在現代制造工業中,隨著精密鑄件的復雜性和精度要求不斷提升,行業對先進的質量控制手段的需求也越來越強烈。激光三維掃描技術憑借其高精度、非接觸和高效的數據采集能力,正成為業界實現質量提升和成本控制的重要手段。
01 項目背景
本案例中的客戶專業從事傳統汽車、新能源汽車、通信、光伏儲能、逆變器、軌道交通、醫療航空及通用工業零部件鋁合金壓鑄和精密加工。公司以技術引領生產,以“高品質”為定位,注重產品質量與研發,憑借著近二十年的行業經驗和技術,在模具設計與制造、壓鑄工藝、半固態輕量化新工藝、精密數控加工技術等領域擁有多項專利和創新工藝。
項目中客戶需要測量的是汽車變速箱殼體表面三維數據,并進行加工余量分析。變速箱殼體是支撐和固定變速箱內部齒輪、軸承和其他零部件的重要部件,在車輛的動力傳動系統中起到了關鍵的保護作用。
變速箱內部有許多精密的齒輪、軸承和其他機械部件,殼體內外表面和安裝孔位的幾何公差會影響變速箱內部零部件裝配準確性,導致裝配偏差或部件磨損,因此需要嚴格把控變速箱殼體的加工精度。此外,變速箱殼體在車輛運行過程中承受較大的負載和應力,需要通過質量檢測識別表面缺陷,保證其在實際工作中的使用壽命和可靠性能。
02 客戶需求及痛點
客戶要求完成以下測量:1.全尺寸檢測:測量表面全尺寸三維數據,確保其符合設計規范;2.孔徑檢測:測量孔的直徑,尤其是用于軸和軸承的孔,以確保其在公差范圍內;3.加工余量檢測:確保足夠的加工余量,保證后續精加工質量。
變速箱殼體鑄件幾何形狀特征較為復雜,包含較多曲面、深腔、圓角、倒角及不規則型面,這給測量工作帶來了挑戰,客戶以往在測量室進行測量,存在較多不足之處:
