A3車型是奇瑞公司的戰略轉型車型,為打造五星安全品質,對該車型提出更加苛刻的質量要求。焊裝車身的制造水平提高依賴于先進的焊接設備,公司引進柯馬公司的生產線,完成車身下部和車身總成的焊接任務,以符合更高的焊接質量要求。
第一部分A3自動化生產線設計綱領
主要負責A3三廂和A3兩廂兩種車型白車身總成的生產,下部線和主焊線是混線自動化生產線,年產能約為20萬輛。
車身下部線完成發動機倉、前地板、后地板等總成零件的拼裝焊接工作,適應車身下部高強度的焊接要求。主要由27臺機器人完成焊接工作、零件抓取,整條線還包括自動化輸送懸鏈,零件緩存器。
主焊線主要是完成車身下部、側圍、頂蓋、包裹架等總成的拼裝焊接工作。由滾床、OPENGATE、和31臺機器人組成。
主焊線OP130工位為在線激光檢測系統,由4臺機器人帶動激光檢測系統,對車身尺寸關鍵點進行在線檢測。
第二部分 電氣控制系統
A3自動化生產線共有兩個部分組成,分為車身下部線和主焊線,有5條空中輸送線,工藝流程為發動機倉、前地板、后地板分別由3條輸送線輸送至車身下部線,車身下部經空中輸送至主焊線,然后通過空中輸送線輸送至調整線。
整條生產線有車型識別系統一套,輥床一套、涂膠設備8套、COMAU機器人62臺,采用SICK的安全保護設備,采用帶有安全集成功能的CPU 416F-2的西門子。控制部分的采用工業以太網和PROFIBUS(現場總線)連接,見圖控制部分示意圖。
現場總線PROFIBUS,是用了7層模型的1、2層,精簡的結構保證了數據的高速傳輸。主要應用于現場分散的I/O設備。PROFIBUS-DP網絡由以下幾部分組成(如圖2):1主控器(PLC);2現場I/O模塊(ET200S),用于連接各種I/O設備;3其他智能裝置,如變頻器,觸摸屏等;4.網絡附件(交換機等)。它能夠直接完成設備的順序、連鎖、閉環控制,完成過程參數的采集以及報警功能。
PLC下面的從站模塊通過兩條PROFIBUS支路進行硬件配置分別有1.MPI網絡的網絡模塊配置2.DP網絡的模塊配置。PLC與PLC之間的通訊通過DP/DP COUPLER完成。PLC與PLC之間的通訊通過DP/DP COUPLER完成
兩條自動化生產線和5條空中輸送線由CPU 416-2DP、CPU 315-2DP的13臺西門子PLC控制。PLC可向系統提供分析設備運行狀態和發生故障點的信息。每條生產采用1臺西門子人機界面PC870進行控制,通過自身的MPI接口與PLC連接,內部安裝西門子組態監控軟件WINCC。整條生產線采用兩種總線模式,PLC與機器人間及PLC與I/O設備之間采用PROFIBUS現場總線進行通訊。PLC與PLC間的通訊全部采用西門子生產的CP443—1交換機進行通訊和數據交換。
機器人和人機界面采用PROFIBUS通訊協議,開關、電磁閥、按鈕、指示燈、I/O從站等全部采用現場總線,區域內PLC間的通訊通過DP/DP Coupler進行信號交換,區域間的PLC通過工業以太網進行通訊。這種總線的組合方式,節約了大量的接線工作,同時實現對整個系統的控制,過程狀態顯示、故障報警信息的顯示,使得整個系統操作簡便、維護方便、可靠性高。
