共讀好書
摘要:
銦鉛銀焊料(154 ℃)熔點可與鉛錫焊料(183 ℃)拉開溫度梯度,且熱導率高于導電膠,可滿足功率器件的散熱要求,因此該焊料在組件類產品功率芯片載體裝配工藝中應用廣泛。傳統的手工燒結方式具有熔融時間長、生產效率低、可靠性差等缺點,通過對基于銦鉛銀低溫焊料的真空燒結工藝的助焊劑選取、焊料厚度和尺寸、工裝夾具設計、真空燒結曲線調試等幾個方面進行研究,最終摸索出一種適用于銦鉛銀低溫焊料的真空燒結工藝方法。
0 引言
常用的芯片安裝技術主要包括焊料燒結和導電膠粘結,導電膠粘結工藝具有操作簡單、成本低等優點,但其導熱性較差,對于功率較大需要散熱的芯片仍主要采用焊料燒結工藝。由于組件類產品結構復雜,通常包含有連接器、電路板、表貼阻容元件安裝等非芯片裝配工序,一般會用到 217 ℃(Sn96.5Ag3Cu0.5)和 183 ℃(Pb63Sn37)兩個溫度梯度,而芯片裝配工序需要與非芯片裝配工序拉開溫度梯度,以保證上道工序裝配的可靠性。功率芯片通常使用金錫焊料燒結工藝先燒結到散熱較好的匹配載片上,再將載片用低溫焊料燒焊到盒體中,以達到較好的散熱效果。
銦鉛銀焊料(In80Pb15Ag5)作為低熔點電子焊接材料,可與 Pb63Sn37 焊料拉開溫度梯度,且具有較高的熱導率、較強的抗疲勞性能,因此在組件類產品功率載片裝配工藝中得到廣泛應用。
傳統的手工燒結方式存在如下問題:(1)焊料浸潤性差,需要載體和盒體先搪錫,再進行燒結,效率很低;(2)由于產品尺寸限制載體入盒無法預留足夠摩擦空間,導致載體與盒體上搪的錫無法充分融合,后期出現載體脫落的質量問題;(3)很多產品要燒結十幾甚至二十幾個東西,手工摩擦需要逐個進行燒結,由于熔融時間過長導致最先燒結的載體焊料發干,后期易出現載體脫落的質量問題。
基于以上原因,急需對基于 154 ℃低溫焊料的真空燒結工藝進行研究,實現基于 154 ℃低溫焊料的低空洞率真空燒結。
1 低溫焊料的真空燒結工藝影響因素
1.1 載體及盒體背面金屬化
154 ℃焊料中的銦元素可與金形成合金,且銦對金的溶蝕作用遠比錫小 [1] ,不會形成 " 金脆" 效應,因此含銦焊料可適用于厚金材料的焊接。一般用于焊接的材料鍍層采用鎳 - 金兩層金屬化結構,對于較常使用的鉬銅載體,鎳層可形成阻擋層,避免銅元素向鍍金層中的擴散,保證鍍金層的純度,保證與焊料的焊接質量。由于盒體通常需要同時適應含錫焊料的焊接,因此盒體鍍金層一般不大于 0.5 微米,這就要求載體鍍金層厚度需要厚一點,以保證銦鉛合金中金元素的百分比,載體鍍金層厚度一般要在 1 微米以上,較厚的鍍金層有利于銦與金的合金成核過程,提高焊料與載體的焊料強度和焊接質量。
1.2 原材料表面狀態
通常情況下,組件產品的非芯片裝配工藝在芯片裝配工藝之前,因此功率載體入盒時盒體已經過了多次焊接過程,前道工序的助焊劑殘留或者其他污染源引入均會導致待焊接表面粘污,從而影響該表面的潤濕性,導致焊料熔融狀態鋪展不良,對焊接效果造成很嚴重的影響 [2] 。因此在焊接前需對盒體待焊接面進行清潔,以除去其表面粘污,保證焊接質量。
1.3 真空燒結工藝曲線
真空燒結是指在一定的真空度下,利用熔點比被焊接材料的熔點更低的合金做釬料,通過加熱使釬料熔化,靠毛細作用將液態焊料填充到焊接接觸面的間隙中,通過液態焊料與被焊金屬之間相互擴散溶解形成金屬間化合物,最后經過冷卻形成高可靠的焊接 [3] 。
