從2009年開始算起,中國研究團隊一路攻堅克難,國產首套90納米高端光刻機已于近期第一次成功曝光。2022年左右有望完成驗收。這意味著,中國半導體材料和設備(工藝技術)產業又向前跨出了關鍵一大步。光刻機被全球業界人士們稱為“工業皇冠明珠”。而事實上,中國科研和工程人員們也都有志在未來,從“工業皇冠”上拿到這顆“明珠”。
國產光刻機達到幾納米
光電所微細加工光學技術國家重點實驗室研制出來的SP光刻機是世界上第一臺單次成像達到22納米的光刻機,結合多重曝光技術,可以用于制備10納米以下的信息器件。這不僅是世界上光學光刻的一次重大變革,也將加快推進工業4.0,實現中國制造2025的美好愿景。
中國生產光刻機的廠家
2、中子科技集團公司第四十五研究所國電
3、合肥芯碩半導體有限公司
4、先騰光電科技有限公司
5、無錫影速半導體科技有限公司
中國光刻機的發展史
2009 年9 月下旬,上海微電子裝備有限公司研發的先進封裝光刻機通過了江陰長電先進封裝有限公司的出廠工藝測試,并正式簽訂了產品銷售合同。該光刻機具有“大視場、大焦深、高套刻精度、邊緣曝光”等技術特點,可滿足先進封裝I藝中8 英寸及12 英寸硅片級重新布線凸點等厚膠工藝要求。自2009年11月上生產線運行以來,江陰長電利用該設備已成功完成第一批8英寸“重新布線及凸點工藝”產品的多層光刻生產任務。
國產首臺先進封裝光刻機的研制成功與使用,標志著我國在高端封裝關鍵設備產品創新與開發中取得了可喜突破,對提升我國集成電路制造裝備、工藝及材料技術的自主創新能力具有重要意義。
2010年7月16日下午,上海微電子裝備有限公司(簡稱“SMEE”) 和江陰長電先進封裝有限公司(簡稱“JCAP”) 在江蘇省江陰市聯合召開了“首臺先進封裝光刻機使用現場匯報會暨SMEE 與JCAP戰略合作協議的簽約儀式”會議。科技部、國家科技重大專項“極大規模集成電路制造裝備及成套工藝”實施管理辦公室和
總體專家組、專項咨詢委、上海市科委、江陰市府等單位的領導出席丁會議,科技部曹健林副部長等領導做了重要講話。
隨著集成電路產業的發展,高端芯片的集成度已經達到數千至數億晶體管,推動著芯片封裝技術向更高密度、更高性能發展,使基于凸點工藝的封裝成為主流技術,對封裝光刻機的性能也大幅提高,傳統的接近/接觸式光刻機已不能滿足高性能、高密度、低成本等先進封裝工藝發展需求,先進的大視場、大焦深、高精度投影光刻機成為先進封裝生產線的關鍵設備。為了改變該類先進封裝光刻機完全依賴進口局面,上海微電子裝備有限公司在國家科技重大專項和上海市科委等部門的支持下,成功開發出了用于倒裝焊凸點制備的先進封裝光刻機。該機型具有自主知識產權,在投影物鏡、高精密的工件臺、對準調焦測量、軟件系統等關鍵技術上取得了系列創新成果,申請了國家發明專利74項,已獲國家發明專利授權22項,申請國際發明專利3項。
2009年9月下旬,上海微電子裝備有限公司研發的先進封裝光刻機通過了江陰長電先進封裝有限公司的出廠工藝測試,并正式簽訂了產品銷售合同。該光刻機具有“大視場、大焦深、高套刻精度、邊緣曝光”等技術特點,可滿足先進封裝工藝中8英寸及12 英寸硅片級重新布線凸點等厚膠工藝要求。自2009年11月上生產線運行以來,江陰長電利用該設備已成功完成第一批8 英寸“重新布線及凸點工藝”產品的多層光刻生產任務。
