作為現(xiàn)代傳感器重要的制造技術(shù),MEMS工藝深刻地影響了現(xiàn)今傳感器產(chǎn)業(yè)的發(fā)展。可以說,MEMS的工藝技術(shù)都是從集成電路(IC)行業(yè)借鑒而來的,特別在MEMS剛興起時(shí),傳統(tǒng)IC行業(yè)的工藝設(shè)備和技術(shù)為MEMS制造提供了巨大的基礎(chǔ)設(shè)施。比如,MEMS中使用的光刻設(shè)備,可能是為IC制造而設(shè)計(jì)的前幾代設(shè)備,但設(shè)備的性能足以滿足MEMS的要求,其價(jià)格卻大幅降低。
MEMS芯片制造采用光刻、干法刻蝕、濕法刻蝕、薄膜沉積、氧化、擴(kuò)散、注入、濺射、蒸鍍、鍵合等基本工藝步驟來制造復(fù)雜三維結(jié)構(gòu)的微加工技術(shù)。隨著多年發(fā)展,MEMS領(lǐng)域也出現(xiàn)了一些專門的工藝,例如各向異性濕法蝕刻(anisotropic wet etching)、晶圓鍵合(wafer bonding)、深反應(yīng)離子蝕刻(deep reactive ion etching)等,但其應(yīng)用仍然僅限于 MEMS,目前來看并沒反過來應(yīng)用于IC行業(yè)。
一般來說,MEMS芯片制造的基本工藝包括三個(gè)關(guān)鍵步驟:沉積(Deposition)、圖形化轉(zhuǎn)移(Patterning)、蝕刻(Etching),整個(gè)過程即:①晶圓/襯底涂抹光刻膠,然后②通過對(duì)光刻膠曝光,去除非圖形化部分的光刻膠,然后③用光刻膠作為掩模來蝕刻下方的材料。整個(gè)過程重復(fù)進(jìn)行,直到完成微觀結(jié)構(gòu)。
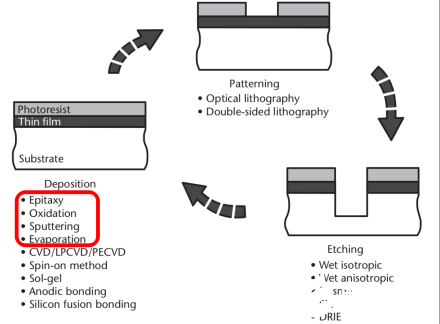
下文全面介紹MEMS芯片中制造的常用基本工藝,以及討論各種工藝對(duì)MEMS芯片及傳感器產(chǎn)品的影響,部分目錄如下:
