以下文章來源于字母哥電子技術,作者劉喜科
一、HDI應用現(xiàn)狀
隨著目前電子產(chǎn)品持續(xù)而迅速小型化、輕便化、多功能化的趨勢,高密度的安裝技術的發(fā)展,行業(yè)上對于作為原件載體和連接體的印制電路提出了更高的要求,以便其能夠成為具有高密度、高精度、高可靠性并且能大幅度提高組裝密度的電子元部件。因此應用于新的PCB工藝技術的高密度互連HDI被廣泛應用于各種電子產(chǎn)品。而HDI疊孔技術作為HDI制作過程中比較高端的一種工藝技術,不僅可以實現(xiàn)線路板內(nèi)部層次間的選擇性互聯(lián),充分提高了線路板的布線密度以及空間利用率。盲孔疊孔制作過程中所采用的電鍍填孔工藝,可有效的提高線路板的焊接面積,消除虛焊的隱患,減少焊盤中盲孔焊接氣泡的產(chǎn)生,增強了焊接的可靠性,同時,填孔后線路板表面平整,有利于密集線路的制作,疊孔形成的銅柱提高了線路板的散熱功能。
二、疊孔分類
① 一階HDI板(無埋孔)
②一階HDI板(有埋孔
③二階HDI板(含疊孔、階梯孔)
④二階HDI板(含疊孔、階梯孔、孔上墊
⑤三階HDI板(含疊孔、階梯孔)
⑥任意層互聯(lián)
三、實例研究
本文以六層帶疊加導通孔無鐵芯印制板的工藝為主要講解,重點介紹盲孔疊孔填孔制造工藝。
示例產(chǎn)品的技術要求:
--設計層數(shù):6層
--芯板厚度:0.1mm(H/H)含銅
--板厚:0.38±0.05mm(成品)
--電鍍要求:所有盲埋孔做電鍍填孔工藝
--最小線寬/線距設計:2mil/2mil(局部削PAD保證線距)
--盲孔最小ring:設計:2mil
■ 疊孔制作圖示
此板盲孔的制作從芯板層開始制作,每層均有盲孔設計,隨著層數(shù)的增加,盲孔疊孔數(shù)量亦隨之增加,疊孔制作過程如下圖:
■ 層壓結構圖示
此板是以L3/4層作為母板,采用減成法進行制作,共進行兩次壓合,其壓合結構如下圖:
■ 工藝流程
>>內(nèi)層制作流程(L3/4層):
>>次外層制作流程(L2/5層):
>>外層制作流程(L1/6層):
注解:在各個層別制作過程中,共進行了3次激光鉆孔,6次棕化減銅,3次電鍍流程,其中激光鉆孔前減銅是將銅箔減至7-9um厚度,為激光鉆孔預處理;圖轉前減銅是將銅箔減至精細線路制作要求的厚度。
■ 制作難點分解
1. 板薄:內(nèi)層芯板0.1mm H/HOZ(含銅),傳統(tǒng)水平線時易造成卡板;
2. 采用鐳射在0.1mm板厚上鉆通孔, 0.1mm的機械鉆生產(chǎn)成本較高,而對于0.1mm板厚上的鐳射鉆孔生產(chǎn)盡管大大降低了時間,卻對孔型、鐳射鉆參 數(shù)、鉆孔精度控制等技術提出了更高的要求;
3. 埋孔電鍍填孔,對通孔做電鍍填孔難度高,一方面填孔飽滿度很難保證,另一方面又要顧及到表銅的銅厚均勻性;
4. 盲孔電鍍填孔,不允許有空洞,且盲孔表面平整度小于10um;
5. 采用填孔工藝后,板面鍍銅均勻性控制難,薄板采用傳統(tǒng)垂直電鍍的鍍層均勻性控制;
6. 蝕刻后線寬/線距的控制,2mil/2mil±10%,所以面銅均勻性必須控制85%以上以滿足蝕刻的要求;
