一、引言
隨著工業(yè)水平的不斷進(jìn)步,航空機(jī)載產(chǎn)品呈現(xiàn)出復(fù)雜化、輕量化、精密化的發(fā)展趨勢(shì),這使得裝配精度要求持續(xù)提高,裝調(diào)難度也日益增加。在這種背景下,自動(dòng)精密裝配技術(shù)已然成為航空航天等領(lǐng)域產(chǎn)品的關(guān)鍵技術(shù)之一。微小型零件的自動(dòng)精密裝配發(fā)展迅速,從早期在顯微鏡下的手工裝配逐步發(fā)展到半自動(dòng)、自動(dòng)化裝配階段,而模塊化裝配系統(tǒng)也日益成為發(fā)展的主流方向。
二、微小型零件裝配的挑戰(zhàn)與需求
微小型零件的多樣化發(fā)展,使得不同的器件需要專(zhuān)門(mén)設(shè)計(jì)和制造特定的結(jié)構(gòu)來(lái)實(shí)現(xiàn)裝調(diào)。在精密裝配過(guò)程中,零件的制造公差和裝調(diào)位置的偏差需要逐件進(jìn)行補(bǔ)償,有些情況甚至需要人工干預(yù)才能確保裝配的順利完成。隨著零件不斷地微型化和精密化,必須避免在裝調(diào)過(guò)程中對(duì)零件造成損傷,以免影響產(chǎn)品的性能。
以懸絲擺式加速度計(jì)為例,它廣泛應(yīng)用于航空、航天等領(lǐng)域,具有量程大、體積小、抗沖擊、精度高等特性,是慣性導(dǎo)航中的核心組成部分。然而,目前該加速度計(jì)的裝配生產(chǎn)主要依賴(lài)手工操作,憑借工人的經(jīng)驗(yàn)和焊接技能來(lái)完成裝配。這種方式對(duì)工人的操作熟練度要求極高,很難保證裝配精度和產(chǎn)品的一致性,也難以實(shí)現(xiàn)大規(guī)模生產(chǎn)。
三、自動(dòng)焊接技術(shù)的現(xiàn)狀與局限
自動(dòng)焊接技術(shù)在機(jī)械加工中具有十分重要的意義。目前的研究表明,焊接機(jī)器人在自動(dòng)焊接技術(shù)中仍占據(jù)主要地位。但是,焊接機(jī)器人由于操作難度相對(duì)較大、成本較高以及結(jié)構(gòu)比較復(fù)雜等因素,導(dǎo)致不能大規(guī)模地應(yīng)用于生產(chǎn)環(huán)節(jié)當(dāng)中。此外,焊接機(jī)器人所需的運(yùn)動(dòng)空間大,在運(yùn)動(dòng)中需要合理的軌跡規(guī)劃,而在狹小的操作空間內(nèi)顯得靈活性不足,存在無(wú)法進(jìn)行施焊的情況。
四、大研智造激光錫球自動(dòng)焊錫技術(shù)的優(yōu)勢(shì)
本文介紹了大研智造的激光錫球自動(dòng)焊錫技術(shù),該技術(shù)集成了力、溫度傳感器和機(jī)器視覺(jué)于一體的自動(dòng)精密焊接系統(tǒng),具有以下顯著優(yōu)勢(shì):
采用龍門(mén)直角坐標(biāo)式機(jī)械結(jié)構(gòu),配合焊槍旋轉(zhuǎn)軸,結(jié)合高、低倍率顯微視覺(jué)相結(jié)合的視覺(jué)檢測(cè)方式,實(shí)現(xiàn)基部與目標(biāo)部的高精度對(duì)準(zhǔn),焊接精度達(dá)到 0.1mm。
能夠控制機(jī)械臂和精密平臺(tái)運(yùn)動(dòng),完成微球高精度的姿態(tài)調(diào)整、微球和微管的自動(dòng)對(duì)準(zhǔn)及裝配。
設(shè)計(jì)專(zhuān)用焊接單元集成力和溫度傳感器,在有限空間內(nèi)實(shí)現(xiàn)對(duì)懸絲張緊情況下微小器件的自動(dòng)溫控焊接,提高了微結(jié)構(gòu)精密裝配的自動(dòng)化程度和質(zhì)量。