真空燒結溫度曲線一般由四部分組成:預熱區、保溫區、峰值區、冷卻區。預熱區主要用來對原材料進行預熱,提高焊料活性,進而保證粘接效果;保溫區主要用來保證原材料受熱均勻,減小溫差造成的影響,同時可以在助焊劑或者還原氣體的作用下去除原材料表面的氧化膜;峰值區主要用于焊料的共晶反應,生成金屬間化合物,實現原材料之間的焊接;冷卻區主要用于控制冷卻速度,避免冷卻速度過快或過慢影響金屬間化合物的晶粒生長,最終導致粘接強度下降等問題 [4] 。通過設置合適的溫度曲線并在合適的溫度點進行抽真空過程,來確保焊料中的氣泡或者助焊劑被抽出,從而實現低空洞率燒結。
2 低溫焊料真空燒結工藝研究
2.1 焊接表面處理
由于組件類盒體在載體入盒前通常已經過了多次焊接過程,其表面粘污對燒結質量影響較大,為保證燒結質量需要對焊接表面進行預處理。經試驗驗證,兩種方式可實現焊接表面的清潔:當表面無可見粘污時,可采用等離子清洗的方式進行焊接表面清潔,該方式效率較高,但僅適用于輕微污染表面;當表面有肉眼可見粘污時,需要用乙醇棉進行擦拭,保證清潔效果。
2.2 焊料選擇
154 ℃低溫焊料成分為In80Pb15Ag5,主要形式有焊片和焊錫絲等。焊片具有可再次加工成型、易實現定量控制等優點,更適合于真空燒結工藝應用。
焊片的厚度和大小決定了焊料量的多少,分別對厚度為 100 μm、75 μm、50 μm 的焊料進行了試驗,厚度為 100 μm 的焊料在不加壓時燒結后載體傾斜嚴重,影響后續鍵合;75 μm 厚度焊料的燒結空洞率明顯優于50 μm 焊料,這是因為鉬銅載體一般較薄,在經過金錫燒結后通常會有一定的形變,較厚的焊料可彌補載體形變造成的空隙,保證焊料和載體的接觸面積,從而保證燒結質量。因此確定了最佳焊料厚度為 75 μm。圖 1 所示為 50 μm厚度焊料和 75 μm 厚度焊料燒結后的 X光照片。
焊片的尺寸對燒結效果影響也較大,由于銦鉛銀焊料浸潤性較差,需要使用助焊劑進行燒焊,當焊料尺寸較大時,焊料熔融時會迅速與載體邊緣形成包角,導致助焊劑不易被抽出,空洞率較大;焊料面積過小時,焊料流動性差,無法浸潤到載體邊緣,導致載體邊緣空洞率差,經反復試驗最終確定了最佳的焊料尺寸為載體面積*80%。
2.3 工裝夾具設計
通過壓塊的方式提供適當的壓力可以在一定程度上增大焊接面積 [5] ,減少焊料與焊接面之間的空隙,保證焊接質量。
組件內待入盒的載體通常都已燒結好芯片,壓塊直接對芯片加壓會損傷芯片,因此需設計鏤空壓塊將芯片位置讓開進行加壓,如圖 2 所示。
對于 TR 組件類產品需要對很多個載體(通常有幾十個之多)同時加壓,使用壓塊加壓效率很低,因此設計了探針加壓工裝:在工裝橫梁上固定很多根彈簧探針,探針在載體上未安裝芯片的位置進行加壓,彈簧探針工裝可實現多載體的同時加壓。圖 3 所示為專供 TR 組件載體裝配使用的彈簧探針加壓工裝。
2.4 真空燒結工藝曲線
真空燒結工藝曲線對燒結質量具有直接影響。為了保證良好的燒結效果,應該選擇合適的預熱溫度,并進行充足的預熱,同時選擇合適的燒結溫度與時間,避免溫度不足導致無法充分反應或時間過長反應過度、溫度過高導致 183 ℃焊料熔融等情況的出現。抽真空的時機也很重要,由于工藝過程中使用了助焊劑,需要在燒結過程中將助焊劑充分抽出,以保證燒結空洞率。因此低溫焊料的真空燒結工藝需改變傳統的程序設計思路。
