汽車行業是AGV應用率較高的行業。目前,世界汽車行業對AGV的需求仍占主流地位(約57%)。在我國,AGV最早應用于汽車行業是在1992年。近幾年以來,已有許多汽車制造廠應用了AGV技術,如東風日產、上海通用、上海大眾、東風汽車、武漢神龍、北汽福田等。
AGV在汽車行業的應用,主要體現在主機廠的發動機、后橋、變速箱、底盤等部件的自動化柔性裝配,以及零部件的上線喂料等。特別是對于后者,由于主機廠的裝配車間一般都非常大,常常需要大量的遠距離物料搬運,AGV代替叉車和拖車搬運物料大有用武之地,且能夠實現批量替代的規模成本優勢,具有明顯的經濟效應。
而對于體量較小的零部件工廠,由于沒有主機廠那種成批量的替代效應,加之既有觀念的束縛,AGV在廠內物流的應用不太普及。但隨著AGV應用的日益成熟,以及人工成本的逐步上漲,相信會有越來越多的零部件工廠考慮AGV的使用。
某汽車零部件企業廠內物流背景介紹
本文所要研究的實例是給1家主機廠供應配套產品的零部件工廠(簡稱A工廠),位于經濟發達的沿海地區,A工廠坐落在主機廠的供應商園區,廠房占地面積約1萬平方米,擁有兩條生產線,從功能上可將廠區劃分為零件收發存區域、生產線、成品存儲區和成品發貨區,工廠布局示意圖,如圖1所示。
圖1 A工廠布局示意圖
其物流過程簡要描述如下:
步驟1:叉車將原材料從供應商送貨車輛上卸貨后,轉移至零件存儲區存放;
步驟2:叉車從零件存儲區取出零件并向生產線喂料;
步驟3:叉車將生產線用完的零件空箱返回到零件收發存區域;
步驟4:叉車將零件空箱轉移至空箱存放區;
步驟5:叉車將零件空箱從空箱存放區叉取至發貨道口裝車,返回給供應商;
步驟6:叉車將生產線下線的成品搬運至成品存儲區;
步驟7:叉車將成品轉移至庫位存放;
步驟8:叉車將成品從庫位取出,發運裝車;
步驟9:叉車將從主機廠返回的料箱卸車,再由叉車搬運至生產線。
在以上物流過程中,全部物料搬運、裝卸車都由叉車完成。由于業務量比較大,總共配置有16輛叉車,其中,零件收發存操作2輛,喂料上線及返空箱5輛,成品下線及返空箱5輛,成品存儲2輛,成品發貨2輛。同時,由于每天工作2個班次,叉車工總數達到了37人。
近幾年來,人工成本上漲壓力頻現,一線叉車工的人工費每年上漲10%;不僅如此,由于A工廠實行兩班制生產,勞動負荷相當大,叉車工離職率一直在高位徘徊,是在春節前后,用工荒得不到有效解決,多次面臨停產風險。
為解決成本上漲和用工荒的問題,A工廠決策層在對國內AGV應用情況進行詳盡調研的基礎上,決定在廠內物流使用AGV來代替叉車作業。
應用AGV經濟性分析
鑒于AGV相對叉車的優勢在于遠距離的物料搬運作業,因此,A工廠在進行廠內物流規劃改造時,即考慮將喂料上線及返空箱的5輛叉車和成品下線及返空箱的5輛叉車,合計共10輛叉車,用AGV來代替。裝卸車及短距離入庫等不利于AGV發揮作用的操作仍使用叉車。
規劃后的物流過程,如圖2所示。
圖2 規劃后物流過程圖
與之前相比,差異在于:
步驟2~6:叉車從零件存儲區取出零件后放置于AGV路徑上的掛載點,由AGV經過該掛載點后將零件掛載上,然后,將零件搬運至生產線上的卸載點;同時,AGV在裝載點將生產線用完的空箱掛載后返回至零件收發存區域的卸載點,將空箱卸下后,再由叉車將空箱叉取至空箱存放區。
步驟7~11:AGV在行走路徑上的掛載點將生產線下線的成品掛載后,搬運至存儲區并在卸載點將成品卸載,再由叉車取走并入庫存放;而由主機廠返回的空箱,則由叉車從空箱存放區轉移至AGV掛載點,由AGV帶回生產線。
經過AGV應用前后的成本分析,可以得到如下對比數據,見表1。
表1 對比數據表
從表1的經濟性分析可以看出,應用AGV可以帶來成本的大幅下降,物流成本可由421萬元降至264萬元,每年對比項目應用AGV之前應用AGV之后資源變化能夠節約157萬元,即37%的成本下降,而且未來人工費預計將會持續上漲,AGV的成本優勢將愈加明顯。圖3為成本對比趨勢模擬。
圖3 成本對比趨勢模擬圖
因此,無論從降低管理難度還是從成本上考慮,AGV方案都具有良好的可行性和實用價值。在經以上綜合對比分析后,A工廠決策層對AGV方案予以了肯定,并決定在廠內物流付諸實施。
-
AGV
+關注
關注
27文章
1280瀏覽量
41008
原文標題:AGV在汽車零部件廠內物流的應用
文章出處:【微信號:industrial_robot,微信公眾號:國聯視訊工業機器人信息服務】歡迎添加關注!文章轉載請注明出處。
發布評論請先 登錄
相關推薦
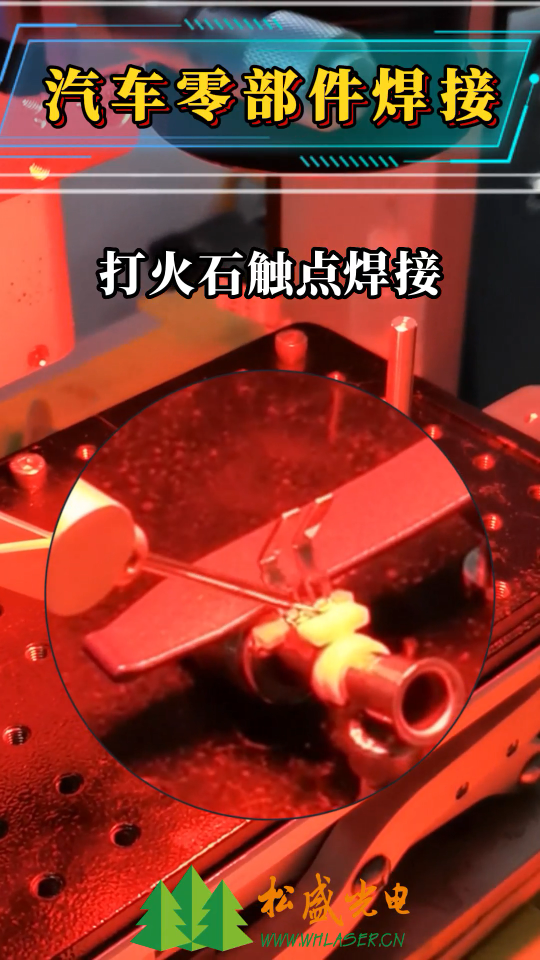
評論