↓↓↓向下滑動(dòng),查看更多↓↓↓
一、沉積1、外延(Epitaxy)2、氧化(Oxidating)3、濺射(Sputtering)4、蒸發(fā)(Evaporation)5、化學(xué)氣相沉積(Chemical vapor deposition)6、多晶硅(Poly silicon)的沉積7、二氧化硅(Silicon Dioxide)的沉積8、氮化硅(Silicon Nitrides)的沉積9、旋涂工藝(Spin-On)二、光刻1、掩膜版(Mask)與光刻膠(Photoresist)2、光學(xué)曝光(Exposure)3、光刻膠厚度對(duì)光刻的影響4、地形高度變化對(duì)光刻的影響5、視場(field of view)對(duì)光刻的影響6、需要雙面光刻的情況三、刻蝕1、濕法刻蝕(1)濕法與干法刻蝕(2)各向同性與各向異性(3)刻蝕的三維結(jié)構(gòu)(4)小結(jié)2、干法刻蝕(1)電化學(xué)蝕刻(2)等離子蝕刻與反應(yīng)離子刻蝕(3)深度反應(yīng)離子蝕刻(博世工藝)
來源:芯生活SEMI Businessweek
一、沉積 外延(Epitaxy)、氧化(Oxidating)、濺射(Sputtering)、蒸發(fā)(Evaporation)等屬于沉積(Deposition)類別的基本工藝,也是用于沉積均勻的半導(dǎo)體、金屬、絕緣體和聚合物層的常用技術(shù)。1、外延(Epitaxy)
外延是一種在硅晶圓上生長晶體硅(crystalline silicon)層的沉積方法,但具有不同的摻雜劑類型和濃度。外延層的厚度通常為 1 至 20 μm。它表現(xiàn)出與下面的晶體基板相同的晶體取向。當(dāng)然,如果是在非晶材料(例如二氧化硅層)上生長時(shí),它是多晶的。
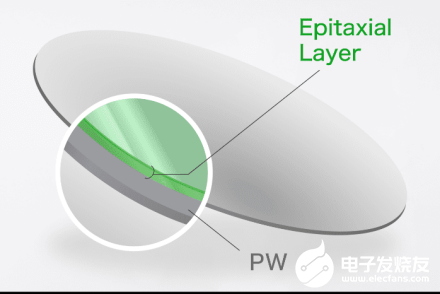
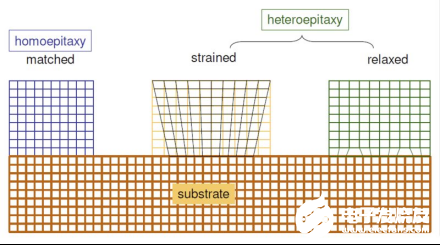