西門子的人機界面HMI為整條生產線的運行與維修提供了強大的保證。在機器人界面上通過組態軟件進行動態調試、人機界面按操作菜單分為工位平面布置圖見圖2、各設備狀態圖見圖3等。人機界面能夠顯示線內的設備分布狀態、并用不同的顏色顯示設備的不同狀態、如運行、停止、故障等信息。子菜單內可顯示PLC與I/O的狀態圖3,顯示變頻器()、機器人的故障信息見圖4。當有故障時能自動彈出報警信息,并對報警信息進行記錄進行歸檔統計,保留歷史故障記錄ZAOCHE168.com,為日后維修與點檢設備時提供參考依據。
所有的操作界面使用西門子公司的HMI,避免了傳統的面板接線復雜、勞動強度大、觀察、維修不方便的弊病。在該生產線中成功地應用了西門子公司的SIMATIC產品的技術,其中Profibus場總線和工業以太網技術在該系統中起到關鍵作用。
第三部分 點焊機器人系統
在汽車焊接工藝中,點焊占整車焊焊接的很大一部分,奇瑞A3自動化生產線焊接系統主要由點焊機器人系統系統組成。點焊機器人系統包括機器人本體、機器人控制器、點焊控制器、自動電極修磨機、自動工具交換裝置、氣動點焊鉗、水氣供應的水氣控制盤等。
A3點焊機器人系統全部采用COMAU工業機器人及相關設備。這些點焊機器人通過控制系統可以進行A3兩廂車型和三箱車型的自動識別和切換。
焊接機器人是典型的機電一體化高科技產品,功能強大、操作簡便。點焊機器人系統的控制方式是:由機器人控制柜通過通信網絡同生產線PLC西門子控制柜構成機器人焊接生產系統。機器人系統內的點焊控制器、自動電極修磨機、自動工具交換裝置、水氣控制盤等裝置由機器人控制。機器人系統根據上位PLC的車型信號輸入來調用對應的機器人焊接程序進行車身裝配焊接。
3.1中頻焊接技術的應用
為了使A3獲得更加優異的碰撞性能,在A3的車身結構中,大量的采用高強度鋼板,同時縱梁等關鍵結構采用激光拼焊鋼板,傳統的工頻焊接技術無法使得在焊接高強度鋼板時獲得最好的剪切強度和抗疲勞強度。為了克服工頻焊接技術的弊病,在車身下部線采用中頻焊接。在A3線中采用BOSCH中頻焊接控制器和NIMAK的中頻焊鉗。
中頻焊接技術使得機器人焊接的優異性能進一步提升,中頻焊接得優點主要有,相對工頻焊接為直流焊接,變壓器小型化、提高電流控制的響應速度,實現工頻控制無法實現的焊接工藝,能夠對三相電網平衡,中頻焊接的功率因數高,節能效果好。
3.2涂膠系統的應用
涂膠系統主要涂車身骨架的點焊密封膠和隔震膠。自動膠槍由機器人攜帶,具有涂膠軌跡一致性高、膠用量控制準確、涂抹后的膠條形狀統一等優點。涂膠系統為A3車型獲得更加優異的降噪性能提供了很大幫助。
供膠系統采用GRACO 公司高粘度供應系統。包括:55加侖壓盤一個和5加侖壓盤一個、氣動柱塞泵、升降器。流體由泵輸出,泵出口裝有雙過濾裝置對膠進行過濾。再經過高壓軟管連接到GRACO P-FLO LT。
供料泵采用雙泵自動切換方式,設備具有自動切換及空桶報警功能:一泵處于工作狀態,一泵處于待命狀態。當工作泵膠桶中的膠用完后,系統發出報警,自動切換裝置自動將工作泵切換至另一待命的泵,此時待命的泵成為工作泵。供膠泵具有雙泵切換功能,在換桶時不影響自動涂膠系統的正常工作,有效的提高了生產線的工作效率。
流量控制采用美國GRACO P-FLO LT精密流量控制器,包括:控制箱,電纜,流體盤,氣動隔膜調壓,流量計等。
GRACO P-FLO LT流量控制的工作原理為機器人提供速度的模擬量信號,控制板控制氣動隔膜調壓即時調整膠的壓力,并通過流量計和壓力計提供實時精確流量和壓力即時修正,形成一個閉環控制,從而實現精確定量控制要求。槍的出膠量隨機器人速度的變化而變化。