國產首臺先進封裝光刻機的研制成功與使用,標志著我國在高端封裝關鍵設備產品創新與開發中取得了可喜突破,對提升我國集成電路制造裝備、工藝及材料技術的自主創新能力具有重要意義。
延伸閱讀:光刻機的發展史
光刻機的最小分辨率、生產效率、良率均在不斷發展。 光刻機的最小分辨率由公示 R=kλ/NA,其中 R 代表可分辨的最小尺寸,對于光刻技術來說, R 越小越好; k 是工藝常數; λ 是光刻機所用光源的波長; NA 代表物鏡數值孔徑,與光傳播介質的折射率相關,折射率越大, NA 越大。光刻機制程工藝水平的發展均遵循以上公式。此外,光刻機的內部構造和工作模式也在發展,不斷提升芯片的生產效率和良率。
根據所使用的光源的改進,光刻機經歷了 5 代產品的發展,每次光源的改進都顯著提升了光刻機所能實現的最小工藝節點。此外雙工作臺、沉浸式光刻等新型光刻技術的創新與發展也在不斷提升光刻機的工藝制程水平,以及生產的效率和良率。
按所用光源,光刻機經歷了五代產品的發展
最初的兩代光刻機采用汞燈產生的 436nm g-line 和 365nm i-line 作為光刻光源,可以滿足0.8-0.35 微米制程芯片的生產。最早的光刻機采用接觸式光刻,即掩模貼在硅片上進行光刻,容易產生污染,且掩模壽命較短。此后的接近式光刻機對接觸式光刻機進行了改良, 通過氣墊在掩模和硅片間產生細小空隙,掩模與硅片不再直接接觸,但受氣墊影響,成像的精度不高。
第三代光刻機采用 248nm 的 KrF(氟化氪)準分子激光作為光源,將最小工藝節點提升至350-180nm 水平,在光刻工藝上也采用了掃描投影式光刻,即現在光刻機通用的,光源通過掩模, 經光學鏡頭調整和補償后, 以掃描的方式在硅片上實現曝光。
第四代 ArF 光刻機:最具代表性的光刻機產品。第四代光刻機的光源采用了 193nm 的 ArF(氟化氬)準分子激光,將最小制程一舉提升至 65nm 的水平。第四代光刻機是目前使用最廣的光刻機,也是最具有代表性的一代光刻機。由于能夠取代 ArF 實現更低制程的光刻機遲遲無法研發成功,光刻機生產商在 ArF 光刻機上進行了大量的工藝創新,來滿足更小制程和更高效率的生產需要。
創新一:實現步進式掃描投影。 此前的掃描投影式光刻機在光刻時硅片處于靜止狀態,通過掩模的移動實現硅片不同區域的曝光。 1986 年 ASML 首先推出步進式掃描投影光刻機,實現了光刻過程中,掩模和硅片的同步移動, 并且采用了縮小投影鏡頭,縮小比例達到 5: 1, 有效提升了掩模的使用效率和曝光精度,將芯片的制程和生產效率提升了一個臺階。
創新二:雙工作臺光刻機。硅片在進入光刻流程前要先進行測量和對準,過去光刻機只有一個工作臺,測量、對準、光刻等所有流程都在這一個工作臺上完成。 2001 年 ASML 推出了雙工作臺系統(TWINSCAN system),雙工作臺系統使得光刻機能夠在不改變初始速度和加速度的條件下,當一個工作臺在進行曝光工作的同時,另外一個工作臺可以同時進行曝光之前的預對準工作,使得光刻機的生產效率提升大約 35%。
雖然從結果上來看,僅僅是增加了一個工作臺,但其中的技術難度卻不容小覷,雙工作臺系統對于換臺的速度和精度有極高的要求, 如果換臺速度慢,則影響光刻機工作效率;如果換臺精度不夠, 則可能影響后續掃描光刻等步驟的正常開展。
