每平方毫米 100,000 個接點(diǎn)數(shù)量。
2021年底,AMD介紹了他們在服務(wù)器處理器上已采用的臺積電混合鍵合技術(shù),2022 年初,AMD宣布Ryzen 7 5800X3D 也采用了Hybrid Bonding 技術(shù),將7nm SRAM 疊接在7nm 處理器之上,銅─銅混合鍵合能提升200 倍的接點(diǎn)密度,而且每個訊號傳遞所需的能量降低至三分之一以下。
值得一提的是,國內(nèi)的長江存儲所推出的Xtacking架構(gòu),即采用了W2W的混合鍵合技術(shù),利用不同的工藝,先后制作Memory晶圓和CMOS晶圓,在后道制程中構(gòu)建兩者的觸點(diǎn)。通過混合鍵合,這些觸點(diǎn)被鏈接導(dǎo)通,Memory和CMOS在垂直方向?qū)崿F(xiàn)了互聯(lián)。
長江存儲官方表示,混合鍵合在3D NAND閃存上實(shí)現(xiàn)數(shù)十億根金屬通道的連接,隨著層數(shù)的不斷增高,基于晶棧Xtacking所研發(fā)制造的3D NAND閃存將更具成本和創(chuàng)新優(yōu)勢。
針對這一項新興技術(shù),設(shè)備廠商們也未能置身事外,混合鍵合作為一項后道工藝,其設(shè)備主要由德國的蘇斯(Karl Suss)和奧地利的EVG(EV Group)所提供,日本的佳能和三菱目前也有意發(fā)展該鍵合設(shè)備,但目前市占率和技術(shù)水平還和歐洲廠商有一定差距。
混合鍵合即是未來?
對于混合鍵合技術(shù)來說,目前最大的應(yīng)用方式依舊是以索尼為代表的堆棧式CIS,經(jīng)過數(shù)年的優(yōu)化后,目前CIS領(lǐng)域在利用這項工藝時可謂是得心應(yīng)手,未來也有望實(shí)現(xiàn)更大規(guī)模的量產(chǎn)。
而第二大應(yīng)用領(lǐng)域無疑是DRAM和NAND,我們可以看到三星、海力士和長江存儲等在這方面的積極布局,部分廠商已經(jīng)拿出了一定成果,可能在2025年,我們就能見到混合鍵合技術(shù)在該領(lǐng)域的量產(chǎn)落地。
而最后的應(yīng)用場景即以臺積電的SoIC技術(shù)為代表的3D先進(jìn)封裝,目前在AMD處理器上已經(jīng)實(shí)現(xiàn)量產(chǎn),未來蘋果也有望在MacBook所搭載的M系列處理器上采用這一技術(shù),其大規(guī)模投產(chǎn)可能也會在2025年左右。
芯片提升性能以往看制程,如今看封裝,封裝看向異構(gòu)集成,而異構(gòu)集成的過往難點(diǎn)就是鍵合,如今銅─銅混合鍵合日趨成熟,背后環(huán)環(huán)相扣的工藝就有望實(shí)現(xiàn)芯片性能的下一步飛躍,我們深信這一天已不再遙遠(yuǎn)。
-
半導(dǎo)體
+關(guān)注
關(guān)注
334文章
27010瀏覽量
216301 -
芯片材料
+關(guān)注
關(guān)注
0文章
9瀏覽量
8847 -
硅晶片
+關(guān)注
關(guān)注
0文章
74瀏覽量
15192
發(fā)布評論請先 登錄
相關(guān)推薦
led封裝和半導(dǎo)體封裝的區(qū)別
PCB半導(dǎo)體封裝板:半導(dǎo)體產(chǎn)業(yè)的堅實(shí)基石
半導(dǎo)體封裝材料全解析:分類、應(yīng)用與發(fā)展趨勢!
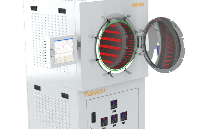
閑談半導(dǎo)體封裝工藝工程師
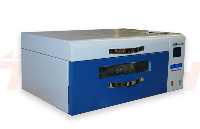
柳鑫實(shí)業(yè)總部大樓及半導(dǎo)體封裝新材料項目奠基儀式
半導(dǎo)體封裝工藝面臨的挑戰(zhàn)
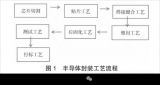
半導(dǎo)體封裝工藝的研究分析
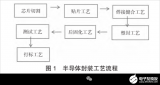
半導(dǎo)體后端工藝:封裝設(shè)計與分析
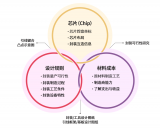
半導(dǎo)體先進(jìn)封裝技術(shù)
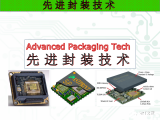
主要先進(jìn)封裝廠商匯總名單半導(dǎo)體材料與工藝設(shè)備
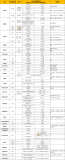
氮化鎵半導(dǎo)體芯片和芯片區(qū)別
半導(dǎo)體封裝的分類和應(yīng)用案例
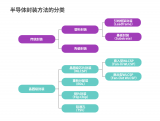
半導(dǎo)體封裝的作用、工藝和演變
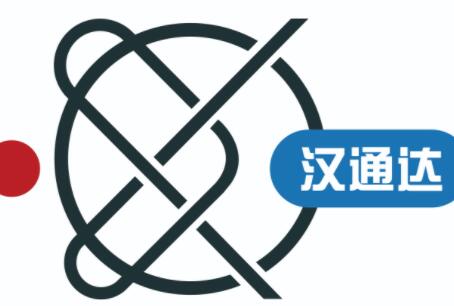
淺析現(xiàn)代半導(dǎo)體產(chǎn)業(yè)中常用的半導(dǎo)體材料
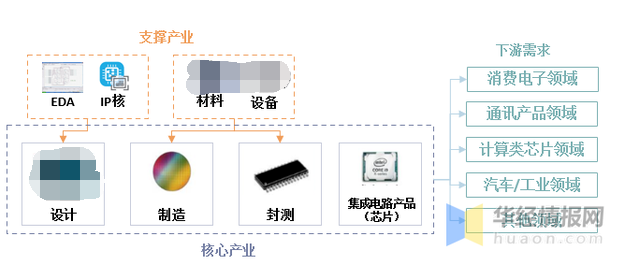
評論