3.3自動電極修磨機的應用
在主焊線上,為了實現生產裝配的自動化,提高生產線節拍,分別為每一臺點焊機器人配備了自動電極修磨機,實現電極頭工作面氧化磨損后的修銼過程自動完成。同時也避免了人員頻繁進入生產線帶來的安全隱患。電極修磨機由機器人的內置PLC控制,示教專門的電極修銼程序來完成電極修銼。同時根據修銼量的多少來對焊鉗的工作行程進行補償。
使用焊接機器人的優點:不僅使生產效率提高了,而且使焊接生產過程變得規范化,使產品質量得到穩定和提高。
第四部分 其他系統
4.1滾床系統
A3自動化生產線整條線使用滑撬輸送,輸送時間為18秒。其輸送路線為:升降段輸送空滑撬到UB10#——滾床輸送——UB110#——升降段輸送——MB10#——滾床輸送——MB150#——升降段輸送。下圖為西部線滾床滑撬系統。
滾床系統結構如圖2所示,其工作原理為:控制信號發出,傳輸電機接收信號,開始工作,滑撬通過摩擦滾輪進入工位,感應器感應,輸送電機停止,升降電機接收到控制信號,開始啟動,升降擺臂單元驅動,滾床開始升降,下降定位后,焊接機器人進行焊接,焊接完成后,控制信號發出,升降電機運行,滾床上升輸送電機運轉,滾床上升到位,運輸電機氣動,滑撬運行并進入下一工位。
M11/2主焊線設計生產節拍為100秒,可進行M11、M12兩車型的任意混流,并考慮第三車型的預留。其中MB30# & MB40# & MB50# 主拼工位占用了三個工位,形式為COMAU公司標準的OPENGATE,具有柔性高,階段投資,改造方便等諸多優點。其自身的結構特點較四面體翻轉也有可采用側圍預裝、兩側施焊空間大等優點。
OPENGATE即主拼夾具,COMAU公司OPENGAT是以夾具體為基礎,采用門形式,結合傳感器SOOQ.cn版權所有,利用PLC進行控制。OPENGATE和焊接機器人系統通過總控制系統進行配合工作,最終實現車身的定位、夾緊和焊接。
OPENGATE由夾具本體,氣路系統,感應控制系統組成。A3主線OPENGATE本體,采用門形式,底座采用直線導軌,通過推力電機進行定向(Y向)移動。X向預裝直線導軌,可以進行車型切換,這樣有利于進行階段性投資和改進。氣路系統采用集中供氣,由執行元件(氣缸)、控制元件(氣閥)和輔助元件組成。感應控制系統由電磁傳感器、PLC(可編程控制器)和計算機控制系統組成,可以實現夾具的信息采集和自動化控制。
OPENGATE工作過程。主線白車身預拼后進入OPENGATE,OPENGATE本體進行閉合,閉合過程中進行側圍和底盤的定位,使白車身預拼位置符合設計要求;定位后電磁感應系統進行工作,檢查定位是否準確,如果無誤,夾緊機構進行動作,將車身夾緊;如果有誤,報警系統進行報警, OPENGATE進入暫停狀態,同時控制系統顯示出現問題的地方和原因,待問題解決后系統繼續進行工作。夾緊后感應裝置進行夾緊狀態檢查,如果出現問題,則系統暫停并報警,如果夾緊狀態正常,焊接機器人開始工作,進行焊接,焊接完成后,OPENGATE夾緊機構打開,門式夾具體打開,白車身進入下一道工序,OPENGATE等待下一輛白車身進入。