五、精密加速度計(jì)組件自動(dòng)裝配系統(tǒng)硬件
(一)模塊化設(shè)計(jì)
根據(jù)裝配任務(wù)及難點(diǎn),采用模塊化設(shè)計(jì)思想研制了該自動(dòng)焊接系統(tǒng)。系統(tǒng)分為工作臺(tái)模塊、視覺(jué)測(cè)量模塊、焊接模塊及焊錫片放置模塊。各模塊之間互不干涉,又相互配合,極大地提高了裝配效率以及設(shè)備的復(fù)用性。
(二)視覺(jué)測(cè)量模塊
重要作用:在整個(gè)裝配過(guò)程中,機(jī)器視覺(jué)系統(tǒng)起著至關(guān)重要的作用,包括待裝配零件的識(shí)別與定位、裝配結(jié)果測(cè)量以及裝配過(guò)程可視化,關(guān)系到整個(gè)裝配流程的精度及質(zhì)量。
組成部分:機(jī)器視覺(jué)系統(tǒng)主要由工業(yè)相機(jī)、遠(yuǎn)心鏡頭、同軸–環(huán)形光源組成。
測(cè)量方案:采用可移動(dòng)的視覺(jué)測(cè)量方案,配合 3 自由度精密位移滑臺(tái),其重復(fù)定位精度為 ±0.5μm。不僅擴(kuò)大了測(cè)量范圍,解決了相機(jī)視場(chǎng)不足的問(wèn)題,而且能夠控制圖像位置,確保待測(cè)量零件位于相機(jī)視野中心。相機(jī)采集圖像并傳入上位機(jī)進(jìn)行圖像處理;遠(yuǎn)心鏡頭可以消除由于被測(cè)物體距離鏡頭位置不同造成的圖像畸變。環(huán)形光源安裝于相機(jī)鏡頭前,使相機(jī)能清楚地觀察零件的邊緣特征;同軸光源安裝在鏡頭一側(cè),以改善零件平面反射成像,二者配合提高圖像質(zhì)量。
(三)焊接模塊
功能與組成:焊接模塊集成于視覺(jué)測(cè)量模塊,以機(jī)械臂為載體,由焊接組件及力傳感器組成,其主要功能是將懸絲焊接到加速度計(jì)底座設(shè)定位置,完成組件裝配的最后一步。焊接組件由焊接頭、加熱棒、溫度傳感器、隔熱材料等構(gòu)成。其中,焊接頭采用黃銅材料制成,表面鍍鉻處理,防止焊接頭沾錫影響焊接效果。焊接頭末端設(shè)計(jì)有一定深度的槽形,在焊接過(guò)程中使錫球嵌入其中。
工作原理:激光將焊錫熔化后,在高濃度氮?dú)獾膰娚渥饔孟略诤副P(pán)匯集冷卻形成焊點(diǎn),控制焊接位置,保證焊接質(zhì)量。溫度控制調(diào)節(jié)模塊的工作原理基于閉環(huán)反饋控制。激光焊錫機(jī)采用激光作為加熱源,通過(guò)紅外檢測(cè)方式實(shí)時(shí)檢測(cè)激光對(duì)加工件的紅外熱輻射,形成激光焊接溫度和檢測(cè)溫度的閉環(huán)控制??刂瓢?PID 調(diào)節(jié)功能可以有效控制激光焊接溫度在設(shè)定范圍內(nèi)的波動(dòng)。首先,鉑電阻溫度傳感器實(shí)時(shí)獲取焊接頭溫度,溫度控制器通過(guò)模糊 PID 自整定模式調(diào)節(jié)變壓器通斷,進(jìn)而控制加熱。工人實(shí)際操作經(jīng)驗(yàn)的焊接溫度為 250℃,焊接時(shí)適當(dāng)提高控制溫度可以確保焊接頭達(dá)到足夠的焊接溫度,保證焊錫完全熔化,最終確定焊接控制溫度為 255℃左右。
(四)焊錫片放置模塊
設(shè)計(jì)目的:由于操作空間有限,且焊接面及焊錫片微小,人眼不易觀察,因此設(shè)計(jì)了焊錫片放置模塊。
