引言
當今汽車行業,法規對安全性、動力性、舒適性、排放等提出了日益嚴格的要求,而這些性能又很大程度受ECU性能和質量的影響。因此在汽車中,ECU不僅數量持續上升,其功能也不斷增強。
在汽車中,分單個ECU系統和多個ECU互聯系統,前者如安全氣囊ECU,后者如發動機管理系統(EMS) ECU。EMS涉及數千個參數和多個電子設備,而且這些參數之間存在數據共享和傳遞,需要通過不同的汽車總線將各個電子設備互聯,以形成車載網絡,并完成復雜的智能控制和故障診斷。ECU復雜性和功能性不斷增加,為確保最終產品質量,需要通過自動化測試手段來減少從定義、分析、設計到實現不同產品周期環節的人為失誤。此外,還面臨如何在最短的開發周期內以最經濟的成本將產品推向市場的挑戰。
控制器開發“V”模式
經過多年探索,業界普遍采用基于計算機模型的控制器開發“V”模式,如圖1所示。該模式可以很大程度地減少反復過程、縮短開發周期,以節省成本。該模式除應用于汽車用ECU開發外,也已成功應用到航空、國防、“白色”家電、醫療設備、工業過程控制等領域。下面按照“V”模式圖橫向對應的先后環節順序作簡單闡述。
系統定義:根據控制系統設計要求,完成設計規范,如控制算法、控制對象參數等。往往需要以往的設計經驗、試驗數據作參考。
設計、仿真:根據控制系統定義,將整個系統在計算機軟件環境下實現,即對控制器的控制邏輯、控制對象環境進行建模仿真,以幫助設計者在先期就對系統指標、誤差等進行快速評估。仿真工具主要有NI LabVIEW、The MathWorks, Inc. Simulink?、MATRIXx等。其中LabVIEW允許設計者在圖形化環境中借助提供的控制仿真模塊對控制系統進行建模和動態仿真,又可集成第三方軟件開發的模型和代碼,包括The MathWorks, Inc. Simulink?、MSC CarSim,甚至C代碼。MATRXx則提供一整套系統設計仿真工具,尤其適合開發和管理大型的、復雜的模型。
圖1 控制器開發“V”模式圖
快速原型:在這里,快速控制原型(Rapid Control Prototype,簡稱快速原型)概念區別于機械制造中根據CAD數據自動構建物理模型的快速成型技術。因為軟件仿真不能完全體現實際的動態環境,需要開發一個控制器硬件原型用以在真實環境下驗證算法,即將控制器模型下載到一個實時硬件平臺,并通過I/O連接至真實環境中的傳感器、執行器并進行測試,該過程即快速原型,也常稱為軟件在環。選用實時硬件平臺是為了仿真的時效性、確定性和穩定性。
代碼生成與軟件測試:控制器模型在通過快速原型環節驗證之后,將該模型自動或手工生成C代碼或其它支持類型的代碼,并下載到ECU的微控制器。并對所產生的目標代碼進行測試。
硬件在環:硬件在環(Hardware in the Loop)是指將已下載目標代碼的ECU通過I/O連接至先前建立的環境模型(硬件在環仿真器),并測試該ECU在各種工況下的功能性和穩定性。硬件在環是一個閉環的測試系統,可重復地進行動態仿真;可在試驗室里仿真夏季和冬季的道路試驗,無需真實的測試環境組件,節約測試成本;可進行臨界條件測試和模擬極限工況,如發動機水溫和油溫、ABS試驗時車速和道路附著系數,沒有實際風險;并可通過軟件(模型)、硬件(故障輸入模塊)來模擬開路、與地短接、ECU引腳間短接等錯誤,以及模擬傳感器、執行器出錯情況。
系統標定和測試:在完成關鍵的硬件在環之后,將修正后的控制器連接至真實I/O環境,并進行臺架試驗、道路試驗,直至最后生產出廠。
以上控制器開發“V”模式符合國際汽車行業標準(ASAM/ASAP),已在諸多著名汽車電子廠家中獲得成功。快速原型和硬件在環是控制器開發的重要環節,目前針對這兩個環節的解決方案普遍面臨成本高的不足。NI根據控制系統的復雜度和I/O數目,為快速原型和硬件在環測試提供不同的、低成本的解決方案。比如對于面向控制算法相對簡單、I/O數目相對較少的車身電子控制的ECU,可選擇CompactRIO平臺進行ECU快速原型和硬件在環測試;針對較為復雜的動力總成系統和主動懸架系統,可選用PXI實時系統平臺。上述平臺均具有開發時間短、通用性、可擴展性、低成本的特點;并在國內外獲得了廣泛應用,如MicroNova,Wineman Technology,KGC,Averna,KPIT Cummins等成功地為整車廠提供了解決方案;在國內,如上海大眾某車型全車多個ECU硬件在環測試是在NI PXI平臺下實現的。
下面舉兩個例子來說明NI軟硬件平臺在控制器快速原型和硬件在環中的應用。
應用舉例一:Yamaha摩托車控制系統快速原型測試
美國Drivven公司承擔為Yamaha YZF-R6 摩托車開發發動機控制系統原型項目。項目要求:毫秒級的控制器模型循環時間;微妙級的噴油和點火正時;并考慮摩托車空間受限、設備供電等因素。