1. 工件的深腔和死角結構較多,以往的測量手段只能獲取部分關鍵點的數據,無法完整采集表面數據。
2. 測量室測量復雜繁瑣,效率低下,且無法對檢測結果進行直觀全面的量化評估并生成余量分析報告,容易導致加工材料浪費,增加后續余量加工時間和成本。
03 解決方案及優勢
為了應對以上挑戰,客戶最終使用了思看科技SIMSCAN 42掌上三維掃描儀,該設備對于狹窄空間及死角處掃描的優勢十分顯著,是測量深腔鑄件的理想選擇,大大提高了檢測效率。
檢測過程:
1. 掃描:利用掃描儀全方位、多角度掃描殼體表面,確保表面特征均能被捕捉到。
一邊掃描,一邊實時生成高精度點云數據,設備體積小巧,便于進入深腔內部掃描,其超短相機基線可以輕松獲取狹縫及死角區域的三維數據,不遺漏細節之處,使得掃描數據更完整。
掃描過程非常高效,SIMSCAN 42以280萬次測量/秒的點云采集速率,僅需5分鐘即可完成掃描。
2. 三維建模:將點云數據進行簡單的處理,如擬合、拼接,最終轉化為實物的高精度三維模型。
設備精度高達0.020mm,對于腔體孔位、圓角及微小表面細節,均能精準還原。
3. 數據分析:借助專業軟件將實物模型與原始數模進行對比,生成詳細的色譜偏差圖,便于直觀地獲取表面及關鍵部位尺寸偏差信息。
4. 余量檢測:通過分析比對,確定加工余量,如果表面鑄件出現較大偏差或余量不足,則可以輔助工作人員進一步優化或調整加工工藝,確保成品符合設計要求及質量標準。
5. 數字化存檔:將所有的點云數據、分析報告進行數字化存檔,作為制造過程各階段狀況的數字記錄,以便后續質量追蹤和管理。這些數據還可以作為產品質量的參考,為后續批次的生產及質量控制提供依據,確保產品的可追溯性。
