AOI
近年來,作為一種經典檢測技術,AOI(自動光學檢測)以如此高的速度發展到AOI設備已廣泛應用于SMT(表面貼裝技術)PCB(印刷電路板)組裝。 AOI通過旋轉相機捕獲圖像,自動掃描PCB,然后在測試的焊點和數據庫中的合格參數之間進行比較。圖像處理將導致表面貼裝PCB上的缺陷暴露,并通過監視器或自動標記顯示或指示這些缺陷,以便返工人員能夠對其進行處理。
AOI主要負責以下檢查目標。
一個。最終質量,即在產品離開生產線之前對產品狀態進行檢查。當制造問題明確,SMT PCB組件覆蓋高混合,并且應該嚴格考慮數量和速度時,該檢查目標應該首先考慮。在這種情況下,AOI設備通常放置在裝配線的末端,在那里它能夠大規模地生成大量的過程控制信息。
b。過程跟蹤,即通過詳細的缺陷分類和元件安裝位移信息,利用AOI設備監控表面安裝組裝過程的過程。當產品的可靠性至關重要時,制造商應首先利用這一目標,需要大批量低混合組件,并且組件供應處于穩定狀態。確定此目標后,應將AOI設備放置在表面安裝組裝線的多個位置,以便在線監控特定的制造情況,并為制造技術調整提供必要的基礎。
雖然AOI設備可以沿生產線放置在多個位置,并且它在每個位置上的位置將導致不同的缺陷檢查,但AOI設備應放置在可以識別和糾正大多數缺陷的位置。可以考慮三個檢查位置:
a。焊錫膏印刷后。如果焊膏印刷工藝完全符合要求,ICT(在線測試)期間檢查的缺陷數將大幅減少。典型的焊膏印刷缺陷包括:
?焊盤上的焊膏不足
?焊盤上的焊膏過多
?焊膏和焊盤之間的不匹配
?焊盤之間的焊接橋接
在ICT的過程中,上述缺陷概率與問題的嚴重程度成正比。稍微不足的焊膏很少會導致缺陷而沒有焊膏,但在ICT期間幾乎會導致缺陷。焊膏不足可能是導致元件缺失或開路的原因之一。然而,缺少組件是由其他原因引起的,這是確定AOI設備放置位置的前提。而且,這些原因必須包含在檢查時間表中。特定的放置檢查直接支持過程跟蹤和表征。在此階段,定量過程控制數據包括印刷位移和焊膏量以及印刷焊膏的定性信息。
b。在回流焊接之前。當在回流焊接之前放置AOI設備時,在焊膏印刷之后和回流焊接之前實施自動光學檢查,這是AOI的典型檢查位置,因為該位置能夠使得大多數缺陷暴露于焊膏印刷和元件安裝。在該位置處產生的定量過程控制信息提供關于IC安裝器和細間距部件安裝器的對準信息,其可用于修改部件安裝或校準表面安裝器。一般來說,這種位置檢查能夠滿足過程跟蹤的目標。
c。回流焊后。 AOI設備放置在回流焊接之后,即表面貼裝組件的最后階段。這個位置是最流行的AOI選擇,因為在回流焊接后放置AOI設備時可以捕獲全尺寸組裝問題。回流焊后的自動光學檢測提供了高安全性,因為它可以識別由焊膏印刷,元件安裝和回流焊接引起的問題。
ICT
ICT設備是應用于電氣測試的最基本設備。傳統的ICT設備利用專業的床釘,與PCB板上牢固焊接的元件接觸,并使用一定的電壓和電流進行最終測試,以便可以知道元件缺陷,包括缺失,位移,錯位,參數偏差,焊接接頭橋接,開口和短路等。床釘適用于簡單的PCBA和大批量生產,因為它具有高速和低成本。然而,隨著PCB組裝密度的逐漸增加,細間距SMT組裝和新產品的推出經歷了越來越短的時期,PCB板變得多樣化,床釘測試必須面對一些無法克服的不可或缺的問題。它甚至無法對某些高密度SMT PCB組件進行測試。
