1微流控技術
微流控技術(Micronuidics),或稱為芯片實驗室(1ab.on.a.chip),是把生物、化學等領域中樣品的制備、反應、分離、檢測等基本操作集成在一塊芯片上,在微納尺度下完成流體操控實現分析功能的一種技術平臺。通過分析儀器的集成化,微型化,可把實驗室中的分析儀器功能集成到幾個平方厘米大小的芯片上。微流控芯片主要以玻璃、硅片、高聚合物等材料作為基底,以微通道為網絡,將微泵,微閥,微電極,微反應器,檢測元件等功能器件像集成電路一樣集成在微芯片上。表1為不同材料的主要特性。圖2 為不同材料的微流控芯片材料對比。
表1 不同材料的主要特性參數對比
圖2 不同微流控芯片材料特性
以上述材料作為結構制作的載體,在載體上設計溝道、微結構、樣品池等單元,再使用入注射泵、蠕動泵等外圍裝置,最后選擇必要的設備并完成整體系統的搭建,以此來實現生物基因測序、細胞捕獲與分離、光學領域相關實驗檢測等功能。
微流控芯片設計與制作之前就需要考慮選擇合適的材料。能否高效率地制造出高品質的微流控芯片很大條件下取決于芯片材料的機械加工性能。另外材料的生物相容性、表面性質、光學性質、分子吸附性、絕緣性及化學惰性等性質也會影響芯片檢測性能。為滿足不同鄰域的使用要求,在選擇微流控芯片材料時需要考慮以下幾點要求,如圖3所示。
圖3微流控芯片選材依據
微流控芯片的商業化過程中,聚合物由于其成本更低,且制造工藝更簡單,同時,聚合物在生物相容性和靈活性方面更優,并且可以通過多種方法進行物理或者化學修飾。其越來越多的應用在微流控芯片的生產當中。常見的聚合物材料有聚甲基丙烯酸甲酯(PMMA)、聚二甲基硅氧烷 (PDMS)和聚碳酸酯(PC)等。
2 PMMA
PMMA 是一種長鏈高分子聚合物,因其具有高透明度,外觀材質又與玻璃相似,故被稱作有機玻璃,也常用作玻璃的替代品。PMMA 作為熱塑性材料的代表,具有較高的機械強度,耐高溫,透光性和親水性較好。PMMA 具有良好的光學性能,高達 92%的透光率使其廣泛應用于光學領域相關實驗檢測。
可以通過激光燒蝕(最廣泛使用的方法)、熱壓、數控加工和銑削等技術進行物理操作。且 PMMA 更易于表面功能化處理,比如親水性和疏水性處理,化學處理胺功能化等。采用較為傳統的加工方式,這樣也有利于降低生產成本,從而實現大批量地生產。具體的制備工藝流程如下。
1) 繪制芯片結構
在繪制微流控芯片結構過程中,會使用到一些常見的繪圖軟件,如 SolidWorks、AutoCAD 等,利用上述繪圖軟件設計并繪制出需求的 PMMA 微流控芯片結構。微流控芯片的結構設計通常包括了三種類型,分別是常規、含彎曲、含擋板通道結構。根據目標找出能夠順利實現目標效果的最簡結構,同時繪制過程也要考慮實際加工難度和可行性。必要時候可以提前研究流體在微通道中的流動、混合效果,以及能否順利流入微樣品池并排出廢液,以此來保證所設計的微流控芯片微通道尺寸的精準性。
2)切割、打孔、刻蝕
針對所設計的微流控芯片結構進行切割/打孔/刻蝕加工操作,此處詳細介紹打孔工藝操作,根據需要設置好打孔儀器的相關參數,固定好加工材料的位置,運行儀器即可對其進行操作。包括 PMMA 在內的玻璃類材料微流控芯片的打孔方式有多種,包括了金剛石打孔、激光打孔、超聲波打孔等。其中,金剛石打孔法所需要的設備較為簡單,并且加工過程所花時間較少,但是鉆頭質量對孔質量影響較大,并且難以滿足較精確的尺寸要求。相較金剛石打孔而言,激光打孔法打出的孔則較細、較深,孔徑大小通常為幾十微米甚至幾微米。但是激光打孔發也存在缺點,在打孔過程中所使用的溶膠微粒容易在微流控芯片材料上沉積,造成裂痕的產生。因此,在打孔之后必須進行拋光,以及超聲清洗。而超聲波打孔法打出的孔邊緣光滑整齊,最小孔徑尺寸在 200μm 左右,但是在封裝前也要嚴格清洗玻璃的表面,以去除殘留碎屑和雜質。具體的打孔方法選擇需要結合微流控芯片結構需求和實際工藝加工水平進行選擇。
3) 拋光、清洗
