隨著工業4.0和智能制造的興起,PLC控制系統作為工業自動化的基石,正面臨著前所未有的發展機遇。
1. 技術革新
1.1 高性能處理器
隨著微處理器技術的發展,PLC的處理器性能得到了顯著提升。現代PLC通常采用多核處理器,能夠處理更復雜的算法和高速數據流,滿足高速、高精度控制的需求。
1.2 更大的存儲容量
隨著控制邏輯和數據量的增加,PLC的存儲容量也在不斷擴大。這使得PLC能夠存儲更多的程序代碼、歷史數據和診斷信息,為系統分析和優化提供了更多可能。
1.3 高分辨率和高精度
現代PLC系統支持高分辨率和高精度的輸入/輸出模塊,能夠實現更精細的控制和測量,滿足精密制造和質量控制的需求。
2. 通信與網絡化
2.1 以太網通信
以太網已成為PLC通信的主流技術,它提供了高速、可靠的數據傳輸能力,支持大規模分布式控制系統的構建。
2.2 無線通信技術
無線通信技術,如Wi-Fi、藍牙和ZigBee,正在被越來越多地集成到PLC系統中,以實現設備的無線連接和遠程監控。
2.3 物聯網(IoT)集成
PLC系統正逐漸與物聯網技術融合,通過集成傳感器和執行器,實現設備的智能監控和遠程控制。
3. 軟件和編程
3.1 編程語言的標準化
IEC 61131-3標準為PLC編程語言提供了統一的框架,包括梯形圖(Ladder Diagram)、功能塊圖(Function Block Diagram)等,這促進了不同PLC系統之間的兼容性和互操作性。
3.2 面向對象編程(OOP)
面向對象編程技術的應用使得PLC程序更加模塊化和易于維護,提高了程序的可重用性和靈活性。
3.3 軟件集成與仿真
現代PLC系統通常集成了高級編程軟件和仿真工具,支持離線編程和調試,縮短了系統開發和調試的時間。
4. 安全性與可靠性
4.1 網絡安全
隨著PLC系統越來越多地接入網絡,網絡安全成為重要議題。現代PLC系統提供了多層次的安全措施,包括防火墻、VPN和加密通信等。
4.2 冗余和容錯
為了提高系統的可靠性,PLC系統采用了冗余設計和容錯技術,如雙機熱備、三重模塊冗余(TMR)等,確保關鍵控制任務的連續性。
5. 集成與兼容性
5.1 與MES/ERP系統的集成
PLC系統正越來越多地與制造執行系統(MES)和企業資源規劃(ERP)系統集成,實現生產數據的實時共享和優化。
5.2 跨平臺兼容性
隨著不同制造商PLC系統的標準化,跨平臺兼容性問題得到了改善,用戶可以更容易地集成不同品牌的PLC產品。
6. 人工智能與機器學習
6.1 智能控制算法
PLC系統開始集成智能控制算法,如模糊邏輯、神經網絡和遺傳算法,以實現更復雜的控制策略和自適應控制。
6.2 機器學習
機器學習技術的應用使得PLC系統能夠從歷史數據中學習,優化控制參數,提高系統的響應速度和效率。
7. 環境與能效
7.1 能效優化
隨著環保意識的增強,PLC系統在設計時更加注重能效,通過優化控制策略和減少能耗來降低生產成本。
7.2 環境監測
PLC系統可以集成環境監測傳感器,實時監控工廠環境,確保生產過程的環保和安全。
結論
PLC控制系統的最新發展趨勢表明,它們正在變得更加智能、互聯和高效。隨著技術的不斷進步,PLC系統將繼續在工業自動化領域扮演關鍵角色,推動制造業向更高層次的智能化和自動化發展。
-
PLC控制系統
+關注
關注
1文章
65瀏覽量
15788 -
工業自動化
+關注
關注
17文章
2299瀏覽量
67177 -
工業4.0
+關注
關注
48文章
2001瀏覽量
118528
發布評論請先 登錄
相關推薦
黑芝麻智能亮相2024高端芯片產業創新發展大會
PLC控制系統與DCS的區別
飛凌嵌入式受邀亮相TI嵌入式技術創新發展研討會
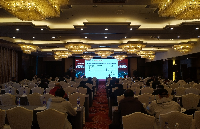
評論