凡與車相關,必有車規級。車規級究竟有什么奇特之處?
如今汽車電子產品價格飛漲,其原因不外乎“車規級”,但人人都在說的車規級究竟是什么?
車規級,顧名思義它是一種汽車標準,符合各個國家立法的關于汽車標準的法規,各國的標準有所不同。例如,在美國,汽車導航需要AECQ認證。以汽車導航為例,首先需要高性能處理器。車規級控制單元專門處理CAN總線信息和控制邏輯,以確保系統的可靠運行。然后是高清音頻和視頻硬件的解碼,音頻和視頻文件的解碼,以及前后座椅聲場以及左右平衡位置的調整。同時,它必須與原始汽車的CAN總線協議和原始汽車的線束兼容,匹配原始汽車的協議,支持原始汽車的方向盤控制,并正常顯示車輛行駛的信息。當然,也需要快速定位和導航,以支持陀螺儀功能的安裝。EMC電磁兼容性能要達標等。
綜上所述,車規級實際上是一套硬件上的規格標準,車規級是在工業級上的擴展。符合以上標準的,可以稱為車規級。車規級汽車電子元件的高標準要求更能滿足汽車行業的需求。
車規級的標準是AEC-Q系列標準。AEC-Q100適用于芯片,AEC-Q101適用于分立半導體器件,AEC-Q102適用于分立光電子器件,AEC-Q103適用于MEMS器件,AEC-Q104適用于多芯片模組,AEC-Q200適用于無源元件。
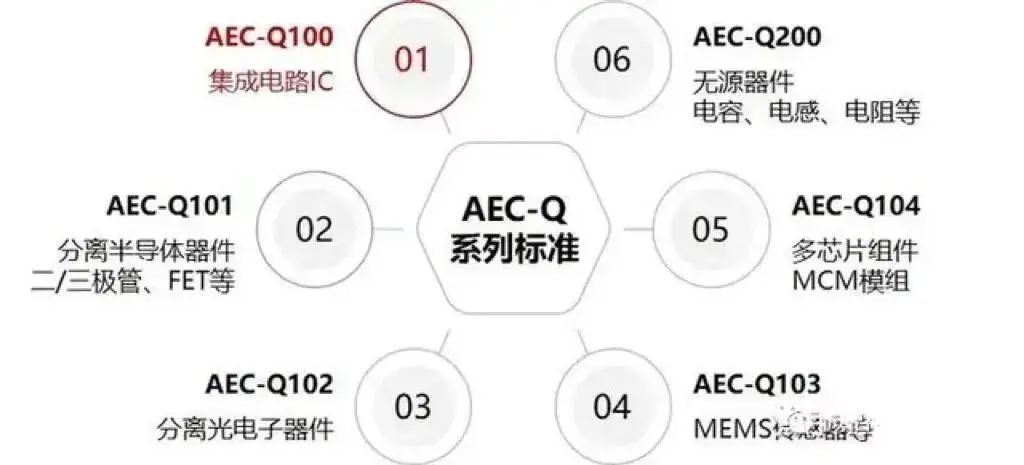
通俗來講,車規級電子元件按照應用場景,通常可以分為消費級、工業級、車規級和軍工級四個等級,其要求依次為軍工>車規>工業>消費。
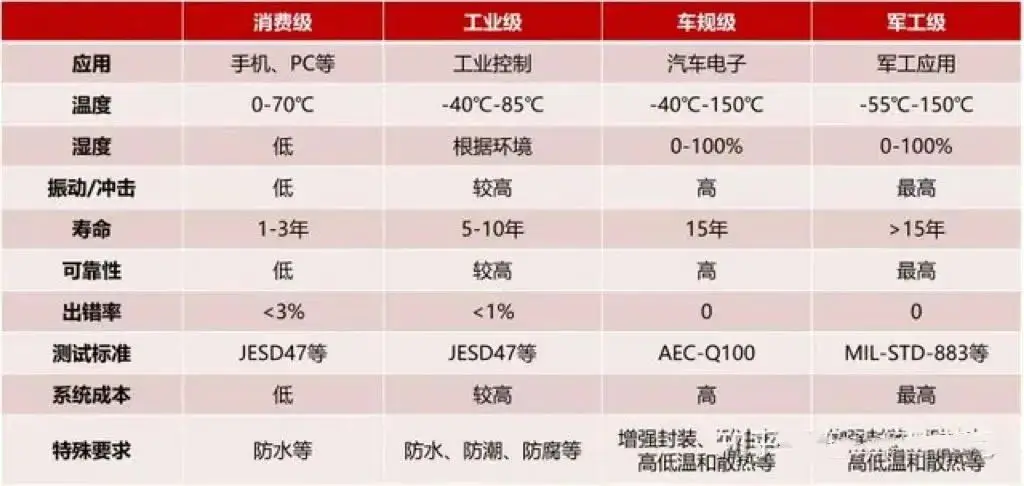
汽車電子元件對外部工作環境,如溫度、濕度、發霉、粉塵、水及有害氣體侵蝕等的要求,根據不同安裝位置等有不同需求,但一般都大于消費級。
以瑞薩車規級芯片的要求為例:要求芯片能夠在環境溫度-40℃~75℃,濕度95%,15~25KV的靜電環境下能夠正常工作,并且還要要求有20年的保質期,保質期內不許壞,產品不良率在100萬分之一以下,幾乎為0。

除環境外,汽車電子在可靠性和一致性上的要求一般也大于工業級。
其測試條件比消費級、工業級電子元器件更加規范嚴苛,苛刻的車規級標準可以確保由大量的ECU和上萬個電子元器件構成的汽車在使用過程具有長生命周期和高可靠性。
可靠性:在規定條件下工作不犯錯的能力。
汽車設計壽命都在 15 年左右,遠大于消費電子產品壽命要求,目前車輛的電氣化程度已經非常高了,特別是電動汽車的各個控制系統,都配置了很多的ECU裝置,每個裝置里面又由很多的電子元器件組成。為保證車輛整車達到相當的高可靠性,對控制系統組成的每一個部分要求都是是非常高的。
一致性:零件保持一致。
對于組成復雜的汽車產品來說,低可靠性、一致性差的元件無疑意味著巨大的安全隱患,因此經常用PPM(百萬分之一)來描述汽車零部件的要求。