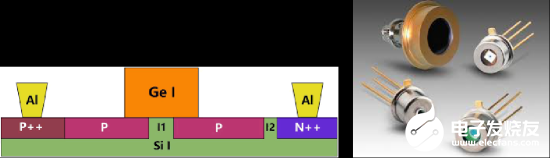
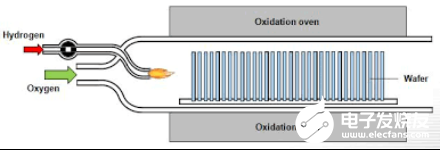
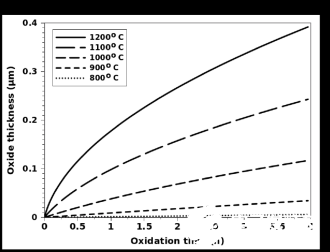
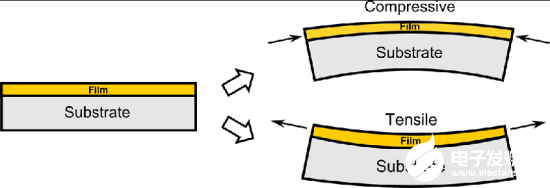
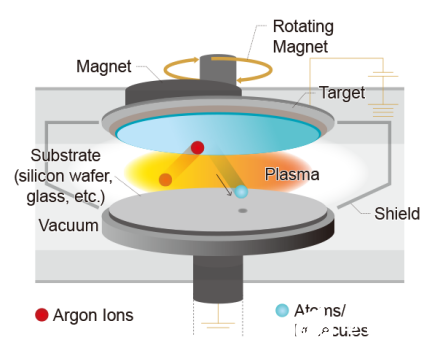
沉積過程中應(yīng)力水平隨濺射功率和腔室壓力而變化,在較低功率和較高壓力下出現(xiàn)拉伸應(yīng)力(tensile stress),在較高功率和較低壓力下出現(xiàn)壓縮應(yīng)力(compressive stress)。零應(yīng)力沉積的理想點(diǎn)很難難控制。在沉積過程中加熱基底有時(shí)可以用于減少薄膜應(yīng)力。 許多金屬,特別是金、銀和鉑等惰性金屬,不能很好地粘附到硅、二氧化硅或氮化硅上,在沉積后或在后續(xù)處理過程中會(huì)立即剝落。一層薄薄的(5 至 20 納米)粘合層(adhesion layer)與底層材料及其上方的金屬粘合,使惰性金屬能夠粘附。最常見的粘附層是 Cr、Ti 和 Ti/W 合金。惰性金屬必須在真空的情況下沉積在粘合層上,因?yàn)榭諝庵械难鯕鈺?huì)立即氧化粘合層,使其粘合效果失效。

蒸發(fā)是一種來自相對(duì)較小體積來源的定向沉積過程。這導(dǎo)致大部分材料顆粒以特定角度沉積到基板上,導(dǎo)致臺(tái)階覆蓋不良,并有角落和側(cè)壁暴露的現(xiàn)象。如果需要薄膜連續(xù)性(例如,當(dāng)金屬是電互連時(shí)),這通常是不期望的效果。在沉積過程中旋轉(zhuǎn)基板以不同角度面對(duì)源會(huì)減少這種影響。 通過蒸發(fā)沉積的薄膜往往會(huì)表現(xiàn)出拉伸應(yīng)力,并且隨著材料熔點(diǎn)的升高而增加。