雙工作臺光刻機系統樣機
創新三: 浸沒式光刻系統。到了 45nm 制程節點時, ArF 光刻機也遇到了分辨率不足的問題,此時業內對下一代光刻機的發展提出了兩種路線圖。一是開發波長更低的 157nmF2準分子激光做為光源, 二是由 2002 年臺積電林本堅提出的浸沒式光刻。此前的光刻機都是干式機臺,曝光顯影都是在無塵室中,以空氣為媒介進行。由于最小分辨率公式中的 NA 與折射率成正相關,如果用折射率大于 1 的水做為媒介進行光刻,最小分辨率將得到提升,這就是浸沒式光刻系統的原理。
ASML 率先推出浸沒式光刻機,奠定自身市場地位。林本堅提出浸沒式光刻設想后, ASML開始與臺積電合作開發浸沒式光刻機,并在 2007年成功推出第一臺浸沒式光刻機TWINSCANXT:1900i,該設備采用折射率達到 1.44 的去離子水做為媒介,實現了 45nm 的制程工藝,并一舉壟斷市場。當時的另兩大光刻巨頭尼康、佳能主推的157nm 光源干式光刻機被市場拋棄,不僅損失了巨大的人力物力,也在產品線上顯著落后于 ASML,這也是尼康、佳能由盛轉衰,ASML 一家獨大的重要轉折點。
浸沒式光刻機原理
通過浸沒式光刻和雙重光刻等工藝,第四代 ArF 光刻機最高可以實現 22nm 制程的芯片生產,但是在摩爾定律的推動下,半導體產業對于芯片制程的需求已經發展到 14nm、 10nm、甚至7nm, ArF 光刻機已無法滿足這一需求,半導體產業將希望寄予第五代 EUV 光刻機。
第五代 EUV 光刻機,千呼萬喚始出來。 1-4 代光刻機使用的光源都屬于深紫外光, 第五代 EUV光刻機使用的則是波長 13.5nm 的極紫外光。
早在上世紀九十年代,極紫外光刻機的概念就已經被提出, ASML 也從 1999 年開始 EUV 光刻機的研發工作,原計劃在 2004 年推出產品。但直到 2010 年 ASML 才研發出第一臺 EUV 原型機, 2016 年才實現下游客戶的供貨,比預計時間晚了十幾年。三星、臺積電、英特爾共同入股 ASML 推動 EUV 光刻機研發。
EUV 光刻機面市時間表的不斷延后主要有兩大方面的原因,一是所需的光源功率遲遲無法達到 250 瓦的工作功率需求,二是光學透鏡、反射鏡系統對于光學精度的要求極高,生產難度極大。這兩大原因使得 ASML及其合作伙伴難以支撐龐大的研發費用。 2012 年 ASML 黨的三大客戶三星、臺積電、英特爾共同向 ASML 投資 52.59 億歐元,用于支持 EUV 光刻機的研發。此后 ASML 收購了全球領先的準分子激光器供應商 Cymer,并以 10 億歐元現金入股光學系統供應商卡爾蔡司,加速EUV 光源和光學系統的研發進程,這兩次并購也是 EUV 光刻機能研發成功的重要原因。
光刻機相關文章:
-
光刻機
+關注
關注
31文章
1148瀏覽量
47273
發布評論請先 登錄
相關推薦
光刻機工藝的原理及設備
光刻機是干什么用的
魂遷光刻,夢繞芯片,中芯國際終獲ASML大型光刻機 精選資料分享
荷蘭光刻機為什么厲害_為何光刻機不賣給中國
光刻機中國能造嗎_為什么中國生產不了光刻機
中國光刻機和荷蘭光刻機有什么區別
EUV光刻機還能賣給中國嗎?
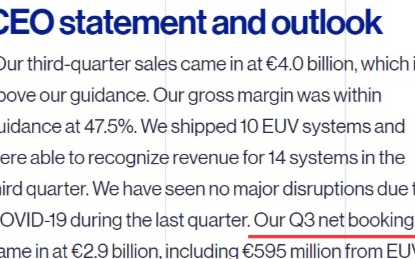
評論