工藝中如果使用到上述的激光打孔法,則必須進行拋光和超聲清洗。通過打孔后的 PMMA 表面會殘留下有機物、無機顆粒和塵埃等雜質,這些雜質的存在將會直接導致微流控芯片表面的不平整、不均勻,以及粗糙程度不一致的情況。在打孔后續會進行鍵合操作,如果前期沒有進行拋光和清洗操作,那么結合界面容易產生衍射紋,這將直接導致鍵合過程的失敗。正確的操作是使用自動拋光機對微流控芯片的孔表面進行拋光處理,從而獲得平整的 PMMA 表面,然后再將其放置于超聲清洗機中進行超聲清洗。
4) 鍵合
微流控芯片的鍵合方法主要有直接鍵合、中間層鍵合兩種類型。直接鍵合包括熱鍵合法、陽極鍵合法等,熱鍵合法是將貼合在一起的基片放置在高溫爐中加熱后退火,界面上發生的化學反應使兩塊基片牢固鍵合在一起。直接鍵合法可以更加精準地對連接兩塊基片而不引入其它物質,但其工藝條件要求較高。中間層鍵合則是采用高分子材料作為粘結劑,粘連兩片基片,如 UV 膠、SU-8 光刻膠、AZ-4620 等。中間層鍵合法工藝簡單、價格低廉,但是工藝精度不高。
圖4 PMMA 微流控芯片工藝流程
3 PDMS
PDMS 由于制造成本低,透氣性好且具有高彈性,使其成為微流控芯片中最受歡迎的彈性材料,經常用于細胞培養和生化分析等領域。
PDMS 是有機聚合物中的一種透明軟質彈性材料,低自發熒光特性使其可以兼容熒光檢測。PDMS可以重復變形而不會發生永久性破壞,利用PDMS具有良好的彈性這一特質,可以設計制作出不同微結構的芯片,并且水、甘油、甲醇、乙醇等流體物質不會使微結構變形。PDMS 的透氣性也為細胞及各種微生物提供了良好的培養環境;除此之外,該聚合物無毒、成本低、制作簡單,能透過 300nm 以上的紫外光和可見光,是國內外研究者廣泛應用的芯片材料
微流控芯片的加工技術來源于集成電路、半導體行業的芯片加工,但微流控芯片工尺寸遠大于集成電路,芯片整體大小為平方厘米級,芯片微通道寬度為微米級。本小節將闡述實際實驗中所使用的 PDMS 微流控芯片的工藝流程,也是常見廣泛使用的加工方式,具體的制備工藝流程如下
1) 制備 PDMS 預聚體
將 PDMS 預聚物緩慢倒入塑料攪拌杯中,然后以預聚物與固化劑質量比為 10:1 的比例加入固化劑,并攪拌混合兩種物質,直到呈現唾液狀混合液為止,即為預聚體。為了避免 PDMS 預聚體中氣泡影響其固化效果,需要進行氣泡去除處理。將裝有 PDMS 預聚體中的攪拌杯置于真空干燥器中,利用儀器的真空泵進行抽氣抽濕,直到攪拌杯中 PDMS 預聚體氣泡基本消失。
2)加工制作模具
利用 SolidWorks、AutoCAD 等設計軟件設計并繪制好芯片三維結構后需要進行模具的制作,傳統模具加工技術基于光刻法制作硅片模具,可以實現微米級的通道寬度,因其對微加工技術條件要求較高,大多科研團隊都選擇委托其它公司或科研機構進行代加工。當微流控芯片結構復雜度不高、尺寸精度要求不大時,也可以選擇 3D打印技術制造的樹脂模具。常見的熔融沉積型 3D 打印機通過熱熔加熱融化熱塑型材料,再將軟化的材料按照設計的結構進行堆積,最終成型。
3)勻膠、倒膠、固化
將預聚體倒入培養皿并放置于勻膠機上,輔勻膠體。將攪拌均勻的預聚體倒入前期制作好的模具內,使用洗耳球輕吹去除 PDMS 表面氣泡,最后放置于真空干燥箱中加熱烘烤。
4)揭膜、切割、封閉
用手術刀沿著邊緣切下 PDMS 芯片,緩慢輕挑一角剝離模具與 PDMS 芯片,先后用乙醇、超純水、氮氣沖刷其表面以去除碎屑、灰塵等雜質。將清洗后的微流控芯片放置在切膠臺上,按照前期設計的尺寸切除不整齊的邊緣部分,最后將制作好的PDMS 片與基片進行粘合以封閉微流控芯片。
圖5 PDMS 微流控芯片工藝流程
審核編輯:黃飛
-
集成電路
+關注
關注
5368文章
11168瀏覽量
358458 -
微流控
+關注
關注
15文章
480瀏覽量
18785 -
微芯片
+關注
關注
0文章
60瀏覽量
13526
原文標題:微流控芯片技術
文章出處:【微信號:gh_38186cae1d9a,微信公眾號:秦嶺農民】歡迎添加關注!文章轉載請注明出處。
發布評論請先 登錄
相關推薦
技術解析:微流控芯片為什么這樣強大?
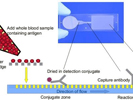
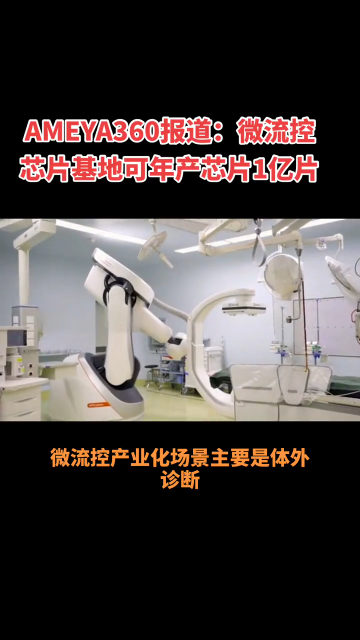
評論