例如,蒸發(fā)的鈮和鉑薄膜可能具有超過 1 GPa 的拉伸應(yīng)力,足以導(dǎo)致晶圓卷曲甚至剝離。此外,與濺射一樣,許多金屬必須使用粘合層。5、化學(xué)氣相沉積(Chemical vapor deposition) 化學(xué)氣相沉積(CVD)的工作原理是在受控氣氛中引發(fā)表面化學(xué)反應(yīng),從而導(dǎo)致反應(yīng)物質(zhì)沉積在加熱的基材上。與上一節(jié)的濺射相反,CVD是一種高溫工藝,通常在300°C以上進(jìn)行。在IC行業(yè)對(duì)用于多層電互連的高質(zhì)量、薄電介質(zhì)和金屬薄膜的需求的推動(dòng)下,CVD技術(shù)發(fā)展已大幅增長。 通過CVD沉積的常見薄膜包括多晶硅、硅氧化物和氮化物、鎢、鈦、鉭等金屬及其氮化物,以及最近的銅和低介電常數(shù)絕緣體(εr<3)。后兩者正在成為IC行業(yè)中超高速電氣互連的主力材料。而在MEMS領(lǐng)域,多晶硅、氧化硅和氮化物的CVD沉積是最常見的。
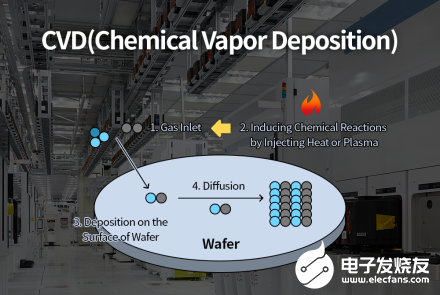
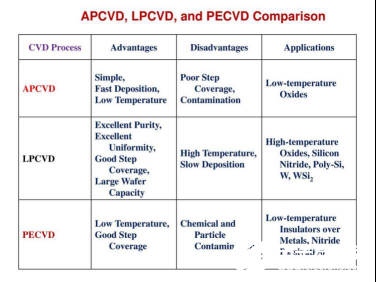
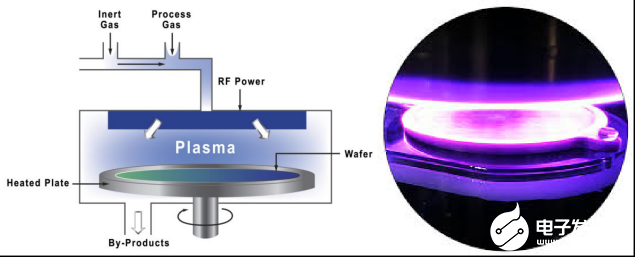
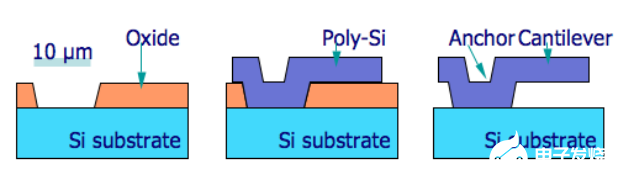
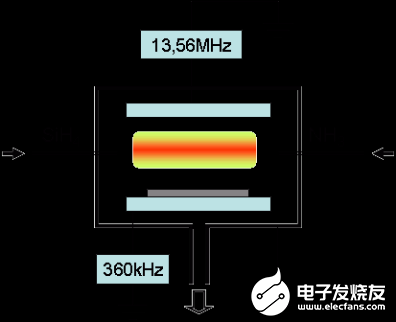
摻雜的多晶硅薄膜的固有應(yīng)力可能很大(>500MPa),應(yīng)力可能是拉伸應(yīng)力,也可能是壓縮應(yīng)力,具體取決于沉積溫度。此外,薄膜厚度上通常存在應(yīng)力梯度,這會(huì)導(dǎo)致釋放后的微機(jī)械結(jié)構(gòu)卷曲。