04 項目小結
借助SIMSCAN對汽車發動機變速箱殼體深腔鑄件進行了全尺寸及余量檢測。針對死角多、結構復雜的腔體結構,SIMSCAN在整個檢測過程中展現出了顯著的性能優勢,憑借非接觸、小巧便攜、高精度等特征,有效提升了檢測效率和加工精度,極大程度簡化了生產工藝流程,為客戶提供更加全面、更有效率、更具性價比的檢測方案,助力客戶邁向高質量、智能化、數字化生產轉型之路。
審核編輯 黃宇
-
變速箱
+關注
關注
4文章
169瀏覽量
18713 -
3D掃描
+關注
關注
2文章
98瀏覽量
21508
發布評論請先 登錄
相關推薦
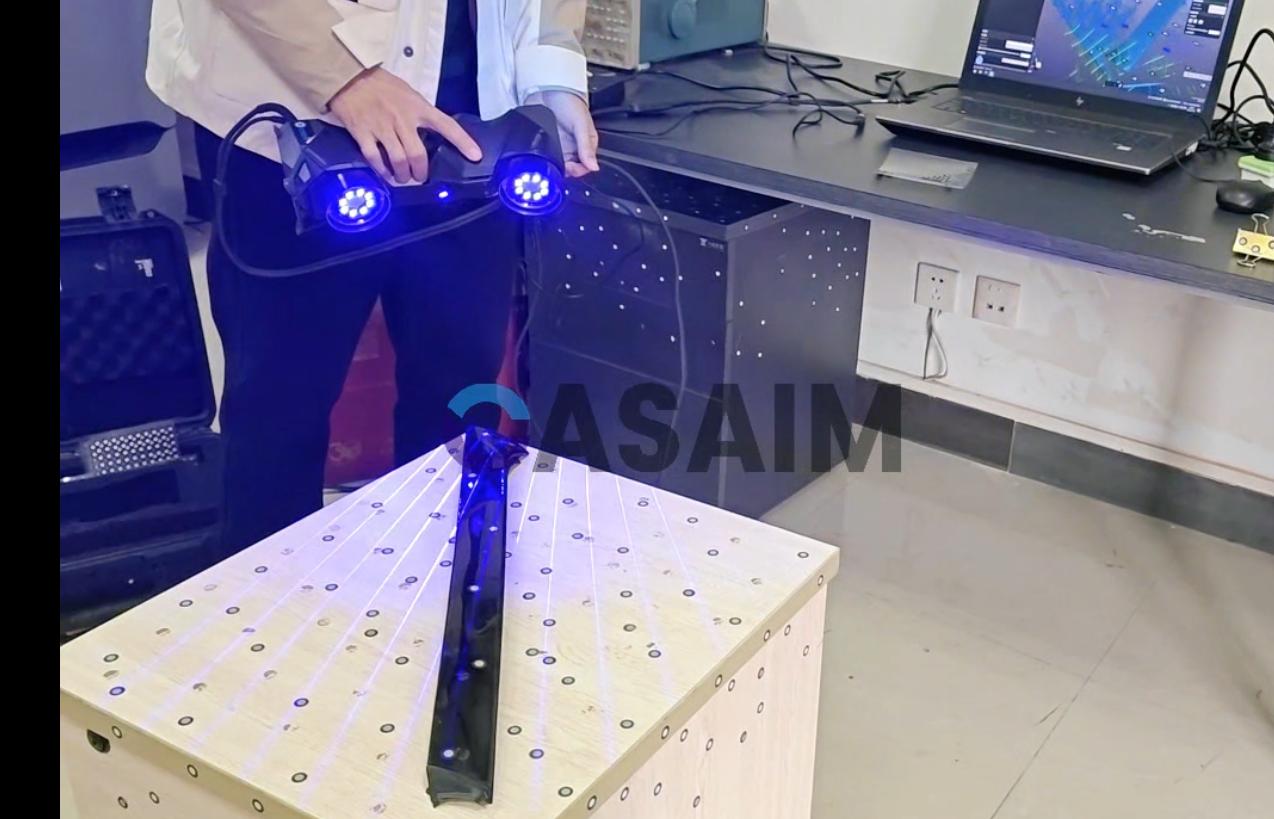