工作方式:首先末端針頭依靠黏附力拾取焊錫片,由相機(jī)獲取當(dāng)前焊錫片的位置后,手動(dòng)調(diào)整三軸微調(diào)平臺(tái)旋鈕,將焊錫片放置到理論位置。該模塊降低了焊錫片放置難度,并保證焊點(diǎn)位置準(zhǔn)確。
六、焊接流程及控制策略
合理高效的焊接流程及控制策略在微裝配系統(tǒng)中起著至關(guān)重要的作用。由于待裝配零件結(jié)構(gòu)復(fù)雜,可操作空間有限,因此采用 “Look and Move” 的焊接控制模式。首先由視覺(jué)系統(tǒng)獲取零件位姿信息,通過(guò)分析計(jì)算,最后控制精密滑臺(tái)運(yùn)動(dòng)至目標(biāo)位置。通過(guò)機(jī)器視覺(jué)及反饋信息引導(dǎo)裝配作業(yè),消除零件位姿微小變動(dòng)造成的偏差,提高裝配精度及質(zhì)量。
在視覺(jué)測(cè)量模塊引導(dǎo)下,通過(guò)焊錫片裝調(diào)模塊放置焊錫片。由于焊錫片與末端針頭處于不同的景深范圍,同時(shí)末端針頭直徑僅 0.45mm,不易觀測(cè),但是能夠在視場(chǎng)范圍內(nèi)獲取焊錫片的清晰圖像,通過(guò)調(diào)整三軸微調(diào)平臺(tái)來(lái)調(diào)整焊錫片位置,確保焊點(diǎn)位置準(zhǔn)確。
焊接模塊集成懸臂梁式力傳感器,能夠?qū)崟r(shí)檢測(cè)焊接接觸力。在傳統(tǒng)的烙鐵焊接過(guò)程中,焊錫片的熔化導(dǎo)致焊接接觸力不斷變化。而激光焊接具有非接觸焊接特性,焊接不受摩擦、靜電等外力影響。激光錫球全自動(dòng)焊錫機(jī)可根據(jù)焊錫片厚度設(shè)定焊接噴嘴與焊盤(pán)之間的微小距離,保證焊錫片受熱均勻、完全熔化,焊接完成后快速抬起離開(kāi)焊接位置,完成焊接操作。具體焊接流程如圖所示。
七、裝配試驗(yàn)
使用該自動(dòng)裝配系統(tǒng)對(duì)隨機(jī)選取零件進(jìn)行裝配及焊接試驗(yàn),將擺組件和加速度計(jì)底座分別安裝到上料平臺(tái),操作裝配軟件系統(tǒng)完成裝配任務(wù)。
(一)焊接結(jié)果
焊接完成后,在顯微鏡下觀測(cè)焊接結(jié)果。焊錫熔化后凝固效果良好,不存在焊錫流向懸絲的現(xiàn)象,微小焊點(diǎn)位置準(zhǔn)確、質(zhì)量可靠,無(wú)虛焊。
(二)間隙及位置調(diào)整
采用標(biāo)準(zhǔn)標(biāo)定尺(制造精度 1μm),在滿視場(chǎng)的情況下對(duì)相機(jī)的實(shí)際像素進(jìn)行測(cè)量標(biāo)定,標(biāo)定結(jié)果為 X、Y 方向像素尺寸均為 1.745μm/pixel。擺組件相對(duì)于磁鋼間隙的測(cè)量距離為 1mm 左右;懸絲中心相對(duì)于底座底面位置調(diào)整依靠精密滑臺(tái)運(yùn)動(dòng)擴(kuò)大圖像采集范圍。系統(tǒng)采用三維精密位移滑臺(tái),其重復(fù)定位精度可達(dá) ±0.5μm,從誤差累積原理上來(lái)說(shuō),精度能夠滿足小于 10μm 的要求。
待裝配零件質(zhì)量存在差異,一致性較差,因此會(huì)對(duì)裝配結(jié)果產(chǎn)生一定的影響。裝配完成后,通過(guò)視覺(jué)系統(tǒng)對(duì)裝配結(jié)果進(jìn)行測(cè)量,其測(cè)量原理與上文裝配調(diào)整的方法類(lèi)似,測(cè)量擺組件相對(duì)于磁鋼間隙,以及懸絲中心相對(duì)于底座底面間距。總體來(lái)看,擺組件相對(duì)于磁鋼間隙偏差小于 10μm,懸絲中心相對(duì)于底座底面位置精度優(yōu)于 20μm,能夠滿足裝配精度要求。