所以需要在900°C或更高溫度下進(jìn)行退火,通過晶界的結(jié)構(gòu)變化產(chǎn)生應(yīng)力松弛,并將應(yīng)力降低至微機(jī)械結(jié)構(gòu)通常認(rèn)為可接受的水平(<50MPa)和應(yīng)力梯度。 7、二氧化硅(Silicon Dioxide)的沉積 通過在APCVD、LPCVD或PECVD反應(yīng)器中使硅烷和氧氣發(fā)生反應(yīng),在低于500°C的溫度下沉積二氧化硅。由于與熱生長氧化物的工藝(thermally grown oxide,簡稱熱氧)相比溫度較低,因此被稱為低溫氧化物(LTO,low-temperature oxide)。
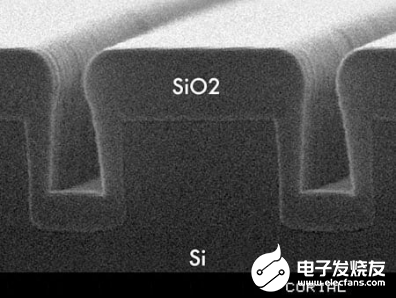
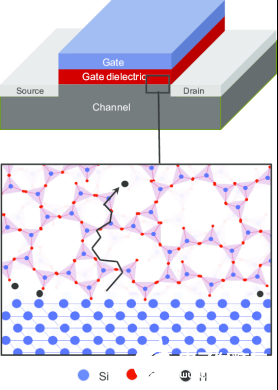
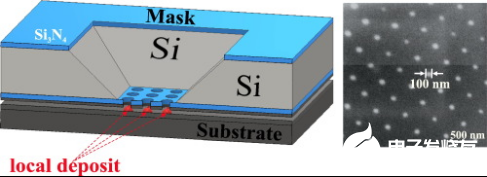
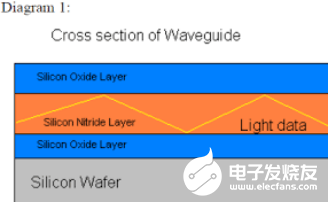
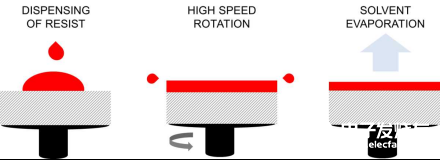
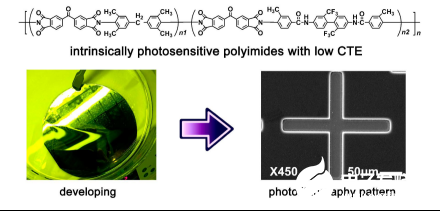
- 光刻膠(Photoresist)的應(yīng)用,它是一種感光乳劑層;
- 光學(xué)曝光(Exposure),將掩膜版(mask)上的圖像打印到光刻膠上;
- 浸入顯影溶液(Developer)中,以溶解曝光后的光刻膠并使?jié)撓窨梢姟?/span>
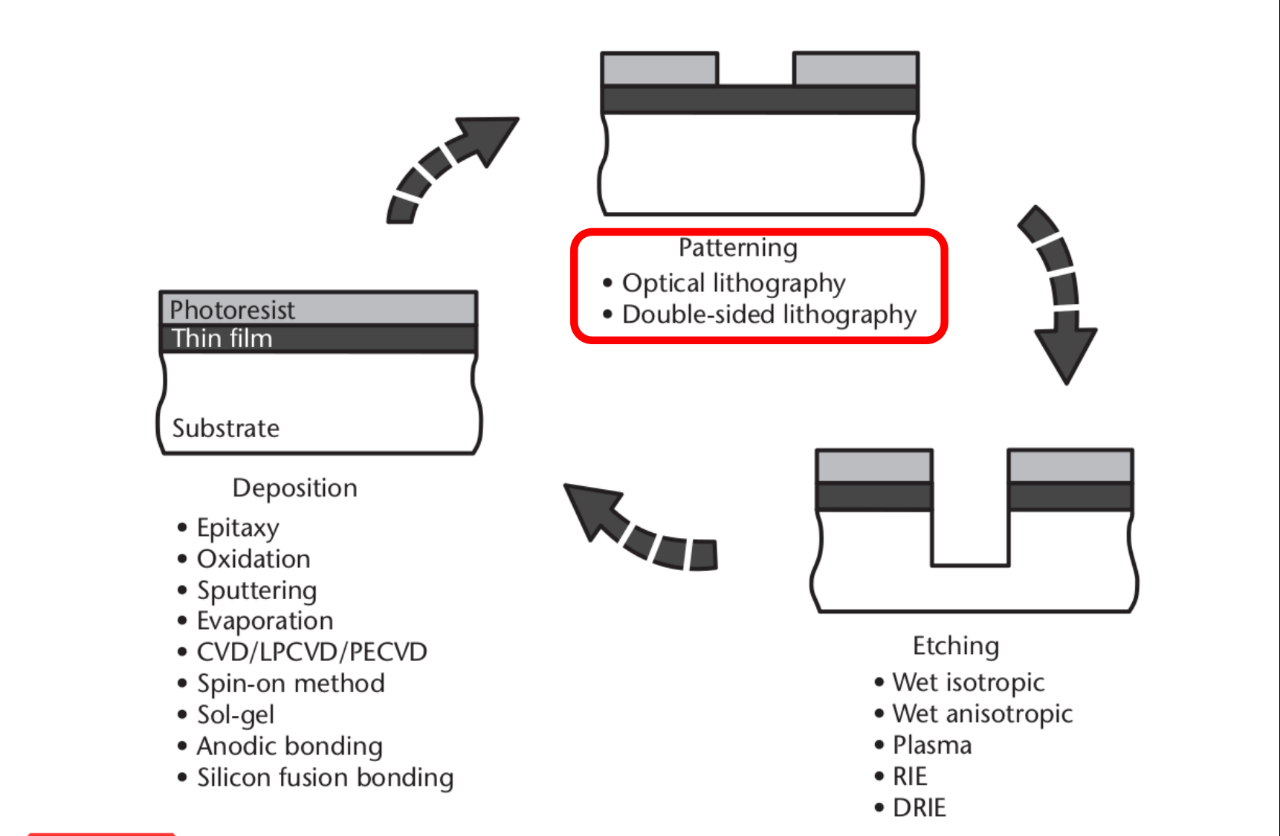
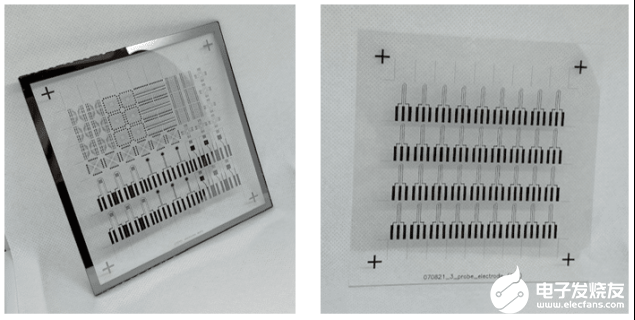
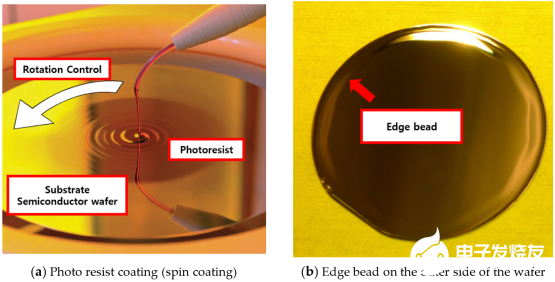
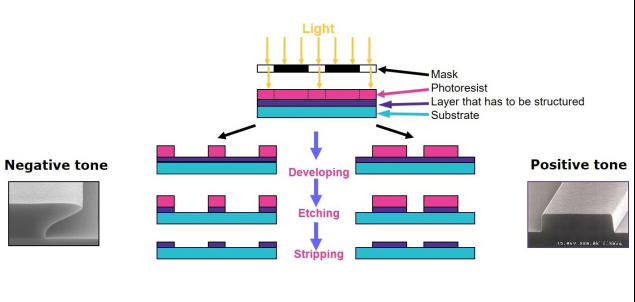
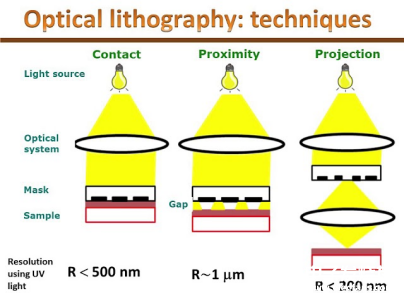
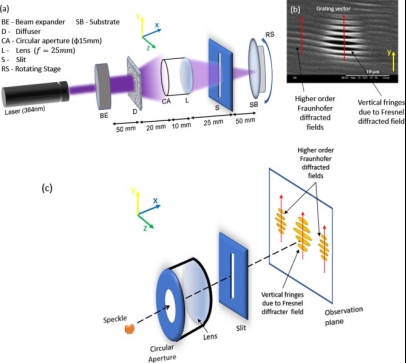