OPENGATE的特點。COMAU公司OPENGATE側圍合拼采用預裝形式進行預裝配,側圍合拼焊接工位,采用側滑形式進行側圍的夾具切換,M11和M12側圍部分的夾具采用共用設計。夾具中定位銷、基座、非加工件采用標準化和系列化的部件,水平面上定位孔與定位孔之間的公差為±0.02mm,粗糙度為1.6um,所有的定位孔與基準面的公差為±0.05mm,粗糙度為1.6um。夾具定位銷和定位塊的安裝需采用“調整墊片式”的結構,定位銷調整墊片厚度為5mm。此外,設計中預留三坐標測量的位置和加工面,在復測時不需要拆卸夾具和滾床等其他設備。
目前A3車型已經基本實現公司的“2mm工程”,COMAU公司OPENGATE為“2mm”工程提供了很大的保障,它為奇瑞A3的五星品質奠定了堅實的基礎。
4.3機械化輸送懸鏈與BUFFER
機械化輸送懸鏈的主要是用于大總成零件的自動輸送,主要是發動機倉、前地板總成、后地板總成的輸送。
其中后地板的吊具是兩種車型共用。采用先進先出的方式進行零件的排序。如果零件與機器人抓取的過程不一樣可以進行零件的放行,當零件被機器人抓取后,空吊具沿返回道返回。同時要求具有強制返回功能,當發現問題時,零件不被抓取強行返回。
機械化懸鏈零件的放置和取下都是由機器人完成。
BUFFER主要是用于小零件的緩存。人工將零件擺放到BUFFER上,零件在BUFFER上是被可靠定位的。機器人在抓取零件時對零件的裝配的位置進行識別,如零件的裝配位置不正確機器人不進行零件的抓取,并報警。人工裝配完成后按確認進行放行。裝配員工需要根據生產計劃進行零件的排序。每個BUFFER上裝有顯示屏,對零件的數量進行倒計數。裝配者根據生產計劃進行零件的裝配。對一些情況,如將鍍鋅件裝配成非鍍鋅板機器人是無法識別的。
4.4車型識別和生產管理系統
自動化生產線將自動化控制系統,制造業執行系統(Manufacture Execute System,MES)集成在一起形成生產線的管理系統。在前期,生產計劃輸入工控機計算機中,通過工控軟件推算出個人工上件點的上件點的生產計劃。通過以太網傳給PLC。后期對系統進行改造,自動化線能夠及直接接受MES系統的生產計劃。
M11和M12采用拉動式生產的方式進行,生產線接收MES系統的生產計劃。每個工位都有基于MOBY-Ⅰ形式的車型識別系統,車型識別系統載體安裝在每個滑橇上。每個工位將根據車型識別系統識別的信息自動進行焊接程序和焊接參數的切換。
在發動機艙總成工位是計劃安排的起點。在總成工位粘貼條形碼,確定車型信息。發倉被放置在轉運平臺上時,掃描設備掃描VIN碼信息傳送給PLC控制柜。控制柜根據接收的生產計劃確定機器人是否進行零件抓取,信息無誤時給機器人傳送信號,機器人執行零件抓取。同時,將VIN碼信息傳遞給下一個工位。
主焊線第一個機器人設置VIN碼掃描點,并將信息寫到雪橇載體上,并將生產信息傳送給下個工位,第二個工位根據信息提前判斷功能,提前做好夾具、焊接參數、焊接程序的切換準備工作。當雪橇到達第二個工位時,設備讀取雪橇上的車型信息,并將從雪橇上讀取的信息同第一個工位傳遞的信息進行核對,核對正確的情況下,執行程序。以此類推。
整條生產線有9臺抓件機器人,上件機器人具有兩種車型的識別能力,能根據生產計劃選擇相應車型的零件,一旦零件錯誤或缺少零件,該機器人停止工作并且報警,同時每個BUFFER上具備車型識別系統。
4.5在線激光檢測系統
主線130為機器人激光檢測工位,由四臺機器人攜帶激光檢測傳感器組成,用來保證汽車精度而設立的,對M11.M12車身的252測量特性進行檢測。
