張仁柏認為,作為一家專業的動力電池系統公司,普萊德也同動力電芯企業一樣,面臨既要高比能量,又要高安全的矛盾問題。
“我們連續五年獨立第三方Pack企業排名第一,去年整個出貨量大約是2.3GWh,今年預測4.7GWh。”
近日,北京普萊德新能源電池科技有限公司(下稱“普萊德”)副總裁張仁柏在“中國(青海)鋰產業與動力電池國際高峰論壇”上自信地表示,普萊德擁有300多項專利,其中發明專利136項,這成為公司產品市場競爭能力的保障。
目前,市場上搭載普萊德動力電池系統的車型數量達到3000輛車,已經運行了三年,體現了市場的接受度和技術可靠性。
▲普萊德副總裁張仁柏
張仁柏認為,作為一家專業的動力電池系統公司,普萊德首先就是要關注安全,但基于國家新能源汽車補貼退坡、雙積分等政策的頒布,普萊德也同動力電芯企業一樣,面臨既要高比能量,又要高安全的矛盾問題。如何平衡兩者,成為雙方的共性問題。
為此,他以專業的動力電池系統企業角度,從整個電池系統的失效模式、四大電池系統安全、熱管理系統設計、電池輕量化技術等多個方面進行了詳細闡述。
(一)電池系統失效模式
動力電池系統安全肯定最先分析整個電池系統的失效模式。我列了一下有五項,一是電擊,即電能非正常釋放,然后是燃燒、爆炸、碰撞、腐蝕。
因為每賣一輛車基本質保條件是八年12萬公里,在這種情況下腐蝕也會影響到車輛的可靠性。腐蝕也是關注安全的一個方面。
(二)四大電池系統安全
普萊德開發的創新點,電池系統安全測試至少有四大安全。第一個是化學安全,材料阻燃、電芯安全,包括一些標識。
第二個電氣安全是系統上設計的重要關注點,膨脹力、傳感、電壓采集、溫度采集,絕緣耐壓、電磁兼容,電磁評比、漏液檢測、冗余設計,交叉檢驗算法。
第三個機械安全。現在行業里面可以做到IP67,后續會做到IP68,這里面還有隔熱、耐腐蝕、耐振動。
第四個最重要的是功能安全。基于ISO26262,把電池系統放在汽車里面,功能安全指自動滅火、主動&被動安全、碰撞過程中斷開、高壓。剛才孚能的王總也介紹了整個電池系統里面的容斷等等設計,包括濕度、煙霧、短路、過充。
一個電池包的開發周期一般是24個月,其中光測試要求就要高于國標,或基本跟國際上持平,現在也增加了測試數量。
普萊德的產品安全采用全仿真的分析,有靜力、球擊、模態、振動,還有沖擊、擠壓、疲勞和碰撞。從電芯到模組級的仿真模型,這都是必備的設計。很多廠家找我們說三個月開發一個電池包,這確實很難,一般測試都是標準24個月的周期。
(三)安全與能量密度如何平衡
基于新能源汽車補貼退坡和雙積分的推動,大家看到我們做電池系統和做電芯一樣,也是一個矛盾體,既要高比能量,又要高安全,這要如何平衡呢?這是一個共性問題。
除了電芯溫度提高,Pack結構設計也是提升能量密度的重要方面,同時要保障整個動力電池系統安全,這是我們每天都要考慮的問題。
目前,能量密度目標,整個行業的平均成組效率在65%,普萊德項目目標是80%;安全性的目標,我們通過BMS的核心技術、系統控制策略優化、結構優化,還有一些系統設計,希望把電池系統保持零事故,這里面基本涉及七大方面:集成模組設計、系統輕量化、廣義BMS的設計、熱設計、梯次利用等。
熱管理系統設計方面,我們攜帶的主要產品都是采用液冷方式,因為能量密度提升對熱管理、保障安全很重要。