焦深(Depth of focus)是對(duì)光刻更嚴(yán)格的限制,特別是考慮到需要曝光較厚的光刻膠或適應(yīng)晶圓上的幾何高度變化。接觸式和接近式系統(tǒng)的焦深很差,也受到菲涅爾衍射的限制。 在投影系統(tǒng)中,可以通過調(diào)整焦點(diǎn)設(shè)置來移動(dòng)圖像平面,但一旦固定,該平面的焦深就會(huì)限制為 ±0.5 × λ/NA^2,也就是說,焦深通常限制在幾微米。投影模式的光刻系統(tǒng)顯然是一種優(yōu)越的方法,但系統(tǒng)的成本可能比接近模式或接觸模式的系統(tǒng)高得多。
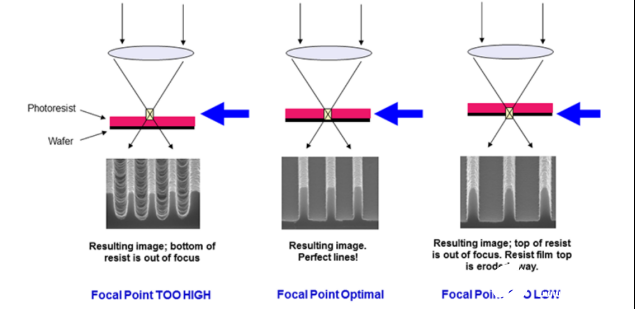
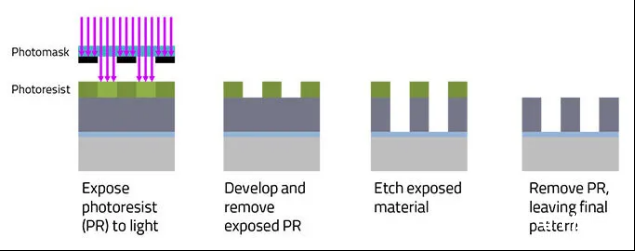
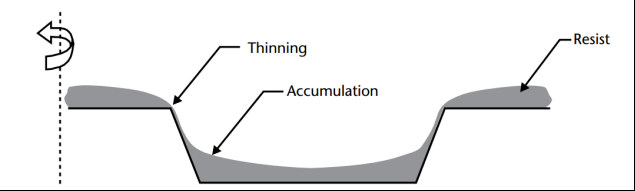
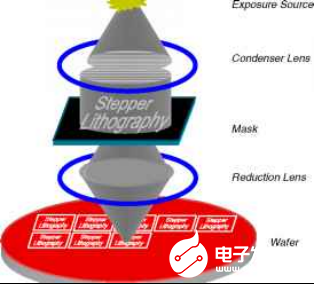
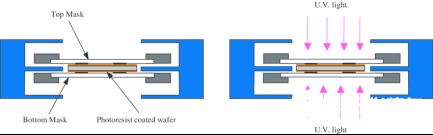
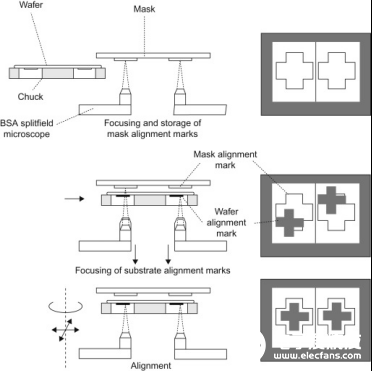
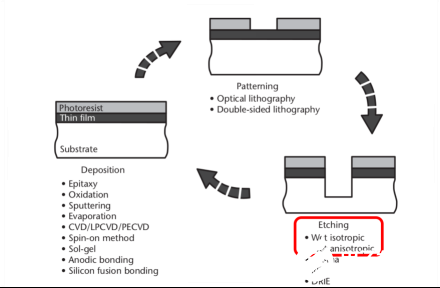
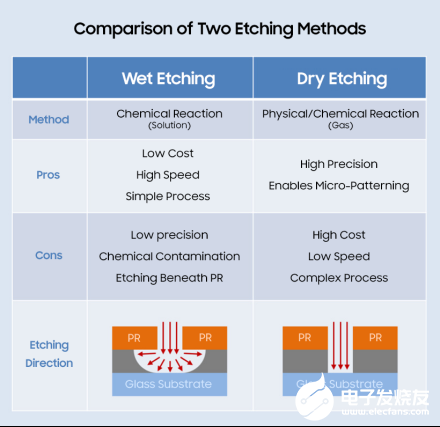
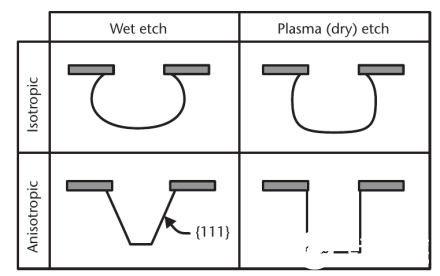
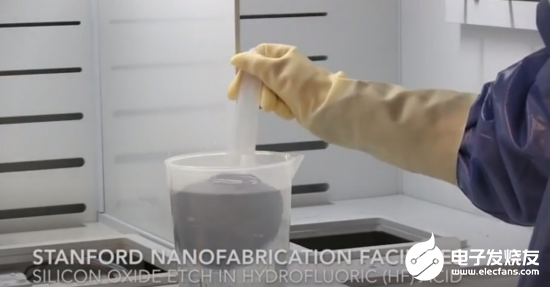
KOH是迄今為止最常見的ODE。刻蝕速率通常在[100]方向給出,對(duì)應(yīng)于刻蝕前沿為{110}平面。{110}面在KOH中的刻蝕速度大約是{100}面的兩倍,而{111}面的刻蝕速度比{100}面慢大約100倍。后一個(gè)特征通常用于在{100}硅片上制作V形凹槽和溝槽,這些凹槽和溝槽由{111}晶面精確描繪。