SMT PCB組裝的另一種流行的ICT方法是飛針測試,它依賴于大量的飛針來測試電氣電路性能。然而,它被廣泛接受應用于PCB制造測試。由于它用于表面貼裝組裝測試,它可以做更多。
AXI
與AOI相比, AXI是一種新開發的檢測方法。當組裝好的PCB板沿軌道進入AXI設備時,X射線在被發射管傳輸并通過PCB后將被下方的探測器吸收。由于焊點含有大量可吸收X射線的鉛,因此良好成形的焊點將在圖像上顯示黑點,而X射線則穿透某些材料,如玻璃纖維,銅或硅。因此,X射線檢測使焊點如此直接和清晰,可以通過圖像分析算法自動檢查焊點缺陷。
由于現代技術的發展,X射線檢測已經從2D發展到3D。作為通過X射線透射的檢查方法,前者產生清晰的元件焊點圖像,這些元件焊點放置在單面板上,同時在雙面板上表現不佳。然而,后者利用分層技術使其能夠檢查雙面板上的焊點。此外,3D X射線檢測還能夠檢查那些看不見的焊點的缺陷,例如BGA焊點和PTH焊點。此外,可以檢查PTH孔中的焊料以確保其充足,從而顯著提高焊點質量。
AOI,ICT和AXI之間的比較
每個硬幣都有兩面。
ICT是制造過程中最常用的測試方法之一,具有以下優點:高缺陷觀察能力和高測試速度。由于其方便快捷的特點,ICT被需要大批量產品的公司所接受。然而,當涉及需要低容量和多種類型產品的用戶時,這是不合適的,因為需要經常更換床釘。此外,隨著電路變得越來越復雜并且密度越來越高,傳統的測試方法必須面對極端的限制,并且ICT越來越難以發現缺陷。此外,更多的接觸點添加會導致測試錯誤和更多的重新測試。
AOI的最大優勢在于極短的測試編程時間和高靈活性。除了目視檢查無法檢查的缺陷外,AOI還能夠累積每個環節的制造質量和缺陷類型,并將提供給技術控制工程師進行分析和管理。 AOI的缺點包括未能檢測到電路錯誤和檢測不可見焊點的殘疾。
作為一種相對成熟的檢測技術,AXI能夠覆蓋高達97%的制造缺陷率并檢測焊料用肉眼看不到的關節。然而,AXI未能在電氣性能方面測試缺陷。
學會充分利用它們。
現在每個檢查方法有其自身的優點和缺點,它們實際上不是兩種相互補充的關系。 ICT,AOI和AXI可以首先分為兩類:ICT和AOI/AXI,因為ICT負責檢查電路中的缺陷,而AOI/AXI則用于外觀缺陷。總之,信息通信技術應該得到肯定,并且應該考慮AOI/AXI或它們的組合。
AOI/AXI在確定表面貼裝組件質量方面發揮著重要作用。它們在很多方面彼此不同:
根據上圖中的描述,成本,缺陷類型和檢查速度主要是當您準備好為表面貼裝PCB 選擇理想的檢查方法時應該考慮的因素。
-
AOI
+關注
關注
6文章
143瀏覽量
24349 -
PCB打樣
+關注
關注
17文章
2968瀏覽量
21656 -
AXI
+關注
關注
1文章
127瀏覽量
16598 -
華強PCB
+關注
關注
8文章
1831瀏覽量
27724
發布評論請先 登錄
相關推薦
XILINX FPGA IP之AXI Traffic Generator

AOI控制電路板質量
什么是ICT探針
ICT維修/二手ICT維修/德律ICT維修/專業維修各類ICT測試儀
比較AOI和AXI
ICT,AOI,AXI和汽車功能測試提供的測試和檢查解決方案
泰瑞達ICT故障處理
ICT測試儀與飛針測試儀的分析
AOI在SMT中的應用
從應用角度詳解什么是AXI
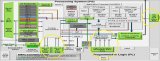
評論