本文的自動(dòng)焊接系統(tǒng)能夠完成加速度計(jì)組件的自動(dòng)精密焊接,滿足裝配精度要求,改善了裝配質(zhì)量,能夠?qū)崿F(xiàn)加速度計(jì)底座組件裝配作業(yè)自動(dòng)化。
八、結(jié)論
針對(duì)加速度計(jì)組件手工裝配困難的問(wèn)題,研制了專(zhuān)用自動(dòng)化裝配及焊接系統(tǒng),實(shí)現(xiàn)零件焊接等任務(wù),以自動(dòng)化設(shè)備替代人工裝配,能夠確保裝配過(guò)程中精確定位以及微力控制。通過(guò)裝配試驗(yàn)驗(yàn)證了系統(tǒng)的可行性,試驗(yàn)結(jié)果表明,焊點(diǎn)位置準(zhǔn)確,無(wú)虛焊,擺組件相對(duì)于磁鋼間隙偏差小于 10μm,懸絲中心相對(duì)于底座底面位置精度優(yōu)于 20μm,裝配質(zhì)量滿足精度要求。該精密自動(dòng)裝配及焊接系統(tǒng)提高了產(chǎn)品精度一致性,為精密微小器件的自動(dòng)化裝配提供了借鑒。未來(lái),隨著技術(shù)的不斷進(jìn)步,激光錫球全自動(dòng)焊錫機(jī)在精密加速度計(jì)組件以及其他微小型精密器件的裝配中將發(fā)揮更加重要的作用,推動(dòng)航空航天等領(lǐng)域的制造技術(shù)向更高水平發(fā)展。
本文由大研智造撰寫(xiě),我們專(zhuān)注于提供智能制造精密焊接領(lǐng)域的最新技術(shù)資訊和深度分析。作為集研發(fā)、生產(chǎn)、銷(xiāo)售、服務(wù)為一體的激光焊錫機(jī)技術(shù)廠家,我們擁有超過(guò)20年的行業(yè)經(jīng)驗(yàn)。想要了解更多關(guān)于激光焊錫機(jī)在智能制造精密焊接領(lǐng)域中的應(yīng)用,或是有特定的技術(shù)需求,請(qǐng)?jiān)诖笱兄窃旃倬W(wǎng)聯(lián)系我們。歡迎來(lái)我司參觀、試機(jī)、免費(fèi)打樣。
審核編輯 黃宇
-
加速度計(jì)
+關(guān)注
關(guān)注
6文章
698瀏覽量
45858
發(fā)布評(píng)論請(qǐng)先 登錄
相關(guān)推薦
大研智造 探秘激光錫球全自動(dòng)焊錫機(jī)在耳機(jī)端子制造中的應(yīng)用方案

MEMS加速度計(jì)的工作原理是什么
PCB Piezotronics推出357A67型三軸電荷輸出加速度計(jì)
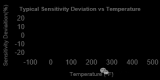
大研智造激光自動(dòng)錫球焊錫機(jī)——電子制造領(lǐng)域的卓越之選
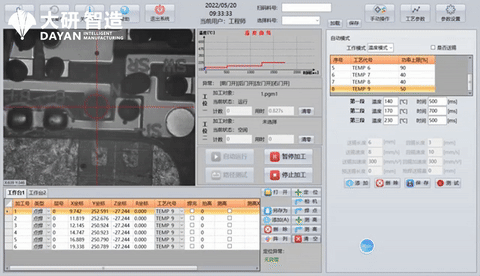
具有TLV2772的3V加速度計(jì)
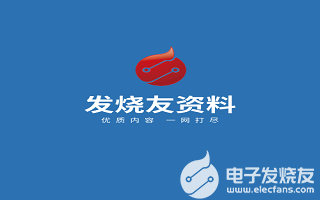
EPSON工業(yè)級(jí)加速度計(jì)選型
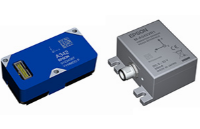
三軸加速度計(jì)LIS2DUX12開(kāi)發(fā)(2)----靜態(tài)校準(zhǔn)
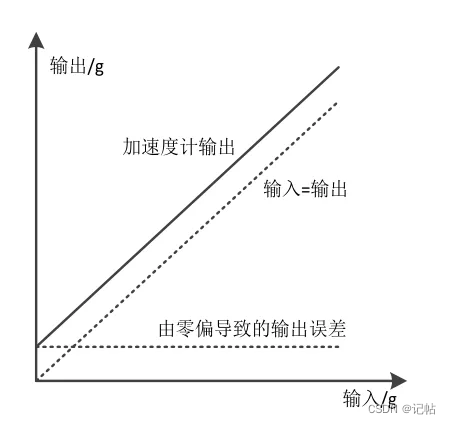
采用可調(diào)電熱微梁的近零剛度MEMS加速度計(jì)
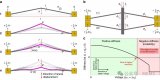
ADXL1001加速度計(jì)沒(méi)有輸出的原因?
