幾十年來,汽車行業對于自動化行業來說,是如同“常青樹”般的下游產業。
2018年,中國汽車行業迎來了轉折性的一年,在經歷連續28年增長后首次出現負增長。
中汽協發布的最新數據顯示,2019年前5個月的汽車產銷量整體下降趨勢仍沒有緩解。
有行業人士評,車市將進入前所未有的“增量停滯,存量升級”的時代。
受累于汽車行業的下行,去年自動化市場也相應出現了波動。
那么,身處上游的自動化供應商們,該如何在這一新變化中把握機遇呢?
追本溯源,自然是從汽車行業的“轉型升級”上下功夫。
兩個角度
工控君了解到,得益于近兩年國內政策在汽車智能制造的推動,汽車行業明顯朝著網聯化、自動化和數字化轉型。
這也對自動化供給側提出了新的要求,同時,更是自動化的新機遇。
實際上,從自動化角度來說,“網聯化、自動化和數字化”可以統稱為工業4.0時代的“新自動化”。
從一輛汽車的全生命周期來看,自動化廠商有兩個角度可切入。
一個是縱向,即產品從無到有的各環節服務,利用數據優化工藝;另一個則是橫向,即產品全生命周期的服務,利用數據打通產業價值鏈。
誠然,以上兩個角度不是唯一的方法,但的確是近兩年市場增長比較快的需求。
顯然,核心是數據的有效利用。工控君認為,轉型的結果都會落到數字化虛擬和數字化現實兩方面,而虛擬最終也會反饋到現實。
數字化虛擬和現實
何為數字化虛擬?
它代表了企業里非真實存在的構成,而這一切來源于數據。
此前,工控君參加的一些自動化用戶年會和智能制造論壇上,有兩個前幾年不太被提起的技術,今年幾乎成了最熱的新寵兒。
它們正是虛擬的魅力——三維仿真技術和虛擬增強現實技術。
今年凡是關于上述兩個技術出現的場合,都會吸引眾人的圍觀。
像西門子、施耐德電氣、羅克韋爾自動化等國際巨頭均做了相應的部署。
三維仿真技術和虛擬增強現實技術在產品設計、生產制造和數字化工廠系統集成等領域的應用已經在多家車企落地。
例如西門子為中國一汽打造的數字化工廠,即利用了其“數字化雙胞胎”理念,營造了與現實世界對稱的數字化鏡像。
從產品研發、生產制造,到工廠管理環節,虛擬的鏡像都能發揮作用。
在產品研發階段,利用三維軟件實現協同操作,并對虛擬的產品進行仿真測試和驗證,縮短開發周期節約和研發成本。
在生產管理階段,將虛擬的制造流程模型集成到管理系統中,可實時調度、調整和優化生產。
在設備管理領域,通過虛擬調試模型,實現機械和電氣信號的連接,縮短投產時間。
最終,“當實時數據與三維仿真模型連接后,工廠將可視化和透明化,通過虛擬和現實兩個世界數據的不斷迭代,模型的不斷優化,進而獲得最優的解決方案。”
據悉,吉利汽車某個智能工廠的搭建,也是基于虛擬技術實現了工廠的集成調試,生產效率約提高20%、成本降低約20%……
另一方面,基于大數據建立的虛擬模型對于設備的預測性維護也尤為重要。
例如北京奔馳,結合大數據+深度學習算法,將大量的生產數據轉化為可被識別和利用的信息,并將這些信息建模和分析,輸出最終預測結果反饋到現場,為現場作業提供決策。
同時,根據現場的實際情況,再反饋到大數據平臺,不斷優化預測能力。
現在,奔馳的點焊產線可以提前8小時以80%的準確率實現設備故障預警,涂膠產線可以提前24小時以78%的準確率實現設備故障預警。
如果說,虛擬技術在縱向上優化了工藝流程,那么信息系統的集成則在橫向上優化了產業鏈,這一部分對于自動化廠商來說再熟悉不過,工控君不再過多復述。
值得一提的是,虛擬技術的實現也必須是建立在信息互通的基礎上。
奔馳之所以能夠實現訂單式生產,是因為從生產零件到整車都有相呼應的二維碼追蹤,并在接收到訂單時這些信息隨即進入到了智能生產控制模型中。
在汽車生產過程中,所有參與生產流程的環節都能實時共享系統中其對應的信息。
“依據電子標簽與控制終端,可以實現裝配質量控制、生產系統報告數據的實時監控、記錄、分析、反饋與調節的閉環控制。”
未來,隨著數據的深度挖掘和有效利用,將發揮更智能化的作用。
-
西門子
+關注
關注
94文章
3009瀏覽量
115664 -
自動化
+關注
關注
29文章
5519瀏覽量
79122 -
汽車產業
+關注
關注
1文章
173瀏覽量
12802 -
智能工廠
+關注
關注
3文章
987瀏覽量
42372
原文標題:汽車產業下滑后,來看看這份自動化供應商生存指南吧
文章出處:【微信號:ofweekgongkong,微信公眾號:OFweek工控】歡迎添加關注!文章轉載請注明出處。
發布評論請先 登錄
相關推薦
科達嘉電子亮相AWC 2024深圳國際智能網聯汽車產業展
DigiKey 將在 SPS 2024 重點展示自動化產品與服務
羅克韋爾自動化發布第九版年度《智能制造現狀報告:汽車版》
天馬榮膺通用汽車“2023年供應商質量卓越獎”
天馬榮獲通用汽車“供應商質量卓越獎”
杰發科技受邀出席一汽-大眾2024年供應商主題日活動
英特爾為芯片制造自動化組建日本團隊
【換道賽車:新能源汽車的中國道路 | 閱讀體驗】 新能源到底新在何處?新能源在國內如何發展?
