用戶總是要求我們提高所設計的機械的性能,同時減少資金成本。為了達到這兩個矛盾的目標,我們將注意力放到在機械設計方面有巨大潛力的機電一體化上。本文著重展示了使用嵌入式分析工具的現代計算機輔助設計(CAD)系統如何實現機電一體化設計。
在機電一體化設計中,三個設計團隊(機械、電機與控制)并行工作。在機械團隊完成設計前,電機與控制團隊需要預先得到有關機械的信息。虛擬原型技術可以預先提供機械信息,通過將3D CAD系統與一個運動和結構分析工具,以及一個虛擬控制器相連接, SolidWorks公司與NI公司創建了一個真實的機電一體化設計環境。使用這些工具并不表示機械設計過程中的繁重工作減少了,而是工作量在整個設計周期中由設計團隊分擔了。
圖 1 初次共振實驗示意圖。虛擬原型技術的巨大價值在于,它允許出現并校正設計錯誤,而不會出現制造實物樣機所帶來的資金耗費與時間延遲。
圖 1 初次共振實驗示意圖
虛擬原型技術設計過程
經常失敗與早期失敗是虛擬原型技術設計的必經之路,失敗的方式體現在設計過程中而不是事后。其訣竅就是在正確的事情上失敗,確定什么是機械的關鍵性能指標(KPI’s),并將這些作為隨后測試的參數與目標。首先看看取放機并領會虛擬原型技術如何在設計過程引導我們。
圖2 取放機示意圖
運動輪廓是所有機械的基石。最簡單的情況是將物體A從 B處 移到 C處。但是在某些情況下,從B到C的最佳方式并不那么顯而易見。一步運動還是兩步?凸輪還是伺服?利用CAD可以快速地安排機械的運動部件,并檢查沖突與運動范圍。由于大多機械并不是從草圖開始的,最初的CAD組裝很可能是3D模型與布局草圖或是結構圖的混合體。
即使只有如此簡單的幾何形狀,SolidWorks仍可以基于草圖或用戶定義的部分計算出近似的力與轉矩,圖2為裝配馬達與驅動的取放布局圖。我們現在可以將這些要求告知電機工程師,他們會對馬達與驅動提出建議。再者,有可能借助于軟件的優勢直接從3D信息中心 (擁有超過一百萬個模型)或者制造商的網站下載馬達與驅動的CAD模型。
圖3 裝配馬達與驅動的取放布局
最初的設計迭代提供力的大小來確定“最初估計”的馬達和驅動尺寸。使用裝配圖中包含的馬達與驅動CAD模型,運動仿真能夠快速地重復運行來完善馬達與驅動需求。當機械設計成熟并且CAD裝配變得更加完整,運動分析軟件可以周期性地重復運行,確保實物樣機制造時不會出現意外。
當馬達尺寸確定后,我們可以將注意力轉移到機械的性能與其結構上。典型的機械KPI是其位置公差,就機械學的層次來說,是由機構剛度與驅動順性決定的。對取放機而言,需要一個與較輕的,但很硬的移動結構結合一個非常剛性的支持結構,、驅動以及連接系統,它們能夠充分滿足機械的需求。
使用SolidWorks集成的仿真套件,可以從運動分析中取出力與轉矩,并將其放入結構仿真中來*估機械強度、耐久性以及柔韌性。現在,機械工程師可以回答有關機械性能的基本問題了。在任何運行速度下機械是否會共振?機械是否超出設計標準?是否能減少機械的重量以及由此導致的花費?機械部件的使用壽命是多久?這不是只做一次的仿真,而是當機械開發時,不斷運行以發展與改進,不斷為機電一體化團隊提供最新、精確的信息,根據具體情況作出設計決定。
目前為止,我們只考慮了機械與電機工程師,而機電一體化設計模式是關于并行工作的三個工程團隊。那么虛擬原型技術如何幫助控制工程師?我們已經看到了虛擬機械如何在CAD系統下被驅動,但是控制工程師想要的是一個虛擬控制器,能夠直接與CAD幾何圖形對話并驅動運動分析(圖4),如同用于SolidWorks的LabVIEW NI SoftMotion所能實現的。
圖4 通過馬達尺寸以及其它部件的確定,虛擬控制器能夠直接與CAD圖形對話并驅動運動分析
現在,控制工程師可以驅動虛擬機械,微調控制代碼并實時觀察機械行為。控制工程師可以確保運動輪廓正確,調查有關機械性能順性的效果,并留意設計一些安全裝置,例如傳感器或者限位開關。對機械與電機工程師來說,因為虛擬機械是由“真實”代碼驅動, 新增的好處是,機械工程師可以確定“真實”的力與轉矩,而電機工程師可以估計“真實”的馬達與驅動需求。
-
CAD
+關注
關注
17文章
1081瀏覽量
72367 -
機電一體化
+關注
關注
1文章
96瀏覽量
23254 -
虛擬原型
+關注
關注
0文章
5瀏覽量
5117
發布評論請先 登錄
相關推薦
淺談新能源光儲充一體化電站設計方案

一體化機芯技術解析:鏡頭、傳感器與電路板的完美融合
《嵌入式機電一體化系統設計與實現》讀后感
安消一體化平臺建設方案
名單公布!【書籍評測活動NO.36】嵌入式機電一體化系統設計與實現
室內外一體化定位技術的普及和應用
什么是通感算一體化?通感算一體化的應用場景
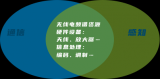
評論