Drivven在經過市場調查之后,最終選擇NI CompactRIO嵌入式系統平臺。該平臺包括實時嵌入式控制器、內置FPGA芯片的機箱以及內置信號調理的模塊。整個系統具有小型、堅固、9-35V直流供電,適應復雜的測試環境和有限的測試空間。FPGA芯片是CompactRIO體系結構的核心,但設計者借助LabVIEW FPGA模塊,無須硬件描述語言和相關專業知識,便可在WINDOWS操作系統上用圖形化方法開發自定義的FPGA邏輯代碼并下載。該平臺又是一個開放的平臺,既可選用現成的針對不同信號類型的模塊,又可自己開發自定義模塊。Drivven根據項目需求,開發了模數混合模塊、燃料噴射模塊、氧傳感器模塊、可變磁阻和霍爾模塊等。
通過LabVIEW實時模塊編程實現高性能賽車常用的速度密度法和節氣門開度速度法組合控制策略。速度密度法是指利用發動機轉速和進氣密度來計算各缸進氣量,系統驅動噴油器提供所需的油量,以滿足各種節氣門狀態下的理論空燃比要求和在節氣門全開情況下的最大扭矩需求,應用于低轉速、低負荷工況。節氣門開度速度法是指根據兩者參數值在二維圖表上查找空氣質量經驗值。
將CompactRIO原型平臺布置在該摩托車上,進行試驗,系統和程序界面如圖2、圖3所示。試驗結果表明:發動機轉速可高達15500RPM;能很好地實現噴油、點火正時等策略。同時,實時控制器可記錄下試驗過程中包括進氣氣壓和溫度、大氣氣壓、冷卻水溫度、節氣門位置、噴油初始角、點火提前角等參數。Drivven公司總裁Carroll G. Dase表示:“和過去類似項目相比,利用CompactRIO平臺從過去兩人一年的工作量并耗費50萬美金下降到三人一個月的工作量且只需花費15000美金。”
圖2 發動機控制器硬件原型
圖3 發動機原型上位機測試界面
應用舉例二:MicroNova發動機硬件在環測試
德國MicroNova公司面臨在短時間內開發緊湊的、高精度的板卡用于汽車發動機管理系統硬件在環測試,要求能夠仿真2缸、4缸、6缸和12缸完整的測試環境的項目需求。
基于對PXI平臺模塊化、靈活性的了解,MicroNova選擇了NI PXI平臺,包含PXI-8196實時嵌入式控制器、PXI-7831 FPGA板卡、PXI-6723模擬輸出板卡以及PXI CAN模塊。其中,PXI-7831是能提供模擬的輸入輸出、數字的輸入輸出、PWM生成和測量的標準板卡,并可通過LabVIEW FPGA編程實現曲軸、凸輪軸、爆震、點火等非標準信號。通過LabVIEW仿真接口工具包集成已有的在Simulink環境下開發的仿真器模型,協同TESIS DYNAware提供的發動機模組來構建虛擬的測試環境,并運行于PXI實時控制器中。MicroNova開發了信號調理模塊,對信號大小、I/U、U/I、U/R等進行調理,以滿足類似ECU電流在休眠模式下為幾個μA,而工作模式時可達50 A的需求。此外,系統還包括Magneti Marelli ECU、故障輸入模塊和真實負載。
整個硬件在環測試系統的軟件架構如圖4所示,包括FPGA目標、實時系統和上位機三個部分,其中上位機為用戶操作界面和自動化測試管理程序。該系統具有小型化、高精度、開發時間短、低成本的特點。不僅可直接使用已有的模型、接口板等;又可根據系統需求進行模塊替換或擴展;板載FPGA便于實現靈活的可重復配置,但無需復雜的軟件硬件知識;通過PXI背板總線實現數量眾多的I/O在不同的總線速度下同步。
圖4 MicroNova發動機硬件在環測試軟件架構
該平臺已成功用作BMW某12缸直噴發動機的硬件在環仿真器;還可用于其它不同系列發動機,如:含可變氣門驅動、可調式凸輪軸控制、直噴技術的V-12和6缸直列發動機;帶渦輪增壓、空氣中冷4缸直列共軌柴油機;用于摩托車的進氣管噴射、2個爆震傳感器和雙節氣門的V-2發動機。
總結:
目前,基于PC技術的控制器開發“V”模式已成為汽車ECU開發一套行之有效的方法。對于其中快速原型和硬件在環兩個關鍵環節,設計者可根據ECU I/O數量和控制邏輯的復雜度選擇對應的CompactRIO平臺或PXI平臺,且整個系統是在圖形化設計工具LabVIEW下實現的,無需復雜的軟硬件知識;均具有成本低、開發時間短、可擴展性、通用性等特點。
-
控制器
+關注
關注
112文章
16214瀏覽量
177479 -
汽車電子
+關注
關注
3024文章
7883瀏覽量
166551 -
NI
+關注
關注
19文章
1123瀏覽量
100206
發布評論請先 登錄
相關推薦
ecu電子控制器復位什么意思
嵌入式系統軟硬件基礎知識大全
經緯恒潤推出新一代快速控制原型產品 ControlBase_S

應用分享 | 高性能電源在汽車ECU地漂測試中的應用
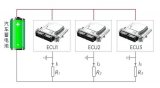
KubeCASH:基于軟硬件融合的容器管理平臺
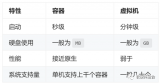
評論