傳統真空燒結曲線如圖 4 所示,在常溫時進行兩次抽真空 - 充氮氣循環進行氣氛換氣,隨后在真空下進行升溫,這一過程主要是為了防止焊料氧化;當溫度升到最高點時充入少許氮氣(60 Torr~150 Torr 之間)進行導熱使焊料熔融,焊料熔融狀態下開始抽真空以抽出焊料中的氣泡,之后開始降溫進入冷卻區。
154 ℃低溫焊料的真空燒結程序曲線如圖 5 所示,經過兩次換氣后在常壓下進行升溫,原因是銦鉛銀低溫入盒工藝主要應用于組件類產品,很多產品背面有腔體,真空狀態升溫很慢,常壓下可實現氣體輔助升溫,且有助焊劑不會導致焊料氧化;在焊料熔融前開始抽真空,因為當焊料熔融后助焊劑較難抽出;然后進氣等待焊料熔化,熔化后再進行三次抽真空 - 充氮氣的循環,這樣可將大的氣泡吹散,保證燒結空洞率。
該程序還可實現組件產品的快速程序調試,快速實現多品種小批量特征明顯的產品生產。將程序最高溫度控制在 185-190 ℃,以確保 Pb63Sn37(183 ℃)焊料不會熔融,當進行新產品調程序時,將真空燒結爐的測溫熱偶置于盒體表面進行盒體溫度監測,通過延長最高溫進氣時間使焊料熔融,試驗一爐后即可確定最終燒結程序。
3 試驗結果
經過以上各項工藝研究,基于銦鉛銀低溫焊料的真空燒結工藝達到了較好的燒結效果,可實現燒結空洞率<10%,滿足功率載體入盒的工藝要求。圖 6 所示為 TR組件低溫焊料真空燒結后的 X 光照片。
4 結束語
154 ℃低溫焊料的真空燒結工藝與原材料表面狀態、焊料厚度及尺寸、加壓情況、真空燒結工藝參數等因素有關,通過有效的表面處理措施、合適的焊料厚度及尺寸選擇、工裝夾具設計及真空燒結工藝曲線調試,得到了較好的燒結效果,實現了組件類產品功率載體的低空洞率燒結。
隨著 TR 組件及微波組件類產品在各類工程中的廣泛應用,154 ℃低溫焊料真空燒結工藝為該類產品的功率載體入盒提供了合理的工藝路線和適合工程化應用的工藝方法,可大大提高生產效率和燒結質量。
審核編輯 黃宇
-
焊料
+關注
關注
0文章
28瀏覽量
8195 -
燒結
+關注
關注
0文章
16瀏覽量
7002
發布評論請先 登錄
相關推薦
低溫無壓燒結銀在射頻通訊上的5大應用,除此之外,燒結銀還有哪些應用呢?歡迎補充
物聯網行業中3D打印工藝——SLS(選擇性激光燒結)工藝
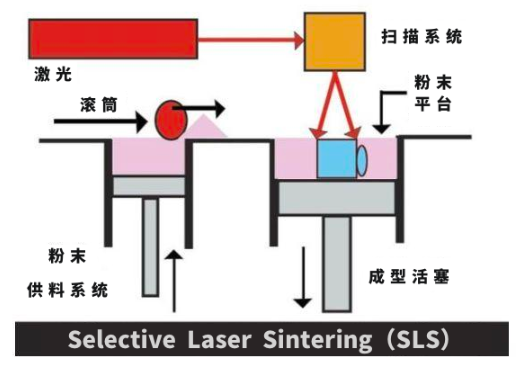
燒結銀AS9378火爆的六大原因
SiC功率器件先進互連工藝研究
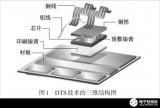
晶圓級封裝用半燒結型銀漿粘接工藝
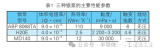
無鉛低溫錫膏的特性與儲存方法
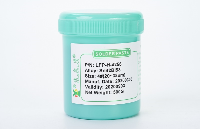
IGBT模塊銀燒結工藝大揭秘,成本降低與性能提升雙贏策略
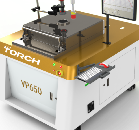
IGBT模塊銀燒結工藝引線鍵合工藝研究
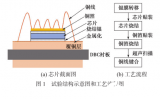
評論