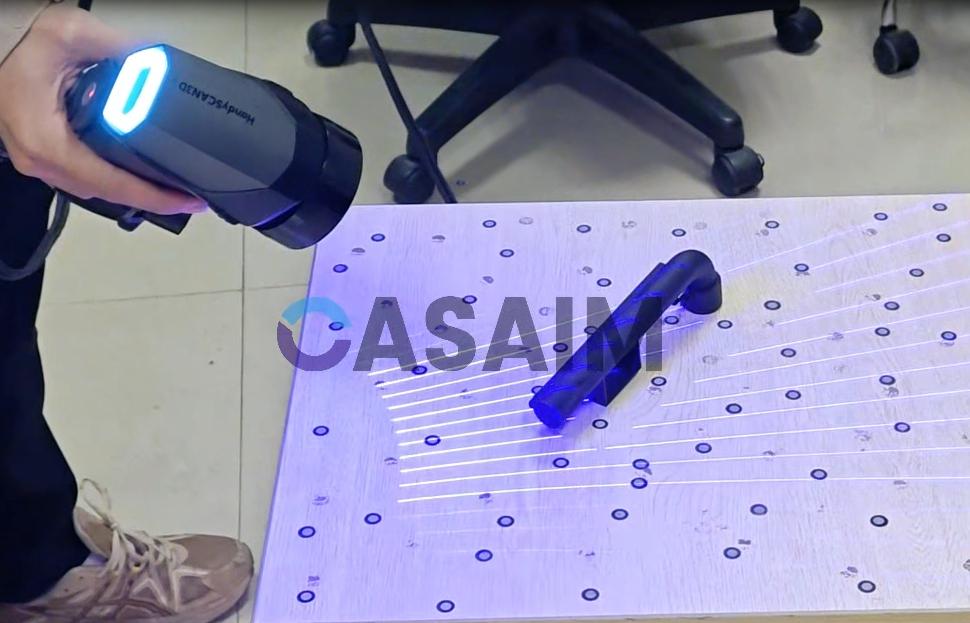
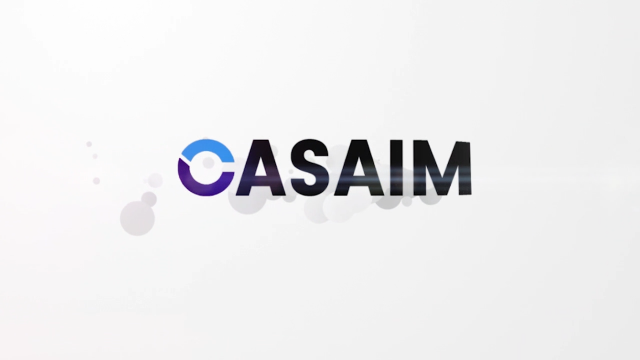
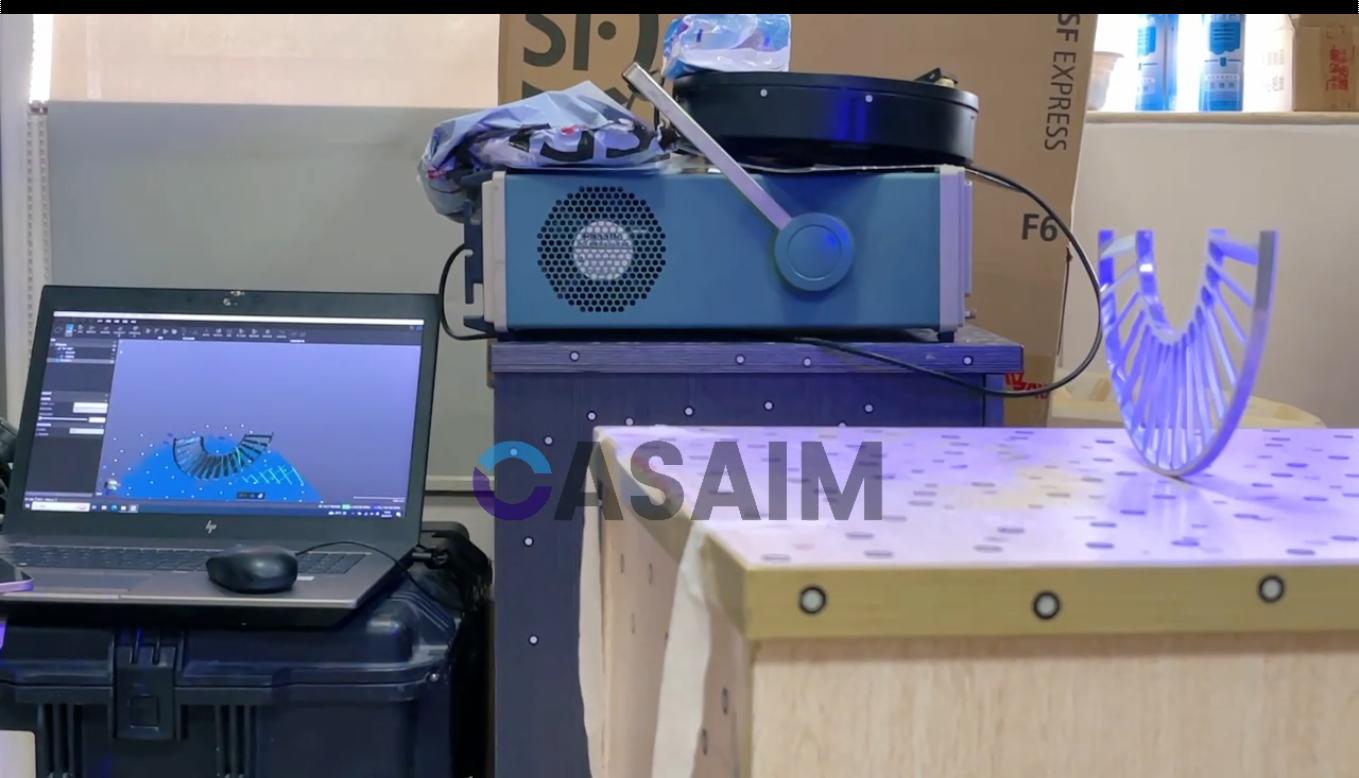
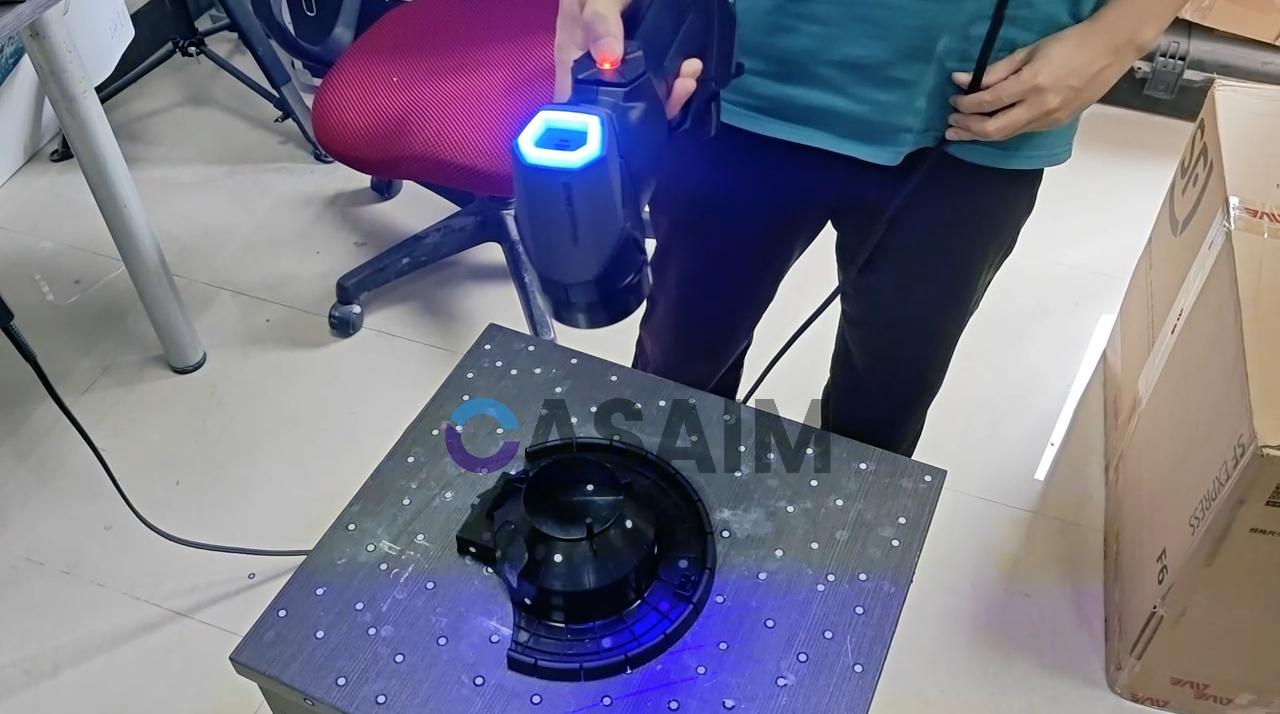
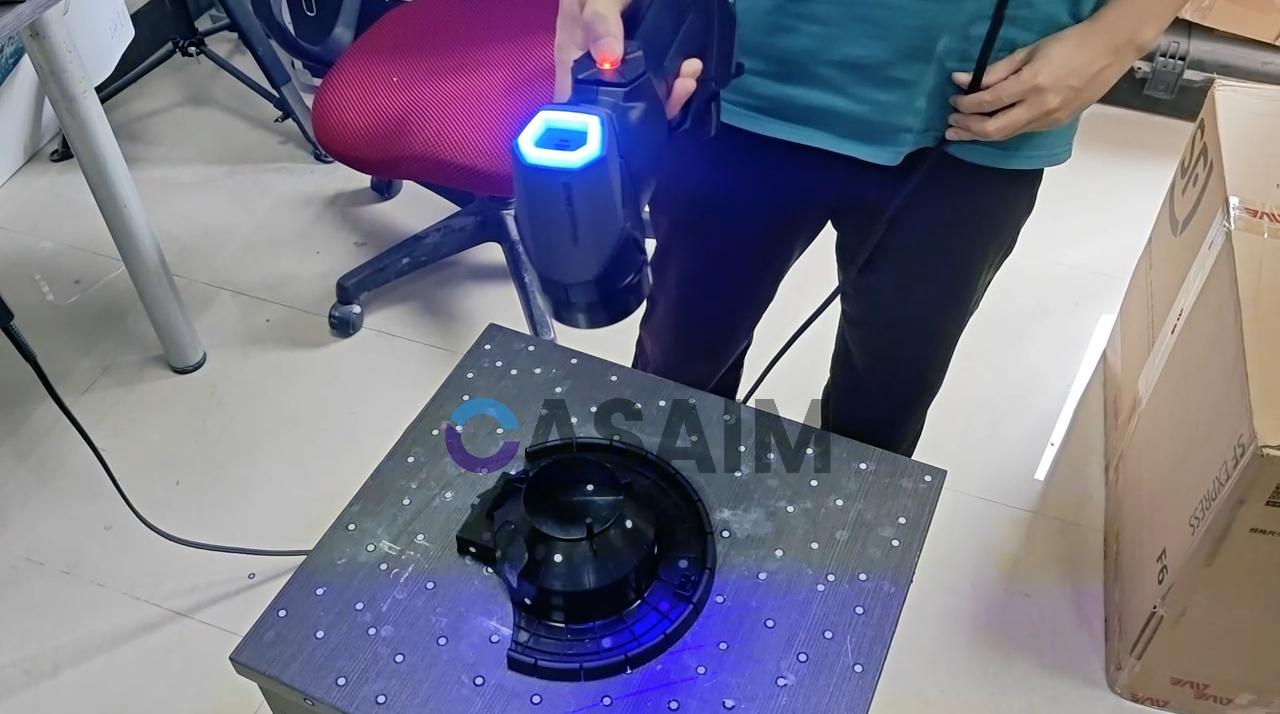
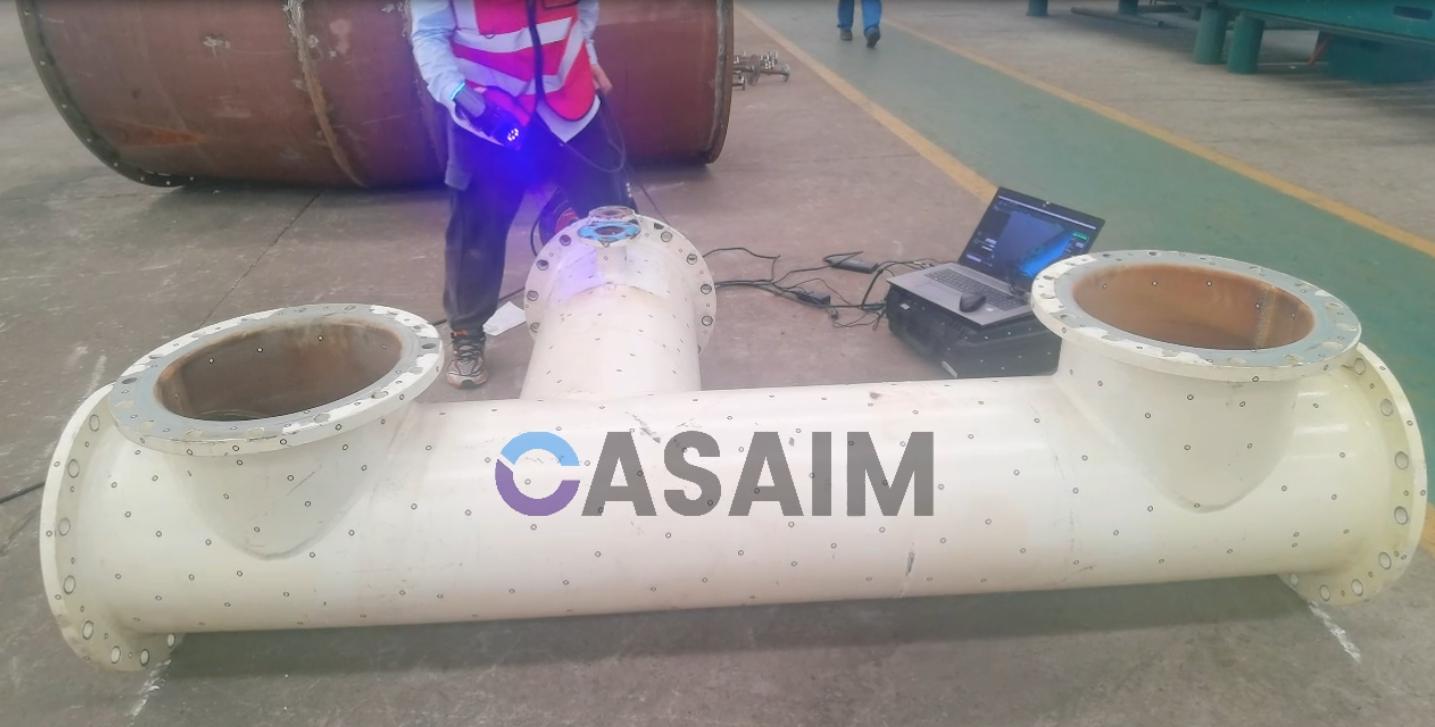
日本車自動擋為何偏愛CVT變速箱
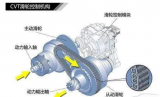
各種類型變速箱油的區別與選擇
dct變速箱和at變速箱哪個更好?