現在的汽車都是大規模生產方式,廠家一款定型車輛一年可以生產數十萬輛,所以就對產品質量的一致性要求非常高,對于零部件組成復雜的汽車產品來說,使用一致性差的電子元器件將會導致整車出現安全隱患。
再來看幾點其它的需求。
制造工藝
汽車產品制造工藝的要求,雖然汽車的零件也在不斷的向小型化和輕量化發展,但相對消費產品來說,在體積和功耗上還相對可以放松,一般使用的封裝較大,以保證有足夠的機械強度并符合主要的汽車供應商的制造工藝。
產品生命周期
雖然近些年,汽車產品不斷的降價,但汽車還是一個耐用的大件商品,必須要保持相當長的時間的售后配件的供應能力。同時開發一個汽車零件需要投入大量的驗證工作,更換元件帶來的驗證工作也是巨大的,所以也整車制造企業和零部件供應商也需要維持較長時間的穩定供貨。
標準及驗證
這樣看來,滿足汽車產品要求的確復雜,而且以上的要求是針對汽車零件的(對于電子元件來說就是系統了),如何去轉換成電子元件的要求就變得很困難,為解決這個問題就自然有一些規范標準出現,比較得到公認的就是AEC 的標準:
AEC Q100 針對有源(Active Device)元件的要求
AEC Q200 針對無源(Possive Device)元件的要求
任何選擇都有雙面性,要求比軍工級高,但成本要比其低,這就增加了車規級產品的設計難度。首當其沖的困難是車規級開發驗證花費大、門檻高。其次因零件復雜度造成的選型困難往往導致要放棄一些集成度高的方案。最后車規級芯片制作周期非常長,大量驗證工作會影響產品上市速度。芯片廠家大多選擇在消費電子市場成熟后才將產品應用到汽車市場上。
車規級芯片要求已經如此之高,應用于新能源汽車的車載電源及充電樁功率器件更甚。
猜想很多人還會說,還有許多的整車廠的企業標準。其實一些整車廠確實是有相關的一般可靠性要求的標準,但它考核的是一個完整的汽車組件(由電子元件構成的系統),而非直接針對組成這些組件的電子元件的要求(電阻,電容,三極管,芯片等),雖然它的要求是可以用來參考對下級元件的選型,但作為電子元件測試等來說還是非常的不合適的。
車規的驗證
車廠的工作中,難免會使用到一些沒有 AEC Q100/200 認證的電子元件,很多車廠的人員都會希望進行一些可靠性驗證,來驗證它是否滿足車規要求。
個人認為這種方法并不太有效,因為這些測試都只能是必要不充分測試。只能用于否定該器件的可用性,而不能確定其可以使用。
原因很簡單,樣本數量太少測試的項目并不充分。對于半導體這種大批量制造的元件,通過少量的樣本的測試來確定其可靠性,個人認為是非常的不靠譜的,這里我們也可以來看看 AEC Q100 進行的主要認證測試項目,也就可以看出差別。
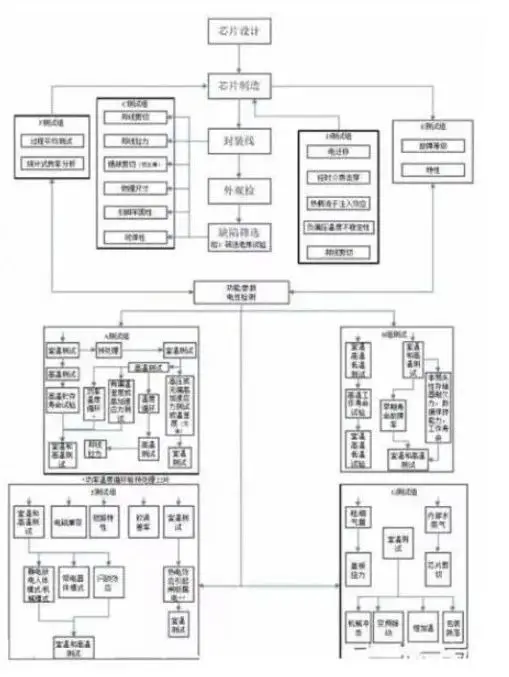
哪個標準要求高?