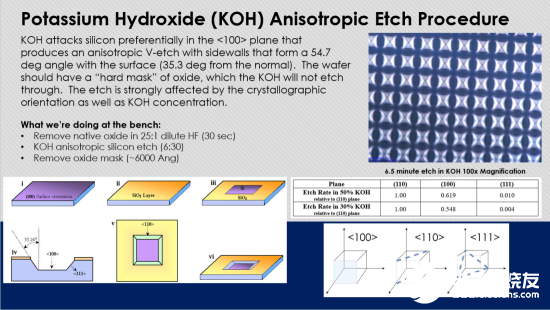
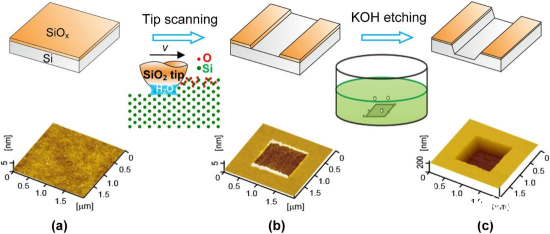
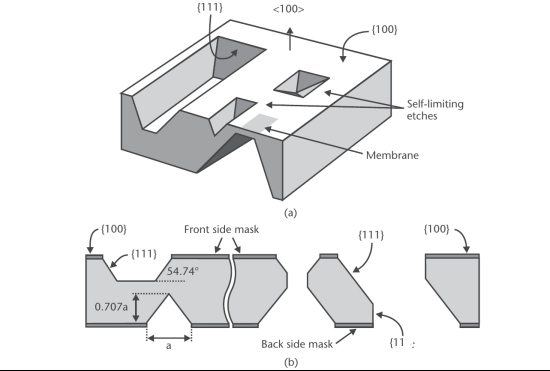
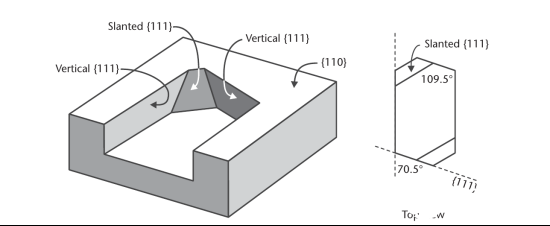
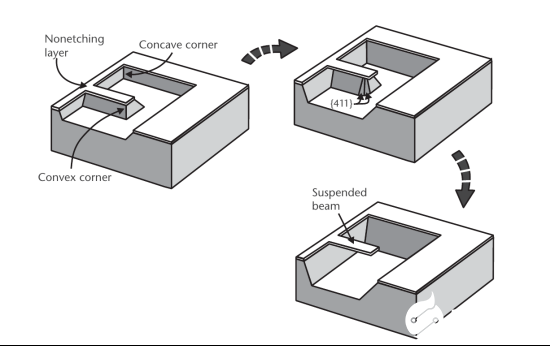
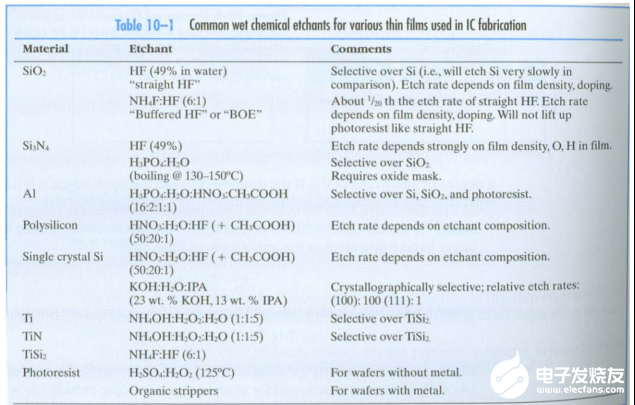
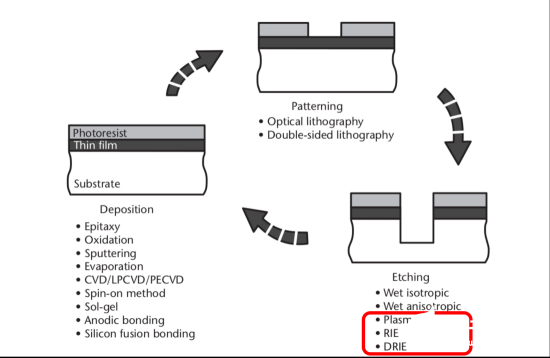
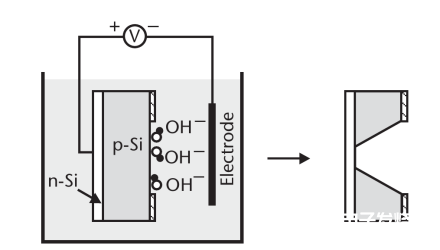
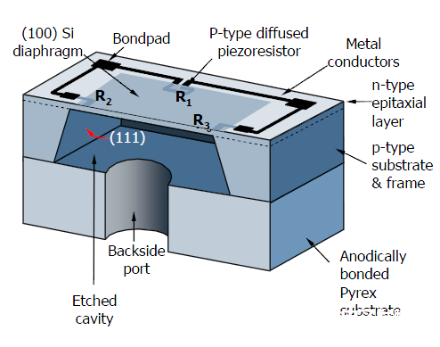
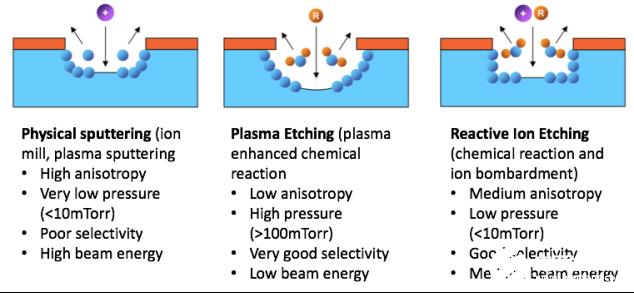
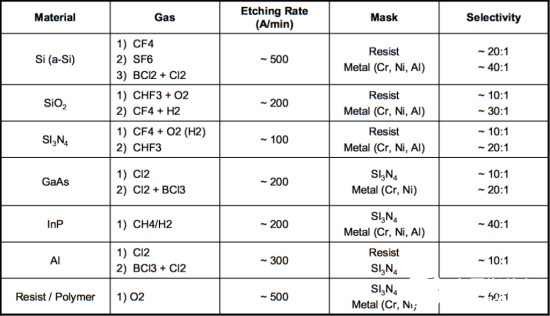
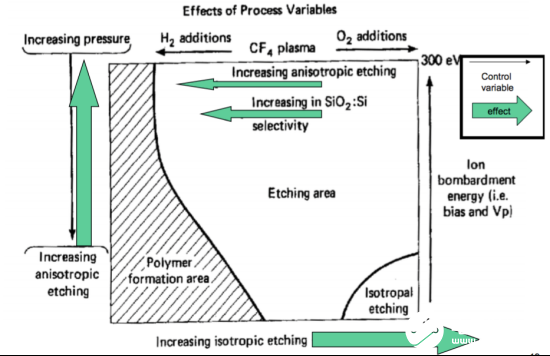
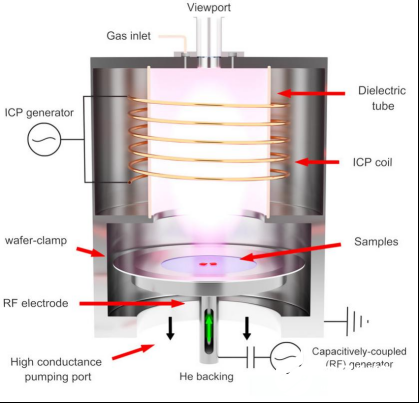
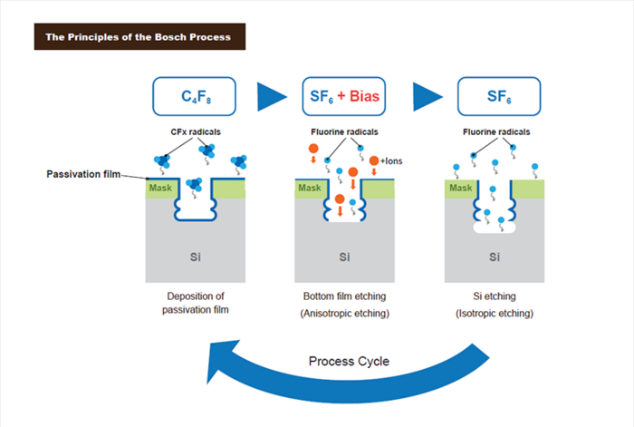
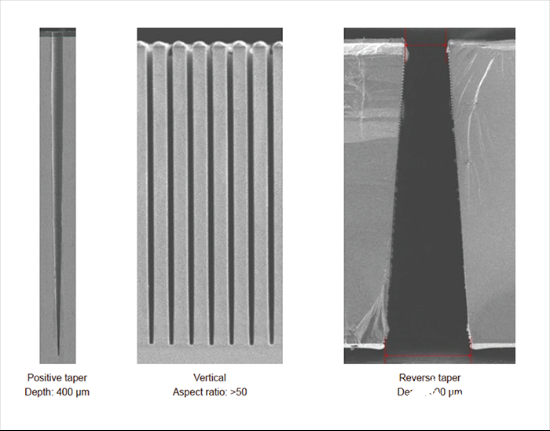
審核編輯 黃宇
-
傳感器
+關(guān)注
關(guān)注
2548文章
50668瀏覽量
751951 -
芯片
+關(guān)注
關(guān)注
453文章
50396瀏覽量
421789 -
mems
+關(guān)注
關(guān)注
129文章
3896瀏覽量
190340
發(fā)布評(píng)論請(qǐng)先 登錄
相關(guān)推薦
SMT工藝流程詳解
mems傳感器是什么意思_mems傳感器原理是什么
簡述連接器的工藝流程
芯片底部填充工藝流程有哪些?