系統輕量化設計方面,從以前的鈑金到沖壓,現在全面轉接到高強度鋁和復合材料,我們在模組設計里面再加上一些固定邊框,同時加強了溫度傳感器和電壓測試系統,能夠保障能量密度達到一定的指標。
BMS方面,除了對產品的檢控以外,我們對SOC、SOP、SOH的管理也做了后臺大數據,保障每一輛車在運行過程中都有數據記錄,實現數據全面可追蹤,監督它的健康狀況并進行預測。
除從上述三方面著手外,普萊德進一步解釋了集成標準模組的設計、系統輕量化設計,并針對全生命周期的廣義BMS和熱設計做了一些工作。
這是我們的自動化工藝設計里面的部分,包括我們的光學檢測、激光連續焊、工裝模塊化的組裝、CMT機器人,還有一拖二雙工位焊接工藝,大大提升了制造的效率和可靠性。
其中,重點講BMS里面的大數據庫部分。整個工作原理是,通過電池系統運營、電池系統參數傳輸、模式算法,最后達到經由云平臺傳輸到數據庫里面進行結果的可視化和電池保養的提示。保證我們的產品出去以后除了BMS在車上的重視,也有后臺數據庫的實時跟蹤。
(四)電池輕量化
輕量化方面,普萊德從結構、材料和工藝里面做了一些具體工作。比如結構上,普萊德有一個Pack結構設計。
匯總一下整個對于安全、能量密度和可靠性做的一些工作。這是整個電池包的拓撲圖,里面包括模組、電子電氣、熱管理、電池連接件、輔助材料等等。
這是260km和350km兩個電池包的對比,我們是用實施鋁合金型材電池殼體技術方案分析,保證強度與可靠性基礎上,控制模具投資,實現重量和成本的降低,同時關注電池下殼體選材,對比重量范圍、模具投入、生產節拍和成本預估四方面進行分析。
從成本來講,以前講鋁材一般的成本是鋼材的三倍,重量是鋼材的1/3,但是現在通過技術提升,成本能夠控制在3000元左右,但是開發時間也嚴重縮短,從6個月縮短到1個月,重量從以前一個電池包60公斤降到40公斤。
這是整個的數據對比,材料強度、抗拉強度、斷裂伸長度等。這是結構差異和不同的可靠性的數據分析。
通過這種分析大家可以看到,擠壓鋁型電池的殼輕量化效果明顯,開發周期短,投資最小,并且生產效率高、成本低,所以現在從今年開始全面轉換成一個產品設計思路。
-
動力電池
+關注
關注
113文章
4514瀏覽量
77482 -
電芯
+關注
關注
14文章
718瀏覽量
25810
原文標題:【派勒智能?洞見】預計出貨量4.7GWh 張仁柏談普萊德安全與能量密度平衡
文章出處:【微信號:weixin-gg-lb,微信公眾號:高工鋰電】歡迎添加關注!文章轉載請注明出處。
發布評論請先 登錄
相關推薦
出貨量持續稱霸全球,聯發科天璣芯片強在哪?

江波龍自研SLC NAND Flash累計出貨突破1億顆
隆基綠能強化市場競爭力,引領光伏行業新發展
北京芯片獨角獸芯馳科技:出貨量破600萬片,加速駛向全球舞臺
強達電路:持續提升創新能力,增強市場競爭力
?強達電路:持續提升創新能力,增強市場競爭力
TCL電子上半年出貨量強勁增長,大尺寸及高端電視市場引領潮流
SK海力士與Amkor攜手推進硅中介層合作,強化HBM市場競爭力
英偉達去年數據中心GPU出貨量占比約98%
全球車載顯示面板出貨量預測:大陸地區面板廠領先
EMC測試整改:提升產品合規性和市場競爭力?|深圳比創達電子
2023年中國AR/VR市場業績概覽:AR出貨量攀新高,VR銷量下滑
GGII:2023年國內儲能鋰電池出貨量超200GWh
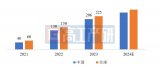
評論