7. 盲孔疊孔對準度的控制,上、下盲孔對準度控制±1.5mil。
■ 設計調(diào)整
1. 由于板薄,在過水平線時,容易卷板,且水壓大時會造成板面上下受壓力過大,造成板裂等。因此在設計時采用兩面錯位的方式在基材區(qū)鋪設銅皮,板邊四周采用流膠塊與大銅皮相結合的方式進行設計,盡可能的增加板的應力;
2. 因內(nèi)層埋孔需采用電鍍填孔的方式,按現(xiàn)行的工藝制程能力是極難制作的,所以鐳射時采用制作盲孔的形式,即鐳射不射穿L4的銅皮形成盲孔,利于電鍍填孔;
3. 盲孔填孔工藝的選擇,采用專用填孔藥水,確保盲孔表面平整度;
4. 由于線路密集且最小線寬/線距只有2mil/2mil,必須確保面銅的均勻性,保證蝕刻均勻性,因此采用傳統(tǒng)垂直電鍍時,必須改良電鍍方式,選用特制邊框夾具進行垂直電鍍,并能有效控制電銅均勻性;
5.因盲孔疊孔對準度要求高,必須建立一套系統(tǒng)的對位控制程序,保證盲孔對準度以及上、下盲孔疊孔對準度。
■ 實際制作過程控制
1. 板內(nèi)圖形輔助設計:
考慮到芯板較薄,蝕刻后基板與殘銅受力不均勻,容易造成板裂,因此在設計時基材區(qū)采用鋪設陰陽銅粒或銅皮,如下圖:
2. 由機械鉆孔設計
考慮到芯板無通孔設計,不利于電鍍時藥水交換,故利用在圖形間采用平均分布鉆排氣孔的方式來滿足電鍍藥水交換的充分性,從而確保面銅的均勻性,排氣孔設計見下圖 :
3. 對位控制系統(tǒng):
3.1 影響盲孔的疊孔精度的最主要的影響因素就在于圖形的對位精度及層間的AB差,影響疊孔對位精度的主要因素魚骨圖分布如下:
3.2. 對位系統(tǒng)選擇:
a.內(nèi)層埋孔及圖形,均以同一系統(tǒng)的機械鉆孔定位,同時制作出第一次壓合的靶標圖形;
b.次外層鐳射孔D23、D54:分別以內(nèi)層L3、L4圖形靶標定位;
c.次外層線路:以第一次壓合后X-RAY孔對位,同時制作出第二次壓合的靶標圖形;
d.外層鐳射孔D12、D65:分別以次外層L2、L5圖形靶標定位;
e.外層線路:以第二次壓合后X-RAY孔定位;
通過以上的控制點確保了埋孔、內(nèi)層線路、次外層線路、次外層盲孔、外層線路、外層盲孔均在同樣的對位控制系統(tǒng)上,因此板件的對準度也得到有效的控制。
通過以上對位系統(tǒng)的選擇與控制,實現(xiàn)了各層次盲孔間的精準疊加,如下圖:
通過上述的控制系統(tǒng),疊孔精度可以做到±1.5mil以內(nèi),且從上述控制系統(tǒng)中可以看出,層別圖形對位精度及層間對位精度是影響盲孔疊孔精度的最關鍵因素。通過對以上對位系統(tǒng)進行技術沉淀以及改進,已成功應用于實際生產(chǎn)制造中,已成功制作出10層HDI銅柱疊孔板,如上圖。
4. 盲孔電鍍填孔
盲孔結構與通孔結構不同,通孔在攪拌等外力作用下,鍍液在板兩面形成壓力差進行藥水交換,就可得到較好的銅沉積.而盲孔電鍍,鍍液完全是僅靠一個開口進行藥水交換,依靠物理作用是很難完成的,因此,必須依靠化學添加劑的控制而完成的,其次是適當進行攪拌輔助完成的.這里用到了電鍍填孔藥水及特殊參數(shù)。電鍍填孔化學添加劑主要成分及作用如下:
a.加速劑:加速銅的沉積;