兩軸加速度計(jì)和三軸加速度計(jì)的使用區(qū)別?
mems加速度計(jì)的量程是指什么
采用創(chuàng)新制造方案的聚合物壓電MEMS加速度計(jì)
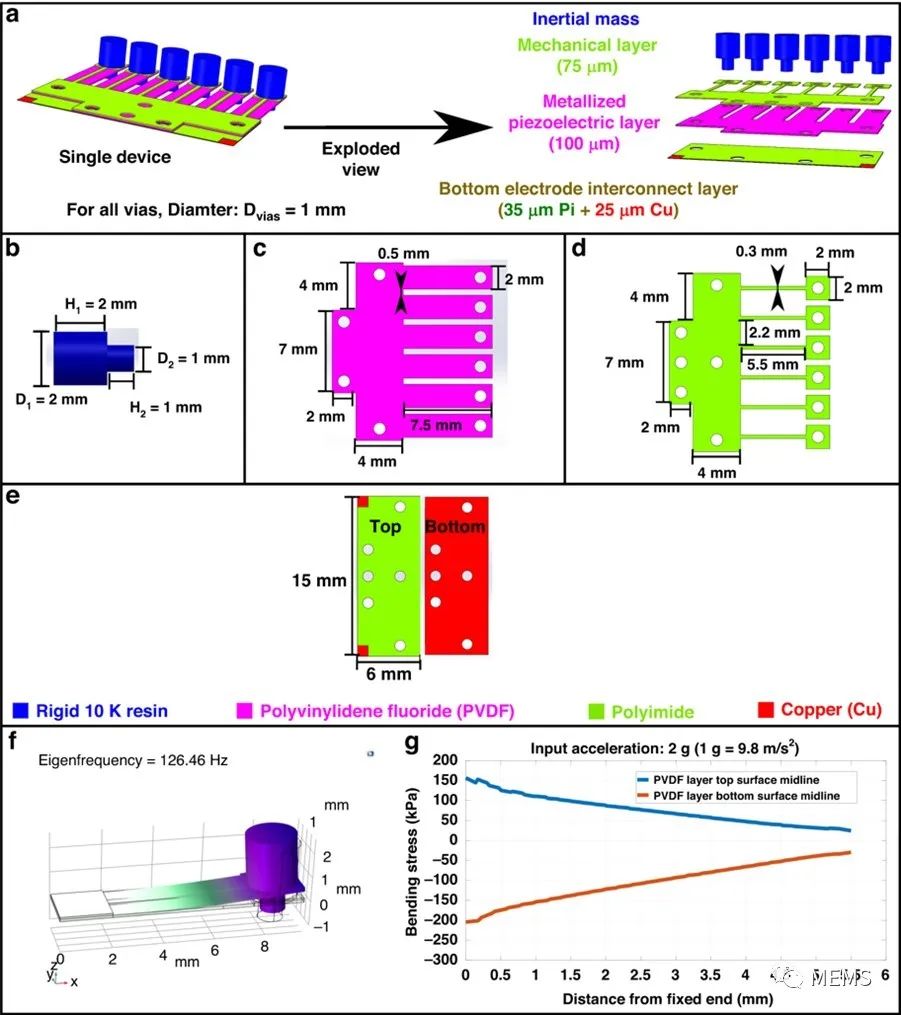
MEMS加速度計(jì)基本振動(dòng)特性
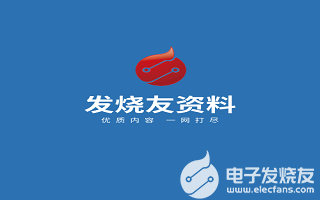
加速度計(jì)和其他感器主導(dǎo)的應(yīng)用領(lǐng)域
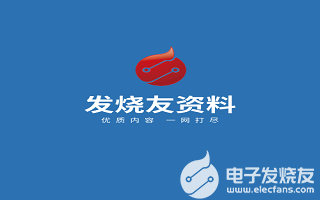
評(píng)論