車規和工規,誰的要求高。普遍的認為標準的高低順序是軍工> 汽車 >工業> 消費電子。但個人卻不能完全接受這個順序。工業是個很寬的范圍,也遇到的環境和可靠性需要也是差異巨大的。可以想象得到比如一個大型工業設備的可靠性要求絕對不會比汽車要求低。(比如一個大型電廠的關鍵設備),而同時環境的苛刻度也可能會遠超汽車的要求,并不能簡單的說工規要求就比汽車低。
使用車規零件的壞處
任何選擇都不可能只有好處沒有壞處,使用車規電子元件有什么壞處呢?首先就是貴,體系要求高,開發驗證花費大,產量低導致成本高出消費電子一大截。相對較高的門檻也使得存在較多的銷售溢價。
其次的壞處就是選型困難。玩電子的人都知道發展到今天,電子元件相當的豐富,做相同功能的產品可以有多種方案,復雜度可能差異巨大,但有時為達到車規的要求,不得不放棄一些集成度高的方案。
還有一個比較明顯的壞處就是某些產品技術落后,大量的驗證工作影響到了新產品的上市速度,同時,芯片廠家一般的投放策略也是希望在消費電子市場上成熟后,才將該產品應用在到汽車市場上。比如在 2013 年小編在開發的一款產品使用的 ARM Cortex A9 的處理器,當時在汽車市場已經基本上是最好的產品了,但消費市場上 ARM Cortex A57 的處理器并不稀奇。
使用非車規的電子元件在車上到底有多大的風險
這個問題真是比較復雜,得從多個方面來判斷:
1. 僅僅是沒有得到相關的認證,但其實產品的性能和可靠性是滿足要求的,并且也得到過大量的應用驗證。如果屬于這種情況風險相對較小。
2. 這點是很重要的一點,就是元件和系統的關系。系統的性能和可靠性是由下一級的電子元件來構成的,所以在同樣的設計下,使用非車規的元件產品肯定要差。但好的設計,可以降低元件的性能要求,一個保護措施設計完善并能做到元件失效對系統影響輕微設計,就有可能使用非車規元件做出更好的產品。
由于當前技術工藝限制的影響,不是每種需要用在汽車上的電子元件都可以達到所謂的車規要求。但為了實現汽車上的某些功能,就必須要用到這些元件。這種情況可以分為兩類:
a. 該功能的安全要求高,不能接受偏差
例子:緊急呼叫的 E-CALL 功能,為保證該功能,需要給設備安裝上后備電池。而該功能是涉及到生命安全的,按照某些公司的 ASILI(ISO26262)評級,要求達到 B 級。
而我們知道電池要做到 -40 度時保持高性能是很困難的。所以有公司的解決方案就是在電池上包上加熱電阻絲,在低溫時加熱它來保證性能,此時用單個元件的標準來看不合格,但作為零件總成,就可以滿足車廠的標準要求。這也可以看出整車廠的企業標準和元器件標準之間的關系。
b. 該功能一般不涉及安全,可以考慮接受偏差
如娛樂系統的液晶屏。在低溫時可能顯示的響應和光學性能都會下降。但這種情況會被打部分工程人員接受下來。
3. 一些「膽大」心不細的人,出于某些想法,如降低成本,或者可以獲得更好的性能,并僅想通過小數量的樣本,在較短時間來進行驗證其性能和可靠性,這種情況我只能說以后的事情靠人品了,誰都不清楚會發生什么。
來源:智能車產業庫
-
電子產品
+關注
關注
6文章
1112瀏覽量
57738 -
電子元器件
+關注
關注
133文章
3204瀏覽量
104038 -
車規級芯片
+關注
關注
2文章
230瀏覽量
12075
發布評論請先 登錄
相關推薦
評論