b.整平劑:如整平劑吸附在高電流區(qū)時,可以抑制銅的沉積,對表面或孔壁凹凸不平區(qū)有整平作用;
c.抑制劑:填孔時對銅的沉積有抑制作用,抑制高電流區(qū)電鍍銅的沉積速率,同時提高低電流區(qū)電鍍銅沉積;
通過對電鍍填孔參數(shù)的調(diào)整,每一層盲孔的填孔率均能達到85%以上,盲孔凹陷小于15um,實現(xiàn)了多階HDI板盲孔疊孔的制作,如下圖:
5. 電鍍均勻性的控制:
此板內(nèi)層芯板厚度不到0.1 mm(次外層0.2-0.25mm,外層0.3-0.33mm),板件很軟,根本不足以支撐銅缸內(nèi)浮架,加工過程中板件容易變形彎曲,甚至卷板,鍍層均勻性根本不能得到有效保證.為了有效保證鍍層均勻性,因此采用專用的電鍍夾具框來實現(xiàn)薄板電鍍工藝。上、下夾具框各一個以及相對應鉚釘孔組成一套完整的薄板夾具框,在與夾具對應尺寸的薄板上鉆相應的鉚釘孔,在沉銅板電前,根據(jù)相對應的鉚釘孔把板鉚在上、下夾具框中,形成一個帶框的薄板,如下圖。此薄板夾具框利用覆銅板板框及鉚釘實現(xiàn)飛巴上夾具與加工板件的電流傳導,由于有覆銅板板框,電鍍飛巴與銅缸浮架的受力通過夾具框來分擔,從而避免了薄板在加工過程中的變形,確保鍍層均勻性,實現(xiàn)薄板在垂直電鍍線的正常加工。
四、結論分享
1. 通過對HDI板整個生產(chǎn)時的對位系統(tǒng)進行科學有效的控制,提高了盲孔的疊孔精度,使盲孔的疊孔精度小于1.5mil;
2. 電鍍過程中采用輔助薄板電鍍夾具以及電鍍參數(shù)、藥水的調(diào)整,實現(xiàn)了盲孔填孔、孔面凹陷小、表銅均勻性高的目的。
3. 由于盲孔在電鍍過程中需要進行電鍍填孔,表銅的厚度亦較大,無法實現(xiàn)2/2mil精細線路的制作,故在電鍍后線路制作前,采用減銅的方法,使面銅厚度達到精細線路的制作要求。
-
電子產(chǎn)品
+關注
關注
6文章
1148瀏覽量
58200 -
pcb
+關注
關注
4318文章
23022瀏覽量
396423 -
制造工藝
+關注
關注
2文章
176瀏覽量
19734 -
HDI板
+關注
關注
2文章
55瀏覽量
15611
原文標題:多層HDI板疊孔制造工藝研究
文章出處:【微信號:深圳市賽姆烯金科技有限公司,微信公眾號:深圳市賽姆烯金科技有限公司】歡迎添加關注!文章轉載請注明出處。
發(fā)布評論請先 登錄
相關推薦
什么是HDI?PCB設計基礎與HDI PCB制造工藝
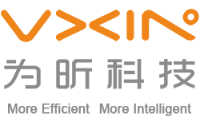
HDI(盲、埋孔)板壓合問題
可制造性拓展篇│HDI(盲、埋孔)板壓合問題
如何判斷盲/埋孔HDI板有多少“階”?
可制造性拓展篇│HDI(盲、埋孔)板壓合問題
[華秋干貨鋪]可制造性拓展篇│HDI(盲、埋孔)板壓合問題
高密度互連板與普通HDI板的區(qū)別
hdi盲埋孔線路板生產(chǎn)工藝流程
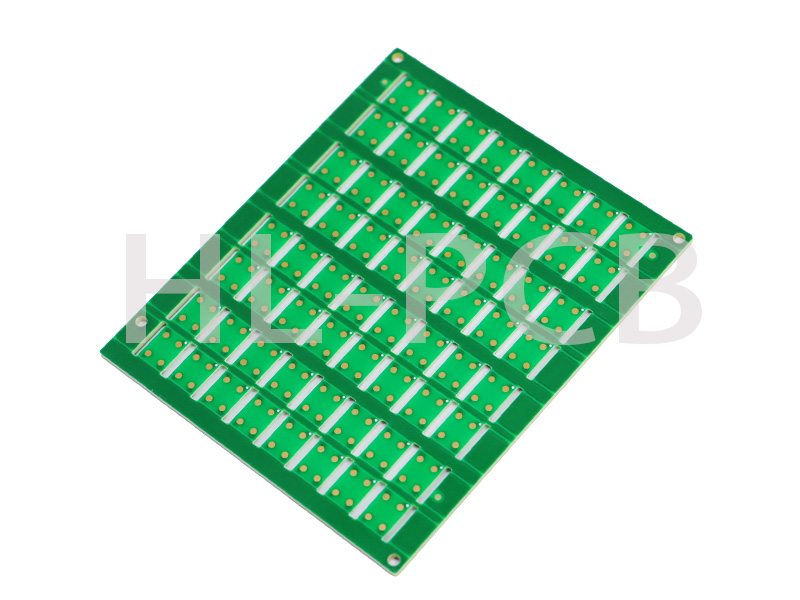
PCB HDI產(chǎn)品的介紹
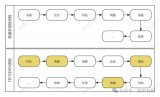
評論