Perceptron測量系統通過機器人上的激光傳感器采集車身實際尺寸,系統通過中轉器把數據傳輸到數據控制站進行分析和標準數據進行對照比較,尺寸出現超出工藝范圍,數據站立即發給PLC控制的生產線故障和報警信號,停止生產線,防止不合格車身流到下道工序。
4.6安全系統
硬件配置:CPU 416F-2的西門子PLC, 光柵、急停按鈕、安全門、區域掃描儀等。
安全集成的輸入輸出信號作為過程的接口,可以直接連接單通道和雙通道的輸入輸出信號,例如急停按鈕和光柵。安全集成信號作為冗余信號內部連接在一起。采用故障安全的分布式輸入輸出系統使系統的安全工程配置被PROFIBUS-DP部件替代,包括急停開關設備的替換,保護門監視裝置,雙手操作等等。
在程序塊中對工位的各種安全設備如急停、安全門、光柵進行邏輯控制,替代了傳統的安全繼電器控制方式;在程序中對各安全設備的邏輯處理主要通過三個程序模塊實現:光柵屏蔽數據功能模塊,急停屏蔽數據功能塊、安全門屏蔽數據功能塊。
集成在標準自動化系統的安全集成工程的優點主要有:
1.具有安全集成功能的自動化系統比機械電器解決方案更靈活
2.基于可編程控制器的安全系統相對與傳統的硬接線系統大大降低了接線成本
3.集成功能由于采用標準工程工具進行系統的編程配置因而可以減少工程用時
4.成故障安全功能的CPU不僅可以處理與安全相關的控制,同時可以參與到標準的自動化任務當中
5.故障安全程序和標準程序可以在統一的平臺上共享數據和通訊
小結
A3自動化線是COMAU為奇瑞公司打造的一條現代化生產線。為實現自動化生產,提供各種自動化設備,并進行有機集成,使用現場總線于PLC進行連接,PLC與PLC之間通過工業以太網進行連接,為生產線的使用、維護提供諸多方便。同時人機界面大大的提高了生產線的可控性,為維修提供了便利條件。
COMAU公司的OPENGATE技術為實現車身的“2mm工程”奠定了基礎,恰到好處的使用中頻焊接技術為提升車身性能起到關鍵點作用,各種輔助自動化設備極大地提高整條線的自動化率。
作為奇瑞“十年磨一礪”的主打、戰略車型A3,經歷過開創性的“十萬公里連續不間斷公開測試”、“突破性的通過C-NCAP五星安全測試”,連續被評為“自主品牌汽車”。這些良好的綜合性能,尤其是安全性,與奇瑞打造精品車身是分不開的。A3的優秀品質,是對設計、規劃、工藝、制造等投入大量人力、物力和先進技術換來的。COMAU公司設計制造的自動化線為A3車身卓越的品質的提升起到關鍵的作用。A3自動化線是自主品牌汽車向國際標準看齊的產物,A3車型品質的飛躍得益于自動化線的應用,使得車身焊接裝備的探索又邁向更高一層。
-
機器人
+關注
關注
210文章
27839瀏覽量
204599 -
plc
+關注
關注
5001文章
12946瀏覽量
459233
原文標題:機器人焊接生產線在奇瑞A3車型中的應用
文章出處:【微信號:jiqirenyingyong,微信公眾號:jiqirenyingyong】歡迎添加關注!文章轉載請注明出處。
發布評論請先 登錄
相關推薦
華南機器人應用培訓中心工業機器人培訓班招生
焊接傳感器一款轉為焊接機器人而設計的焊縫跟蹤傳感器
點焊機器人工作原理_點焊機器人的應用
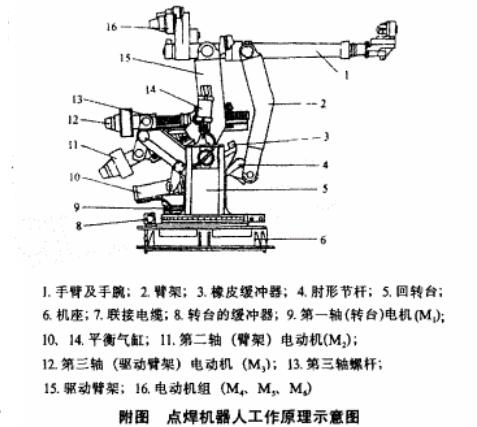
點焊機器人的組成及應用
點焊機器人的工作原理以及應用
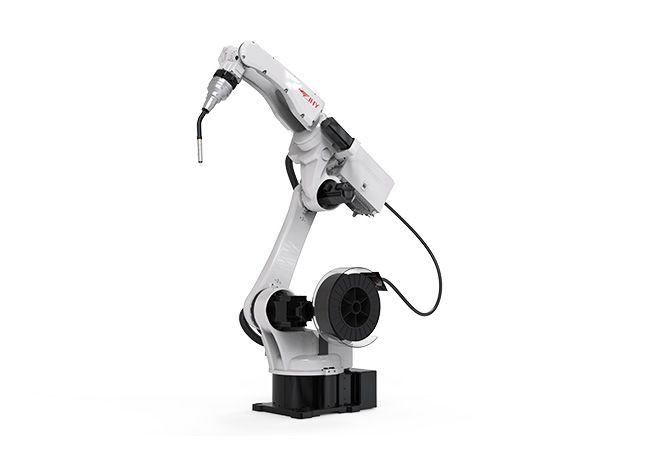
評論