【換道賽車:新能源汽車的中國道路 | 閱讀體驗】1.汽車產業大變局
動力電池智能工廠數字孿生可視化,助力新能源汽車產業數字化轉型
奧托立夫與江鈴汽車共謀發展 榮獲“A級供應商”殊榮
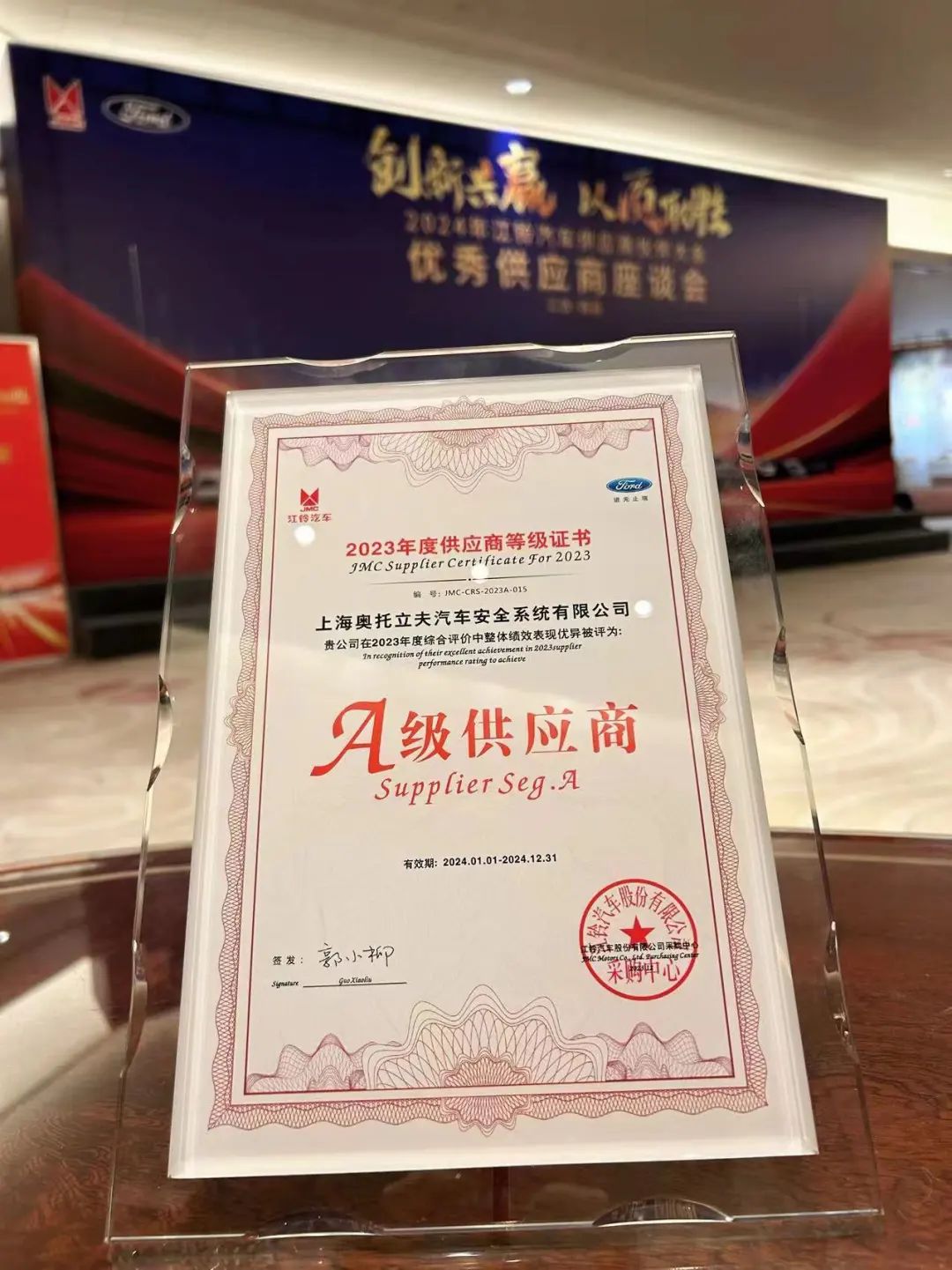
評論