3D掃描儀助力大尺寸汽車鈑金件模具加工檢測
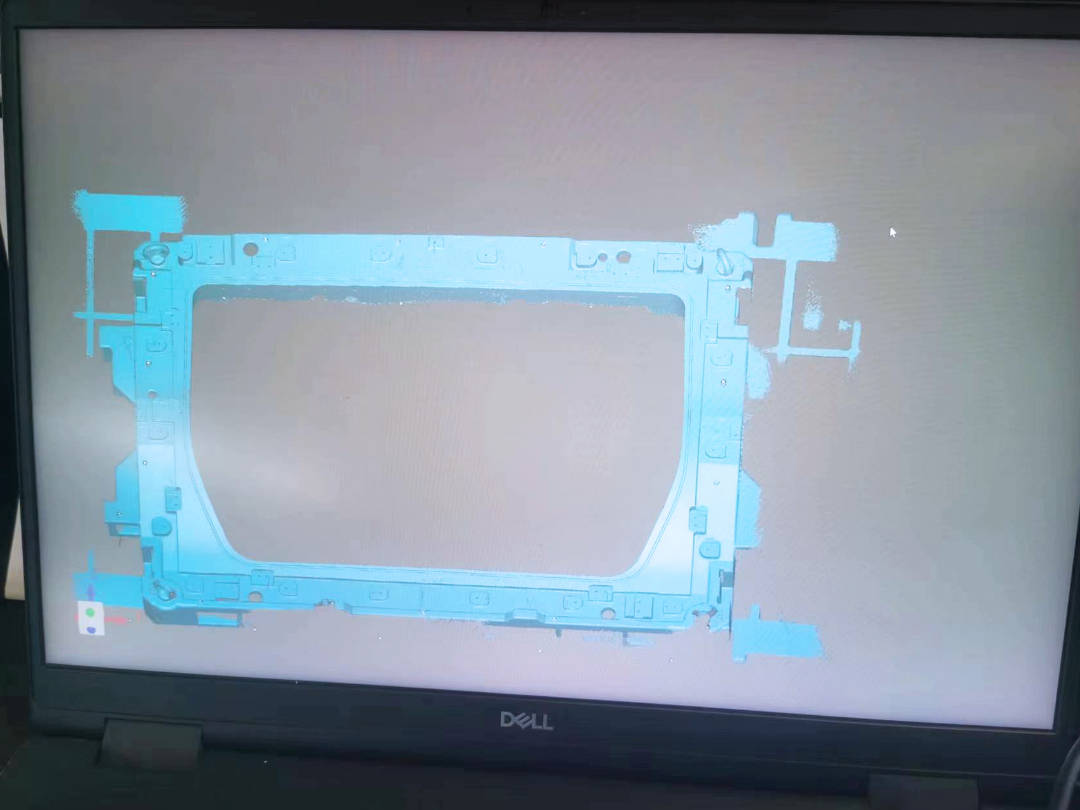
評論