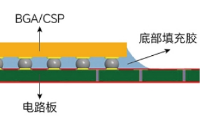
上海工研院MEMS取得重大突破,智能傳感器工藝從定制化向標(biāo)準(zhǔn)化持續(xù)邁進(jìn)
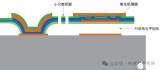
一文解析DARM工藝流程
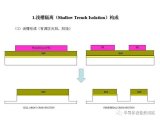
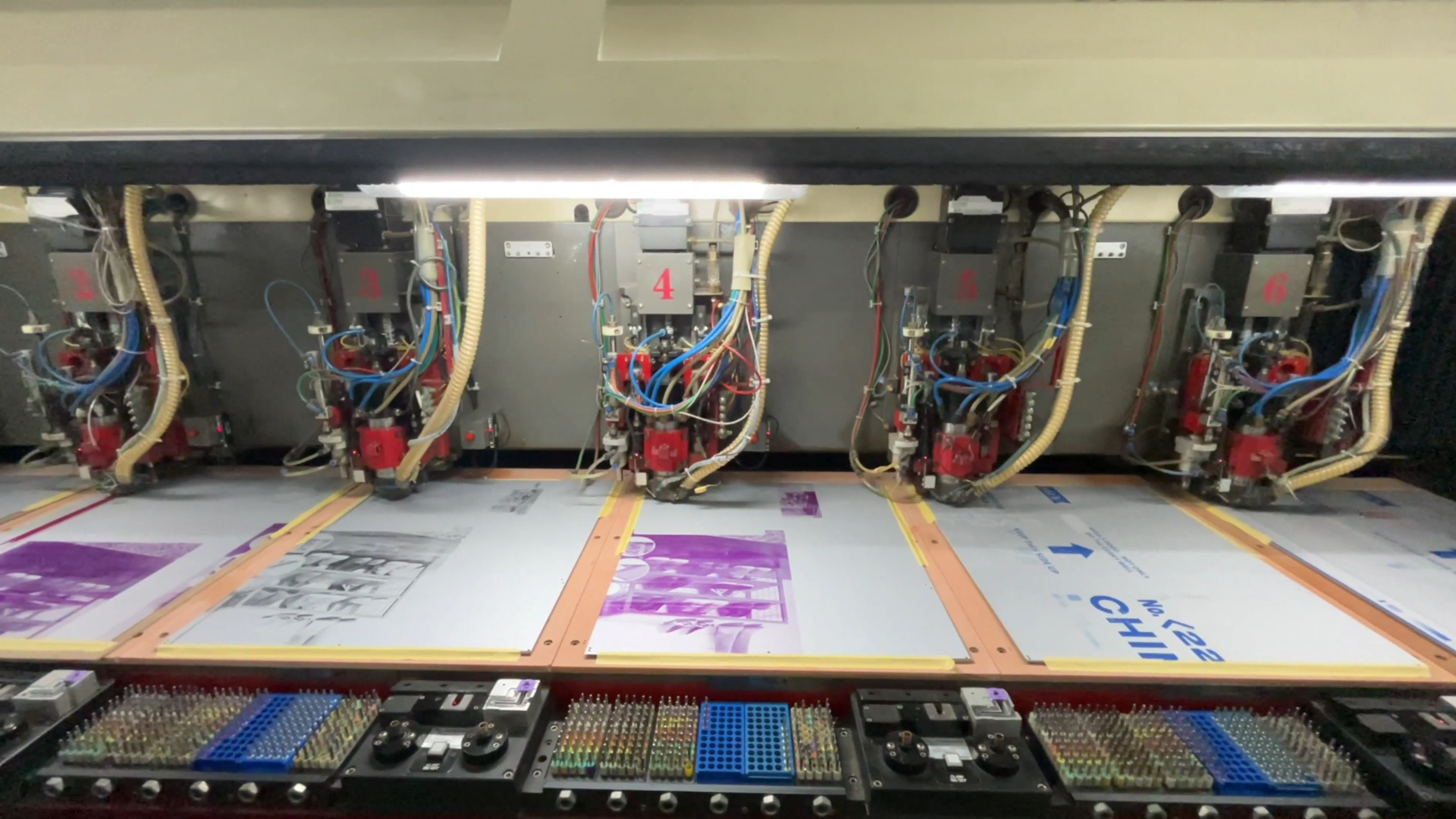
評(píng)論